Insulating a Slab on Grade from Above

This could illustrate a reason to use a pseudonym, because I have lots of ideas and some of them may be half baked, but I’d like to invite commentary. Please take a moment to contemplate this one because there are some predictable knee-jerk reactions. The question is about an insulated slab on grade, which has previously been thus (from the top): 4” concrete >> 4” EPS >> Stego wrap (or similar vapor barrier) >> 4” gravel bed. The concrete slab was going to be exposed. The reason the vapor barrier goes below the foam is that EPS can absorb moisture, and avoiding XPS is a design goal.
There are a few issues, including thermal bridging around the perimeter at the stem walls, and some interior columns and shear walls that require the slab to thicken and rest on a footing (no insulation below the slab there). The stem walls get insulated from the outside, but they’re not very tall and the footings are a heat sink.
Another issue with the slab on grade is that it fails Stewart Brand’s concept of Adaptability. To repair or relocate a pipe is trouble when there’s reinforced concrete to break and excavation required. A crawl space is better, by this reasoning. However there are two factors that prevent doing that here: first the height limits (can’t go up) and second the proximity of two large trees, which according to an arborist will be okay but excavation should be minimized. There are no ducts in the building so a crawl space never seemed particularly useful.
Getting to the question, here’s a new proposed floor assembly, from the top: wood floor >> plywood subfloor >> treated 2×6 joists >> 4” concrete >> vapor barrier >> gravel bed. The 2×6 floor framing rests directly on the concrete, which gets waterproofed from below but can also have a covering of poly with taped seams. Between the 2×6 framing, how about some rockwool, and apologies for mentioning the stuff again but it seems like a good solution. This floor is kind of a crawl space with zero height. The question is whether this makes sense to the other BS artists (building science, that is).
With this assembly, adaptability improves because renovation doesn’t require breaking any concrete. Services can run through the framing. Thermal bridging is no problem anywhere, and there’s no risk of a chilly concrete floor. There are actually heated floors upstairs but not at the ground level, most of which is an accessory dwelling below the main house.
A variation would be 2×4 sleepers laid flat over 4” EPS over concrete. That wouldn’t change much thermally compared to the 2×6 floor, but it might be less adaptable. It would seemingly reduce concern about rising damp. Compared to the original floor, it adds the sleepers, plywood and wood finish in order to address thermal bridges, which it does by relocating the insulation above the slab.
GBA Detail Library
A collection of one thousand construction details organized by climate and house part
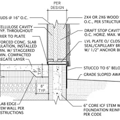
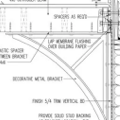
Replies
Thomas,
Many builders have done this, typically when converting a garage into living space. As long as you have done a careful job addressing moisture issues, so that the slab is dry, it works.
Thomas, I love half baked ideas
maybe someone else can finish baking it for you
Lstiburek says "The Best Crawl-space is NO Crawl-space"
I don't think the adaptabilty aspect makes sense for plumbing because there is not enough space to get traps and drainage.
I also don't see a need for treated wood ...
A capillary break seems more important
Are you proposing this as a method of combining slab construction with the adaptability of a framed floor and crawl space? If so, the problem may be that there's not enough height for plumbing traps or drains with grade below your wood subfloor. You'd still have to go into and under the slab for that.
What's more likely in my mind--assuming you can excavate--is to pour your stemwall as usual but then hang the floor joists from the mudsill. That minimizes the height of the floor and you have room for pipes.
For this to address Adaptability the depth would need to increase, at least a 2x8 in place of a 2x6. My first reaction to a 2x8 cavity under the floor is that it’s more than the R-value needed for the climate, but of course that's not what the Passive House crowd would say. The closest examples of PH projects have 8" and 9" EPS in their floors. That's a separate debate though. Going to 2x8s wouldn't be a problem for excavation, because the floor assembly would still fit above the footings.
Is the main goal to substitute EPS for XPS?
David,
I've discussed my wall and roof assemblies in other threads and described the apparent advantages of rockwool vs. rigid foam for those applications. In this case it took a while before a non-foam solution came to mind, and there aren't quite the same technical advantages but the Adaptability issue does seem meaningful. Mostly my intent is to make clever design decisions and solve actual problems rather than creating new ones. Thermal bridging was the the motivation to turn the ground slab upside down. Foam plastics aren't particularly desirable as a substance and XPS is worth avoiding, which is possible but presents some design issues to resolve.
To call a wood floor over plywood Adaptable isn't necessarily realistic, because it's not easy or painless to get inside there from above. That's the value of a crawl space. At best this is an in-between state, where a major renovation avoids becoming any more major and should avoid conflict with the structure.
As others have noted, even 2x8s wont offer enough space to plumb a toilet (3" sweep and waste pipe with ¼"/foot slope).
And you're effectively creating two structural floor systems: concrete and repetitive wood framing. Martin's statement that this works in garage renovations is no reason to use it for new construction. The topside foam board and sleepers is both more sensible and resource-efficient.
This idea seems to be in response to the following concerns:
These issues are commonly and easily addressed. If the slab is poured inside the stem walls, then slab edge insulation (with beveled top if necessary) addresses lateral thermal bridging. Monolithic slabs can be poured on top of 25 psi foam board, including thickened footings at perimeter and intermediate bearing points. And even a conventional footing-under-stemwall can be poured on top of 25+ psi foam (a typical 2-storey house with center bearing places about 10-15 psi load on a 16" wide footing (3/4-1 ton per square foot on the soil).
'
Lstiburek is a stand-up comic, too. He often says things for their attention-grabbing value.
When contemplating the millions of mushroom-growing crawl spaces in the US, his statement has some merit, but when considering adaptability and incorporating the BS principles which can make a crawl space functional and safe, then his blanket statement is meaningless.
Insulating above the slab is easier because of simple geometry--just a flat surface. The foundation underneath includes a number of footings of different depths. To fully wrap insulation below those would be quite complex and use a lot of foam. A real thermal break between the stem wall interior and the floor slab would make a visible gap, with an exposed concrete floor. Maybe the best solution is to mostly ignore adaptability because there's not going to be a crawl space, and just address thermal bridging by placing EPS above the slab and then 2x4 sleepers to support a finish floor.
It's too bad about missing the opportunity to grow mushrooms in the crawl space. That will have to wait for another project.
Robert,
I thought you preferred to build without a crawlspace?
Perhaps you have a different image in mind than I do, but - again - both of these solutions are used routinely and are not complex at all, unless you over-complicate the footing design.
Here is a picture of a thickened edge slab with thickened center footing (looks like a combination of XPS under the footings and EPS under the field of the slab:
http://www.sucasamagazine.com/contents/Spring08/features/green_materials_gallery/fullsize/greenmatelim_fs.jpg
And here is a graphic of beveled slab-edge insulation:
http://www.architectureweek.com/2001/0307/images/11319_image_5.150.jpg
John, I wasn't talking about my preferences, but merely commenting on the adaptability/accessibility issue of slab vs crawl.
I do think crawl spaces are foolish, unless perhaps you're building where there is ledge (bedrock) close to the surface. My preference would be either a slab on grade (inside of FPS grade beam) or full basement. But I would not use a slab unless it could do triple duty as finish floor, radiant floor and solar thermal mass.
Up here, if you're going to dig down 4-5' for a frost wall, it's silly not to go the extra 3' for a full, usable basement.
Here's another variation on the proposed assembly: place the slab 16" below floor level, 10" below grade. Build the interior floors using something like a Larsen truss, to lift a plywood subfloor some 14" above the slab. That's enough space to run the plumbing, and doesn't require too much framing material. The floor cavity could hold R-50 insulation.
That'll work. But it wouldn't be a Larsen Truss - it would be a conventional parallel-chord floor truss with diagonal web members. It would be a top-chord-bearing truss, however, which requires lateral bracing perpendicular to or 45° to the bottom chord to prevent lateral shimmy.
The second house I built on a community land trust in rural TN in 1983, after the 8" double wall Warm & Dry, was a prototype panelized design created by the Tennessee Valley Authority for low-income housing. The TVA engineer who brought the 4' oc doubled 2x4 top-chord-bearing trusses that we capped with 1-1/8" double T&G plywood insisted the floor was strong enough for an elephant to walk on.
Well, when the homeowners moved in and put their washing machine on a somewhat unbalanced spin cycle, the entire house shimmied like a stampeding herd of elephants. The problem was eliminated with a three runs of perpendicular bracing on the bottom tied to the gable walls.
The whole project went like that. When the TVA architect and engineer showed up on site (to be helpful, the said), the first thing they did was nail to a tree a huge metal sign of Murphy's Laws - and every one of them came true.
The roof trusses, also double-wide 2x4, were 8' oc and we had to fabricate roof/ceiling panels of 3/4" plywood, stained on the bottom, with 2x10 girts attached on top perpendicular to the trusses to carry the span. The fiberglass batts went in from the top and then the corrugated sheets of asphalt roofing (Onduline) that they spec'ed. It was fun getting sheets of finished 3/4" plywood with four attached 2x10-8s up onto the trusses.
There was no roof sheathing above, so we couldn't walk on the Onduline without either breaking it (if it was cold) or bending it (if it was warm), and it had to be attached with 3" gasketed nails through the high points.
This was designed by this architect/engineer team, but there was no wind bracing to keep the on-edge girts from racking and tearing the nails out of the asphalt sheet. There was also no provision for a ceiling vapor barrier (in those days, we went crazy with butyl caulked poly), so I had to cut 14.5" wide strips and caulk them to the bottom of the roof "troughs" before insulating.
And then I made a zig-zag truss on the top edge of the girts with baling wire to prevent or at least limit wind racking.
The wall panels were also 8' long with the "studs" horizontal and pre-finished with foil-faced foam board and sideways T-111 siding!
And to think we've trusted the TVA to build and run nuclear power plants!
Robert, I was thinking the floor trusses would rest on the concrete and just serve as a spacer to lift the subfloor. The slab would be a pretty good lateral brace for the bottom chord.
Thomas,
I don't like the idea of a slab 10 inches below grade in a closed crawl space with zero access. If the slab ever gets damp -- highly likely since it's below grade -- who's going to see what's going on?
If you're going to create a below-grade crawl space, make it high enough for someone to enter and perform maintenance.
Martin, point taken. The plumbing would need to drop below the foundation anyway because 10" below grade isn't deep enough to run the water main out toward the street. If plumbing runs below the concrete then the floor assembly should be the minimum thickness needed for insulation, not 16". EPS over the slab also makes sense, and the slab can be slightly above grade.
Here's a link to a Passive House project in Oregon, with some interesting enclosure drawings: http://www.rootdesignbuild.com/blog/passive-house/air-tightness/#more-680
There are many points of difference between the drawings in the link and my project, but the thing that's making sense is having a monolithic slab and perimeter grade beam and then insulating entirely from above. No insulation on the exterior or underside of the concrete simplifies the interface with the soil and avoids any hazard of insects or critters. It reduces the surface area of insulation, and avoids thermal bridging.
Hah! The water main runs in from the street. Your water is going to flow backwards. ;-)
Ah, well you may have a point. But you plug a power cord IN to the wall socket, even when the current flows the other way. The act of connecting is performed from the site toward the street.