Interpreting R317.1 of the 2015 IRC – pressure treated bottom plates

Hello Everyone –
Quick context here is we used non-pressure treated lumber for all of our interior partition bottom plates, which caught the attention of a contractor friend. It’s a very small house, so not too much to demo, but a tough lesson learned.
I did notice that the code language in 317.1 refers specifically to bottom plates on foundation walls or concrete slabs exposed directly to the ground: (2) & (3) below. Since our slab rests on 3” of foam and a vapor barrier, does this technically still apply? I intend to do it right In any case, but figured I’d at least ask.
SECTIONR317
PROTECTION OF WOOD AND WOOD-BASED
PRODUCTS AGAINST DECAY 
R317.1 Location required.
Protection of wood and wood-based products from decay shall be provided in the following locations by the use of naturally durable wood or wood that is preservative-treated in accordance with AWPA U1 for the species, product, preservative and end use. Preservatives shall be listed in Section 4 of AWPA U1.
-
1.Wood joists or the bottom of a wood structural floor when closer than 18 inches (457 mm) or wood girders when closer than 12 inches (305 mm) to the exposed ground in crawl spaces or unexcavated area located within the periphery of the building foundation.
-
2.Wood framing members that rest on concrete or masonry exterior foundation walls and are less than 8 inches (203 mm) from the exposed ground.
-
3.Sills and sleepers on a concrete or masonry slab that is in direct contact with the ground unless separated from such slab by an impervious moisture barrier.
-
4.The ends of wood girders entering exterior masonry or concrete walls having clearances of less than 1/2 inch (12.7 mm) on tops, sides and ends.
-
5.Wood siding, sheathing and wall framing on the exterior of a building having a clearance of less than 6 inches (152 mm) from the ground or less than 2 inches (51 mm) measured vertically from concrete steps, porch slabs, patio slabs and similar horizontal surfaces exposed to the weather.
-
6.Wood structural members supporting moisture-permeable floors or roofs that are exposed to the weather, such as concrete or masonry slabs, unless separated from such floors or roofs by an impervious moisture barrier.
-
7.Wood furring strips or other wood framing members attached directly to the interior of exterior masonry walls or concrete walls below grade except where an approved vapor retarder is applied between the wall and the furring strips or framing members.
GBA Detail Library
A collection of one thousand construction details organized by climate and house part
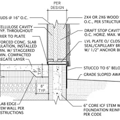
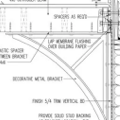
Replies
Zane,
Perhaps future code changes will take the situation you describe into amount, but for now I don't see anything that exempts you from the requirement.
Rather than replace the plates with PT material, can't you lift the exiting walls and slip in a sill-seal?
Malcom,
Thank you for your quick reply. Unfortunately not, because the interior walls are glued down with construction adhesive as there is radiant tubing in the slab. I’d rather demo the walls than risk sinking a fastener into the pex. It’s a bummer but likely not more than a day or two of work all told.
I was wondering if the language of (3) was a potential exemption, since it say “sills and sleepers that are on a concrete or masonry slab that is in direct contact with the ground...” I now see that could be another way of referring to all slab on grade construction, exempting second floor slabs etc but not slabs on foam. It’s a matter of semantics I suppose, but I’m not trying to play games with our inspector. Just part of the learning experience.
Thanks again,
Zane
Zane,
Yes, the existing code is making the distinction between slabs on grade and suspended slabs (which are entirely within the conditioned space).
I think you are right in that your assembly eliminates the risk of using regular lumber for the plates. But with the myriad of possible slab on grade assemblies, I wonder if the code will ever get rid of the requirement.
I'd say a slab on 3" of foam is unambiguously not in direct contact with the ground. My house is slab on grade on an insulated raft, and all the interior walls are standard SPF. The building inspector never batted an eye.
Trevor,
Right now the three distinctions in the code for framing are:
- Above grade.
- Close to grade.
- In contact with grade.
The latter two requiring lumber to be separated from concrete by an impervious material, or be pressure-treated.
While there is a good case to be made that foam practically protects the slab from moisture, I don't see the distinction being made anywhere in the code.
A slab on 3" of foam may seem to be "unambiguously not in contact with the ground" to you, but so would any slab separated by a vapour barrier, or one separated by a 1/2" layer of foam. You may find a sympathetic inspector, but that's different from meeting what appears to be a long-standing interdiction on using SPF as bottom plate on slabs.
I was just going by the words in the cited section above. Based on that alone, I don't think any reasonable person would say two surfaces separated by 3" of anything are "in direct contact". Two surfaces separated by an easily damaged vapour barrier, 0.006" thick, you could make a reasonable argument that's direct contact. If there are definitions spelled out elsewhere, then obviously that supersedes any reasonable arguments either way.
I think the glue down plates will also be an issue. They need to be mechanically fastened to the slab.
Mechanical fasteners would only be meaningful for load bearing walls. With partition walls it really doesn't matter.
Hmm so I guess there is some room for interpretation. Personally I feel the odds of the SPF rotting out are slim to none, but it does seem to be general practice to us PT anytime it’s touching concrete. In any case, I just demoed the walls. Only took a few hours and one less thing to worry about.
As for glued down plates, it’s standard practice here when there’s radiant tubing in the slab. These are interior partitions mind you. All exterior walls have standard 10” anchor bolts. I’m going to do a quick write up on the adhesives, but loctite polyurethane was a royal pita to get up. Split the wood into tiny pieces before it would let go of the concrete. Frankly I’d say it would beat tapcons or powder actuated nails by a significant margin given my experience today.
#7 is interesting. It still applies even with foam and/or a vapor barrier on the exterior. Also interesting that it changed from "impervious" in #3 to "vapor retarder". Probably to allow EPS and XPS foam and drying of the wall to the interior.
My guess is that "direct" was used in #3 to specifically except cases with foam and/or poly underneath the slab. But it's unclear, so one can't blame anyone for interpreting it conservatively.
Jon,
Poly vapour-barriers under slabs have been required in most codes for decades, and during that time there has also been the requirement for treated-plates, or separation between the slab and plate by an impermeable material.
That's how this whole discussion came up. A contractor who regularly has to use pt plates noted Zane had omitted them. If the "directly" meant they aren't required, why has no one noticed until yesterday on GBA.
I work in California and in high seismic areas the code doesn't like adhesives in structural applications. With epoxies to concrete a special inspection is needed. For partition walls they still need to be structural anchored. ( in a code approved way at the top and bottom)
FIrst, I would fall on the sword, tell the inspector and see what they say. It is always possible to talk them into your understanding of the code
Second, is it possible to commission the heating system before you need to rectify this?
turn on the heat get out the thermal camera and nail away
Personally I always take pictures of tube before pouring concrete, or overlaying flooring in wood applications.
And yes, PT in interior walls is a waste of time, precisely zero rot after 40 years when we pulled up partitions in this house, no vapor barrier or foam, but code be code and the inspector is the law.
Indeed the code does require pressure-treated bottom plates whenever they are in direct contact with masonry. The ironic thing is that we generally install sill sealer--closed-cell XPS foam--as an air-sealing detail when in fact the closed-cell sill sealer is also a capillary break, stopping water from wicking up from the masonry to the wood.
The problem with "solving" the wicking problem with pressure-treated wood is that it does not accomplish a capillary break, so you potentially move the mold or rot from the bottom plate up to the bottom of the non-pressure-treated studs.
Best practice in my book is to install sill sealer whenever wood framing touches concrete, even when on interior partitions you don't need the air seal, but it's a good idea to have the capillary break, even if on interior partitions you may only need the cap break during the first six months, when the lion's share of the moisture of construction in the concrete moves up and out.
See this GBA blog: https://www.greenbuildingadvisor.com/article/pressure-treated-sill-plates-and-the-building-code
Peter
Also wonder about the moisture content in an insulated slab. Wouldn’t the radiant heat eliminate any moisture within the slab? if so, why use PT wood? I wonder about the off gassing of the PT wood on a radiant slab. Is there off gassing? Any thoughts on this?