Insulate an existing concrete floor slab?

I have an existing ADU (in-law suite) in Portland, OR (Zone 4C). It’s part of a garage structure, sharing the same concrete slab floor. The stem wall extends 18″ deep below grade, and rises about 12″ above the floor. I’m preparing to remodel the ADU including replacing the carpet with new finish flooring (probably laminate planks).
My question is: Should I insulate the floor slab while I have the concrete exposed? I’m thinking of laying down foam above the slab and floating a new subfloor above it, as has been aptly addressed on this site. Or do I just leave it alone? I’m more interested in energy efficiency than comfort, as this is a rental unit.
My thinking is that in this climate, there’s a trade-off between the cold floor heat loss in the winter, versus the benefit of having a cooler floor in the summer. Would perimeter insulation on the outside make more sense? If som complications include the stem wall above grade, a sidewalk abutting the foundation on one side, and the garage sharing the slab. Thanks.
GBA Detail Library
A collection of one thousand construction details organized by climate and house part
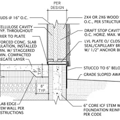
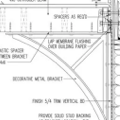
Replies
Gary, because concrete is a very good conductor of heat, in a situation like yours it's probably best to create a "bathtub" of foam inside the existing concrete. The IRC requires R-10 under a slab in your climate zone, and that's a good minimum target--at least 2.5" of EPS or XPS. You'll get lower energy bills, increased comfort, and an under-appreciated benefit: a low risk of mold and fungal growth.
If purchased new, EPS is a much better choice, due to the extremely damaging blowing agents in XPS. If you have a source for used XPS it's a viable option--just understand that the aged R-value is 4.2 to 4.4/in, not the R-5/in advertised.
Thanks for the input Michael. I hadn't thought of a foam "bathtub." It'll create an interesting 12" tall bump-out at the bottom of the walls, but definitely an option I'll consider.
>"The IRC requires R-10 under a slab in your climate zone, "
No, it doesn't.
The IRC requires R10 at the slab edge-only, down to either the footings or to 2' below grade, whichever is less. There is no under-slab requirement. See TABLE N1102.1.2
https://codes.iccsafe.org/content/IRC2018/chapter-11-re-energy-efficiency
In zone 4C (a heating dominated climate) it's still "worth it" on a lifecycle energy cost basis to install ~R8 (2" of EPS) over the entire slab. The deep subsoil temperatures in Portand OR are in the mid-50sF, which isn't exactly warm, but not super frigid either. The much longer/deeper heating season benefit far outweighs any summertime "free cooling" benefit. If it's possible to retrofit the code-min R-10 onto the exterior side of the stemwall that's worth it too.
For a second opinion, see Table 2, p10 of this document:
https://www.buildingscience.com/sites/default/files/migrate/pdf/BA-1005_High%20R-Value_Walls_Case_Study.pdf
For a slab-on-grade it would be fine to use 1.5" of polyiso rather than 2" of EPS under the subfloor, but not for a basement slab where flooding is possible or likely.
For a shorter term "payback" it may only make financial sense for 1" polyiso under the subfloor unless using used or factory-seconds goods at a steep discount. The greenest foam insulation is reclaimed foam or factory blems that would otherwise be wasted as scrap in a landfill or worse. There are several used-foam vendors in OR, some of whom advertise here from time to time:
https://portland.craigslist.org/search/sss?query=rigid+insulation
With used foam it's important to check thickness variations when laying it down for a slab-top application, since the nominal thickness is sometimes compressed a bit over time in commercial roofing applications.
Thanks so much Dana! One follow-up: you said the "exterior side of the stemwall." It's possible, but much more difficult than the inside of the stemwall, and I think less effective (because of the sidewalk outside, the stemwall insulation wouldn't go below grade, so there's a heat loss path from the soil to the slab inside). Did you specify outside stemwall for a reason, or are you onboard with Michael's "bathtub" approach?
Just to circle back on insulating the floor/stem wall. I plan to go forth with the insulation as recommended. Maybe not quite to code, but close (targetting 2 inches, so depending on the type...). So then any reason not to do polyiso in this situation? I know in the winter it's going to suffer from cold weather performance, but I'm thinking at the ground temperatures here it's still going to have higher-R than EPS. If the slab is dry, it should be fine, right?
Gary, IF the floor never floods, polyiso should be fine. But it absorbs liquid water so it's safer to use EPS. Or recycled XPS.