Installation cost of foam in ceiling vs walls

Getting ready to start construction on a new house. Talked w/builder today to go over energy specs. We have a “1.5” story house. By that, I mean one “half” of the second floor is bedrooms, the other “half” is conditioned/insulated attic space.
We are at the north end of climate zone 3. Current plan is R-6 polyiso exterior rigid foam. Either a BIBS system or open cell spray foamin the 2×6 wall cavity (puts us at ~R-24 for the whole wall). Builder was asking what we wanted to do to get to R-38 in the ceiling. I said my idea was 1″ closed cell foam for a vapor barrier, and then either a blown insulation or open cell to fill the rest of the rafter cavity. His comment was that in the walls, open cell spray foam wasn’t particularly more expensive than the BIBS, but in the ceiling, the cost of the spray foam went up due to install costs. Does this sound right? Or could it be that the price he’s getting from his insulation sub is due to him quoting open cell in the walls and closed cell in the ceilings?
Also, what route would you all recommend? It seems to be that the 1″ of closed-cell is a necessary step as a vapor barrier for my conditioned attic, am I right? After that 1″ of closed foam, what would be the best route to fill the rest of the cavity? More closed cell (seems overly expensive)? Open cell? BIBS or dense pack cellulose?
Thanks in advance!
Matt
GBA Detail Library
A collection of one thousand construction details organized by climate and house part
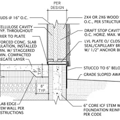
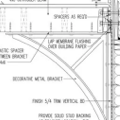
Replies
With a 1.5 story, if you are insulating the roof, then you don't need to insulate the knee walls.
The R6 of plyiso above the deck is just about enough for condensation control in your climate, a bit more wouldn't hurt to be safe for not much extra cost. The rafters can just be insulated with fluffy insulation. There is no point for any SPF under the deck. With a new build it is always better to design SPF out.
Make sure you tape the seams on your roof sheathing as the air barrier under the foam. You don't need a vapor barrier anywhere, but if you do want one, you can go with foil faced foam.
The important detail with 1.5 story is connecting the roof air barrier to the walls on the main floor. This can be done with tapes, but it is hard because the floor/celing joists poke through your air barrier. A bit of SPF (small two part kit) here is much simpler.
Sorry, I should've been more clear in my original post. R6 polyiso on exterior walls only, not the roof. I had enough trouble finding a builder here who would do it on the walls....they'd probably walk out the door if I pushed doing it on the roof. Sorry for not being clear on that.
So right now, walls = R-6 polyiso on exterior, BIBS in the 2x6 cavities. That gets me to something like R-24 for the total wall assembly assuming the BIBS is installed at the proper density.
Roof is still up in the air. I've attached an image of a profile view of the second story to give a better idea of what I'm talking about. 12" rafters. Since we're not getting any insulation above deck, I thought 1" closed cell + 10" of BIBS would get me to R-44 in the cavities. Would that be an acceptable solution? Builder indicated they don't normally do BIBS in ceilings. Is that true (I'm not overly familiar with BIBS)? Our architect had suggested 1" closed cell + dense pack cellulose. Thoughts on the best combo there?
BIBS can be installed in the ceiling, the contractor just might not like to do it as it require working at height. Cellulose is the greener option plus it does add some moisture management benefits, but it tends to be more expensive and fewer installers do it. Generally batts are the cheapest option.
Your roof assembly with flash and batt should work quite well. I would bump up the SPF to around 1.5" as it provides a bit more safety margin for condensation control. Make sure they take the SPF down to the top plates on your exterior walls for air barrier continuity.
There is no point in going above code for R value for the roof, there is very little energy savings especially with the thermal bridging of dimensional lumber rafters.
If the roof is not yet built, going with TJIs for the rafters gets you a ~15% increase in assembly R value because of reduced thermal bridging. In my area they are about the same price for longer length, so not a big cost difference.
The R19 insulation in the floor above the porch is pretty low, I would aim for that to be higher, even better install some of that R6 rigid under the joists and above the porch ceiling. A good air barrier there will make a big difference for leaks and colder weather comfort. T&G can be easily nailed up through the foam with 2.5" nails.