Insulated Mechanical Room

We are building a 16’x24′ Cabin. We may eventually add on a 26’x34′ portion, to create a complete small house. Climate zone 5B, in Skamania County, Washington. In the attached rendering, I’m only showing the portion of the stem wall that’s above grade. For now, the cabin will have a 83 1/2″ high crawl space. Later, I would like to create a 4′ x 10′ mechanical room (for solar control equipment, possibly batteries, and for a heat pump water heater). Creating a full, insulated walkout basement seems cost-prohibitive, and probably unnecessary. And would also require a radon fan.
-Could I add this small mechanical room later on, with insulated wood walls on 3 sides, and rigid foam against the concrete on one side?
-If so, what would you suggest for minimum r-value for the walls?
-Since headroom is limited, is there a low-profile way to create an insulated floor?
-If so, what would you suggest for minimum r-value for the floor?
Thanks in advance.
GBA Detail Library
A collection of one thousand construction details organized by climate and house part
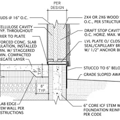
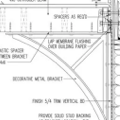
Replies
Miles,
I'm a little confused. It sounds like you are aiming for a conditioned crawlspace, in which case it would be coupled to your main living area and you'd would want to make provisions for mitigating radon. If the crawlspace will be conditioned and almost 7 feet tall, why not add a couple of feet and create a full basement? I'm not wild about basements, but building one might make more sense in this case.
Thanks Steve. On the one hand, I agree with you. But when I think about extra excavation, extra concrete, adding a slab, adding a radon fan, increasing the excavation to the full 16' footprint, waterproofing the stemwall, insulating the stemwall, insulating the slab . . . that sounds like thousands and thousands of dollars. And then once you create such a nice basement, you want to add windows. So more money for windows, concrete forming, etc.
Please see attached elevation, with one notable change; I will skip the stepped stemwall, and run the concrete stemwall all the way up to where it says top of wood stemwall.
Do you have time to take a stab at the questions above? Thanks, Miles
Note that you only need a radon fan if you're in a radon problem area. I assume since you mentioned it, you probably are in such an area, but wanted to point that out anyway.
It shouldn't be that big a deal to do some more digging if an excavator is onsite anyway to dig out a foundation. A lot of the cost of an excavator is just getting the equipment to the site. an Once you're on site, more operating hours isn't usually that big of a deal unless you have a LOT of extra work to do. Use the material you remove for fill somewhere else on the lot and you have no disposal or haul away issues to deal with.
Concrete work is similar, although a basement slab does have more finish work involved. It would be worth pricing it out with your concrete contractor though -- it might not be as much as you think, and a basement has many advantages (mechanicals, storage, etc.). Insulate the slab and foundation walls with reclaimed foam, XPS or EPS -- both are green when reclaimed! -- and you're not spending lots of money on new insulation.
Windows are up to you. You don't "need" any, so they shouldn't really be a negative on a basement. You could always plant some landscaping outside the exposed walkout basement walls to conceal the otherwise empty wall from the world, although I'd put a door somewhere for ease of access when bringing equipment in and out in the future. This is especially important if you're going to be using big batteries with a solar system because they are HEAVY. You also might find you need an exhaust fan for the battery room depending on the type of battery chemistry you decide to use. Since I design battery rooms at work, I can also recommend keeping your batteries in a separate room from your electronic equipment since there are many advantages to this.
BTW, you don't necessarily have to excavate an entire basement. You could always do a smaller area just for a mechanical space, but you'd probably find the cost savings wouldn't be as much as you might think. An "83-1/2" crawlspace" is nearly 7 feet, almost a basement already! Why not just go a little deeper and really make it a basement? This doesn't sound like a huge increase in what you're already doing, and you're going to still have to insulate things regardless per code. There are lots of reasons to insulate the walls and not the ceiling in a crawlspace, so you may find the insulation work isn't really any different in terms of cost.
Bill
Hi Bill, thanks for all of the advice. And good point; I'll check into the additional costs for excavation and concrete. Haven't been able to locate a source for reclaimed foam in my area yet. There will eventually be a deck above that tall stemwall, so it won't be very visible, and yes, there's a door there, on the tall side of the stemwall.
Good tip about batteries in a separate room - I hadn't heard that.
The purpose of separate battery rooms is to prevent any corrosive battery fumes from corroding electronic equipment. This is a problem when using lead acid batteries, especially the big flooded cells that are commonly used with off-grid systems. You normally keep the battery room at a slight negative pressure compared to the rest of the structure by running a small exhaust fan all the time. A hydrogen sensor is a good idea too to alarm in case of overcharge.
Bill
Thanks Bill, that makes sense. The wall between the battery room and equipment room can be normal construction (wood studs, sheetrock), right?
Yes, just detail it as airtight. Commercially, I just use 1 hour walls (1 layer of 5/8” type X drywall on each side of the studs). It’s pretty much just a basic wall, just be careful not to have too many open holes between rooms. Any small leakage will be handled by an exhaust fan if you keep the room under negative pressure.
Bill
I think a Heat Pump water heater needs more space than a 4x10 room.
Rheem calls for 700 cubic feet minimum, so the HPWH intake would need to be ducted to the outside.