Large barn insulation

Southern IN climate zone 4
I am building a traditional framed barn 50’x80′
2″x8″x14′ walls with scissor trusses, 4 large roll-up insulated doors and radiant heat with footer and under floor insulation
Ribbed metal siding over tyvek and osb sheating
Interior will be either hardy board or ribbed metal walls
Ceiling is ribbed metal
Shingle roof
Insulation plan:
R40 cellulose on top of ribbed metal in the attic
spray foam in the walls
I would like to use open cell due to cost but no contractor will spray with out a waiver. They say I need closed cell or I will have water pouring out of my walls from the wicking open cell foam. Should I be concerned about this waiver or keep looking for contractors?
Brian
GBA Detail Library
A collection of one thousand construction details organized by climate and house part
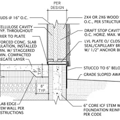
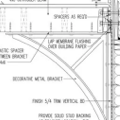
Replies
What is going inside the barn? If animals or a grow operation, there will be lots of indoor humidity and you've got to design for that. If just dry storage (not hay unless really dry), you might be OK but you should still consider future uses. Condensation issues are related to indoor moisture sources, and if there aren't any real indoor moisture sources, you won't have a problem.
That said, you could design for water running down the walls. If you installed a layer of fiberboard sheathing inside the ribbed metal cladding, the fiberboard would provide enough support for the spray foam. But fiberboard is very vapor permeable, so any vapor diffusing through the foam would be able to enter the air space inside the metal ribs. It would condense inside the metal skin in cold weather and run to the bottom of the wall. In extended cold weather, you'd probably get a pretty good layer of ice inside the metal that would release all at one time when the weather warms up. So long as the base of the wall is designed to drain, this might not be a bad way to go.
You haven't mentioned what the interior finish will be. You can't leave spray foam exposed to the interior in most uses for fire reasons. If you install an inch of Thermax foam on the interior and tape the seams, that is your vapor barrier, and you don't worry about condensation inside. Thermax comes with heavy duty metal skins that can be your interior finish. Some is tough enough for powerwashing, specifically for ag uses. You could fill the wall with fluffy insulation to offset some of the cost of the Thermax.
With your current plan, you will get quite a bit of thermal bridging with the 2x8 studs, and this makes the spray foam less attractive economically. You could fill the wall with fluffy insulation and install an inch or two of exterior foam under the metal skin for similar cost and better overall R-value, with no risk of condensation.
I should have specified content of the barn. This is more of a machine shed, RV storage and man cave.
Exterior is metal over Tyvek and osb sheating
Brian
I clearly remember the first time I misused the word "barn" in the presence of a farmer. I indicated a building nearby, and asked a question about the barn.
"That's not a barn," he responded. "That's an equipment shed."
Do you plan on heating and or cooling this space?
If not the insulation is a waste of time and money.
Why would you consider hardy board for the interior?
Once painted pine would look the same at 1/3 the cost between labor and materials.
Walta
I am not planning to run AC but we may run a dehumidifier.
There is radiant heat in the floor and I plan to keep it around 60-65 in the winter. This will keep my RV from freezing and will allow the space to always be comfortable when we head out there.
Brian
Brian,
I think the foam contractors' concern -- namely, that you "will have water pouring out of my walls from the wicking open cell foam" -- is unfounded.
The first question we have to answer when we are discussing a moisture problem in walls is, "Where is the moisture coming from?"
Are you and the insulation contractors worried that rain will enter your walls? If so, you need better flashing details, siding details, rainscreen details, and a better roof overhang. Switching insulation materials won't help.
Are you worried that the source of the moisture is the interior of the building? If so, where is the moisture coming from?
The stored machines? No.
The parked RV? No.
The man cave? Maybe -- but only if you re-enact locker-room celebrations by pouring cases of beer or champagne on each other's heads, for hours at a time.
Martin,
The moisture is believed to be coming from the air in the barn. This building will have:
Concrete floor with Radiant heat with 2' foam under the radiant tubes and down the footer walls(water/vapor barrier).
14'X14', 2- 10'x10' , 1-10'x16' and one man door
There are floor drains under the parking areas for wet vehicle. I do not plan to wash vehicles or have excessive water in the building.
Brian
Brian,
There is no reason to believe that the air in your equipment shed will be moist enough to cause problems. I have no idea what your contractor is thinking.
Martin,
Does the interior covering, hardy board or metal sheeting have any effect on this? Dry wall would allow more breathing but I’m not sure if this would be + or-.
Also, is there any problem with Chinese/poor quality foams being sprayed by companies? I heard this from some bidders as well!
Brian
Brian,
If your climate were a little colder -- if you lived, say, in Climate Zone 5 -- building codes would require your walls to have an interior vapor retarder. In Zone 4, that isn't required.
Even if you did need an interior vapor retarder, installing it is easy. Kraft facing, vapor-retarder paint, or a so-called smart vapor retarder like MemBrain would all be possibilities. But you don't need a vapor retarder.
Any wall assembly benefits from airtightness -- but if you insulate with open-cell spray foam, you've got that issue under control.
I haven't heard any reports of U.S. contractors spraying Chinese-made foam. I suspect that is a rumor.
With the vapor only entering at the seams of the ag metal or hardie board would there be any need for a vapor barrier in any condition?
Brian,
This assembly does not need an interior vapor retarder because your climate is mild. Ordinary attention to air sealing is all you need.