Interior Board Insulation

Hi all, I am upgrading the exterior walls in a few rooms and am looking for some advice on the best method (having already read this article: https://www.greenbuildingadvisor.com/article/insulating-walls-in-an-old-house-with-no-sheathing)
I have a 1955 stucco home in zone 3, stucco over building paper against the studs, rock lath already removed inside. My footing is about 10” above the slab. Because I am in a mild climate my plan is to use 1” polyiso, foil to exterior, over 3/4” strips against the building paper to create the rain screen and air seal. I’ll tape the board at seams and around the edges of each stud bay. I’ll then net the studs and hand pack dense pack cellulose by weight to get to my 3.5-4 #/cu ft target. Then I’ll shear wall (having already added 5/8” anchors in each bay) with 7/16” struc-1.
Then we’re at the point I need advice: I am thinking it would be nice to add another 1” of foam and 1/2” drywall over that, screwing through to the studs and not really adhering the insulation to the sheeting (maybe some adhesive or a few cap nails to hold it in place, figuring the drywall will pin it to the wall). If I can get unfaced polyiso I might go that way. My questions are: will the polyiso and plywood still allow the assembly to dry to the interior as I understand it needs to? Should I use a different rigid foam? Is there much point in a thermal break on the inside of the stud wall? Should I use furring strips on the struc-1 and fill the spaces with polyiso or is furring unnecessary to support the sheet rock?
Finally my issue is with how I address the transition of my drywall over the footing. It’s the main reason I might consider furring the drywall as those strips can continue to the floor. But the studs are flush to the interior face of the footing so I could try to add a water resistant barrier (like a butyl flashing) between the footing and the struc-1, and just extend the plywood down to the floor. Or is that just asking for water damage to the plywood?
Any help is much appreciated!
GBA Detail Library
A collection of one thousand construction details organized by climate and house part
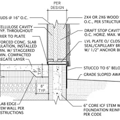
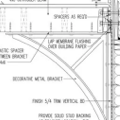
Replies
Evan, any chance you could share a section drawing? I don't understand your footing situation, and it's a bit hard to follow your multiple layers and options.
Hey Michael here's a sketch of the existing. I don't have much building experience but the footing doesn't make any sense to me either. Ideally I would guess the best course of action would be to tear out the exterior walkway (it's about a 4" thick slab along the perimeter of this part of the house), and remove it plus about 6" of soil and create better drainage so that exterior moisture can't accumulate against the footing above the grade of the interior slab. Honestly I didn't realize how big of a difference there is, but essentially my footing looks like a little miniature basement wall right?
In zone 3 your have so few heating degree days that the cavity insulation upgrade by itself is more than enough.
You might want to get some rigid (~3/4 plyiso) onto the inside of the stem walls but that is about it. I don't know how your interior finishes line up, so the interior rigid there might create a bit of a shelf. In this case probably easiest is to strap out the wall a bit on the inside to bring it flush with the rigid over the concrete. This would also give a bit more room for batts in the walls.
Thanks for the feedback! I have pretty equal need to insulate from summer heat (105-110 degree highs) as winter cold (35-40 degree lows)… I agree some of this is overkill but I figure I’m only opening the wall once - at least from this side. I also have the exterior shelf on the footing that is a major source of water, if money and time weren’t an issue, residing the house with zip-r or similar would be a great way to make a flashed overhang and fix the wall from the outside.
Anyway my main concern is making sure I don’t trap water around the footing and sill plate by making the interior work too water resistant.
Regarding rigid over footing, would you just use adhesive to apply and then use adhesive for the drywall over that, or strap out the footing and add polyiso between the straps, to screw drywall to the straps?
Heating or cooling, your delta T is so small that you don't need a high R value wall. Lot of the discussion on here is in places with much colder climate where there is a 70F delta between indoors and outdoors. Worst case you are less than half that, so an R10 wall is really good enough. Never hurts to shoot for more, but I would loose no sleep with less. If you want more, instead of dealing with interior rigid, you can strap out your walls enough to take a 2x6 batt. 2x6 batt + 1" foam baffle will get you pretty much to Passivhaus levels of insulation in your climate.
If you have water issues, you need to fix these before doing much. If your stem walls are wet it will rot your sill plate and could be a source of mold on any insulation on the interior.
As for attaching the foam and drywall glue works so does strapping. I find that strapping out the foam with 1x4s the simplest, easy to screw drywall to it plus it gives something to nail baseboards to. Plus it is easy to shim it in case things are not flat which is always the case in older homes.