Insulating 140 yr. old balloon framed building w/ brick facade

I am trying to come to grips insulating and air sealing a 3 story 140 yr old brick facade building with wood balloon framing.
The order of materials from the exterior is brick, 2″x5″ studs 1′ on center, 1″ sheathing (widths very from 6″ to 30″), vertical lath on top of the studs, horizontal lath (spaced for plaster key ways) and plaster which has been removed. There is no insulation currently in the building and the brick ties are two cut nails tacked into the exterior side of the studs and imbedded in the brick mortar joint.
We are in SW Michigan zone 5, approximately 6,600 hdd, and 34″ of precipitation per year.
I am looking for ways to insulate and create an air barrier while keeping the budget from blowing up.
One idea is to remove the lath and sheathing and install rigid insulation between the studs, batt or cellulose to fill the cavity and rigid insulation on the interior of the studs. Some sort of diagonal let in bracing would need to be installed for sheer.
I have not sat down and thoroughly thought this through but would welcome any suggestions.
The homeowner would like to avoid the use of spray foam insulation.
Thanks for your time and response!
Sam
GBA Detail Library
A collection of one thousand construction details organized by climate and house part
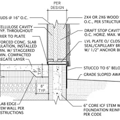
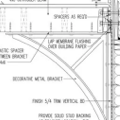
Replies
Sam,
Is the brick wall structural? Or is this a wood-framed building (with structural studs) with brick veneer?
If this is single-wythe brick veneer, you have to assume that the bricks will get wet every time it rains. That would mean you need an air space on the interior side of the brick. You could, perhaps, install a plastic dimple mat of some kind before insulating on the interior.
If it is a multi-wythe structural wall, you have to worry about possible deterioration due to increased wetting (resulting from interior insulation). For more on this issue, see Insulating Old Brick Buildings.
Martin, thanks for the response and will clarify.
Wood framed structure, single wythe brick veneer that does get very wet.
We are working to eliminate bulk water infiltration w/ tuck pointing and prop
er flashing details.
I understand that we need to leave an air gap between the brick and studs to allow for drying.
A dimpled mat may be difficult to install due the 1 ft. on center studs and cut nail brick ties which has me looking for a solution that doesn't involve doing anything between the exterior face of the studs and the brick.
I'm typing on my phone (not driving) so hopefully this makes sense and will keep it short.
Sam
Keeping the brick dry with proper shedding of bulk rainwater is indeed key. Only after the wall is able to deal with that, can we think about interior insulation, Airsealing and vapor control.
For multi wythe walls we have details available that avoid foam and use cellulose and a smart vapor retarder from foursevenfive.com (our company dedicated to foam free high performance) The intelligent vapor control allows some wetting (int or ext causes) to be absorbed/redistributed by cellulose and dry inwards. Outer wythe shouldn't be to porous/absorptive for this to work.
If a single wythe brick wall has a very low absorption value (a value) it will be able to stay dry too in most cases, with proper detailing (lintels, sills, cornices or roof overhangs). If the single white (or multi wythe outer brick) soak up rain readily, the risk of adding interior insulation increases (cool things dry slower)
You can test the absorption rate of exterior brick with a karsten tube to get an initial idea of its absorption rate.
The wall in current state can be easily evaluated - especially if the building hasn't been heated for a winter - the wall will clearly show moisture/elevated humidity levels in the brick on the interior. If the wall is humid, the nails would start to rust, and one could test the bricks moisture content (mass % of water) could be tested if interior insulation could be safely done.
Please feel free to contact us at [email protected] with specific question in regards to these
construction details and specific high performance foam free solution for retrofits like this.
Floris: Thanks for the info and your products seem very interesting but it looks like the construction details you provided pertain to 3 wythe brick structure where the insulation is in contact with the brick.
Assuming we eliminate bulk water intrusion from the exterior, insulate between the studs, and air seal the interior (which I haven't quite figured out where the 2nd and 3rd floor joist are nailed along side the studs and sit on a 1" x 5" horizontal let in brace) what do you think the long term effect on the exterior (brick facing) side of the studs?
Sam
A single whyte brick (as all construction) needs to not get soaked. A big roof overhang, and proper flashing will go along way. But low absorption values of the brick, especially close to the ground are important factors when internally insulating. The INTELLO Plus air and smart vapor control can help redistribute some of the unforseen exterior moisture that gets absorbed by the cellulose insulation.
Airtightness of the assembly is important, and the floor joist should be sealed. Question is, if they bear on the 2x4 wall (which would be preferable). It will take some diligence to get them taped tight, but this is far from impossible. So picture.
Floris,
You wrote, "A single whyte brick (as all construction) needs to not get soaked."
Of course it's a good idea to include roof overhangs that minimize the exposure of a brick wall to rain.
But all brick walls get wet, and all buildings are subject to wind-driven rain almost every year, and often every month.
If a wall assembly depends on the bricks staying dry, the wall assembly will fail -- because all bricks get wet.
Bricks can even take on copious amounts of dew , it's not just a rain wetting issue (though limiting the rain wetting is of course still primary.)
The building owner isn't going to like it, but 1.5" of rigid foam on the exterior with a drain-plane material between the foam and brick would allow you do dense-pack the cavities with a new-school fiberglass like Optima or Spider. With 12" o.c. full-dimension lumber 2x5" framing even in a balloon framed building the framing fraction is likely to be around 30%, and the thermal bridging of literally ANY cavity fill alone (even if you could get away with it, but you can't) wouldn't quite bring it up to IRC 2012 from an average U-factor point of view. With 1.5" of foil faced iso (R9) on the exterior and a R4/inch high density fiber in the cavities you'd be running a respectable whole-wall R of about R21 (assuming 30% framing fraction), and there would be little wintertime moisture accumulation in the brick to rot out the stud edges. If you go with XPS it'll still work from a moisture point of view, but will only run about R19 whole-wall.
I'm reluctant to recommend cellulose in this app, but if it can be determined that there is little or no "rising damp" moisture wicking up the brick from capillary forces cellulose might be used in place of high-density fiberglass.
Blowing fiber into a balloon framed wall usually requires blocking the joist bays to keep it from filling up the floors too, but most insulation contractors are already aware of this.
Hanging rigid foam to masonry can be done with 1x furring through-screwed into the masonry at least 1.5", 24" o.c.. If the pointing is in rough shape it may be worth cleaning it up a bit and applying a sacrificial parge of lime mortar to preserve the integrity of the older mortar. (It'll be moving a lot less water AFTER you've covered it with a drain plane/weather-resistant barrier, and put a foam warming blanket over it.) Even fiber cement siding can usually be nailed to 1x furring with ring-shank nails (of an appropriate material) for reasonable retention despite the shorter penetration.
Serious consideration has to be given about how windows & doors are flashed when taking this route, and you may be well -advised to add better (preferable stainless steel) brick ties to keep it all from falling down in a mild earthquake- it's probably susceptible right NOW.
OK, the budget just exited Mars orbit on it's way to the asteroid belt ... :-) Bottom line, there's no cheap way out, but you CAN get there from here.