Wall Cavity Insulation to Meet Code

youstina
| Posted in Building Code Questions on
Hello, im building my home in hermitage, TN, 37076, davidson county, climate zone 4, i need to use the 2×4 walls because i have a limited budget so what type of insulation can fit in 2×4 walls to comply with 2018 IECC guidelines which require R 20 or R 13+5
Thank you
GBA Detail Library
A collection of one thousand construction details organized by climate and house part
Search and download construction details
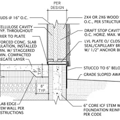
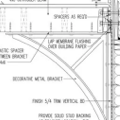
Replies
R13+5 means R13 in the 2x4 stud bays and R5 continuous insulation on the exterior. The usual way to do this would be fiberglass batts in the stud bays, and note that high density fiberglass or mineral wool batts will get you R15 here, and 1” of exterior rigid foam of either R6 (polyiso), or R5 (XPS). EPS can’t quite make the required R value in 1” thickness, so if you want to use EPS, you’d need a thicker layer. I would use polyiso.
You’ll get much better performance with thicker exterior rigid foam. If this were my project, I would use R15 mineral wool in the stud bays and 2” polyiso (R13) on the exterior, which would give you a pretty robust wall assembly.
Bill
Thank you so much
for r20 You'd need to spray foam, which is a bit wasteful in normal wall construction due to all the framing and windows, or cut and cobble strips of rigid foam board.
for r13 + 5 you need a typical 2x4 fiberglass batt + continuous rigid foam insulation on the exterior ( between 1-2 inches depending on the type) make sure to tape the seams of any exterior foam.
Thank you so much
Sharpen your pencil but my guess is your inspectors would pass a 2x6 wall without exterior insulation and I am guessing you can build the 2x6 wall for less money than the 2x4 plus the exterior insulation.
Consider advanced framing IE 2x6 24 inches on center and using the minimum number required as most homes use about 20% more than necessary making the lumber bill almost the same.
https://www.greenbuildingadvisor.com/green-basics/energy-efficient-framing-a-k-a-advanced-framing
Note any large area of spray foam in new construction is a huge red flag for poor planning and wasted money.
Walta
Thank you , do you know how much cost difference to upgrade to 2×6 walls, im building 2400 sqft home
One thing to consider is that typically, 2x4 walls require studs every 16", but 2x6 walls can have studs every 24" (and support a second story floor above). If you compare the costs of the two alternatives, they end up comparable, even though you have a deeper wall (with fewer studs). Partly this is due to a bit lower labor costs (fewer studs), as well as buying fewer studs. In addition, if studs, floor joists and roof rafters or trusses are aligned every 24", it improves the structure of the building, and reduces the labor installing sheathing too (nailing at 24" instead of every 16"). Note that there's less labor for installing insulation batts when there's fewer stud bays to fill (2 every 4' for 24", instead of 3 every 4' for 16")
So...consider 2x6 walls, and price them out vs. 2x4 walls, including the required insulation. Note that you now have typical commodity fiberglass batts that are R-19 for a 2x6 wall. Add the R-value of the sheathing, interior drywall, and you reach R-20. No exterior foam necessary, which reduces both material cost (no exterior insulation purchased) and labor (no exterior insulation installed). The two alternatives may vary in cost locally, including local labor practices (and preferences).
I agree with Bill that mineral wool is a superior choice to fiberglass, polyiso is a better choice than other foam board alternatives, and 2" exterior insulation is a better choice than 1". Although it may cost more for mineral wool batts and 2" polyiso vs. 1" polyiso, there are a number of advantages to his preference:
1. You will pay lower utility bills with a much better insulated wall (about a third less heat loss in the walls). That's for the rest of your life or for others who live there after you.
2. You can spend less on your heating system and your AC system, since you will need a lower capacity heating system since your heat losses and heat gains are less. Or your heating system would run less frequently, leading to lower maintenance if you get the same system.
2. Its easier to do a good job of installing Rockwool mineral wool batts than typical floppy fiberglass batts. So that adds to the energy efficiency too, fewer gaps with insulation not installed well.
3. Mineral wool is fireproof.
4. Mineral wool is less friendly to mice and critters who might get into your structure.
5. Mineral wool suppresses noise better than fiberglass, so your house will be a little quieter despite exterior noise.
6. Your house will be more comfortable when it is better insulated and more airtight.
There are many other Q&A discussions in which other contributors state that they would use mineral wool batts instead of fiberglass, for ease of installation, better insulation, and higher R-value, despite the higher price.
Thank you , do you know how much cost difference to upgrade to 2×6 walls, im building 2400 sqft home
Costs are highly regional and project specific. The right person to tell you the cost difference is the person who is going to be purchasing the lumber and doing the framing. Presumably that's either a builder or contractor, or it's you if you're doing it yourself.
Walter and Robert have both said that they think the 2x6 wall isn't likely to be much of a cost increase. There's a chance you might even save money. You're not likely to get much more detail than that. I would be very surprised if the choice to use 2x4 vs 2x6 walls was the thing that made or broke your budget.
2x6 walls are very common in homes these days, and they make meeting your energy code requirements (R-20) very straightforward. Knowing very little about your specific situation, 2x6 walls are probably the way to go in almost any new construction these days.
Going with 2x4 walls vs 2x6 walls will cost a bit more and a bit less for materials, labor installing insulation as well as building the walls, ...not a huge difference, except making your home more efficient for lower utility bills later, and a smaller HVAC system. There are MANY other ways to reduce building costs that will have a bigger impact.
If you are trying to cut costs, try reducing the square footage, simplify the construction details and room layout, buy fewer and larger windows, and if possible, do as much of the finish work yourself if possible (e.g., painting, trim, floating wood flooring, maybe tile work...), or defer some of the work for the future. Eliminate a full basement and opt for a floating slab foundation or similar, and build a shed or larger garage for extra storage you may need. Seal the house tightly, and insulate heavily, so you can dispense with central AC and central heating, or downsize them, and use mini-splits and a little backup electric resistance heating since your heating and cooling load will be much less. Try to avoid big west (and east) windows unless they are well shaded to avoid summertime solar heat gains.
Bigger savings can happen if you design your home to be a multiple of 4' in width and 4' in length (or at least stick to multiples of 2'), and a simple rectangle (e.g., two-story 28' x 44'). That way, you can do less cutting sheathing, sub flooring, and have less waste to throw away...fewer corners and bump outs...simple gable roof with trusses, which avoids work roofing valleys etc....less work laying out the foundation forms/steel/...on and on. So a rectangular Colonial style, ranch style, modern, ..., and avoid turrets, bump outs, and other framing complexities.
Would also be good to centralize plumbing by co-locating bathrooms/laundry/kitchen sink/DW/water heater, rather than have them spread all over the floor plan in different places. (Not to mention waiting for hot water in a remote bathroom etc.)
Try to eliminate as much corridor space as you can, as its essentially wasted space. Open floor plan, stairway to upstairs near the middle of the building with surrounding bedrooms... You may find you can create the same usable space with a smaller total square footage, to reduce construction costs.
Consider if you can use cheaper finish materials that are okay but not as upscale. Vinyl siding, laminate countertops, less expensive tile, or try to shop some gently used, returned or discontinued materials at Habitat for Humanity stores, outlets, or sale items. Finish work is half the cost of building a home.
These types of efforts can save thousands or tens of thousands. Consider submitting a summary of your plans as a separate question, and ask for suggestions for cost savings.
In my area, 2x6s are actually a little cheaper per board foot than 2x4s. This may not be true in your area. Of course, there's more board feet in a 2x6 than a 2x4, assuming the length of each is the same.
Current lumber prices at my local building supply work out to about $23.13 for the studs to build 4 LF of 2x4-8' wall 16" OC, and $21.92 for studs to build 4 LF of 2x6-8' wall 24" OC—roughly 5% cost difference. As others have said, the labor for framing on 24" centers is also potentially a bit less, and you'll save a bit more materials and labor if you do two stud corners with drywall clips, rather than three stud corners.
Assuming a single story 2400 SF house with 8' walls and a square footprint (49' x 49'), 2x6 studs on 24" centers in my area would actually be about $50 cheaper for the materials than using 2x4 studs on 16" centers. This is basically no difference at all, especially since 2x6 plates will be a bit more expensive than 2x4 plates.
Your contractor would be a better person to ask. The answer will depend on stud spacing, as well as lumber prices. Also, is the contractor working hourly or on a set contract?
There are many variables listed in the posts above, these need to be worked out before anybody will give you an accurate price, and you will never get an accurate price on this forum.
There's a variety of ways to reduce material costs. Some (not all) also reduce labor costs. In industrialized nations, labor tends to be at least equal to cost of materials, if not more.
Will this be an owner-builder project, or are you primarily relying on contractors? If the latter, are framing contractors familiar with and willing to build framing systems that use 2x6 lumber on 24" centers? Are you willing to design using braced wall sections rather than fully-sheathed walls, and if so, will your building officials accept it? If you plan to use drywall contractors, will they use drywall clips or require three-stud corners?
There are techniques that potentially save money on materials, but may not be worth it if the pushback from trades in your area means fewer contractors willing to bid your job, or higher bids based on perceived hassle.
Finally, (maybe most importantly): do you absolutely need a 2400 SF home? A smaller, more optimized design may well reduce upfront cost of construction (at least for materials), as well as lifetime operational costs.
David,
I think your response raises good issues. One small point: Framing with 2"x6"@24"oc is just like framing with 2"x4"@16". The unconventional variant's only come in if you decide to go with Advanced Framing.
True, Malcolm--I should have clarified.
In my neck of the woods (maybe in yours, too) 2x6 24" OC seems pretty standard practice. On the other hand, Advanced Framing/OVE is very uncommon. I used advanced framing for my current project, mainly because as an architecture professor, I wanted to understand from direct experience the pros and cons of the system. I did stick with double top plates and trimmers, but used two stud corners and ladder blocking.
Had to order drywall clips, as no one locally uses them.
David,
Ah - I see what you meant. The mistake was mine.