Insulating 1860s home when getting new siding

I am residing my 1860’s home in the Chicago area, zone 5. It has no sheathing, only open cavities and tar paper under the existing siding. Inside I have plaster and lathe walls with multiple coats of paint. What is the best way to insulate this when residing while not causing moisture problems?
My plan is to remove all the siding. From the outside I plan to install Kraft faced insulation in the cavities followed by either OSB / plywood or a foam board of some sorts. After that will be Tyvek Drain Wrap followed by LP smart siding. Any suggestions on if this is the correct way to insulate or is there a better way to insulate while controlling moisture issues for an old home?
I have considered spray foam but due to cost I am looking for a lower cost solution. Thanks
GBA Detail Library
A collection of one thousand construction details organized by climate and house part
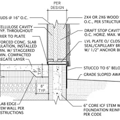
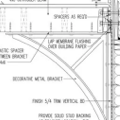
Replies
First verify that there is cross bracing, and that the siding isn't structural. Standards in 1860 aren't the same as what's in today. Exterior OSB or CDX can add that structure (if needed), and can be detailed as a robust air barrier.
How deep are the studs?
Are the studs on a standard 16" or 24" spacing, or are they somewhat random, or some other regular but not standard spacing?
Hi DR1 - (be great to have a name for all of us in the GBA community to use for you)
Dana has it right: you have a great opportunity to install an exterior continuous air barrier. That could be detailed with the housewrap but I prefer rigid air barriers so taping/sealing your exterior sheathing is the way to go.
Peter
Thanks, I am Dennis R, but when I tried to use that it said it was in use so I used initials.
After relooking at my pictures of the small section I had opened up...
- I have sheathing on the inside, could be tongue and groove, 3/4" thick?
- stud depth 4"
- stud spacing on the one was 17" open space
so my current build up from the inside is: Paint (probably oil based lead & latex)-- Plaster and lathe -- wood sheathing -- air -- tar paper - wood siding
Proposed Future: Paint - Plaster and lathe - wood sheathing - fiberglass insulation (kraft faced or unfaced ??) -- rigid sheathing (OSB / plywood or foam board) - Tyvek Drainwrap - LP Smartside siding
Any suggestions on insulation if all the stud bays are 17" wide or vary in width?
Thanks
Dennis,
If your studs are random spaced, the easiest option is dense pack (cellulose or fiberglass) or spray foam. If you are looking for DIY option, get mineral wool bats for 24" stud spacing, turn them sideways and cut them to the width of the stud bay. This way the off cuts can be re-used further up the wall.
The most important part with retrofitting old houses is dealing with flashing around windows/doors. Old houses don't usually have much which are mostly OK with open stud bays but will cause endless problems when insulated. Do not skimp on this.
Rock wool batts are designed for 3.5" or 5.5" depth, not 4.o". Compressing an R23 to 4.o" can work, but it's not an insignificant amount of compression. Fluffing a 3.5" to 4" won't have sufficient loft/spring to guarantee a full cavity fill.
And that's a LOT of batt-trimming detail to get right!
Blown cellulose is usually the best choice here, but verify and rectify any deficiencies in the window flashing. Cellulose shares the moisture burden with the structural wood, keeping the moisture content low, but it can also soak up bulk water incursions if the windows aren't properly flashed, which would be a problem.
So to verify, the existing t & g sheathing is on the interior side, abutting the plaster and lath, and the siding is nailed directly to the studs?
If yes, an exterior layer of half inch plywood or OSB works. Blown insulation can be installed from the exterior once the exterior is sheathed. In Chicago anything over 3.2lbs per cubic foot density isn't likely to settle, but shoot for 3.5lbs. Neither foam board or rigid rock wool is rigid enough to withstand the pressures of installing blown insulation, but the CDX or OSB provides that rigidity, as well as stiffening the wall against racking forces.
If the spacing doesn't line up well with 4'x8 ' sheets you may need to install 1 x 4 girts 16" or 24" on center to install the modern sheet goods, which fattens the wall by 3/4" and may become too thick for adequate exterior foam for dew point control without adding a lot of work to the trim detailing. If that's the case, skip the foam, but back-ventilate the siding with at least 1/4" of air to the WRB layer as a drying path for the sheathing. (Strips of 3/8" plywood nailed to the sheathing 16" o.c. would probably fly as the but run it by the local inspectors first, and take a look at the siding manufacturer's fastener requirements.)
Assuming you don't need the girts, 4.0" of cellulose (~R15) , if also installing exterior foam it's prudent to put at least R6 on the exterior in your climate. That would be 1" of polyiso which along with the half-inch sheathing adds a full 1.5" to the wall thickness. If using rigid rock wool over the sheathing and the siding is back-vented/rainscreened the exterior R matters a lot less since there is ample drying capacity toward the exterior. So it's a matter of just how much thickness can be added to the exterior without making a lot of extra work.
When a home gets to be this old please do not think of yourself as “the owner” but rather as the “current care taker” this home has outlived several owners and with luck it will outlive you and several more owners.
I like your plan to save energy, but you make it sound so easy. Please understand it will not be cheap or easy especially if you are keeping the original windows, doors and ornate trim. I do not know about your city and neighborhood but many have rules requiring approval of an historic commission, even if your home is outside of the historic district it would be a shame to strip an old home of all its character and leave some bland eunuch in your wake.
Modern high performance wall have not stood the test of time as your current walls have. The smallest flaw in a modern wall can easily lead to rot or mold, while a similar problem in your current wall would likely never be noticed.
The safest way to avoid moisture problems is to skip the foam board. Then the important thing is to get all the window and door flashing done correctly keeping the rain out of the walls after that keep the air from blowing thru the walls. So it is mostly about getting a thousands of little things right and if caulking is the only thing keeping the rain out of your walls you are doing it wrong.
I am not a big fan of Kraft faced fiberglass. Consider skipping the Kraft facing and have a look at unfaced or Rockwool.
Will you be updating the wiring while the walls are open?
Walta
Thanks Walter / Akos.
I agree that we are the current caretakers. We are trying to keep the originality and improve on it if possible. We do not have a historical society so we are not bound anything but we want to do it right for another 100 years.
After reading a lot on this forum, it sounds like I may not need the faced insulation for a vapor barrier. I want to make sure that I put in the best option for my situation. Is there an advantage of rock wool over fiberglass insulation?
I know I will have probably lots of things to do when the walls get opened up, fire stops if it is balloon framed etc. Our electric is somewhat upgraded but I may add outlets in some of the rooms from the outside.
Since we will be replacing the trim on windows and doors it will be a good time to insulate the rough openings (low expansion spray foam planned) and do a good flashing job.
I really appreciate your input. If you have any suggestions or recommendations please let me know.
Thanks
Dennis
Dennis,
Technically your layers of oil paint are a vapour barrier. I would check with local builders if they have had sheathing moisture issues after insulating.
If in doubt the safest is about 1" or more of rigid insulation on the outside. Adding on 1.5" would almost double your effective wall R value.
As Walter says "The smallest flaw in a modern wall can easily lead to rot or mold, while a similar problem in your current wall would likely never be noticed."
For those retrofitting an old house, would the vapor permeability of an exterior rigid rockwool (comfortboard) not add some significant fail-safe's to an otherwise 'high-stakes-at-every-detail' system of vapor impermeable foam over an old structure.
To what extent does this added drying potential to the exterior add tangible resiliency to a system that has stood for so long under a vastly different moisture management regime.
In other words, for those that are 'care taking' long lived structures and don't have the precise control one might have with new construction, is there enough of a benefit to exterior mineral wool that one should seriously consider its use over foam? (given that it costs more)
I have a hard time with the only description I have of your home “Chicago 1860” My mind’s eye I see a 3 story brick row house I know that is not what we are talking about so now I see a Victorian with a wide porch an turret again I think that is likely wrong. This may be one of those times where a photo is worth a thousand words.
If you were to fill the walls with R19 fluffy stuff you will have made a huge improvement thermally from 3 to R14 with very low risk.
If you add 1 inch of foam you from R3 to R17 but now you have moisture risk and you need to extend all the trim over the foam without letting in any rain that would make the wall rot. You get very little energy saving from 14 to 17. I see big risks and small rewards.
The 3 products you put in your question are all on my list of things best avoided.
1 Fiberglass insulation: It can be installed well and do a good job. My problem is it is so often not installed well makes it best just avoided.
2 House wrap: Same thing, it can be installed well and do a good job. My problem is it is so often not installed well makes it best just avoided. If flaps in the wind for months and gets full of rips that never get patched.
3 LP smart siding: This Company sold tons of this crap that is defective and is now swelling and flaking! Somehow they avoided and bad press and continue to sell this stuff while delaying all warranty claims for 20 years. When I bet they say it kept the house dry for 20 years so there is nothing wrong with the siding, who cares if it is ugly.
Talk to me about your plan to deal with the lead dust during this job. Are there any children living in this house?
I would like to see a plan with Hardy Plank siding, rain screen, Zip sheeting and fluffy insulation.
Walta
Thanks everyone for your comments. Let me try to answer some of your questions and ask a couple of new ones.
I have attached 2 pictures of the house, it is an old 2 story farmhouse that has a single story dining room and kitchen attached, it has a different porch put on several decades ago.
- the majority of the house has T&G sheathing on the inside. Some if not all of the single story has the sheathing on the outside. Not sure why but does. The single story is a similar vintage, it has a stone foundation and wood in the attic as the rest of the house.
- I have quotes from multiple contractors to do the siding. All recommended the LP Smartsiding product. Several talked about issues they have seen with Hardie siding. The best I could figure out is that LP has a much improved product over the older stuff.
- I will be having Hardie half rounds installed on the gables of the house. LP does not make any or are way too expensive.
- I choose to use Drainwrap over regular Tyvek. DuPont™ Tyvek® DrainWrap™ is a moisture barrier designed to provide enhanced drainage in areas subject to extreme, wind driven rain. It combines the superior air and water resistance, vapor permeability and strength of Tyvek® with a vertically grooved surface, to help channel water safely to the outside. LP experts agreed it could be a good alternative to my situation.
- All of the trim around the windows and doors are being replaced with LP boards. The crossheads above the windows will be replaced
- All siding will be removed by the contractor using appropriate lead precautions. We do not have children.
- I originally planned to do the insulation myself. Depending on the final design I may go with a professional insulating contractor if blown in insulation is the choice or for other reasons.
- Based on your comments I am leaning towards rockwool bats or similar vs. unfaced fiberglass. Are there other performance benefits when comparing the two?
- Walter what do you mean by R19 fluffy stuff?
- How much lack of performance or what issues will they be if I use 3.5" of insulation in a 4" cavity?
- Any recommendations on material for taping the sheathing? Windows and doors?
Thanks for your help
Dennis
Dennis,
That is a lot of wall to insulate by hand if you have to cut all the batts to size. You don't want 3.5" batts in a 4" wall (you can get convective loops from the hot to cold side, makes the insulation less effective).
If you do want to go with DIY, there is a 4" Rockwool AFB available (check commercial drywall suppliers). It is meant for metal studs, but if you are trimming to size, it doesn't matter.
Having said all that, I think in your case, blown insulation is much better choice. Cellulose does a decent job of sealing up the house as well.
Depending on your fuel costs, adding in more insulation might be a good return. It might be worth it just for the comfort (sitting by an R32 wall in near 10F weather and don't feel a thing). Whether it is extra furring for more insulation or OSB/CDX with foam or ZIP R, I think it will come down to what your contractor is comfortable installing.
As for fixing your stud spacing problem, I find the easiest is to add in the missing studs at 8',16' etc. (assuming your building code doesn't require staggered sheathing).
I'm weary of these magical drainage products for siding. Nothing beats a small air gap (3/8" plywood like Martin suggested).
While your working on the outside, you might want to insulate/air seal the floor and underside of your box window. Those are notorious in older houses.
For siding, lot of older homes around here go with EIFS. Gives you a "free" layer of exterior insulation and is pretty durable (you can get the EIFS guys to go even thicker than standard for minimal extra cost).
>- Based on your comments I am leaning towards rockwool bats or similar vs. unfaced fiberglass. Are there other performance benefits when comparing the two?
>- How much lack of performance or what issues will they be if I use 3.5" of insulation in a 4" cavity?
Batts are designed for 1.5 x 3.5' studs on either 16" or 24" centers, and don't really fit full-dimension 2x4s on random centers. The half-inch air gap easily turns into a thermal bypass path and/or a critter-condominium. Blown insulation is almost certainly going to perform better since it fills completely with no bypass paths around or through the air-retardent fiber. With a full 4" of fluff the thermal bridge through the framing is about R4.8. With only 3.5' it's about R4.2. That R0.6 difference may not sound like much, but it's about a 10% higher heat transfer rate through the fraction of the wall that is already the most thermally conductive.
Rock wool is completely fireproof- fiberglass melts. Fiberglass fibers are light enough that broken particles can stay airborne and enter the house air through infiltration paths. Rock wool does not. When all else is equal, rock wool is a generally better product.
DR1
When I look at your photo the original siding looks to be in reasonable shape. I know the photo is old and painting is no fun. When I look at the numbers, they do not justify pulling off the original siding.
I made a few guesses and made a BEopt model for different walls 2500 sqft in Chicago
No sheeting, no insulation= $2826
OSB, no insulation= $2775
OSB+R5foam, no insulation= $2425
OSB, R15 in wall= $2345
OSB+R10, no insulation= $2305
OSB+R5, R15 in wall= $2275
OSB+R10, R15 in wall= $2249
Please note these numbers are not just energy used but are energy used plus the cost of the improvement finances over 30 years. Given this is a retrofit your costs will likely be higher than ones used in this estimate.
Walta