ISO Recommendation for slab edge insulation at walkout basement, zone 6B

New residential construction in climate zone 5B, has a detail with which I’m not familiar, hoping you guys can set me straight. The plan includes a walkout basement with a hydronic radiant heated slab. Below grade walls are Nudura ICF, above grade Murus PUR SIPs (OSB sheathing). We’re using 2″ (R10) or 3″ (R15) crete-heat under the slab, in case you’re unfamiliar that’s just a product that holds the radiant tubing in place and includes moisture resistance and insulation all in one. All ICF exterior surfaces will be protected by Nudura waterproofing membrane.
Below grade the crete-heat will abut the interior ICF foam wall, thus completing a moisture barrier and insulating blanket around the bottom and edge of the slab, as well as preventing the hydronic heat from radiating downward. The crete-heat/slab will rest on the concrete footer. This seems pretty straightforward, please let me know if I’m not thinking straight on this.
But on the walk-out side, the crete-heat, slab, and SIP sill plate will rest on the top of the ICF wall, not the foundation. See the attached detail.
My questions –
* With 8+” from the top of grade to the bottom of the SIP do I still need to be concerned about capillary action wrt the SIP’s OSB, sill/bottom plate, and rigid insulation at the slab edge?
* Given zone 6B, what R-value is needed at the slab edge? I have read varying accounts, and have concluded a minimum of R-3 is needed. Is that correct?
* I have very little practical experience with conditioned spaces above slabs. What specific material would you recommend for the rigid foam at the slab edge? If R-3 is the minimum, then I think either XPS (R3.0 at 1/2″) or polyiso (R3.2, although I’ve read it degrades significantly in our climate) would suffice, EPS would not (R2?). If there is no concern of capillary action I could go with a polyiso product, e.g. Sika, and that gives me R-3.2, which is the best I can get with rigid foam (or would its performance degrade in our cold climate?). But it seems perhaps foolhardy to expect no moisture in that area…?
* What type of sill/insulation sealant and flashing would you recommend for this detail?
GBA Detail Library
A collection of one thousand construction details organized by climate and house part
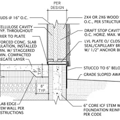
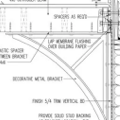
Replies
Anyone out there? Did I post on the wrong forum or use the wrong category?
Between XPS and polyiso, polyiso is much greener. However for underground uses polyiso is not suitable. EPS is usually the recommended option. Why only 1/2”? If you are going through the trouble of installing this 1/2” will end up being the same amount of work as 2-3”. Also I don’t think R3 is enough. BSC recommends R10. See link below, page 10, Table 2:
https://buildingscience.com/sites/default/files/migrate/pdf/BA-1005_High%20R-Value_Walls_Case_Study.pdf
Thanks for the reply. Under slab we’re using R15, the foam I’m asking about is for the edge, not below. The reason for 1/2” is so the foam is not visible after instaling 1/2” drywall and baseboard.
The question is whether moisture will wick up into the foam from the ICF, and if so, would polyiso be a bad choice.
Also the foam is above grade,
The BSC article recommends R10 for slab edge specifically in CZ 6.
Ah, I see that table now, I somehow missed that the first time I read your reply. Ugh.
So, let’s see…. Other than at the walkout the slab is below grade and wrapped by R-24 ICF with R-15 below, so we’re good.
At the walkout the R-24 ICF runs from the footer up to 8” above exterior grade. And an R-27 SIP wraps the top 1” of the slab. Then there is a 2x bottom plate and sill plate below the SIP, so that’s what, R-3 or so? So I need another R7 for the rigid foam, which means for EPS or polyiso I need 2” instead of 1/2”? Hmm, and the foam is only the height of the slab which is 4”. Sounds tricky.
As for what rigid foam material to use, do you get what I’m asking about capillary action? It is resting on an ICF wall 8” above grade, so is not below grade. Is polyiso still not usable?
Slab edge is more important to my mind than underslab. You can get away without underslab, but not slab edge
Looks to me like that whole edge of the slab is not very well insulated, with the tapered exterior foam.
The only way you will see the edge foam is bare concrete floor. Also, sheetrock then baseboard.
I think I would want that underslab to continue to the wall, if the engineers allow. There is no load on the last foot of the floor anyway.
If you have a finish floor, no reason not to have 2 inches [or more] at slab edge
You make a good point about the flooring, we may leave it bare for a while but will eventually cover it anyway. So the foam being visible vs. my radiant system costing me a small fortune is a no-brainer decision ;-).
It's a radiant heated floor, so underslab is also very critical. The detail is a bit misleading, the Crete-Heat (3" EPS with attached vapor barrier, R-15) will continue to the wall (slab will not contact the ICF concrete), so it's just the part of the edge that isn't wrapped by the SIP that is an issue.
The issue isn't the slab edge, that rest against the SIP so well insulated. The issue is the concrete connection of the slab to the ICF core. Find out if this needed, if not needed you put an inch or so of rigid between the two to decouple them.
Another option is to use regular ICF form and cantilever the wall a bit and use 2x4 lumber for the rain screen. This would get siding flush with the outside of the ICF blocks and give you more insulation there.
SIP walls are very sensitive to moisture and bulk water issues. Make sure your window flashing details are perfect and install your siding over a rain screen.
The detail is a bit misleading, it shows the slab and its insulation as one object. The Crete-Heat (3" EPS, R-15 with 10-mil polystyrene film vapor barrier) will indeed rest on the ICF below the slab, i.e. continue to the wall (slab will not contact the ICF concrete), so it's just the part of the edge that isn't wrapped by the SIP that has thermal bridging, due to the bottom and sill plates (that's 3" our of 4" slab height insulated only by wood). Hence the need for insulation at the edge of the slab.
Thanks for the note and recommendation about SIP moisture issues. The wall SIPs are from Murus and are PUR with OSB. They recommend house wrap but not rain screen. We are building in high desert, not a lot of rain, but non-zero. Do you have a favorite/recommended source of information about rain screens and any specific product recommendations?
Akos is right. You very likely don't need to connect the slab with the foundation. Check with your engineer. If you don't need to, then decoupling them thermally is easy.
Also, your slab edge is INSIDE your wall. It's not an exposed slab edge. So it's protected by the insulation of your SIP. At that point, the bottom of your panel, it's up against lumber rather than insulation. But framing lumber itself has an R-value of about 1.25 to 1.5 per inch. I'm not sure the value for pressure treated lumber but it's probably a little lower, maybe R-1 per inch. So your 2x6 P.T. sill gives you around R5.5. Any foam insulation you add to that is good, of course. Assuming 1/2" drywall and 5/8" base trim, you could also potentially hide 1" of foam insulation.
By the way, Insulfoam makes a Type IX EPS that have a value of R-4.35 per inch at 75 degrees, and rising to R-5 per inch at 25 degrees. An inch of that in addition to your framing lumber would be more than adequate.
Thanks for helping me quantify and for adjusting my thinking - not exposed, but subject to thermal bridge at the sill. The PUR SIPs are only 4 5/8", so the PT sill is 3.5". Adjusting your math then to get to R-10 I need to add R-6.5. Sounds like that's just another 1/2" of Insulfoam Type IX EPS, so 1.5" will do the trick.
Two questions -
1. An inch of polyiso would also get me to R-6.5, right? Which takes me back to my original question. Being above grade, is it ok to use poyiso?
2. It looks like the supply houses around me stock only Insulfoam type 1 products, where do you find the higher R-value Insulfoam?
Given that the polyiso is actually inside I expect it will last indefinitely. It will, like XPS, lose a bit of its insulating value over time. But if you've got R-9 instead of R-10 15 years from now the difference would be imperceptible, both in your energy consumption and your comfort.
By the way, typically the P.T. sill is dimensioned for the full width of the SIPS panel, not just the width of the insulation itself. You'll see in your detail that there are 2 plates, a "bottom" plate that is the width of your insulation, probably a standard 2x4, and below that the pressure treated sill, which is the full width of your SIPS panel, probably a 2x6 ripped to 4.5".
Your pressure treated sill, at 4.5" and R-1 (conservatively) gives you R-4.5. Your 2x4 "bottom" sill is not pressure treated and probably has an R value in the 1.25 to 1.5 R/inch range. Assuming 1.25 that gives you R4.4. So I wouldn't sweat the details. You're going to be fine with an inch of any kind of insulation at your slab.
Polyiso or EPS are both fine. Polyiso is more R/inch at the start of its life, but loses some value over time. EPS is constant and doesn't lose value. Twenty years from now they'll probably be near the same.
Ah, good point about the PT sill. One last question - the detail shows the vertical foam resting on the ICF, would it be better if it rested on the horizontal foam (Crete-Heat) instead? Or does it matter? If resting on the ICF would there be a risk of capillary action bringing moisture to the polyiso?