Insulating a *vented* cathedral ceiling

Hi all,
I’m in a bit of a unique spot, and having read (and re-read, and re-read again!) Martin’s article, “How to Build an Insulated Cathedral Ceiling,” I have a couple of options and I’m wondering folks’ thoughts on the best option.
First, my situation:
I’m building a two-story structure (in Climate Zone 6) with a garage below and a loft living space above, with a simple 8:12 pitch gable roof (with no hips, valleys, dormers, etc.) with 2×12 rafters at 16″ on center. The roof is screw-down metal panels with a vapor-impermeable underlayment (the lumberyard specified the underlayment and the framer used it before I knew about it). Because of the vapor barrier underlayment, I am going to use a vented assembly so the roof deck can dry to the underside, since the vapor barrier will prevent it from drying to the top side. Therefore in order to vent the roof assembly I’m planning to use rafter vent baffles all the way from the soffit vents to the ridge vent.
In terms of insulation I would like to use at least some 2-lb. closed-cell spray foam since not only will it provide R-value but will also serve as an air sealant to prevent air leaks, which will also avoid the need for an air-sealing membrane (which I’m not confident of detailing the installation of which well enough for it to actually serve as an effective air barrier).
That said though, I understand that the thicker spray foam is installed, usually the worse the quality of installation (I’ve read a number of places that installing more than 2″ in a single pass is unadvisable due to shrinking, cracking, etc., and all of the spray foam subcontractors I’ve spoken with say they would spray 5″ at a time!). Given that and the high cost of spray foam, I’d like to install as little spray foam as possible and fill the rest of the cavity with mineral wool, essentially using a “flash and batt” method in my roof assembly under the vent baffles.
I understand that I need to install enough spray foam to accomplish two things:
– provide a good air seal; and
– prevent moisture build-up in the roof assembly.
Based on Martin’s article, “Calculating Minimum Thickness of Rigid Foam Sheathing,” I think I understand that I need R-25 of rigid foam to prevent moisture buildup. If that’s the case, that’s about 3 1/2″ – 4″of rigid foam.
Is that correct? Or can I get away with less?
Thank you very much for all of your help!
GBA Detail Library
A collection of one thousand construction details organized by climate and house part
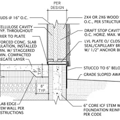
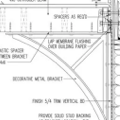
Replies
Chris,
Your question is confusing. Do you plan to use spray polyurethane foam or rigid foam? Or both?
If you want to install spray foam on the interior side of your ventilation baffles, I think that open-cell spray foam is safer than closed-cell spray foam. Vapor-permeable insulation is acceptable in your roof assembly, as long as you have a ventilation channel under your roof sheathing.
If you take my advice, all you need is enough spray foam to create a decent air barrier. If you use open-cell spray foam, that means that you need is about 3 inches of spray foam -- or 5 inches if you are very conservative.
For more information, see Air Leakage Through Spray Polyurethane Foam.
More than 2" of closed cell foam in a single pass is more than just a quality issue- it's also a fire hazard during the curing period.
Only at R49 center cavity with closed cell foam on the exterior side of the insulation layers you would need a minimum of R25. But with a vented roof deck you don't need the foam to be on the exterior side. Using open cell foam on the exterior side vapor-open to the vent channel would air seal as well or better than closed cell. It can be safely installed at 5.5" per pass, which is more than half the available depth.
If the vent baffles are vapor permeable you can go ahead and use only fiber if you wanted, no interior side vapor retarder necessary. If you wanted to use a layer of foam on the interior side for air tightness you can do that with as little as 3" of OPEN CELL foam at a fraction of the environmental impact. OR, you can use open cell foam against the vapor-open baffles as long as it's half the total R or more, again, no interior side vapor retarder necessary.
Your problem would be getting the R49 in a 2x12 rafter with a code-legal 1" vent gap (2" would be better.) A 2x12 rafter is 11.25" deep, less the 1" air gap leaves you at 10.25" for the insulation. That would require an average R/inch of R4.8.
Going unvented, with a skim-shot of 1" of closed cell foam on the underside of the roof deck and the next 10.25" being dense packed fiberglass (1.8lbs density minimum) or rock wool would get you to the R49 code minimum, but you would then need an interior side class-II vapor retarder, preferably a smart vapor retarder such as 2-mil nylon (eg Certainteed MemBrain, at about 15 cents per square foot, installed). This is NOT a disaster, and far cheaper & greener than another 3" of closed cell foam. The 1" closed cell foam by itself is a reasonable air seal and at less than 1.5 perms protects the roof deck even without interior side vapor retarders. Adding the 2 mil nylon limits the wintertime moisture uptake at the foam/fiber layer to miniscule levels, yet allows the assembly to dry much more rapidly than it takes on moisture.
Martin and Dana, thank you for the feedback!
Martin, I am planning to use spray foam for it's air-sealing benefits (could be either open or closed-cell, I hadn't even considered open!).
I hadn't even considered open-cell foam. I'm not very familiar with it!
- How does cost compare to closed-cell polyurethane?
- It sounds like open-cell foam is an air barrier, but NOT a moisture/vapor barrier? Is that correct?
I had been considering using plastic AccuVent baffles. Since they're plastic I imagine they are not vapor permeable. If it would be better to have a vapor permeable baffle, I guess I could site-build the baffle out of strapping and a thin sheet of luan plywood or MDF or something...
Assuming I used a plywood, MDF or other moisture-permeable baffle that would allow the insulation to dry to the vent channel, and assuming open-cell spray foam is also moisture-permeable, does that mean I could then use a small amount of open-cell spray foam as an air-sealant (say, 3 inches), then stuff the rest of the cavity with mineral wool, and be in good shape?
Thank you!
Half pound open cell foam runs about 30-35 cents per board foot (R3.7-ish) as compared to about $1.00- $1.15 a board foot for 2lb foam (R6-6.5-ish ) in my neighborhood. YMMV. That's about half the cost per R-foot.
Half pound foams typically run 7-10 perms @ R20. It's air tight, but vapor permeable.
With any vented roof deck scheme you won't be able to hit R49 in 10.25" without a higher R/inch than the ~R3.7/inch you get out of half pound foam. Even 0.7lb open cell foams only run about ~R4/inch, which would still leave you a bit shy at R41-ish for 10.25". If you did an air-sealing shot of 3" of 0.7lb foam you'd be at ~R12, but the remaining 7.25" would have to add up to R37, which is R5.1/inch.
You can't beat the geometry- you'll either need to qualify it on a U-factor basis or a whole-house performance basis, or go unvented with the flash inch of 2lb foam + high density fiber + smart vapor retarder to actually hit R49.
A full 11.25" of 0.7lb open cell foam unvented would get you pretty close to code min at ~R45 , using only as much polymer as 4" of 2lb closed cell. It's vapor permeance would be in the 3-5 perm range, about the same as standard latex paint, so you 'd still want the 2-mil nylon vapor retarder. It can be safely installed in two lifts of 5.5". eg:
http://www.icynene.com/sites/default/files/US%20content%20uploads/Classic%20Plus%20-%20USA%20Technical%20Product%20Data%20Jan%202015.pdf
Or, install 8" of closed cell foam under the baffles at $8 per square foot, and suffer the performance hit from the higher thermal bridging, using 8x as much polymer as the flash-foam + fiber solution, and a bunch of HFC245fa (unless going with Lapolla's HFO blown foam.) That meets code min, but is hardly the stuff of green dreams.
Okay, yeah, I understand the space limitations.
Fortunately (or unfortunately?) my code officer was going to be perfectly happy with me spraying in 5" of closed foam and calling it a day (that's only R32!), so I won't have any issues getting the building approved... but that said I still want to do the best job I can!
So maybe then I get 5 inches of half-pound open-cell sprayed in (since it can be done in one lift) for a good air barrier and ~R18, then fill the remaining ~5 inches of the cavity with R23 mineral wool for a total of R36 with a good air barrier and no HFC245fa?
I know R36 in a roof assembly in Climate Zone 6 is not good, not even hitting code minimum, but the place is only going to be a weekend/vacation place and likely won't be used much in the deep winter (and the rest of the building is going to be incredibly efficient... off-grid solar, minisplit heat pump, LED lighting, etc, so I can feel pretty good about myself, right? ... Right? :-P
Chris,
If you decide you want to have at least code-minimum levels of insulation, you can scab some gussets on your rafters and add some 2x4s on the bottom to deepen the rafter cavities, providing more room for insulation. Or you can install a continuous layer of rigid foam on the interior side of the rafters.
I hate to sound like a broken record -- I've written this many times before -- but you shouldn't plan to heat an off-grid house with electricity. It won't work. Trust me. I've lived off-grid since 1975. When you need heat, you won't have enough sun to keep your batteries charged.
The only two ways to heat an off-grid house are with a wood stove or a propane space heater with through-the-wall venting.
I just came across another blog by an off-grid homeower who wrote about the deep disappointment resulting from installing a central heating system (designed by an architect) for an off-grid house. Of course it drained the batteries instantly. He switched to a propane space heater after wasting many thousands of dollars.
Oh sorry, I didn't mean to suggest we were going to be heating solely with the heat pump, or powering solely from solar!
We're going to have a heat pump, backed up by propane heaters, backed up by a wood stove. For electricity, we'll have the solar array w/ battery array, backed up by an automatic propane generator, backed up by a manual gasoline generator (plus we have the option of a grid tie if we find that we want it)!
Re: the insulation, unfortunately because of the height limitation, we can't add anything to underside of the rafters other than the half inch drywall (the ceiling heights are really low as is)!
Chris,
I understand. I live this way. We all have a backup generator. (Generator fuel is very expensive. Better to burn the fossil fuels directly, in a propane space heater, rather than to charge your batteries and operate a minisplit.)
Don't buy the minisplit -- it's useless. Heat with an appliance that requires no electricity.
Or do it your way. Then write me an email after two winters have passed, and you can tell me whether or not you regret the minisplit purchase.
In a snowier zone 6 climate a mere R32-R36 is a recipe for ice dam issues, but if you went with 5.5" of half-pound foam plus R23 rock wool it would work just fine as long as the chutes are vapor permeable.
You can't really heat zone 6 house reasonably with off-grid solar and a mini-split, but you can probably air condition the place reasonably during sunny summer days, assuming that luxury is worth it for you. In sunnier not so cold places (say zone 2, Austin TX or San Diego CA) you can probably do the bulk of the space heating in a high thermal mass house with a mini-split without having to (ab)use the batteries much, but even there a wood stove makes more sense. Still, being on site to keep systems up & running is important.
An unpowered vented wall furnace under thermostat control is probably going to be the best bet for when you're not there. Anything that requires electricity can't be counted on, since you can't maintain & repair any issues the power when you're away either. The fewer "must-operate" systems in the freeze control chain the better! When you're on the grid the utility will be there to keep the power system up within hours or at most a few days, even if you're not there. When you're off grid you're on your own. Even with a huge surplus of soalr, when the PV panels get snowed on the daily output goes way down, and if drifting snow clogs the compressor on the mini-split with nobody around to shovel it out and clean it up you'd be out of heat.
But a cheap 3/4 ton mini-split can still be an asset in the summer, maybe even for daytime heating during the shoulder seasons, as long as you don't go nuts using it after dark.
What is the insolation of the site like? There's a big difference between going off-grid with solar in a Vermont forest vs a clear mountaintop in Colorado. You might not see the sun for months at a time in the former, while the longest sunless period in the latter might be only a few days max. Where I live, in zone 5 in New Mexico, I have never seen a period of time in the winter with no sun that lasted for more than about three days.
Chris,
If you are willing to connect to the grid, of course you can use a ductless minisplit. You'll also save several thousand dollars by avoiding the cost of batteries.
Here is a link to an article you might want to read: Site-Built Ventilation Baffles for Roofs.
Chris,
If you hook up to the grid, buying two generators is also overkill. There's another couple of thousand dollars of savings.
Grid power is much, much cheaper than off-grid power.
If the grid is available and not egregiously expensive, hook up to it! The environmental hit of using the grid is lower than the hit from manufacturing the amount of battery needed to use the mini-split, and the carbon offset and grid infrastructure benefits of your PV exports to the grid are also quite valuable, a better use of the resources and has greater benefit to both you and the world than an isolated one-house micro-grid.
Off-grid makes sense when extending the grid to your house costs much more than it's worth. If it costs $100K to bring the grid to you staying off grid may be appropriate, but at $10K, not so much.
With grid availability you can skip the fossil burners too. In most places the grid is sufficiently reliable that even a backup generator isn't really a rational purchase. With a grid attached PV reporting it's output online you'll know when the grid is down in your neighborhood and will be able to take appropriate measures if it's down for an extended period of time.
Hi all,
The NREL insolation value for my area is 4.26 kWh/m^2/day. It's not New Mexico by any means, but it's not bad. Also my building is located on a treeless hilltop, oriented due south. Unfortunately given that it's a brand new building I can't even estimate what the electrical usage will be, but it should be very low.
Martin and Dana, I'm really surprised to hear you advocate burning fossil fuels over the heat pump! If it's simply a matter of raw wattage consumption, I could easily (and cheaply) just use the grid... the utility lines are already there (and since Maine gets most of its electricity from nuclear generation, I wouldn't feel too bad about it).
Dana's points about the reliability of the heat pump are well taken, but our area doesn't actually get THAT much snow (so clogging the compressor 4-5 feet off the ground is very unlikely), and we're planning to shut the entire building down, drain the plumbing, and turn off the heat when we're not there in the winter. Given that, would you both still recommend propane heaters, or a grid-powered mini-split?
I called a number of local spray foam contractors this afternoon and surprisingly the couple I spoke with don't work with low density open cell foam at all! I know of several other contractors and I'm confident I'll be able to find at least one who does work with open cell, but it was surprising! At this point based on the feedback above my plan is to build vent baffles out of whatever is the cheapest, relatively sturdy, vapor-permeable material I can find, then spray 5.5" of open cell foam, then fill the rest of the cavity with mineral wool.
In that case I will connect to the grid.
That said though, the grid in my area is pretty unreliable and typically goes down at least a couple of times per winter (snow and ice storms...), such that pretty much everyone in my area has an automatic backup (typically a Generac propane generator). Buying and installing a $2000-$3000 automatic propane backup generator (and the $700 transfer switch, etc.!) when I've already got solar seems silly, so I'd prefer to use the solar as the backup.
In order for the solar backup to actually be reliable in the winter though I'd need batteries (since of course the PV modules won't be generating all the time, especially during the bad weather when the grid typically goes down).
So now I'm back to a grid tie plus batteries...
:-/
Chris,
A backup propane generator is a lot less expensive than backup batteries.
Moreover, you'll get more kilowatts from the propane generator -- unless you get a very large, very expensive battery bank.
And if you have an ice storm -- your batteries won't last long on solar alone. (Winter is cloudy.) So you'll still need a generator.
Conclusion: buy the generator. Skip the batteries.
In the current reality of PV prices and Utility disincentive strategies for grid tie systems, I would question the 100K calculation proposed by Dana. The cost calculation is I think much tighter around here maybe in the neighborhood of 20K. It is of course as Dana points out better for all of us if grid tie systems are the first choice but that is not the path being pursued by our local Wisconsin utilities.
Mark,
I agree that $100,000 is a little high as a cut-off point for grid connection charges. But $20,000 may be too low.
$20,000 will buy a pretty good off-grid system -- but you'll pay more if you want to have a really good stationary generator. And an off-grid system locks you into a lifetime of limitations (limitations on electricity use and appliance watt draw) and a regular (and expensive) routine of battery maintenance and periodic battery replacement.
So if I had a friend who said, "It will cost me $20,000 to bring grid electricity to my building site. Should I pay that much?" I would answer, "In a heartbeat."
An interesting part of this whole discussion is that currently the state of Maine is using a net metering scheme in which the customer pays a monthly grid connection charge of about $7/month, then receives credits for however many kWh of electricity their solar installation feeds back into the grid. Those credits are netted against the kWh of grid electricity the customer consumes. Unfortunately, those credits expire after one year and there is no way for customers to be compensated if their solar installations generate more power than they consume. Combined with the monthly charge for just connecting to the grid, that means the customer will always be paying the utility and disincents customers from installing solar in the first place.
The Maine state legislature passed a bill a month or so ago that would have changed the current scheme to one in which customers are paid monetarily for the energy they feed back into the grid, meaning if your solar installation is large enough, you could not only make back the monthly connection charge, but you could even make money every month. This of course would have increased the financial incentive to install solar systems. Surprisingly in our current atmosphere of partisan politics, the bill was supported by both political parties and every other interested party: the utility company supported it, the state-appointed panel of electric ratepayers supported it, the solar contractors' and manufacturers' associations supported it, etc. etc.
Unfortunately, our horrible monster of a governor Paul LePage vetoed the bill and the legislature came close to overriding his veto, but was unable to. Now, solar policy in Maine is going to be remanded to a panel of officials (all appointed by LePage) for review. So it's now anybody's guess what is going to happen with solar policy in the state.
Mark: To be clear, I wasn't putting $100K as a threshold OR a cut off point, but as an order of magnitude at which it's always more cost effective to stay off grid. I'm sure there are many situations where $20K (or even lower) for a grid hookup would still tip toward staying off grid, but very few where $10K or less to hook up is still too much.
The local regulatory and rate structures can move the marker quite a bit in either direction from $20K. In some parts of Australia it's even cost-rational for the already-connected to pay to be rid of the grid when they buy PV, but that's not the case anywhere in the US. That said, I recently walked a guy in Texas through what it would take to build an urban off-grid house, since he was adamant that given the local regulatory and utility climate with unfavorable remuneration for exports to the grid that he was willing to deal with the extra up-front cost an maintenance issues, despite having the grid less than 100' from the property line.
Chris: I've been watching the whole rate restructuring fight in Maine avidly, since the proposed solutions to potential cross-subsidy problems with retail net metering were innovative, and had buy-in from a wide range of stake holders. It seemed like a very worthwhile experiment to run on the state level, and possibly a model for the rest of the country not yet dealing with the impending solar tsunami. Only a smart ALEC parrot like LePage would have gall to shoot than one down. (How is it that he got elected in the first place, then RE-elected? http://mainebeacon.com/gov-lepages-alec-speech-is-latest-example-of-corporate-influence/ )
LePage barely managed to get elected (twice!) with only small minorities of the vote (about 35% both times IIRC) because in both of his elections a third-party independent candidate named Eliot Cutler ran who appealed to a lot of moderates. So Maine's moderate & liberal vote (about 65% of the population) got split both times right down the middle between the Democrat running and Cutler, allowing LePage to walk away with the governorship with only about 35% of the vote.
ANYWAY, politics is infuriating, so back to building science!
I just got off the phone with the biggest spray foam contractor in my area (and the only one who even works with open cell foam!), who was absolutely adamant that I NOT use open-cell foam, to the point where he said he'd refuse the job. His position was that open cell foam, being vapor permeable, would allow moisture (presumably from the conditioned living space) into the roof assembly and condense due to dew point issues, causing moisture damage. I described the idea of using vapor-permeable vent baffle material so the moisture could dry to the vent channel and be vented out of the building, and he said he wouldn't trust that to remove the moisture sufficiently.
Instead, he advocated applying 5" of closed-cell foam directly to the underside of the roof deck sheathing, with no venting, such that the dew point would be buried in the foam and not cause any condensation issues (and said that this is the normal way of doing it in our area and that his company has done it thousands of times).
I asked if he thought there would be problems sandwiching the roof sheathing between two vapor barriers (the Elephant Skin underlayment on top and the closed-cell foam underneath) and he said that there shouldn't be because there shouldn't be any way for moisture to get into the sheathing in the first place. I asked about the screw-down metal roof panel screws penetrating the underlayment as a means for moisture to get into the sheathing, and he didn't seem to think that would be a problem.
Martin? Dana? Thoughts?
EDIT: FWIW, apparently this contractor knows Joe Lstiburek and has attended many of this seminars and that's the method Lsiburek advocates? Hrmm....
Dew point is a temperature, not a location. A dew point can't "...be buried in the foam...", it can't be anywhere- it's a temperature, the temperature at which moisture begins to condense out of fully saturated air into fog, or onto objects as dew (ergo the name.)
The relevant dew point here is dew point of the conditioned space air relative to the outdoor air temperature, which determines the magnitude of the moisture diffusion drive present pulling water vapor into the assembly. When the out doors (and roof deck) are much colder than the interior air's dew point, the difference in vapor pressure moves water vapor through vapor permeable materials toward the colder side of the assembly. But with a vented roof deck that moisture flow is intercepted and purged to the outdoors by the venting.
An 8:12 roof has PLENTY of convective drive, and even some stack effect drive to keep a reasonable flow through the channel. Venting with only an inch of space would be a problem on a 2:12 or lower roof, but that's not you.
Your foam contractor is basically saying that vented roofs aren't adequate for managing moisture diffusion through the assembly, which is absurd. Were it an UNvented assembly with open cell foam against the roof deck he would have a case (sort of, unless there was a smart vapor retarder on the interior), but in fact VENTED roof decks insulated with open cell foam are among the driest roof deck assemblies, because the water vapor permeance is high, and the air leakage practically ZERO. Far more moisture can be transported by air leaks than by vapor diffusion alone, but even fiber-insulated vented cathedralized ceilings have a pretty good track record, despite being far more susceptible to air leakage than an o.c. foam insulated vented roof.
A flash inch of closed cell foam on the roof deck is sufficient to protect the roof deck even without the interior vapor retarder, but WITH an interior vapor retarder it's even more protected. Read and absorb this bit o' WUFI simulation studies performed by BSC, in particular note how well the roof decks fared in zones 6 & 7 with only 1" or 2" of closed cell with the rest being dense packed fiberglass, as summarized in table 3:
http://buildingscience.com/file/5809/download?token=18Y6NJQ8
Only with a light metal "cool roof" finish would 1" prove insufficient without an interior vapor retarder. (What color is your metal roof?) But a smart vapor retarder is SO inexpensive it's worth installing as cheap insurance, which would also dramatically reduce the amount of moisture that could ever accumulate in the fiber layer (or in the open cell foam).
With a vented space above the open cell foam the foam dries into the vent even in winter, since it can pass moisture roughly twice as fast as standard latex on gypsum, but on the order of ~10x as fast as the moisture could get through 2 mil nylon (MemBrain), ~15x faster than vapor barrier latex, and ~25x as fast as the moisture gets through Intello Plus. So, if the foam guy is going to refuse to bid the job based on BS (that doesn't stand for "Building Science :-) ), find another foam guy.
At 5" closed cell foam would be almost as structural as the roof deck itself. If you were going down that road you might as well have put 3" of 3lb foam above the roof deck, skipped the metal, and put R23 batts under the roof deck.
All that is appreciated, but at this point, since he is the only contractor in the area that works with open cell foam and he is refusing to install the open cell foam, what I need to know now is if his idea of spraying closed cell directly to the underside of the roof deck sheathing will work.
If the only foam guy in the 'hood insists on closed cell, that will work. But limit it to 2", the deepest that can be done safely in a single pass. At 2" the foam is WELL into Class-II vapor retardency territory, which is sufficient to protect the roof deck in almost any residential application.
A layer of 5" of closed cell foam is both a crime against the planet, and it vacuums out your wallet. It buys you no more moisture resilience than 1-2" of foam and a smart vapor retarder would.
Fill the other 9.25" with fiber and it'll actually come in close to code-min, (and outperforms 5" of closed cell without fiber.) Use cellulose for the fiber and the moisture burden is safely redistributed- it won't all end up in the cold rafters. Most of it will be harbored as adsorb inside the hollow fiber structure of cellulose, without loss of insulating function, and without damaging the cellulose. If you use fiberglass or rock wool the rafters will have somewhat higher peak moisture content, but you'd be at or above the R49 code min, and a smart vapor retarder would still keep the peak moisture content of the rafters below mold & rot levels.
At only 2" of closed cell foam code requires a Class-II vapor retarder on the interior side. You could use "vapor barrier latex" on the gypsum board, but it's better to use a broad sheet smart vapor retarder detailed as an air barrier, since it's a more reliable air seal than gypsum board, and more moisture moves via air transport than via vapor diffusion. With either v.b. latex or a smart vapor retarder the total moisture burden would be miniscule unless it leaks a lot of air (which is impeded by air-retardent cellulose at any density, or dense packed fiberglass), but with the smart vapor retarder the drying rate is 8-10x faster than through v.b. latex. With smart vapor retarders any moisture that manages to get in leaves in the early spring, before the assembly is warm enough to promote mold growth.
This assembly would be somewhat outside the letter of code per R806.5, since it technically it violates condition 5.3, but it's still quite safe with air-retardent fiber and an air tight smart vapor retarder.
So he's the only contractor who does open cell, but that doesn't mean much, as he's refusing to do it anyway. So what about either:
a) Other contractors who would do closed cell following Dana's plan, or
b) Scrap the spray foam completely and dense pack cellulose with venting (sorry if I missed the discussion of this type of option as I came to this discussion late).
Charlie: I'd personally prefer...
b) asphalted fiberboard vent chutes and dense packed cellulose
...over open cell foam, but Chris expressed a preference for foam for it's more inherent air-tightness. Open cell was suggested as a lower impact (and still moisture-safe) way to get that air tightness, yet his contractor seemingly has a problem with that. Still it can't get to get to code min performance levels without interior side rigid foam on vented assembly. To hit code min in an 11.25" without a ridiculous amounts of closed cell foam is an unvented assembly as-described.
At 16" o.c. rafter spacing even a full R49 would underperform a U0.026 code-max roof by a bit, but would still meet the letter of code on the center-cavity R.
Check out this foam, called Gaco "OnePass":
https://gaco.com/product-details/gacoonepass/
This is the stuff the contractor says he uses, and he says it can be applied 5" at a time (the manufacturer says 4" at a time).
I don't trust my (or any local contractor's) ability to properly detail a membrane vapor retarder as an air barrier... the precision needed to cut and seal around every drywall penetration (lights, outlets, etc.) is beyond my abilities, and I don't trust any contractor to do an airtight job either. So I need to avoid membrane vapor retarders.
So, my circumstances are as follows:
1) No vapor barrier membrane - cuz it won't be done right
2) No open-cell foam - cuz nobody will install it
3) No interior-side additions to the rafters - cuz ceiling height requirements prevent it
Given the above, it looks like my only option is a layer of closed-cell (of some thickness) directly on the underside of the deck, with fiber insulation filling the remaining cavity.
Is that correct? Am I missing anything?
Smart vapor retarder membranes with dense packed fiber still works, even if the air sealing is imperfect. With lower density fiber the risk rises, but still isn't large. The air retardency of the fiber limits the amount of air that will convect into the assembly. But taping & can-foaming penetrations is definitely not rocket science to do right.
Friends don't let friends install recessed lights in a cathedralized ceiling. If that's the look you're after there are plenty of LED surface mount options for putting the glarey round dot in the ceiling, just like recessed cans.
You still seem enamored of closed cell foam, eh?
The Gaco foam is ultra vapor-tight compared to most 2.1 lb polyurethane. It tests at 0.44 perms @ 1", already deep into Class-II vapor retardency, and at 5" would be a Class-I vapor retarder, comparable to 6-mil polyethylene. If you go with that stuff be sure to test the moisture content of the wood before applying it, since it's a "dries never" stackup even at 4".
It also tests at R25 @ 3.5". At 4" it would then be about R28+, leaving 7.25" of cavity left to fill. You could fill the rest of the cavity with cellulose or half-pound foam for another ~R27 and would have dew point margin at the closed-cell/other boundary AND you would be code compliant on R-value. You would never need more than 4" of the stuff even without interior side vapor retarders, so why 5".
Like most 2lb foam it's an HFC blown product, with a massive global warming potential. Anything more than the minimum is arguably "too much".
LaPolla Foam-Lok 2000 is a 2lb foam blown with a very low global warming potential HFO1234_ _ variant blowing agent. At R27.2 @ 4" it too would be sufficient to fill the rest with fiber or open cell foam, and at 4" would still be in the middle of Class-II vapor retardency (= would be able to dry over a 6 month drying season if needed):
http://www.lapolla.com/wp-content/uploads/2014/08/foam-lok-2000-4g-closed-cell-data-sheet.pdf
http://www.lapolla.com/foam-lok-2000-4g/
It's still a lot of polymer per R, but it's a heluva lot nicer to the world than the Gaco alternative.
It's not that I'm enamored of closed-cell foam (or that I'm trying to kill the planet! On the contrary I'm trying to do the best I can here), it's that I don't see any alternative.
The entire notion of the membrane gives me the willies all over. The labor alone to install it detailing for air barrier would set me back a month doing the work myself on the weekends as I am (BTW, yes, I am using surface-mount LEDs instead of recessed cans. The Philips Lightolier Slimsurface LEDs are expensive but they're going to be perfect for my application... I'm a CRI snob; it comes with my line of work) and contractors in my neck of the woods aren't exactly the most surgically precise bunch.
If I'm enamored of anything, it's the air-sealing quality of spray foam in general. And since open-cell foam isn't an option for me, that kinda by default means closed-cell.
Chris,
If you are building an unvented roof assembly with spray foam on the underside of your roof sheathing, then closed-cell spray foam is much safer than open-cell spray foam.
If you are building a vented assembly, you have lots more options. I would choose open-cell spray foam before closed-cell spray foam under the ventilation baffles (just to be sure I didn't get any condensation on the interior side of the cured spray foam), but you could use closed-cell spray foam under a ventilation baffle if you want, as long as the spray foam is thick enough.
But if you are installing ventilation baffles, why use any spray foam at all? Your best approach is probably to use cellulose, mineral wool, or carefully installed fiberglass batts rather than spray foam.
In all cases, paying attention to airtightness makes sense. If you are installing drywall as your ceiling, it's pretty easy to make the drywall airtight, as long as you pay attention.
If you are more comfortable with your contractor's skills with making drywall airtight than making a membrane airtight, but you want the smart vapor barrier advantage of MemBrain, you can add it above the drywall without worrying about making it air tight, and it will still work to control vapor diffusion, even if the air sealing is done at the drywall layer.
The labor of detailing a membrane air barrier give you the willies? Really? The air tight membrane approach is EASIER than an air tight drywall (hell, even Canadians can do it- they're even good at it! :-) ), and with a vented roof deck there is a LOT of forgiveness (read "resilience") to minor air leakage, since it can dry into the vent gap. (And if you did a 5.5" shot of open cell foam you wouldn't have ANY air leakage.)
Seriously, slapping up a sheet of film stuff is dead easy- just pay attention to a few simpler rules:
Overlap and tape every seam.
Don't have any seams that aren't supported by framing on at least one edge of the overlap, sealed to the framing with an appropriate goop.
Lay it over air-tight electrical boxes then make a X or star slits, fold the flaps in and tape to the inside of the box with a fire-rated tape (temperature rated aluminum tapes are fine.) With even minor practice we're talking maybe 5 minutes per electrical box. Just how many electrical boxes do you have in the ceiling, 20? 40? Even if you had the worlds glariest sea of 50 down lights you're talking only about a half day dedicated to installing and air sealing the membrane, call it one full weekend day for a rank amateur with 10 left thumbs.
There are no rocket scientists wasting their careers on air sealing broad sheet vapor retarders- it's really not complicated. Ceilings are usually much easier than walls (except for the sore neck if you spend all day looking up), and even walls aren't that complicated:
http://www.certainteed.com/resources/30-28-137.pdf