Insulation recommendations for walls with stucco cover wood sheathing

[email protected]
| Posted in Green Building Techniques on
Many, including me, are having Issues involved with the insulation of house walls with stucco covered exterior wood sheathing.
Potential serious moisture damage might occur to the wood sheathing when trying to effectively insulate the home and increase r-value in order to cut heating bills. Good advice would is really needed bere and Appreciated!! Be advised, it’s a complicated issue!!
Regarding a home remolding & insulation project that I’m try to get right by using insulation best practices.
This is a potential problem for any home owner with stucco trying to Insulate their home, but particularly and potentially very damaging to those who have wood sheathing walls covered by stucco! Further complicated if your stucco has been painted!
I’m trying to Insulate and remodel a 120 year old (built circa 1903 or maybe earlier) that has a vertical wood plank and beam method of construction. The Exterior is now stucco and would have been originally “Clap Board” but was subsequently changed to stucco.
A “Plank House” also sometimes called a “Box House’ or “Doubled Boarded House” (a term used in Eastern Pa.) and they Have NO stud or balloon walls whatsoever.
They were common in the Northeast and Northwestern U.S in the 18th 19th.and early 20th. Centuries.
They were Commonly built in my area – N.E. Pennsylvania between 1870 and 1910, often in the coal mining towns of the area and often built by the mining companies themselves for their miners and employees. There are many thousands in Pa. alone
They were just build of Vertically assembled, rough hewn boards, that were 1″ to 1.25″ thick and 8″-12″ wide. These boards are of 7′-10′ and varying lengths and sometimes they would extend from the rim beams at the foundation up to the gable, 1 1/2 to 2 stories high.
These double vertical boards were sandwiched together and became a “double board” 2 1/2″ to 3″ inches in thickness. Often, they were later covered on the inside of the house with nothing but wallpaper and sometime lath and plaster.
The double boards were then Nailed to thick horizontally oriented (approximately from 3″x8″ to 8×9″) rim beams and additional horizontal rim joist/beams between the 1st. and 2nd. floor, also between the 2nd. Floor and the attic. These beams also carry floor joists and rafter weight and the support of the roof.
With no stud walls it’s very difficult to run electric wiring, insulation, lighting and plumbing.
But this construction does make “continuous insulation” possible upon and along each wall before any insulation will be installed and the new stud walls (to be able to install electric and plumbing, lighting and additional in-wall insulation, if required) are built and erected.
Sometime during my house’s life, probably 1945 to 1970, the house was covered with stucco.
The evolution of Stucco over the last 100 years went from a covering that kept water out but allowed vapor to escape back through the stucco to when when certain ingredients and installation methods were changed or added to the stucco process. This reduced vapor transmission in stucco from over a 30 “Perm Rating” to about a 10 “Perm Rating”
Source: Joseph Lstiburek, Ph.D., P.Eng, – a highly regarded expert on the subject and the principle of buildingscience.com This is a great source of explanation on the subject through various post, pdfs and videos by Joseph Lstiburek.
Check out this excellent video by him:
Additionally, painting stucco, as I had a contractor do in 2019, could further reduce the “Perm Rating” and the drying power of good permeability for wood sheathing. Unfortunately, I didn’t know the issues involved with painting stucco before I gave him the go ahead to paint the stucco
Moisture can greatly damage wood sheathing and cause mold, mildew and possibly create a slew of health problems. Repairs can be hard and very costly.
This lack of drying to the outside of the house makes the vapor “drying” process much more limited to drying mostly to the inside of the house.
Therefore, one must be careful not to reduce the ability of the wood sheathing to dry out, if it absorbs too much moisture, and it cannot dry out in either direction because new insulation can cause permeability reduction. Some of our insulation choices (i.e. close cell foam and certain foiled faced insulations) can seriously reduce permeability and are actually considered to be “Vapor Barriers”.
Also, in 2019 my masonry contractor talked me into painting my Stucco with Valspar Duramax “Elastomeric” Paint and now my Stucco has a potentially even further reduced “Perm Rating”.
Therefore, vapor management is now more complicated and very important. It is an issue for my 2.5″ thick all wood exterior sheathing, now that I’m putting in insulation.
Valspar refuses, as a company policy, to ever disclose the Perm Rating of their Stucco and masonry paints. I’ve written them and even called directly myself. They refuse to reveal the information even when i told them VERY clearly that it was imperative for me and All of their customers to know, especially if they now have any insulation or may ever want to add insulation to their house at any time in the future.
I never would have used Valspar Stucco Paint had I been aware of the potential danger of using their Stucco Paint and their stubborn refusal to release the information.
Sherwin Williams, Behr and other leading paint companies make this very important information available to their customers and contractors.
I would advise AVOIDING Valspar at all costs and look to other paint companies and do the research on painting BEFORE you have your stucco Painted!!!
I need a solution to increase the r-value insulation of my House but not to risk trapping moisture into the wood sheathing. A continuous insulation solution would seem to me to be best
Assuming it will not cause poor permanently.
Weather and Climate Data For my home Northeast Pa. is a follows.
Weather Characteristics:
Climate zone is at the borderline of 5b/6a – generally pretty much leaning 6a.
The Average lows of the 3 winter monthly average low temperatures is 17.66°;
for Dec is 21°, Jan. is 15° Feb. is 17°
The Average of the monthly low temperature in my town is below freezing (31° or lower) for 5 consecutive months – November, December, January, February and March.
Any reccondations are GREATLY appreciated. Thanks from a new member!!
GBA Detail Library
A collection of one thousand construction details organized by climate and house part
Search and download construction details
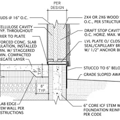
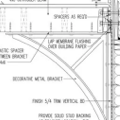
Replies
After hurricane Katrina did its thing, many homes in NOLA required remodeling, but the historical guidelines would not allow to tear any wall exteriors. The solution was to install 1x1 spacers behind the board sheathing; then cut, fit and sealed 1” polyiso rigid foam between the studs and fill the rest of the cavity with permeable insulation. The bottom and top of the walls had openings with bug screens to allow for ventilation.
I know you are in CZ6 and have a different wall assembly, but maybe you could modify my idea to make it work for you. Since you don’t have studs, you could install 1x1 or 1x2 spacers and install full interior 2”-4” continuous rigid insulation per 2021 IRC Table N1102.1.3, plus additional insulation if needed. Allow the wall to ventilate. If you can, add horizontal 2x2s @ 16’-24” o.c. to create a channel for all electrical and plumbing needs, plus additional insulation.
Maybe someone else have a different idea or can add to my idea and make it better for your climate.
Thank you Armando! I was thinking of using "Flash and Batt'" directly against the wood sheathing, but worried about the loss of permanently.
Your solution creates a "air gap" behind the polyiso closed cell foam boards (I'm thinking Foamular NGX 250). The 1"x1" spacers between the sheathing and foam board maybe the perfect answer and solution.
I also like the idea of using Rock Wool. I'm wondering if skipping the close cell foam board altogether and using only a high r-value Rock Wool directly against the sheathing, perhaps something like a double layer of Rock Wool. Possibly like putting Rock Wool comfortboard 80 in a continuous application directly against the sheathing, then building the stud walls and filling those stud bays with some Rock Wool Comfortbatt, like their r 23 or r30 between the new studs (and desperately needed for electric wiring and outlets).
That way I get a layer of "Continuous Insulation" without thermal breaks directly against the sheathing and then the ability to add a lot of r-value Rock wool between the studs.
I just don't understand where that would place the "dew point" relative to the sheathing. Perhaps you or someone who sees this post and knows about such matters and calculations can give input on this kinda "modified flash and Batt" rock wool idea of mine . It be would
great if someone knowledgeable about Busch issues would comment as to whether or not that may work.
I fear that I have enough limited knowledge about insulation to get myself into trouble l!! LOL.
Thanks Armando! for taking the time to comment on this matter with such good advice!
Cheers!! and stay warm (or cool as the case may be in NOLA!!)
Thanks again,
Themunz
Armando, in not sure what you meant when you said:
" If you can, add horizontal 2x2 @ 16’-24” o.c. to create a channel for all electrical and plumbing needs, plus additional insulation."
Instead of 2"x2" I was thinking a minimum of 2"x3" or perhaps even 2"x4" or 2"x6" stud walls. That way I can use full size electral "gang" boxes
And thicker batt insulation.
That's exactly what I had in mind for the new stud walls that will hold additional batt insulation (I really like the great fire resistance of using rock wool) wiring, electrical boxes plumbing ect...
Thanks again for your time and valuable reccondations/advice!!
What do you think of me using thicker stud walls???
In my reply I Meant:
using "Flash and Batt'" directly against the wood sheathing, but worried about the loss of permeability.
Sorry!
Is your home ice cold? How much energy are you using to heat it without the extra insulation? If you are very concerned about mold and rot or it will be destructive to repair might not be worth it
I just filled my home heating tanks with approximately 500 gallons of fuel oil and it was $2,700!!
With my current lack of insulation, and over the last 3 heating seasons (October thru May), I needed 1,000 - 1,200 gallons each heating season.
It will be somewhere between a minimum of $5,700 to perhaps $6,720 this season alone. If prices do not go up at all over the next ten years (that's NOT very likely) that will be $57,000 to $67,200.
If I can cut heating usage by just 50% that's $27,500 to $33,600 of savings.
If I can cut it by 75% that's $42,750 to $57,400 over 10 years.
These estimates do not include any future price increases of oil.
$30,000 to $60,000 of savings would pay for a LOT of insulation!!! (And probably most of my other home improvements)
"A gallon of heating oil in Pennsylvania cost an average of $5.86 in the first week in November, according to the federal Energy Information Administration (EIA). The same time in 2021, it was $3.22; in 2020, $2.03."
Yeah that’s expensive, I had oil years ago and switched to a more Efficient furnace with some insulation cut down from 1200 gallons to about 550 gallons most of it I believe was the better furnace. I now have gas heat, and am grateful I’m not paying the current oil prices. Not sure if you have alternative heating options in your area or the age of your current furnace. That also could be where you get savings
I said horizontal 2x2s to save on space, but you could build a 2x4 or 2x6 wall if you have the space to spare.
Thanks Armando,!
Be aware there is absolutely NO wall insulation in the house at all right now. Also there is only a few inches of insulation on the attic floor that's over 45-50 years old now.
Mineral wool is a highly permeable insulation that moisture/water will easily pass thru. You need a highly impermeable, non-organic and well sealed material against the spacers to stop any moisture penetration into the cavity. After the polyiso, mineral wool is a great choice.
I like Armando's suggestion. My thinking is to treat the existing lumber+stucco wall as veneer cladding such as single row brick and build accordingly.
This means leaving an air gap between the board sheathing then code min wall (in my area this is 2x4+r10). The new wall should be fully detailed including WRB on the outside to protect the insulation and framing from any water ingress through the stucco and old board sheathing.
If it was my house, I would insulate from the outside and be glad to never have to deal with stucco again. Wrap the house in WRB (peel and stick WRB is a good way to air seal, so worth the extra cost). Detail all your rough opening to this new WRB, if you want to replace your windows this is a good time to do so. Cover the house in rigid insulation, thicker the better (2" to 4" is a good number), strap out the foam with vertical 1x4s and hang new siding off it. The stucco doesn't need to be stripped, it can stay under the foam. If you don't want siding, EIFS is also a good option just spec one of the drainable systems.
This way all the questionable bits are on the warm side of the wall and you don't have to worry about moisture. The wall can be strapped with 2x2 or 2x3 on the inside as a service cavity and base for drywall.
Be aware there is absolutely NO wall insulation in the house at all right now. Also there is only a few inches of insulation on the attic floor that's over 45-50 years old now.