Low-GWP spray foam kits?

Hi,
Does anyone know of two-component spray foam kits (the 200-600 board foot, DIY type) that use low global warming potential blowing agents? I did find some slow rise and channel fill products from HandiFoam that use HFO blowing agents, but nothing suitable for typical rim joist and attic air sealing applications. Thanks!
GBA Detail Library
A collection of one thousand construction details organized by climate and house part
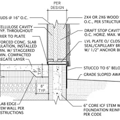
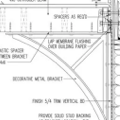
Replies
Jon, I've asked around and have not been able to find any low-GWP two-part kits.
You were so close! I wasn't familiar with HandiFoam so I was checking them out and found this closed cell product:
https://www.handifoam.com/product/handi-foam-high-density-low-pressure-spray-polyurethane-foam-spf/
Looks like it uses a HFO, specifically HFO-1234ze with a GHP of only 6.
Granger has it https://www.grainger.com/product/HANDI-FOAM-Insulation-Insulating-Spray-458J57
Here is the MDS listing the ingredients as HFO-1234ze
http://complyplus.grainger.com/grainger/msds.asp?sheetid=4208306
which according to the EPA has a GHP of 6
https://www.epa.gov/sites/production/files/2015-07/documents/transitioning_to_low-gwp_alternatives_in_building_and_construction_foams.pdf
This particular product manufacturer number P12025, P12030, P12035 is intended for roofs, it might be usable for other cases I've not looked into it. I would like to use some in walls.
Beware as of 2020/05/05 other HandiFoam products available on Grainger.com which use HFC134A which has a GHP of 1430! My guess is that HandiFoam is starting to use HFO with a few products and will roll out to more. That also means being careful not to buy old stock.
Mind you that's a ~3 lbs density foam, not 2lbs foam. With ~50% more polymer there's likely to be ~50% higher net CO2e compared to the more commonly known 2lb HFO blown foams.
The higher polymer per R makes 3lbs HFO blown foam comparable in CO2e footprint to HFC blown 2lb foam, eyeballing it on this reference chart:
https://materialspalette.org/wp-content/uploads/2018/08/CSMP-Insulation_090919-01.png
If they do indeed roll out HFO blown 1.5-2lbs density closed cell foam kits it would at least move the needle in a clearly discernable way.
The 3lb density is likely because it is intended to be able to take foot traffic on a flat roof. If that means 50% more GHP than 2lb density I'll take it. The GHP is HFO-1234ze is only 6, so we'd weight the GHP 50% more so more like 9.
Compared with HFC134A at 1430 it is only 150 times better rather than 250 times better for a 2lb version. The cost in GHP for this is tiny although for a 2lb mix it would be teeny weeny :-)
Do you have any insight into how the polymer portion of the CO2e is calculated here?
I've long assumed that the ultra-high GWP blowing agent would dominate these calculations. As in, a little over a pound of HFC134A generates the equivalent of a _ton_ of CO2, comparable to the combustion of ~600 lbs or more of hydrocarbon.
Eyeballing that chart though, suggests that polymer contribution is roughly equivalent to the blowing agent contribution. (The HFO foam bar is about half the width of the HFC bar.)
On a weight basis alone I struggle to see how this can be the case, short of "charging" the polymer component with the emissions associated with the rest of the barrel of oil that the feed stock came from.
(I should research this myself but am, instead, engaging in wild speculation. Apologies.)
OK. A bit of googling research to hopefully add to the discussion yielded this:
http://www.sprayfoam.org/files/docs/SPFA%20LCA%20Long%20Summary%20New.pdf
Granted, it is from a trade organization, but it doesn't seem to try to paper over the blowing agent GWP issue.
I'm attempting to attach a chart that would seem to support the argument above. The "Low Density" foams in this chart do not use a high GWP blowing agent and, as a result, have dramatically lower lifecycle GWP in their analysis.
Quoting from the same page as that chart: "For medium-density and roofing foams, the release of the blowing agent HFC-245fa contributes approximately 85% of the global warming potential in the embodied phases. Because this emission
has such a large effect on GWP and because blowing agent emissions are fairly uncertain, sensitivity analysis was used to evaluate the effects of different blowing agent loss rates on the product footprint related to the embodied phases. "
They end up assuming that 50% of the blowing agent is released during the product lifecycle.
FWIW-The context here is whether it's meaningful for me to insist that a contractor use a low-GWP kit for foaming the rim-joist area in our very old wood-frame home. The cavities are irregular and many of them are interrupted by electrical conduit or other odds and ends that have accumulated in the 100+ years this structure has been occupied. I know it to be a significant source of air leakage and I'm viewing foam as the most likely-to-succeed method for sealing it all up.
Can this be used to seal around reclaimed poly-iso?
Bill
>"I've long assumed that the ultra-high GWP blowing agent would dominate these calculations."
That's only sort-of true.
In the case of 1.5lbs density XPS the HFC blowing agents dominate the CO2e numbers by nearly an order of magnitude, at 7-9x the CO2e of the polymer's contribution. That's truly dominating the calculation.
In the case of 2lbs polyurethane it's only a ~2x multiplier. The CO2e of the amount of HFC245fa used during installation is roughly the same CO2e per R of the polymer itself, (as you correctly surmised.) A significant adder, yes, but truly dominating? Not so much.
>"On a weight basis alone I struggle to see how this can be the case, short of "charging" the polymer component with the emissions associated with the rest of the barrel of oil that the feed stock came from."
First, none (or very little) of the feedstocks for either polystyrene or polyethylene come from a "...barrel of oil...". The basic raw chemicals used are almost all from natural gas (of diverse sources.)
The CO2e of the manufacturing processing energy and transport for the chemicals is also usually factored in to these types of charts.
Just as the energy and coal used for processing the steel are not normally applied to the steel making slag content of mineral wool insulation, and the energy/other carbon inputs to paper making aren't applied to cellulose insulation the "other products" CO2e content of natural gas from oil refining/drilling used in polymer manufacturing isn't loaded on to the polymers created from that gas in these analyses.
Polyurethane manufacturing has a slightly l0wer CO2e footprint pound per pound than polystyrene but there is also more polyurethane per R in closed cell foam than polystyrene per R in most of these charts (which are usually presuming 1.25 - 1.5lbs per cubic foot for sheet XPS or EPS, and 1.8 - 2lbs per cubic foot for closed cell polyurethane), which is why R-for-R even HFO blown closed cell spray polyurethane ends up with about a 50% higher CO2e than EPS. If using 2lbs density EPS (aka "Type IX") it would be about the same as 2lbs polyurethane.
If all of the inputs to the original paper making or steel making were added on to the rock wool or cellulose the numbers might look as bad or worse than closed cell polyurethane or even XPS. But since the slag and paper feedstocks for making those insulations are recycled material that would otherwise be scrapped it isn't as bad. Nobody mines and refines iron ore into just to create slag for making insulation, and nobody harvests & processes trees into pulp/paper just to make cellulose insulation. But natural gas IS extracted as a primary chemical feedstock & energy resource, and isn't normally scrapped even as a byproduct to oil extraction or refining whenever it's financially viable for cleaning up and pipelining. Quite lot of natural gas byproduct from the oil industry is still scrapped though, flared off in open burning rather than dumping it directly into the atmosphere when the CO2/other content of the gas is too high to be economically cleaned up sufficiently for pipelining, or when there isn't economically viable pipeline or storage access.
Many thanks for the detailed reply Dana. I somehow missed your post before adding the Spray Foam Alliance paper link and quotes above.
The feedstock impact comments in particular are quite helpful and clarifying. They are also, unfortunately, a bit bracing insofar as they make clear that some of the most low-impact options are still dependent on fairly high-impact upstream activities.
Hi!
I've been looking for the exact same thing since 2019--a DIY spray foam kit that has low Global Warming Potential. I am doing a staged remodel and would love to spray portions of my house before winter. I could hire a contractor that uses the Honeywell blowing agent solstice (GWP of 1) but there's a lot of overhead cost for each trip, and again my project is staged.
I don't really need the science, just the product itself. Could anyone send a link? I heard California required low GWP for all spray foam blowing agents as of 1/1/2020, so I'm hopeful that someone has developed a low-GWP DIY kit in California. Thanks.
DAP Touch 'n Foam has a "low GWP" product using HFO-1234ze(E) now. According to the second link it is available in some states. Anyone know how to buy it?
https://dap.com/products-projects/product-categories/spray-foam-insulation/spray-foam-insulation-kits-refills/tnfp-kits-200-low-gwp/
https://www.wconline.com/articles/93526-dap-unveils-new-high-performance-spray-foam-kits-with-low-gwp
There's a kit listed on Ebay right now:
https://www.ebay.com/itm/DAP-Touch-N-Seal-600-BF-Low-GWP-1-75-PCF-FR-Closed-Cell-Spray-Foam-Insulate-Kit/313399921697?hash=item48f8174c21:g:-LYAAOSwXJpgFG06
$859 for 600 BF.
It's listed as 1.75 pounds per cubic foot, which would mean 87 pounds for a 600 board-foot kit. Which means it could be UPS'd in one box per bottle. Also less to carry during installation. Lots of practical advantages to the lighter formula.
Thanks Ross. For my project I ended up using Silent Seal, which has a low GWP blowing agent. Technically this is supposed to be for mines, so I definitely wouldn't mine using the DAP product next time.
What about OCSF? I know the R-per inch is lower and there can be vapor issues, but are these blown with water?
https://tigerfoam.com/sprayfoaminsulation/order-products/spray-foam-kits/tiger-foam-open-cell-formula-1350-kit/