Insulating a 1930s slate roof

Peter_Edworthy
| Posted in General Questions on
I’m planning to insulate the attic under the roof and want to check that I’m not about to create invisible issues in the process, e.g. trapped damp and rot.
The roof is slate over tar paper over 1×6 or similar boards with gaps between them. I’m confident enough air can make it through that assembly to ventilate the air gap without ridge or eave vents. Leaks are a fact of life with an old slate roof. Previously there was a layer of fiberboard across the rafters which has survived many decades of deflecting leaks to the soffits. Despite lacking any eave or ridge vents it has dried rapidly enough to not have been more than a slight annoyance. The house is in climate zone 5. Columbus Ohio to be more precise.
I’m going to be using a couple of layers of polyiso under the rafters so the part in the bays is going to need to dry to the outside. My concern is trying to create something that avoids wind washing, deflects bulk water to the eaves, and doesn’t trap moisture.
I plan to have a 1.5″ deep air gap under the roof with a 1/2″ asphalt-coated fiberboard acting as an air barrier and water-deflecting layer. I’ve drawn a diagram of what I’m thinking.
The detail of how the wind/water deflecting boards are attached to the rafters and each other is a particular area of concern. I only have access from the inside of the roof but ideally, the seal would be on the side facing the roof. I could run the spacers along the beam, smother the side facing the attic in sealer, and push the board into it. I worry that I wouldn’t know if there were gaps with that technique. Sealing from the attic side seems likely to create a channel that traps moisture along the edges of the boards where they aren’t very damp-proof.
For the obvious question “Why fiberboard?” it’s cheap, light, air-tight, vapor open, and easy to cut without a table saw/track saw. The largest downside that I see is that silicon sealants and foam don’t bond to it leaving only construction adhesive to seal gaps. I’m not wedded to it but I’m not keen on paying for a couple of dozen sheets of ply, carrying them all up the stairs, and cutting them with my circular saw. I have thought about something like a vapor permeable membrane instead but that leaves me with even more questions on how to seal it to the rafters and avoid the insulation pushing up and choking the air gap. I could try foam board in the bays but the general view of cut and cobble makes me doubt that all the hassle is worth it.
Let me know if there are more details that it would help to know.
GBA Detail Library
A collection of one thousand construction details organized by climate and house part
Search and download construction details
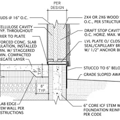
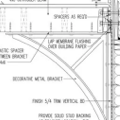
Replies
Deleted
Your approach to insulating the attic under a slate roof in climate zone 5, with specific considerations for moisture management and air sealing, is prudent. Here are some thoughts to help ensure you're not creating any unintended issues:
Ventilation and Moisture Management
Air Gap Maintenance: Your plan to maintain a 1.5-inch air gap beneath the roof is key to allowing for adequate ventilation and drying. This gap helps in managing moisture that might penetrate the roof assembly.
Wind Washing and Water Deflection: The asphalt-coated fiberboard you're considering can serve well for deflecting water towards the eaves and minimizing wind washing. Ensuring that this layer is well-sealed at the edges and joints is critical to its effectiveness.
Concerns with Fiberboard and Sealing
Sealing Challenges: You've rightly identified potential challenges in sealing asphalt-coated fiberboard. While construction adhesive can seal gaps, the concern about moisture entrapment at the board edges is valid. To mitigate this, consider using a combination of mechanical fasteners with washers to press the fiberboard against the rafters and applying a bead of sealant on both sides of the washer for a tighter seal.
Alternatives to Fiberboard: If sealing the fiberboard becomes too cumbersome, a vapor-permeable membrane could be a viable alternative. These membranes can be more easily sealed to rafters with appropriate tapes and adhesives designed for use with them. They also offer the flexibility needed to maintain the integrity of the air gap without the rigidity of board materials.
Insulation Strategy
Polyiso Application: Applying polyiso in layers under the rafters is a good strategy for achieving high R-values. Pay close attention to sealing the layers of polyiso to each other and to the rafters to minimize thermal bridging and air leaks.
Avoiding Cut and Cobble: While the 'cut and cobble' method has its detractors due to concerns about air sealing and thermal bridging, careful application and meticulous sealing can mitigate many of these concerns. However, your approach to use continuous layers of polyiso is generally more reliable and easier to air seal.
Additional Considerations
Roof Leaks: Given the nature of slate roofs and their potential for leaks, ensuring that any water that does penetrate can drain or dry out is crucial. Your strategy should include provisions for managing these leaks effectively without trapping moisture within the roof assembly.
Inspection and Maintenance: Design your assembly in a way that allows for inspection and maintenance. Slate roofs and their underlayment may require repairs, and having a way to access the roof structure without disturbing the insulation too much will be beneficial.
Final Thoughts
Your detailed planning and consideration of the unique aspects of your roof and attic space are commendable. Ensuring a continuous air barrier and managing moisture effectively are key. Given the complexity of your project and the specific challenges associated with older homes and slate roofing, consulting with a building science professional or an experienced roofer who understands the nuances of working with these materials in your climate zone may provide additional insights and validation of your approach. This professional input can help ensure that your insulation strategy enhances comfort, efficiency, and durability without compromising the structure or indoor air quality.