Installing Rockwool Batts in unvented warm roof assembly with I-joists

Hello All,
I am getting close to the point of installing R-30 (7 1/4″ thick) Rockwool batts (already purchased and on site, so no change to product selection at this point…) into my warm roof assembly. This is a low slope (2:12) roof which from exterior to interior is as follows:
Standing Seam Metal Roofing
Continuous Ice and Water Shield
Zip Roof Sheathing with seams taped (also wraps around all assembly (fascia and soffit to the wall sheathing)
3″ Polyiso Insulation (2 x 1-1/2″ sheets with staggered seams)
Advantec sheathing as roof deck (surprisingly cheaper than OSB at the time of purchase…)
In framing a large part of the roofing, we decided to use I-joists (11 7/8″ tall) – 16″ OC. Of course, what I am now finding out is that the Rockwool Batts don’t install as easily as I thought due to the flange and web structure of I-joists – the space is now slightly wider than the width of the batts so no friction fit. Also the flange prevents a tight fit against the roof deck. While I’m not a great fan of the steel wire insulation supports, trying to use them is problematic due to their 16″ width (actually 15.5″) being too short. I’ve experimented with cutting down 24″ ones, but this is a pain, and honestly, I’m not sure I like using these.
So I’ve been doing a lot of research relating to 2 major questions:
1. Just how important is it in my particular assembly for the rockwool to be tight to the roof deck sheathing. At first I thought this was essential, but I find conflicting information saying that that while ideal, this isn’t as important as the whole interior assembly being air tight all the way to that having an airspace above the insulation is actually better. If I could just have the batts rest on the bottom flange that sure would be easy, but then I’d have 4″+ of airspace between the batts and the roof deck.
2. Assuming that I do need to get the batts tight to the roof sheathing, what is the best (as well as easiest for one person) to do this. I’m experimenting with stapling webbing or plastic strapping or bending the 24″ wire support into a square U shape (4″, 16″, 4″).
I’d appreciate any answers or feedback on the above questions with which I’m wrestling. I really would want to avoid having to add in some other product and/or alteration of the batts. I’m intrigued by using the Pro Clima Intello Plus membrane, but was/am planning on using Drywall as my interior air barrier.
thanks!
Carl
GBA Detail Library
A collection of one thousand construction details organized by climate and house part
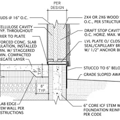
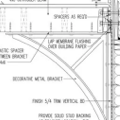
Replies
If you have extra 2x4 rockwool, you can try ripping them in half to fill either side of the web parts and hopefully that will provide enough friction to keep them up. It's an extra cost but it's better than nothing. Another idea would be to staple up netting at the underside of joists (progressively) and shove in insulation filling the entire joists space up. This is also more insulation than it looks like was planed for, but still a solution.
I can't say much about haveing a 4 inch gap under the sheathing other than I'd be worried about moisture condensing there. Others on this forum can talk more intelligently about it.
Jamie
You could buy some Rockwool Comfort board rigid board insulation. You can get it in various thicknesses and densities. We used 1" Comfort board 80 for our roof baffles in a vented assembly. You could rip (or cut with insulation knife) down a 1" board and adhere it to the underside of your roof decking to fill the void between the flanges on top. You could also install rips along the I-joist webbing on one side to narrow the void and give you a friction fit for your comfort batt material. The comfort board can be adhered with Dow Super 77 spray adhesive. It works surprisingly well. It's a little fussy in the install but you can rip all of the pieces at once and it should go up fairly quickly.
If you want a tight fit between the webs, you can order batts made for metal studs. They are a bit larger.
Dense packed cellulose would be an easy solution if you are using intello on the interior.
The problem with the air space is you can create convective loops through your insulation.
Yeah, I just found out about that a little while ago - but I've already got all the rockwool on-site (needed to order it 3 months ago to have enough for the job - Rockwool has gotten VERY popular...)
Another thing you can do is fill the web with some 0.5 inch styrofoam to get a tighter fit.
> Insul-Hold
Worth asking if it will work. Or adhesive sounds good.
As I see it, a top gap is an IRC code violation. Rarely a good idea, especially since I think your R ratio is lower than what code implies. Side gaps aren't a good idea either.
"5.1.2. ...In addition to the air-permeable insulation installed directly below the structural sheathing, rigid board or sheet insulation shall be installed directly above the structural roof sheathing ..."
I've also found a product called Insul-Hold (seems like maybe made by 2 different companies) that looks interesting. Not sure if it would hold these heavier/thicker batts though...
So this morning, I tried one of my ideas of bending a 24" wire insulation support into a 4-16-4 squared U shape (see pic). I then used this with a batt in the cavity. This seems to work really well. The slight compression puts enough pressure to push the batt to the roof deck. The 4" on either side (which rests on the top of the bottom flange make it a no-brainer to install. The squared shape doesn't put differing pressure across the batt width as they normally would. Also bending the support is alot easier than cutting them. So, I think this is the way I will proceed...
I bet I could even make a little relief cut 1" deep down both sides of the top lengths of the batt which would prevent that little gap by the flange.
Looks pretty good. I would get some 3/4" rigid or R8 rolls and fill in the sides. You don't want gaps around batts.