Insulate existing slab

I have a home in Sullivan County, NY built (I’m told) in 1994 on substantial slope.
The back side (down side) half of the house’s basement/foundation is above grade and has 2 bedrooms and a playroom, garage and utility room.
The floor on this lower level is a concrete slab. I don’t know if any insulation was used under the slab.
I would like to add insulation to the floor.
I am hoping to be able to add 3 or 4″ of XPS with a layer or 2 of 3/4″ CDX as a subfloor to vinyl flooring.
I can add a layer of polyethylene or epoxy as a vapor barrier immediately on top of the concrete but my concern is that IF there is insulation under the existing slab, will I be creating an area of trapped moisture (like we need to be careful to avoid in ceilings and walls)?
I understand that 4″ of XPS creates a nice degree of vapor barrier (not as nice as polyethylene). Would that be sufficient?
The reason I ask is because I am hoping to avoid having to attach the XPS and/or plywood to the concrete with mechanical fasteners. I would much rather use a construction adhesive or spray foam.
What would be a good way to proceed?
Thank you!
GBA Detail Library
A collection of one thousand construction details organized by climate and house part
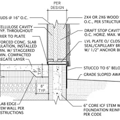
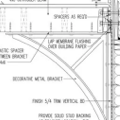
Replies
Can anyone let me know if it would be a mistake to put down 2, 2" layers of XPS with PL300 between the bottom layer and the concrete and between the 2 layers of the XPS?
No poly or other additional vapor barrier.
The 3/4" plywood on top of the XPS using nothing other than PL300.
Thank you!
Your plan could probably work well, but it's not something I've done or heard of others doing so you would be taking on the risk of using an unproved assembly. Walking on the subfloor will "squish" the foam slightly which isn't usually a problem, but if the only way the layers are attached is with construction adhesive, you're relying entirely on the bond.
A similar assembly that has been used enough that you can be confident in how it works is using two layers of sheathing, fastened to each other, floating above the foam: https://www.finehomebuilding.com/2005/03/01/the-no-mold-finished-basement?oly_enc_id=6011J5584489E1A.
XPS is somewhere around 1 perm per inch, and the perm rating is roughly cut in half when you double the thickness, so at 4" you'll have a perm rating somewhere around 0.25. That's pretty tight, but because vapor drive will likely be toward the interior, and you'll have rot-prone material directly above the insulation, I would not skimp on using a separate vapor retarder. In fact I usually spec at least 10-mil, rather than code-minimum 6-mil, for added durability.
4" of insulation is overkill for an unheated floor, even an 1" or so will make a huge difference in comfort.
The thing you have to watch with walk out basements is the slab on grade section can get pretty cold in the wintertime. This is less of an issue if the foundation has perimeter insulation but without that the slab is much colder than in a bellow grade basement. An uninsulated slab is heated by the house air in the winter time, once you put insulation on top of it the temperature will drop. What you have to watch here is the concrete not to go bellow wintertime house dewpoint, this generally not an issue unless you have humidity problems in the basement.
I'm going to disagree with Michsel statement about the poly. The problem with poly is any moisture that gets bellow the rigid (say from a small water leak) has no drying path and can load to mold over time. If you have enough moisture coming up through your slab to rot the subfloor you have bigger problems that need to be addressed in the first place.
Before doing any insulation, I would confirm that there is poly under the slab (make a small test hole to check) and it is always a good idea to check by taping down a piece of poly to check for moisture. Let this sit for a couple of weeks, If you get condensation under the poly, you have moisture issues that need to be fixed first.
You had hit on something that has been nagging at me but I couldn't express clearly enough.
If (more like "when") a spill or leak happens, will any water that finds its way under the finish flooring be trapped there if I put 6mil of poly immediately above the concrete?
Will it be trapped even without the poly if we use 2" (or more) of XPS?
Wouldn't it be prudent, therefore, to omit the poly regardless of whether a vapor barrier exists underneath the concrete? That is, if the concrete has a vapor barrier underneath, and we put another barrier on top, then the concrete is sandwiched between 2 vapor barriers and moisture will be trapped. If the concrete does not have a vapor barrier underneath, then adding one on top will prevent any dissipation of moisture (coming in from a spill/flood/etc from inside the house) downward. Where the vapor barrier characteristics of XPS comes into play is beyond me.
Thank you!