Metal roof on purlins and heating

Hi
I had a metal roof guy tell me my roof won’t pass code and will have water issues. (I don’t believe him, so though I would ask the experts) The plans passed and I got a building permit.
Its a detached garage ( so not that worried anyway) the roof is a engineered truss 6/12 48″ O.C. with 2×4 purlins laid flat 24″ O.C.
The plan was to have metal roof screwed to purlins, sofffit to ridge venting. ( not sure if I need this)
Then blow in cellulose insulation. over the 1×4 strapping holding up the drywall. Heat below.
I have had some concern of water dripping off the metal roof to the cellulose and causing issue.
Not sure if anyway to prevent this, the one metal company offers a coating on the underside of the metal that supposedly stops this, not sure if its a gimmick??
So will my roof work or are there problems down the road?
Thanks for the input.
GBA Detail Library
A collection of one thousand construction details organized by climate and house part
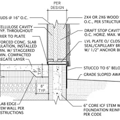
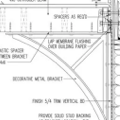
Replies
Judging from your description it appears the issue revolves around the omission of roof decking & associated underlayment. Is that correct?
If so, then the builder is correct. Condensation will form on the underside of the metal roof and drip down onto the cellulose insulation below it. How much condensation depends on your micro-climate.
Dave:
I have an unheated attached garage with a metal roof on trusses and purlins (2x4 laying flat on 24" centers). I liked the idea because there is much more meat of wood to fasten to. -an inch and a half vs half inch (or more depending on what thickness decking you use), and because it is cheaper. That said, I do get some condensation when conditions are just right (wrong, really) in my cold climate. It does not happen that often, but I'd prefer it didn't at all. In your case, with good ceiling insulation and some version of air barrier, I would not think condensation would happen. Plus, I assume you would have ventilated space above the insulation.
Dave,
Code requirements vary quite a bit. If it were me, I would call my local office and pose a hypothetical. They may have fewer concerns about a detached garage than attached garage or home.
Question. Is this roof already built, or do you still have an opportunity to add sheathing?
So I'm in Zone 6 cold winters and hot summers.
I just don't see that much condensation forming, that it would drip down into the cellulose and cause issue?.
The trusses and purlins are being assembled currently. I have no plans to put wood sheathing on. Way to much money, plywood roughly $50 a sheet.
As for air ceiling I am trying to figure out the best approach to air seal this.
Dave B,
Your assembly just needs some underlayment. Most codes would require either building paper or synthetic underlayment, and eave protection (thicker underlayment) at the roof overhang. Any condensation will drop onto the underlayment and later evaporate.
Most codes also require ventilation of the attic, and I'd take another look at the spacing of your roof purlins, the need for truss bracing and the span of the furring for your drywall, to make sure they meet code on a 48" truss span - which is very unusual. These should all be signed off on the engineering that come with your trusses.
As far as air sealing. Your drywall , with any penetrations sealed, will suffice.
The trusses are signed off and stamped for the spacing of 48"O.C. and 24" O.C. purlins. Again this is a detached garage, which falls under the low human occupancy code( up here in Ontario).There are many other braces inside the truss diagonal and lateral.
The under side of the truss will have 1x4 16" O.C. for the drywall.
I'll stick with the soffit to ridge venting. and seal the drywall for my air barrier.
I'll look into the metal roof with built in condensation control. Condenstop
Dave,
As Malcolm suggested, you want to install your drywall in as airtight a manner as you can. Here is an article that discusses this issue: https://www.greenbuildingadvisor.com/articles/dept/green-building-blog/how-hang-airtight-drywall
If you are heating the garage during the winter and the warm air infiltrates into the attic, it may condense on the metal roofing and allow moisture to accumulate in your insulation.
I have had the same concerns on "pole barn" type construction, and have witnessed condensation both liquid and frozen in open metal-roofed structures. I visited Ithaca Ecovillage this year and they used the same approach on their most recent construction so they must have confidence that in a ventilated attic condensation will be rare, and the cellulose can absorb and release the moisture back when conditions are right. See http://nesea.org/project-case-study/ecovillage-ithaca-tree/general.
When I used to design industrial buildings for commercial projects we would add a thin (usually 1 1/2") plastic-faced rolled insulation between the roof panels and the purlins to eliminate condensation. The rolls were 5 or 6 feet wide.
Dave,
This type of condensation can't really be stopped by installing a ceiling air barrier. The phenomenon has to do with weather conditions. When a cold night is followed by warm weather, you'll get condensation under some circumstances, and the condensation will drip on your insulation. In most cases, the moisture later evaporates without harming the insulation. For a garage, you don't have to worry much.
That said, roofing underlayment is a code requirement. But many barns and outbuildings use the details your propose.
Martin, in my case with 4' O.C. truss and 2x4 purlins 2'O.C. where would the roof underlayment go, and what type would be required?
I figure with enough blown in cellulose and air sealing in the attic section, heat escaping from below should be minimum, so that shouldn't be a cause..
I know there will be still some condensation dripping possible because of temps., but hope the cellulose will dry out with the little that does. I still might install the "condenstop" , but that may depend on price and how much I believe in the product.
Dave,
Roofing underlayment needs to be installed above solid decking. Either OSB, plywood, or a solid board deck would work.
In your case, if your local code officials aren't insisting on roofing underlayment for your garage, I'm not going to stand in your way of proceeding without any underlayment.
I'm curious if anyone has any thoughts about doing a sort of hybrid approach where there is just 1 course of 48" wide OSB or plywood sheathing along the eaves with an ice and watershield applied (to meet code) but then transition to a membrane product for the rest of the roof. The purlins would need to be adjusted for the sheathing thickness but it seems like it could work. Any thoughts? Thanks!
Noah,
Is the idea to save money? Other than that I can't see why you wouldn't just sheath the whole roof.
Save money. Think affordable housing. If the underlayment membrane and purlins are doing most of the work then why introduce the material cost and labor of more plywood? Just trying to do more with less.
If you are DIYing it, it would save some money, if you are paying for the roof install I'm pretty sure it will be more expensive.
Installing the 2x4 purlins is about the same amount of work as putting on plywood, probably harder as you don't have a solid surface to work on as you proceed.
Getting a membrane over purlins is WAY more work than rolling underlayment over plywood. I can't see any roofer signing up for this as it is tricky to move around and easy to rip the underlayment as installed.
The one spot where I've found to save on plywood deck is with standing seam over exterior rigid insulation. Here you can either embed the 2x on flat or strap out the foam. Put the underlayment over the foam and install the metal panels without needing another layer of plywood.
Noah,
It wouldn't be an option here, as the sheathing is necessary to create a diaphragm for shear in most of the PNW. Leaving aside whether it would end up cheaper, and concerns over build-ability, to me it brings up the question as to how much can you remove from a house and still have it retain some level of robustness.
There are areas where wall sheathing is commonly omitted, or only used at the corners, and foam substituted in it's place. Some adherents to Advanced Framing also manage to significantly reduce the amount of lumber used in house. My own feeling is that it's a fine line between economizing for either energy efficiency or cost savings, and compromising the core elements the make a house a house at some point may come back to bite you.