Is water trapped between slab’s Radon barrier and XPS insulation an issue?

Hello All,
We are working on our slab-on-grade foundation. We received quite a bit of rain and are projected to get more in the coming days.
We have the radon barrier (StegoHome) and rigid insulation down on top of that. The radon barrier is air/water tights and the insulation is fairly tightly fitting as well — sealed with spray foam to fill gaps. Due to rain, quite a bit of water has found its way through the insulation and is now ‘sloshing’ around under there.
I find myself stressing over how, and perhaps if, that water will be able to get out from between these two, very-well-sealed, layers. I am thinking that the day before the pour, I should go out with a little vacuum/pump and a small tube and suck the water out of there.
I feel like this has to be a fairly common occurrence, especially in radon zones, but I feel like that water will cause problems. Without the concrete being able to directly reach the water, it seams like it could be stuck there and cause issues with the concrete. FYI — the concrete will be our finished floor.
Any thoughts on how we should deal with this?
thanks again!
WD
GBA Detail Library
A collection of one thousand construction details organized by climate and house part
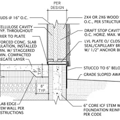
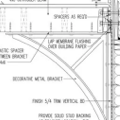
Replies
Yes, this is why you install your vapor barrier above your insulation.
https://www.greenbuildingadvisor.com/article/polyethylene-under-concrete-slabs
I would consider drilling holes through your stego radon barrier and insulation to allow drainage and installing a new radon and vapor barrier above your insulation.
The insulation has dimples for securing the radiant PEX tubing to. As I understand it, the concrete is "supposed" to fill in around them and the pex. So, with the VB on top, that would surely create large air gaps and make the radiant less efficient.
I would still do it, as a theoretical minor drop in efficiency is worth it if the alternative is lifelong moisture issues. I doubt there will be an efficiency drop that is noticeable though, as your heat energy still has the option to either go up through your low r concrete or your high r insulation.
Thanks Freyr_d,
I was reading through the specs for the insulation. It has an integrated VB.
Honestly, I am wondering if having the radon barrier is worth it at this point. I feel like just taking the barrier out and securing the insulation directly on top of the gravel is the simpler less troublesome way to go -- assuming the AHJ doesn't require an independent VB.
I think that would work fine if you are only concerned with the vapor. If you are concerned with Radon I think I would go with a membrane on top, as you will achieve a better air seal in my opinion. But I am certainly no Radon expert so maybe research or ask a local one. You can see that the foam was obviously not sealed perfectly and the VB was by the amount of water intrusion and ponding, so I imagine radon will find its way through.
WD,
Especially if your slab is going to be finished, you need that water gone, and as freyr_design said, pouring the slab with the membrane in the wrong spot means more bleed water will make it way through the foam exacerbating the situation.
The sub-foam water could take years to dry, which among other things precludes you from getting a finish on the slab.
The insulation has dimples for securing the radiant PEX tubing to. As I understand it, the concrete is "supposed" to fill in around them and the pex. So, with the VB on top, that would surely create large air gaps and make the radiant less efficient.
Sorry - I had forgotten, we discussed this set up in another thread.
Your solution may work, or another alternative would be to drill a few holes through the foam and Stego to drain the water into the crushed rock below. That would also help deal with the slab bleed water The holes will not materially affect its function as a vapour-barrier.
I'm with Malcolm; according to BS guru Joe Lstiburek, a few holes in your vapor retarder don't make much difference in performance; the physics are different than for air barriers, which should be continuous.
I also don't like the idea of having foam above the vapor retarder, regardless of what the manufacturer says, but it sounds like you've committed to that idea. You definitely don't want the water to remain where it is. That leaves one option: drain the water.
Malcolm - when you say "your solution" are you referencing me using a small pump to extract the bulk of the water?
idahobuild,
Yes, although that still leaves the problem of bleed water from the slab.
Like feyr_design, I'm not sure of what effect holes for drainage will have on radon infiltration. My understanding is it can move through intact concrete, not just cracks, and I don't know what effect sealing the slab has on it.
Deleted
Since all of the barrier and insulation isn't down.
Should I just remove the insulation and then pull out the radon barrier. Finally, replace the insulation (with its integrated VB) and call it good?
All of course assuming the AHJ replies to my question regarding any locally mandated independent VB.
Radon atoms are tiny and go right through concrete and foam. A high-quality poly will slow it down. I live in a high radon area so the radon membrane is the last thing I would give up. If your foam has a product applied that doubles as a radon barrier, then you could likely eliminate the separate membrane.
The foam mentions an integrated VB but nothing about radon. I am in Idaho with a "red" radon rating (52% of tests conducted are over 3.9 pCi/L). Which is why we have the passive radon system.
It seams like I need the barrier, but if under the foam and if left open to the elements -- which it currently is it will collect water.
The barrier on the foam doesn't appear to be rated for radon (ASTM E1745?).
So, I can pump the water out and have holes in the radon barrier - to get the water out and reduce the concrete bleeding water.
Move the barrier to the top and have gaps between the concrete and foam/pex.
Use only the VB included with the foam and seal it well -- with no ASTM rated radon barrier
Does that sum it up?
I have 3" pipe in the gravel. If I leave the poly under the insulation drain it as much as possible prior to the pour and poke a few holes in 'trouble spots'. If I installed a radon fan on the pipe (per code) and turned it to an active system, would that mitigate the risk presented by making the holes in the barrier?
this is how my priority list would go:
Radon
Moisture
Efficiency
Perfection -- thanks Freyr_d!!
idahobuild,
IMHO, the efficiency loss from not having the concrete in full contact with the pex radiant could be higher than you think. Placing a second plastic barrier between your pex/foam and the now less connected slab mass creates the equivalent of a staple up installation in a joist supported floor. Frequently, heat spreader options are sold to make staple up pex more effective by increasing conductive transfer. The Warmboard product is entirely clad in aluminum for the same reason.
My own pex floor tubing is embedded 1/3 from bottom of total slab thickness to ensure maximum contact and to put the heat where it is needed. The R-15 insulation under the slab (and under the plastic barrier) reduces the losses to the radon rockbed under that. I suspect that like a staple up pex install without spreaders, efficiency of transfer will suffer if you don't fully encapsulate the pex. I do not recall any issues with bleed water during the floor slab pours, but I live in a very low humidity climate. I did have damage caused by a cloud burst that hit before the cure had hardened sufficiently.
Making your radon collection active should alleviate concerns about radon leakage/transfer through the slab. Poking holes in the current vapor barrier to drain rain water would not have much effect on upward radon movement as the negative pressure of an active collection system would pull down through and cracks and keep diffusion based transfer at bay, too. Hopefully, the bed of "gravel" your 3" pipe is in means washed rock. Also that your radon bed is drained properly. Ground water should not be rising up into the radon piping bed.
For some perspective on how much damage poking holes to drain the current radon Stego film I guessed a slab area of 1400 sf. 1 tenth of 1 percent is still 1.4 sf. It takes over 2300 1/4" holes to fill a square foot, so happy drilling. Just make the radon system active and pray for a good long sunny day when you pour your slab.
Thanks Onslow - I do feel like it would be less efficient to have the radon on top of the pex. Also, the 2,300 holes math was very helpful. Even if we make 500 holes and deal with a few damaged areas from framers and concrete crews we'll hopefully be dealing with leakage levels through the radon barrier that a decent radon fan can overcome.
I do like freyr_design's breakdown of 1) Radon, 2) Moisture and 3) Efficiency. So, I considered and integrated the suggestions and have come up with the solution listed in #18.
let me know what you think.
Thank you all for your thoughts, suggestions and ideas thus far!!!!!!!!!!!
I have been giving this some thought. The weather here in SW Idaho is fairly dry (i.e right now the temp is 68 degrees F with relative humidity hovering around 32 percent) and a bit windy. We even got a 'credit' on our manual J for latent something or other. So, I am feeling like if we get water under the insulation that it will likely dry -- even if it's under the insulation. Am I applying that correctly?
For the garage, we've punctured the VB (there is no radon barrier for that space). Then, resealed the holes with an acrylic tape. When we left, the sloshing under the insulation was significantly reduced. So, we're are going to keep it the way it is (poly on bottom and xps on top) and staple the pex over the xps.
For the house, we're thinking that we'll wait until after the rain before laying the Stego to giving the 6" base of cleaned/washed gravel a good chance to dry. The weather after the this weekend, if you can trust the forecast, is mostly sunny and windy leading up to and including Pour Day (Red Box in atch'd ). We will have a conversation with the concrete sub regarding the weather and the potential of using concrete mix that isn't extremely wet.
If the weather, everyone's schedules and the gods are against us -- then, the fallback would be to drill holes as needed - cause, if I am being honest, we would have to deal with at least a slightly leaky radon barrier either way .
Then, once the house is built, we can test for radon and add sufficient suction to overcome our 2,300 - 1/4" holes (okay - probably not that many holes).
Am I crazy or should I rethink...?
idaho build,
TL/DR ahead.
Glad to see that your appears to be what I refer to as washed stone. I grew up in a former gravel pit back East, so my usage of the word "gravel" means the glacial deposit layer composed of coarse sands and very small stones. Great for lots of uses, but it does hold water thanks to the fines included in the mix of sizes. Other layers of ancient stream beds provided killer sandbox material in abundant quantity. My Dad found it convenient to have the layers of sand and gravel to pick from when pouring concrete or mixing mortar for the two houses he built. And an interesting geology experience to have in ones yard.
Stories aside, the washed stone bed really doesn't need much air drying. Your drainage piping should be set to keep any ground water draining away from the perimeter and interior concrete. This will also keep water out of your radon pipes and rock bed. No idea what your immediate terrain grades are, but the rock bed should be set on native soil that is graded to direct water toward the lowest grades you have (assuming that doesn't impact neighbors rights). Level the rock prior to placement of the radon plastic and foam pex panels.
I'm built on a solid stone layer, so my sub grade inside the basement walls entailed a fair amount of rock depth on the low end. I connected to the perimeter footing drains to a footer pass thru drain to collect the spring run water that follows the rock layer. Final exit is 3 feet below below slab levels Your soil profile may be more forgiving and not present such a problem. Just the same you don't want natural ground flow to be blocked on the inside lower grade end of your slab stem wall or turn down. Here locally, it can be a real problem thanks to the stone layer we all sit on.
Regarding the radon management, once you have a negative pressure system; ie: an extraction fan on your pipe layout, then the holes should not leak anything upward. All your gaps, cracks and drain holes will serve to pull downward toward the rock bed and then out the final vent point. Diffusion through the concrete should also become moot as the radon concentrations under the slab will constantly be reduced via the same extraction pipes.
Personally, I would poke as many holes as needed to get the water out from under your PEX panels (under 2300 of course) to clear the pooled water. The EPS panels will be very, very slow releasing water upward especially due to the VP skin on the panels. Just better to let the trapped water drain downward. During my pours the floor mix I saw placed was stiff enough that two crew members had to keep forcing it around for primary leveling. I would be concerned if it self levels like a gyp-crete. I did have synthetic fiber added to the garage slab to handle future high loads. Not recommended if you are polishing the floor to live with directly as the fiber can show up.
For all my PEX placement, I zip tied the tubing to the under side of the 4x4 mesh. A real PITA to be sure keeping the zip ends aimed down. In coordination with the (very helpful) cement crew, we first set the stone, radon piping, reclaimed XPS sub slab insulation and the plastic barrier. I then wrestled the PEX into my desired run lengths and pinned it to the foam with lawn staples. The crew then cut and placed the wire grid mesh on chairs to control slab depth placement. I returned that night to tip toe around the mesh and zip tie the PEX to the bottom side of the mesh, undoing the lawn staples as I went. Tedious to be sure, but in a 4" slab pour I needed to keep the PEX at a safe depth. I was warned that tying to the top side of the mesh risked cracking above the tubing due to thinning depth. Anyway, the floor is fine.
For your garage PEX, you could slip lift blocks under the tubing as you staple to fully embed the tubing in concrete. But it is your back not mine that will need to decide. I would tend to not patch the garage drain holes despite the radon not being actively removed under the slab. The same under one tenth percent hole to whole applies. Water drainage first IMHO. The seals required for interior home to garage doors should make interior post construction radon level checks credible. Testing the garage separately would be tricky and bit questionable given that the doors open and close frequently.