I am looking at the performance of closed cell foam.

I am looking at the performance of closed cell foam and I have read many forums including the pro’s and con’s on this site which are very helpful. My question though is, have there been any issues of damp showing up on the interior surface of the drywall.
I am not looking at external insulation at this point and the wall structure I am most interested in would be brick or stucco over OSB or ply with 3.5″ closed cell foam, 2 x 6 studs @ 24″ centers and 1/2 inch internal drywall.
[Edit: The following was pasted from a subsequent posting]
In reference to my previous question, the last part seems to have been cut off. Specifically I want to know if problems of damp have occurred at stud locations.
Concern being that there would be no vapor barrier between studs and drywall to offer some moisture transfer protection as would be the case in traditional construction.
GBA Detail Library
A collection of one thousand construction details organized by climate and house part
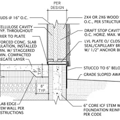
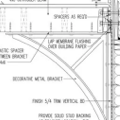
Replies
Paul,
What's your climate?
While it's possible to have problems originating from cold studs, these problems are not solved by a vapor barrier.
The classic situation (called "ghosting") occurs in walls with fiberglass batts. Because the studs act as thermal bridges, they create cold stripes on the wall. During the winter, these stripes can be somewhat more humid than the adjacent drywall -- because that's where the interior moisture condenses. (Note: we're talking interior moisture, not exterior moisture -- which is why a vapor barrier doesn't help.)
If the occupants smoke cigarettes or burn candles, small particulate matter can be attracted to the moist stripes on the wall. At that point, the stripes become visible -- the classic "ghosting" scenario.
I've never heard of a ghosting problem on a wall insulated with spray foam, but it could happen.
Martin,
Someone's got to change this web site so that questioner's location is a required input.
Thanks for the input Martin.
I'm in Toronto and typical winter temperatures fall to around -10c excluding wind chill effect. Of course it can drop further although normally not for sustained periods.
I understand the ghosting issue and I guess I should more correctly have indicated concern about potentially damp studs exacerbating the issue by direct damp contact as opposed to just increased moisture inside the barrier due to contact with the cold stud. I'm thinking about interstitial condensation occurring in the stud and then causing interior problems including mould possibly. I'm new to this climate so less familiar with the degree to which one should be careful about the magnitude of condensation issues caused by greater temperature differentials than I am used to dealing with. I have also not yet built with closed cell foam. It may well be that I am being overly cautious. Perhaps also, plywood in place of OSB as the sheathing material would permit greater diffusion towards the exterior.
Paul,
You are suggesting the installation of R-23 cavity instulation. That's not a lot. I would advocate more.
If you're worried about cold studs, the solution is fairly easy: include exterior foam sheathing, 2 inches thick or more. But you say you don't want to use exterior foam. Your choice -- but if you are worried about cold studs, why shy away from the solution?
That said, you are worrying too much about condensation within your wall. If you insulate as you have described, you have no particular reason to worry about condensation within your stud cavities. However, you'll be losing more energy than if you planned an R-32 or R-40 wall.
Martin,
Thanks very much for your answer.
I thought I might be overly concerned.
Don't get me wrong, I'm not averse to external insulation at all. It's just that I have been looking at various wall designs, performances and costs from double stud to SIP panels I and came to conclude I needed some additional opinion / advise on the basic cladding, sheathing, foam, drywall option.
I take your point about the R-value as well. That's a performance and life cycle cost to initial budget trade off I can offer above and beyond the minimums.
Thanks for taking the time.
There are three different ways of looking at the R-Value of a wall: Cavity R-Value (the R-Value of the insulation in the wall cavity section of the wall), Clear wall R-Value (which is the R-Value of the cavity portion of the wall and the framed portion of the wall) and Whole Wall R-Value (which is the R-Value of all portions of the wall, including windows).
With 3-1/2” of a closed cell insulation like Corbond, which has an aged R-Value of 6.2 per inch, you have an cavity insulation R-Value of 21.7. According to a table published by Corbond, with 2-1/2” of Corbond, you have at a 90˚ temperature ∆ an 87% efficiency (i.e. reduction in heat loss).
http://www.corbond.com/efficiency.htm
At 3”, you have a 90% efficiency, and at 3-1/2” you have about 91% efficiency. Clearly, going beyond 3” is going to result in drastically less return for the dollars spent on very expensive Corbond or other closed cell insulations.
A typical home might have a framing fraction of 23% (i.e. the portion of the wall that contains all the framing members like studs, plates, headers, blocking and doesn’t contain closed cell insulation). I don’t know the framing fraction you’ll end up when your studs are 24” O.C. but let’s assume it drops to 20% unless you use other smart framing techniques. The R-Value of a 2x4 stud is about 3.7 and a 2x6 stud about 5.8 (these figures vary depending on the source, but are accurate enough for comparison here). With 3-1/2” of Corbond in a 5-1/2 inch cavity, in essence, you really have some portions of that 20% of your wall with an R-Value of only a little over 3.7 plus the R-Value you gain from sheathing.
But you raise an interesting point about interstitial humidity, Paul. The temperature of the 2x6 stud just to the interior of the 3-1/2” of Corbond would have a temperature that is well below the dew point and I think, getting back to your concern, I do wonder whether under the right conditions if condensation couldn’t occur on the studs right next to the Corbond. I’ll grant you that the 2” cavity will be fairly warm, maybe 60 degrees, and any condensation would turn to vapor as outside conditions moderate.
In my mind, it is appropriate to next turn your attention from Cavity R-Value to Clear Wall R-Value. I agree with Martin that R-23 in your wall cavities is not enough insulation and you should consider rigid foam. By adding rigid foam insulation to the exterior of your sheathing, you can with an inch of XPS or 1-1/2” of Polyiso, effectively more than double the R-Value of 20% of your wall. Additionally, you also boost the R-Value of the Cavity R-Value too, raising the interior surface temperature of the closed cell insulation and the stud interface.
As an aside, I’d like to get other forum readers’ take on the following. I’m a spray in foam advocate. I really like the stuff. But the table from Corbond (Icynene publishes a similar table with similar efficiency results)
http://www.icynene.com/assets/documents/pdfs/Resources/Building-Science/The-Economic-Thickness-of-Thermal-Insulation-Dec08.pdf
really bothers me. If you can believe the numbers, at some point it just doesn’t make sense to keep adding insulation. If by adding an 1-1/2” of Polyiso with an R-Value of 9.8 to the 3-1/2” of closed cell insulation Paul is considering, results in a 40% increase in Cavity R-Value, but yields, if Corbond’s table is to be believed, only a further one or two percent reduction in heat loss in the cavity section of the wall, at what point do you think that increasing Cavity R-Value doesn’t make economic sense?
I have a big interest in Passive House. I am an advocate for superinsulated structures. I think staggered stud assemblies that maximize the thickness of the insulation in our walls are very effective. Outsulation techniques make sense for a number of reasons. I think Larsen trusses are very effective. But having said all that, if you can believe the Corbond table and want to build a very cost effective but highly efficient home, it seems to me that what makes the most sense is to create as tight an envelope as possible, insulate the cavities with three inches of closed cell insulation to maximize R-Value in a 2x4 wall or 5-1/2”of cellulose in a 2x6 wall, add rigid insulation to the exterior (and/or interior) to increase the clear wall R-Value, and then finally, spend the money you would have spent on thick walls with lots of insulation on properly sized ,spec’ed and oriented high performance windows to boost the Whole Wall R-Value.
Sorry to ramble on, but I think it is an interesting question. Just how do we allocate our dollars when we design and build structures in a way that is most intelligent?
Good discussion. One of the big issues with spray foam is the continuity of the vapour barrier properties- i.e. the foam(2lb) is a great product and proven as a vapour barrier but what about built up wood portions like window/door framing. Built with low quality(not straight) wood or as the wood shrinks -gaps can open up between the individual wood members that could allow air movement in the wall to reach the cooler outside surface and condense inside the wall or roof. Some builders are sealing these gaps with poly and/or caulking. May not be a problem with continuous interior finish but if there is a poorly sealed electric box or other wall opening next to a gap??? The tighter buildings put added (air)pressure on any weak point in the building envelope. One key is to eliminate or minimize air movement through the wall or roof assembly
Paul,
If you're using a reservoir cladding, like brick or stucco, then it's imperative that there be either a drainage plane (air space) between cladding and sheathing, or a very vapor-open envelope behind it. OSB is relatively vapor closed and highly vulnerable to moisture - plywood is far preferable. And closed-cell foam would create a vapor barrier to the inside and prevent inward drying.
As long as you control indoor RH with ventilation and source control, you shouldn't have to worry about vapor diffusion from the inside or consequent interstitial condensation. But, with a reservoir cladding, you do have to be concerned about the much greater solar vapor drive to the inside. That's a much greater moisture issue.
With stucco, be sure to use a double layer of felt or asphalt-impregnated kraft paper. And with either brick or felt, a drainage mat between felt and sheathing would be highly protective. Cavity insulation should be vapor-open, such as open-cell foam or cellulose. But be sure to get at least the minimum recommended R-value for your climate.
Derek,
Those "diminishing return" graphs or charts that every foam manufacturer seems to use are deliberately misleading (and hence your confusion). They are designed to "prove" that using minimal (and less costly) foam thicknesses are "better" than more R-value.
Once a thermal envelope is properly air-sealed, heat loss is directly proportional to R-value. Those charts show the percentage "efficiency" of additional insulation compared to no insulation. With a zero starting point, the most improvement comes from the first inch of insulation or the first 1 R. From then on, every additional R is going to offer less of an incremental savings (compared to no insulation).
But, as we all should know, for the cavity wall area of a thermal envelope, doubling the R-value at any starting point halves the conductive heat loss (or doubles the efficiency). So going from 4" of foam to 8" of foam will double the efficiency of the insulated wall area, but will be so cost-prohibitive that nobody would buy spray foam.
It's also true, as we should also know, that with higher cavity R-values, the degrading effect of the thermal bridges becomes more significant. But the solution isn't to restrict the R-value but rather to create a thermal break - whether with interior or exterior foam board, cross-hatched framing, or some form of double frame system.
Spray foam has it's place, but there is almost as much hype propagated by the foam industry as there was by the Pink Panther years ago.
Craig,
The vapor barrier quality of closed-cell foam is, perhaps, its least attractive quality. All walls (and roof assemblies) need to breathe in order to prevent moisture accumulation and consequent problems. Ideally, a thermal envelope will breathe in both directions, as diurnal and seasonal changes alternate the vapor drive.
We've known for a long time (anyone who's been paying attention) that we don't need vapor barriers - we need air barriers. Vapor diffusion from the interior is rarely a problem, unless indoor RH levels are monstrously high. In some cases, a vapor retarder is in order as long as it isn't so restrictive as to limit drying. With reservoir claddings, like stucco and brick, it's imperative that a wall assembly can dry to the interior. Closed-cell foam prevents this.
In a "hot roof", closed-cell foam will prevent a roof leak from showing up until it does major damage to roof sheathing. Even open-cell foams in "hot roofs" can hold large volumes of water sufficiently long to cause sheathing damage or mold.
As with almost every other petrochemical plastic used in construction, we will soon discover a host of "unanticipated consequences", and wish we had used the sustainable (green) materials that nature has always graciously offered us.
Robert, I only mention it as I still see problems of this kind with poor vapour barrier installation and poor(gaps/holes) exterior paper air barrier allowing air leakage/ into the wall cavity creating condensation It still seems that a majority of the workers doing this work (not to mention designers) do not understand these issues. And then the electrician adds wiring and doesn't seal the penetration. Also, the increasing use of spray foam is creating a learning curve. About 80% is 2lb and the remainder 1/2 lb (with a sprayed on vapour barrier!!) or more rarely an airtight drywall situation. I live in the Vancouver BC area (leaky condo capital) and wonder how long it will be before our building codes stop requiring an interior vapour barrier. I think you would agree that the air barrier is even more important without a vapour barrier- that means skilled tradespeople. Love this discussion group- Thanks
Craig,
Here is on of my favorite recent documents by Joe Lstiburek.
http://www.buildingscience.com/documents/insights/bsi-024-vocabulary/?topic=/doctypes/building-science-insights
I think it is easier to visualize things with this "new" vocabulary
Layers instead of barriers etc.
And...... if you download the pdf..the graphics are little better
John B,
In Vermont, a layer is what gives us our morning eggs.
Joe's semantic suggestions are a step in the right direction. We've got to get away from the notion of barriers - not only because barriers work both ways and can be as dangerous as they are helpful, but also because there are no artificial barriers that can withstand the forces of Mother Nature (just ask the residents of New Orleans or those living in the Mississippi River flood plain).
But I'm not sure that the vernacular perception of "control" is much different. While a scientist or engineer might understand "control" to mean variably-effective means of limiting the influence of external factors and forces, I suspect the term creates the illusion of complete mastery to the lay person, much like "barrier".
Perhaps better terms would be " resistance elements", as in thermal resistance element, water resistant element, air resistant element and vapor resistant element. First, because resisting nature's forces is the best we can hope for, and it's important to plan for failure; and second, because each of those may be a material layer or a design element, and more than one function can be combined into each element.