Matt Risinger Shows a House Built With A Layer of ZIP R-9 Over Another Layer of Exterior Sheathing

This is an interesting video from Matt Risinger about a house being built with a layer of exterior sheathing on the walls and then that first layer of sheathing is covered with a second layer of ZIP R-9 insulated sheathing.
https://www.youtube.com/watch?v=7loNsWGYJ3w&t=41s
(minute 3:05)
At first I thought that having two layers of sheathing (with a 2-3” layer of foam in between them) was overkill but then I thought of all the postings I’ve read through on this site from people asking about what type of exterior insulation to choose and how to properly detail and install it. Usually the questions begin with “how do I fasten the cladding through the rigid foam exterior insulation” and end with “how do I detail the tops, bottoms and edges of the cladding/air gap/furring strip/insulation rain-screen system”?
Then there are the further complications you run into when using a mineral board product for your exterior insulation – how do you handle possible compression of the board, how do you prevent the cladding from sagging under it’s own weight (especially if the mineral wool board is 3-6” thick), etc?
For the system shown in this video, I’m guessing that the best reason for using it is that the first layer of sheathing acts as your “shear wall” and the second layer of ZIP R-9 is not only your exterior insulation (now required almost everywhere that gets cold by code) but also gives you a solid nailing base for your furring strips and cladding. I would also think that detailing the edges of the ZIP R product would be a lot easier than a mineral board edge simply by covering the exposed foam with some regular ZIP sheathing and taping the edges.
As an aside, I was always hesitant to use ZIP R products by themselves as the exterior sheathing because of the layer of foam between the wall stud and the sheathing after I’d read a comment from Dr. Joe Lstiburek who, when asked about ZIP R (and similar products), said “good luck achieving shear values with that”. Putting ZIP R over another layer of sheathing seems to solve the problem with shear values as well.
The only thing they didn’t get into was the WRB. I guess if the first layer of sheathing was regular 5/8” ZIP you could just tape the seams but if you used OSB or plywood you might have to use a liquid applied product before you put up the ZIP R.
What do you think of the system used in this video?
GBA Detail Library
A collection of one thousand construction details organized by climate and house part
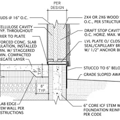
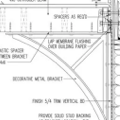
Replies
rockies63,
It's panelized construction, so they didn't really have any choice about whether there was an interior layer of sheathing or not. Their rather hesitant explanation of the two layers seemed to come down to "because we are good builders".
Joe L's general comments aside, Huber supplies fastener schedules for Zip-R to meet code required shear values in all but the highest wind and seismic zones. https://www.huberwood.com/uploads/documents/technical/huber-zip-system-r-sheathing-sell-sheet.pdf So aren't we really down to whether it makes more sense to use exterior foam or Zip-R, rather than whether two layers of sheathing makes sense (I can't think of an instance when it would).
I agree - it's easier to detail your rain-screen and cladding over Zip-R than exterior foam. However you do lose the benefit of your sheathing being kept warmer and consequentially drier by the continuous exterior insulation, so there is a trade-off.
While I enjoy Matt's videos, I wish he was a bit less credulous, and acted more like a journalist than a booster of every process or new product he sees.
His videos are interesting and he does good work, but I find too many of them are sponsored product features. The series of his own house build were full of product feature videos. They work, but there are often less expensive options that may suit better.
I imagine it's a combination of massive sponsorship and possibly being a cost plus builder. Zip R9 is probably one of the most expensive ways to simply add exterior foam.
I think it's more the sponsorship. The videos have a five second mention of the sponsor at the beginning and then it's a full product feature, like the new Jeld-Wen windows or the Halo light automation. I think most people would lean towards Lutron Caseta and installing whatever lights you wanted rather than sticking to one brand. His main bath with the over the top Kohler stuff. He doesn't tell you that touchscreens don't work when your fingers are wet.
And yet I still watch them :-)
I'm in the same boat, haha. Many of the ideas shown can be executed in more cost effective ways. Or I just look for the useful detail among the touch screen shower controls and steam baths. The concept behind his HVAC system for example. Execution was not so great. If I'm not mistaken, he has ~4tons between 3 units for a passive house in texas...
It is true that Zip-R sheathing can serve as a shear wall. However the shearwall aspect ratio is limited to 1:2 (width no less than half the height). Wood structural panels don't have this constraint. Design within the Zip-R limitation and it can be an efficient way to go. But I find that most of my designs don't work with it. I'm designing in seismic zone D, the most severe. But I expect it works great in other parts of the country.
I don't know why Risinger went with the 2 layer system but it would be one way to solve the seismic problem. There are probably better solutions.
jgsg,
I work in a high seismic area. The prescriptive code solutions, and the ones I get when the project is engineered, both rely on discrete shear-walls, not the entire sheathing of the structure. These two layers just don't seem to make sense to me in either typical or high seismic situations.
Thanks for the input, Malcolm. Although you probably know everything I'm writing here I'm responding for the benefit of anyone else who might find this comment stream and not be as familiar with the subject.
Discrete shear walls, such as the Simpson's steel or wood "Strong-Walls", are among the sorts of "probably better solutions" I was referring to at the end of my comment. Also, referring to Table R602.10.5 of the IRC, we see that shear wall panels as narrow as 24" can contribute towards our total shear, using standard plywood or OSB construction. Of course, with Zip-R these wall sections would not be counted. In my own work I find these narrow wall sections are essential in helping me to achieve my design goals. That's why I default to continuously sheathed plywood shear walls instead of Zip-R.
In other seismic zones Zip-R might be more than sufficient, in which case by all means consider it. However I can't imagine any situation where applying it over wood structural panels would be the best solution, at least for structural reasons. I suppose if people wanted continuous insulation AND a continuous exterior nailing surface, such as if they were applying cedar shingles to a wall, in a complicated pattern that didn't work with normal furring, Zip-R would provide that. And if in addition they needed a more rigorous shear wall, then the combination of Zip-R and plywood MIGHT make sense. But the situations where that combination would be the best solution seem to me rare.
To add to this is to look at the Ga value in the shear tables. Ga is the apparent stiffness and is used to calculate the shear wall deflection. The Ga for ZipR panels is closer to that of drywall than of plywood or a OSB shear wall. Deflection = damage in a seismic or wind event.
Given that, it looks like the prefab panel manufacturer didn't want to build & ship panels with ZipR due to the possible damage in shipping & field construction.
Your comments make sense to me. Just one correction, though--"exterior insulation" is NOT required; "continuous insulation" is required. With double-stud walls the continuous layer is in the center of the wall; other designs have the continuous layer at the interior. You can also do the math for the UA alternative, which basically says that if you have thick enough walls you don't need to worry about thermal bridging.
> The only thing they didn’t get into was the WRB. I guess if the first layer of sheathing was regular 5/8” ZIP you could just tape the seams but if you used OSB or plywood you might have to use a liquid applied product before you put up the ZIP R.
No real reason to detail the first layer with tape (or a liquid applied product), as with Zip R as the outermost layer, you'd want it to be the water and air control layer.
When I extensively renovated my home, The addition areas were Zip R over 2x6 walls and all the existing walls got a layer of Zip R as well. The existing walls all had board sheathing, and part of the reason I used Zip R in the first place was that it was a way to air seal that old sheathing *without* touching every board sheathing gap.
rockies63,
This is the second building assembly you have recently linked to which proposes an additional layer of sheathing. Broadening the discussion out a bit, the question that comes up for me is: If the only criterion for deciding to add materials to an assembly is that they improve it, however marginally, how do we know when to stop?
So for example, why not add a third layer of sheathing to both assemblies? Conditioned attics could definitely benefit from a vented over-roof, both to aid drying, and prevent ice dams in colder climates. And sheathing the inside of all the exterior walls with plywood adds a variable perm vapour-retarder, a secondary air-barrier, and provides backing for drywall, trim, window covering hardware, and cabinetry. The usefulness of both these new layers would also be enhanced if the sheathing was 3/4" to hold fasteners better.
What mechanism should we use to decide a perceived problem warrants any given solution?
Great question, Malcolm. In my world, that mechanism is affordability, with a measure of "how everybody else is doing it", a trace of aesthetic, and virtually no "green." I appreciate Risinger's videos for showcasing new stuff, but it's a rarified world that's way beyond the means of most of us. I wish he would talk sometimes about techniques that are truly scalable for the housing crisis. A few rich folks with well-performing (and usually huge) houses does nothing for that.
AndyCD,
I agree - and if you do add in the "green", the argument becomes more persuasive. There seems little point in, for instance, trying to minimize the concrete use in a project, while at the same time adding large amounts of other materials.
" If the only criterion for deciding to add materials to an assembly is that they improve it, however marginally, how do we know when to stop? "
This is why I sometimes hesitate when I see people using double walls. This nearly doubles the amount of wood required to frame those walls when the real goal is to achieve higher R-values, not increase the amount of structure.
But it does make sense to do that in some situations. I suppose we know when to stop based on diminishing returns.
Am I correct that Zip R is a vapor barrier? Is it OK to have a vapor barrier on the inside and the outside if the one on the inside is one of those smart vapor retarders?
No, the fiber-faced polyiso in Zip-R sheathing has similar permeance to the OSB layer, in the ballpark of 1 perm, and the water-resistant coating is vapor-open at something like 15 perms.
Malcolm: In your comment #1 you mention that by using the ZIP R you lose the benefit of your sheathing being kept warmer and consequentially kept drier by the continuous exterior insulation". Since the ZIP R has the continuous insulation on the inside of the assembly, why would it matter if the exterior sheathing is colder? The heat flow from the inside of the house towards the outside would be dramatically slowed or stopped by the continuous rigid foam on the inside of the sheathing, wouldn't it?
In your comment #9: I tend to want to explore assemblies and products that I've never seen before. There must be a reason as to why the builder chose that assembly or product, I'd just like to hear what others think of it, or if they can possibly think of improvements to the assembly of better methods altogether.
My main issue with ZIP R was the shear values, and I still think it gets harder to achieve them the thicker the layer of foam between the ZIP sheathing and the wall stud. However, what if you used lateral metal bracing for shear instead of the additional layer of exterior plywood or OSB?
Jollygreenshortguy: What exactly is the "shearwall aspect ratio"?
Finally, as to Matt Risinger's sponsored videos, if I were being offered free products (or products at a greatly reduced price) to use when building my home I would certainly take them, but that doesn't mean that I'm going to put garbage products in my home or recommend them to anyone else just because they gave me a price cut. Even if Matt never personally used any of his sponsor's products I'd still like to know about them.
Rockies, I feel that Risinger's content is increasingly sponsored, which leaves the audience wondering at times, trying to discern content from commercial. Like you say, as pros in this field we are willing to watch anything that educates us about new products, and the channel seems pretty open about disclosing when something is "sponsored." But still, his tone seems fawning at times, and I worry he's not being objective. His use of some over-the-top stuff seems goofy, like he'd never use it if he had to pay for it or if he didn't have a blank check from his client. Yeah, I'm jealous of the free stuff too.
The aspect ratio is the height divided by width of the braced wall element. It needs to be factored in the building design if using ZipR. It is not a 1 for 1 replacement for wood panel shear walls.
rockies63 - "aspect ratio" - If your floor to ceiling height is 8' then your Zip-R panel has to be at least 4' wide (1:2 or 4':8') before it will be considered to contribute to the shear resistance of your wall. Anything less than 4' wide is too flexible to be useful. For a 10' ceiling your panel would need to be at least 5' wide.
For a lot of house designs this constraint can be annoying and overly limiting.
If you use plywood or OSB on the other hand, you can go down to wall sections as little as 2' wide and still have them contribute to the strength of your walls.
Jollygreenshortguy: What if you added lateral metal strapping to the wall studs for shear and then used ZIP R? Could you reduce the aspect ratio then?
I can only imagine that achieving shear values get more and more difficult as you move up to ZIP R12 with all that foam.