Improving conditioned and unconditioned attic insulation

We built our house recently (in Maine Climate Zone 6) and I worked to try to make it as efficient as possible within our budget. The entire house including the garage walls are insulated 2×6 bays with R-19 unfaced fiberglass with the exterior wrapped in 3/4″ R-3.8 rigid foam board. We built with two spaces to be finished off in the future, one above the garage and a 3rd floor walk up attic with 3 dormers. With that in mind, we had them both wired and insulated by the builder as conditioned spaces with soffit and ridge vents and R-38 unfaced fiberglass in the rafter bays, but they weren’t included in the sizing of the geothermal heating unit. The other attic area is an unconditioned space where the 2nd floor duct trunk runs through and out to the various outlets. That is insulated on the ceiling with a combination of batts and blown in to an R-49 value.
After a lot of reading on here and before the extra spaces are fully finished I would like to improve on what we have to make the house better insulated and more efficient. My question is two fold. What would be my best option on improving this in its existing condition and design? Should I remove the existing insulation and fill the cavities with 10″ of spray foam? I got a quote for all the spaces (including the unconditioned attic) using open cell foam for $10000. I have also read about adding rigid foam board to the underside of the rafters. Could I do this with my existing vented setup or would it prove a conflict? I feel like this would be exceedingly hard trying to contour to the dormers.
Can/Should I add these additional spaces into my existing geothermal HVAC system? We have a 4 ton Waterfurnace unit. If I improve my insulation and bring my ducting into the thermal envelope could I offset the increased load for the additional space/s?
GBA Detail Library
A collection of one thousand construction details organized by climate and house part
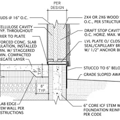
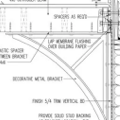
Replies
>"Can/Should I add these additional spaces into my existing geothermal HVAC system? We have a 4 ton Waterfurnace unit."
If the WaterFurnace currently keeps up with the load without using much auxiliary strip heating, adding the additional space adds remarkably little to the whole house heat load, once you've tightened it up. If you're burning heat strip a lot of the time already, you may want to do something different for the additional space, such as a small ducted mini-split.
But you have some higher priority issues to deal with:
> "The entire house including the garage walls are insulated 2×6 bays with R-19 unfaced fiberglass with the exterior wrapped in 3/4″ R-3.8 rigid foam board."
When compressed into a 5.5" cavity depth R19s really only perform at R18. But even then, 3/4" XPS isn't nearly enough for dew point control on R18 of cavity insulation in your zone 6 climate zone- it absolutely needs an interior side vapor retarder to keep the moisture content of the sheathing bounded. The IRC code minimum for using interior latex paint as the vapor retarder would be R11.25, which is three times the labeled performance of your exterior foam:
https://up.codes/viewer/wyoming/irc-2015/chapter/7/wall-covering#R702.7.1
The thermal performance of 2x6/R19 + R3.8 continuous insulation also doesn't even meet IRC 2012 or later code minimums for zone 6. A code minimum build would have been 2x4/R13 + R10 c.i. or 2x6/R20 + R5 c.i. :
https://up.codes/viewer/wyoming/irc-2015/chapter/11/re-energy-efficiency#N1102.1.2
If the walls are NOT air tight and DON'T have a polyethylene vapor barrier it's time to get serious about air sealing (blower door & infrared imaging directed), and painting the walls with "vapor barrier latex" primer, before the house has gone through more than a few heating seasons of loading up the exterior sheathing with moisture.
>"Should I remove the existing insulation and fill the cavities with 10″ of spray foam?"
Ten inches of spray foam isn't cost effective and won't move the needle much on the HVAC sizing. 10" of open cell foam is R37, which isn't really any better than what you have now. If they're 2x10 rafters they're really only 9.25" anyway. A 2 x 12 is 11.25". Open cell foam is also too vapor open to protect the roof deck, though you might be able to get away with using a "smart" vapor retarder on the interior. The valleys in the dormers make it impossible to properly vent the roof deck. While 10" of closed cell would get you way past code minimum, it's nowhere near cost effective.
In zone 6 as long as more than half total R is air impermeable low vapor permeance closed cell foam tight to the roof deck the rest can be lower cost fiber insulation. If 2x10 (9.25" deep) going with 4" of HFO blown closed cell foam ($5 - $5.5o per square foot ) would deliver R27-R28, and re-using the existing R38s compressed into the remaining 5.25" would deliver another ~R22, for a total close to the code min R49.
If 2x12s going with 5" of HFO blown closed cell foam would deliver R34-R35, and compressing the re-used R38s into the remaining 6.25" adds another R26-R27, bringing the total to a bit north of R60.
https://s3.amazonaws.com/greenbuildingadvisor.s3.tauntoncloud.com/app/uploads/2018/08/08062722/Compressing%20fiberglass_2-700x310.jpg
Thanks for your reply.
In regards to the heating system. This winter, it very rarely used the auxiliary heating strips to keep the house warm so I was thinking the same thing that it should be fine, but thought it would be best to ask. My plan was to tie it in with some shutoff dampers inline and if I find it does over tax the system, I can shut it off and install a mini split system later down the line and only be out a few hundred bucks on ducting material.
In regards to the walls. I thought what they had done was pretty good with the exterior foam board to eliminate the thermal bridging, but as you say it doesn't even meet the code. The foam is wrapped in typar and then the vinyl siding. I do know that the interior was painted with vapor barrier latex paint. Apart from ripping down all the sheet rock to insulate from the inside or the siding to add more foam on the outside is there anything else I can do retroactively? I was scheduling a blower test before I did any of the attic insulation changes anyways just to see where I stood with things. It seems more pertinent now.
With regard to the attic spaces, I agree with you on the open cell foam. I was skeptical myself and even the questioned the guy but he said it was cheaper that way. All the rafters are 2x12.
>"I thought what they had done was pretty good with the exterior foam board to eliminate the thermal bridging, but as you say it doesn't even meet the code. The foam is wrapped in typar and then the vinyl siding. I do know that the interior was painted with vapor barrier latex paint"
There is no way to "...eliminate the thermal bridging..." short of using studs that are made of insulation. A 5.5" deep stud cut from Eastern Hemlock or other commonly used species is about R1.2 per inch or R6.6. Installing R3.8 over that only cuts the heat flow through the framing by about a third. As the XPS loses it's (climate damaging) HFC blowing agents over a few decades the performance will drop to about R3.2, so over the long term the improvement on the framing fraction will be less than a third. It's better than no exterior insulation, but not a high performance (or code minimum ) assembly.
The vapor barrier latex will help. At 3/4" the exterior XPS runs about 1.5 perms, and the vapor barrier latex is about 0.5 perms, so the sheathing should be able to dry adequately into the air behind the vinyl siding.
>"Apart from ripping down all the sheet rock to insulate from the inside or the siding to add more foam on the outside is there anything else I can do retroactively?"
It's baked into the cake now- the most cost effective thing you can do to the walls at this point is to find and fix all the air leaks with blower door and IR imaging directed air sealing at the same time that you go after it in the attic space.
Unless the foam guy is really hungry (and at $10K it doesn't sound TOO hungry) going with 10" /R37 open cell foam and Intello Plus as an interior side vapor retarder isn't likely to be the most cost effective solution. At just 2" of closed cell foam the roof deck itself is pretty safe, but doesn't provide enough dew point margin for more than R13 of fluffy stuff in your climate. Filling the remaining 9.25" with the compressed R38s, cellulose or open cell foam with Intello on the interior to keep the fiber (or open cell foam) insulation dry could work, and hit pretty close to the code minimum R49, but there are no really cheap solutions to unvented cathedralized ceilings. See Table 3 in this document regarding the relative safety of the roof deck:
https://www.buildingscience.com/sites/default/files/migrate/pdf/BA-1001_Moisture_Safe_Unvented_Roofs.pdf
Take a look at the column labeled "2" ccSPF + spray fiberglass" and the row labeled 6A Minneapolis. Unless you have a "cool roof" type roofing material the roof deck will stay pretty dry, but it'll take a smart vapor retarder to keep the fluffy stuff dry. Air tightness of the ceiling becomes much more important when there isn't enough closed cell foam for dew point control at the foam/fiber boundary.
Thank you for your knowledgeable replies. It will be something I keep an eye on for sure. In regards to the closed cell on the roof deck, there won't be any conflict with the zip sheathing they used sandwiching the panel between two air barriers and not allowing it to dry inward or outward?