Minimum gap between double stud walls
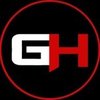
azgreg
| Posted in General Questions on
What would be considered the minimum gap between double stud walls in order to achieve a thermal break using cellulose?
GBA Detail Library
A collection of one thousand construction details organized by climate and house part
Search and download construction details
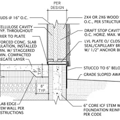
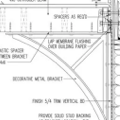
Replies
There is no firm definition of what constitutes achieving a "thermal break". It depends on what your goals are. Insulation never totally blocks heat transfer it only slows it down. If you have a whole-wall performance target in mind that can be calculated, but what constitutes a thermal break is relative.
For simpler, lower performance walls roughly doubling the R-value of the framing fraction (say, R6 or more of insulation over a 2x6 framing) is a good place to start, and most designers would consider that a decent thermal break. For double studwalls the definition of thermal break would be a bit more vague and performance-goal specific.
I'd ignore thermal breaks specifically and focus on whole wall R value vs cost. Or carbon reduction vs cost.
I think what Greg is asking is what is the smallest gap you can fill with cellulose.
Greg:
If you align your studs to the sheathing on the outside wall and to the drywall on the inside will mean the wall studs will be offset, you crate much less of a thermal bridge. For thicker walls this doesn't matter much.
For example a 2x4 double stud with 3.5" gap (11.5" thick wall) ends up around R34 with the studs aligned and R37 staggered. Not enough to loose too much sleep over but free if you can design it in.
With a 1" gap, things start to matter a bit more, without an offset you are at an R24 wall with the offset R29.
The difference between energy use in either case only matters if you are trying to hit something like a passive house energy target, in the real world, the yearly energy use difference is minimal in most climates.
We're looking to build in zone 4B (Yavapai County, Arizona) and according to one of Dana's favorite links R25-30 in the walls should be more than sufficient. That's looking at a 8"-8.5" wall so a gap between the walls would be 1"-1.5".
A 2x4 wall with fiberglass batts is R-13. A Zip-R sheathing with 2" of polyiso is 12.6, giving a combined 25.6. I think that would be cheaper and simpler.
Let me add that a 2x4 with 2" of foam is exactly the width of a 2x6. So all your doors, windows, trim, etc. can be bought in standard sizes.
Thanks DC but our preference is to use as little rigid foam in this build as possible.
OK, so use mineral wool board. The point is that for the relatively modest r-values you're talking about a double-stud wall is overkill.
Your are in pretty mild and dry climate. I would do a quick energy model of your home, for example a 2000sqft house with 9' celings in 20F would loose:
-3600 btu with R20 wall
-2400 btu with R30 wall
There is very little energy savings there. You can get larger energy savings elese where. Being a dry and hot climate, maybe adding some internal thermal mass might be worth it, but hard to say without an energy simulation.
If you are looking for budget high R value wall without foam, your best bet is 2x8 walls 24OC. With R30 batts that gets you an R24 assembly. Dense packed, it would be around R22. You gen get a further R1 bump by going with fiberboard sheathing provided you can hang your siding 24OC.
>"...R25-30 in the walls should be more than sufficient. That's looking at a 8"-8.5" wall so a gap between the walls would be 1"-1.5". "
To hit R30 whole wall with cellulose-only takes more like 9.5", so R8.5" would be the thinnest you'd want to go to reliably hit R25 whole-wall or better. See Table 3, Case 4 in this document (as well as the other details of Case 4 in section 1.4, starting on p.37 (p41 in PDF pagination.
https://www.buildingscience.com/sites/default/files/migrate/pdf/BA-0903_High-R_Value_Walls_Case_Study_rev_2014.pdf
Note that their R30.1 whole-wall assembly with 9.5" cellulose wall also used 2x3s rather than 2x4s for the non-structural stud wall. Using 2x4s for both would knock it back at least R1 or so at the same framing fraction. Pay some time working out the insulation details at the rim joist & foundation sill, which is often a weak point in double-studwall assemblies. See Figure 35 for the construction details, Figure 36 for the performance and THERM modeling they did for Case 4, which showed their band joist had less than half the whole-wall performance.
Table 2, p.10 (p11 PDF) of this document recommends R25 whole wall as the starting point for zone 4:
https://www.buildingscience.com/sites/default/files/migrate/pdf/BA-1005_High%20R-Value_Walls_Case_Study.pdf
A 2x4 wall actually performs at about R-11, assuming a 20% framing factor. Zip-R with 2" polyiso actually performs at about R-11 or lower. For a total of R-22.
A double (staggered) stud wall can also have a common (2x8) plate, does not have to have a gap. There will be increased thermal bridge at the plates vs having a space in between. The thermal bridge could be negated with polyiso (R-10) sheathing, You can technically get an R-40 center of wall in an 8 3/4" wall thickness.
Greg, one thing unique to double stud walls is that there is little penalty to increasing the wall thickness. I'd say that a 1" gap would be the minimum to be practical, unless the studs are offset. But if you're going to gap the studs 1", you might as well gap them 3" to 5". The framing labor and materials are the same; just a bit more cost for insulation.
+1 on what Michael said. If you are going to build two walls, don't skimp on thickness. If that uses too much cellulose, consider leaving the inner wall stud cavities empty (ie all cellulose between the walls and in the outer wall).
Use the inner wall as a service cavity? That would work. I'm planning on using plywood on the exterior of the interior wall for structure and the air barrier.
Walls should be optimized for the climate. Thick walls for the sake of thick walls don't make a lot of sense. Eating up an additional 4" of interior space all round the perimeter needs some purpose. If you are including an inner wall, by all means treat it as a sealed service cavity, but there is no p0int in not insulating it. That insulation will more than make up for the small gap between the two.
I went back and re-read the article about service cavities and that was one of the arguments against leaving them empty and I actually agree. Plus with our current design (subject to change at least 100 times between now and............dinner) doesn't have any plumbing in exterior walls, just electrical.
So two walls, the outer-one about 5" wide filled with cellulose, the inner-one air-sealed on the outside containing services, and (my preference would be) filled with batts. Add a rain-screen and that's a pretty good assembly. My only reservations would be about how to dense-pack the outside wall.
Couldn't the outer wall be netted, packed, then sheathed with fiberboard?
Greg,
You could, but that creates a few problems. Using something as high-perm as fibre board means you don't have a warm-side vapour-retarder, and most fibre board can't be used, or is hard to detail, as an air-barrier. Using plywood or OSB would mean the vapour-retarder is farther to the outside of the wall than is safe, and the gap between the walls, which is fairly easy to insulate with cellulose, but not batts, is on the inside, not the outside of the assembly.
Isn't plywood a vapor retarder? My intention is to have plywood as the structural sheathing on he exterior of the interior wall. What to use on the exterior of the exterior wall is still up in the air.
Greg,
Sorry - I misunderstood and thought you were suggesting sheathing over the netting with fibre board.
The problem with what you were actually suggesting is that you end up with an uninsulated gap between the netting and plywood sheathing on the outside of the interior wall.
I still think you're misunderstanding. There won't be an insulation gap. My original question was just asking about the gap between the two 2x4 walls. My intended wall is pretty much like Lstiburek's wall. Inside out: latex paint, drywall, 2x4 wall with insulation (most likely cellulose), 1/2" plywood (seams taped), exterior 2x4 wall (gap between undetermined at this point) with insulation (between studs and gap between walls), some form of sheathing (fiberboard, densglass, etc.), WRB, rain screen, cladding.
Greg,
Right - so as you suggest in post #21, you net the inner-face of the outer wall and fill it with cellulose. You build the sheathed inner-wall and fill it with cellulose. Unless there is no gap between the two, I'm missing how that space, whatever size you decide on, gets it's cellulose. It's a minor point.
Malcolm, I was thinking I would net the outer face of the outer wall, but I see the issue with that. If it rains before I get the outer sheathing up I'd have a mess. :)
Maybe leave a gap towards the top of the wall when installing the sheathing then patch it after the cellulose is installed.
Deleted
We used the inner stud spaces as a service cavity, but put fiberglass batts in after wiring and plumbing. About 8" of cellulose outside the inner studs, separating the spaces with a membrane attached to the outside of the inner studs.
Stephen, did you just cut holes in the membrane for the cellulose then tape them up afterward?
Greg. That's what we did. We used a Siga membrane and Siga tape to cover the holes. Easy and fast.
I also built a similar wall with intello on the exterior of the interior wall. I netted the top section between walls to allow some air to escape.
This was different in that the interior wasn't the load bearing.
In response to #27, here's how I'm currently thinking about the problem, with regards to panelized construction:
Build a 2x6 stud wall A, place it inside with the plywood facing out. Tape it.
Build an identical 2x6 stud wall B. Tape it. Place it outside, parallel to A, with the plywood facing in, offset by 12 inches sideways from A. Plywood should be touching plywood, with no gap.
Screw through the plywood of B, into A, and into the studs of A.
Screw through the plywood of A, into B, and into the studs of B.
Now net both sides, and dense-pack with cellulose.
Put a WRB of your choice on the outside, and if in a cold climate INTELLO PLUS or other vapor retarder on the inside.
Fur out both sides for interior service cavities and exterior vented rainscreen siding.
You get an effective air barrier in the middle of your wall, and the wall can dry to either side. The worst-case bridged R-value (heat travelling only through wood) adds 12 inches of plywood that heat has to get through. The second-worst-case has 5.5 inches of insulation, then an inch of plywood, then 5.5 inches of wood.
It's practical to sequence on a jobsite, and also probably quite strong structurally by comparison to some of the designs for double-stud walls.
Burninate,
- Whether built on-site or made elsewhere, sequencing the construction so the interior sheathed wall is erected first makes installing the outer one very difficult, on all but the flattest sites.
- As Michael Maines pointed out, the advantage of double-walls is being able to use small dimension framing, and take advantage of the space between the two walls for insulation. Using two 2"x6" walls with no gap negates this benefit.
- I don't see any advantage to using two layers of sheathing back to back. You don't need it for shear, and it represents a lot more materials for a purpose that eludes me.
- The outer-wall still has to be netted and dense-packed from the outside. Again, except for one-story houses on flat sites, this represents a huge increase in the complexity of installing the insulation.
What are the benefits of the wall you are proposing over the one Greg is suggesting?
> Whether built on-site or made elsewhere, sequencing the construction so the interior sheathed wall is erected first makes installing the outer one very difficult, on all but the flattest sites.
Could you elaborate on that?
> What are the benefits of the wall you are proposing over the one Greg is suggesting?
Structural wind rating (in relation to a wall with minimal front to back connection). Warm sheathing with low condensation risk, but dries to both sides. Supposed benefits of application - somebody suggested that dense-pack installers have practical difficulties achieving consistent density with thick cavities and obstacles in the cavity. Ease of platform-framing the inner wall. The potential to balloon-frame the outer wall, creating a consistent air barrier and a low-thermal-bridge design at the floor transition (and eliminating concerns with eg rim joists). If you can do panel prefab incorporating cellulose, the potential to go from foundation to drying in the roof in a single span of a few days of sunny weather.
> As Michael Maines pointed out, the advantage of double-walls is being able to use small dimension framing, and take advantage of the space between the two walls for insulation. Using two 2"x6" walls with no gap negates this benefit.
I think carpenters have historically and are currently (for profit margin reasons) in 2019 too focused on minimizing lumber usage. Labor is often substantially more expensive than lumber these days, and lumber arguably fixes carbon in a beneficial way. CLT is rapidly coming into vogue at R-1/inch.
- If built on-site, walls are typically framed on the subfloor then stood. If brought in from elsewhere as panels they still would need someone to set, fasten and brace them. In each case the worker would have to be outside on ladders or scaffolding, because the inner-wall precludes access from the floor deck.
- The wind rating is mitigated by applying to a structural wall part way through the assembly, meaning much of the outer-wall is unprotected. Very similar wind and shear resistance could be achieved by one layer of sheathing nailed into both walls from opposite sides - or more often using hold-downs and other hardware.
- The advantage of less wood in the wall is mainly to decrease the framing fraction, allowing for more insulation. I'm having a hard time getting my head around the idea that we should use more wood in every build to sequester more carbon.
More generally, unless a facility exists to make these panels, I don't see much advantage to a builder thinking up their own system. Are you suggesting making your own panels somewhere, or getting them made by an existing manufacturer?
The second part of that idea is to dramatically strengthen the structure and eliminate interfloor thermal bridging & rim joist problems by making the outer walls balloon-framed and shipped in house-height 8' wide panels, and making the inner walls platform-framed and shipped in floor-height panels as wide as the house... but I'm still iterating on how you would connect it all and work the window rough openings into it.
I'm sorry, but I really don't see the point of what you're proposing. A 2x4 wall is strong enough to hold up a house. It can be made almost completely airtight. Where it's lacking is the thickness to hold insulation, and thermal bridging. A double wall cuts thermal bridging and gives more thickness, but so does putting a layer of solid insulation on either side of the wall.
There is a real down-side to overbuilding. First, you have to think about the environmental costs of unnecessary materials. More crucially, as your structure becomes more complicated, there are more opportunities for things to be implemented poorly or even completely wrong. I'd suggest checking out this article:
https://www.greenbuildingadvisor.com/article/combining-exterior-rigid-foam-with-fluffy-insulation
If you don't want to use foam, substitute rock wool board for foam.
Thanks DC. My preference is no exterior insulation at all. We're planning on building in an area (4B) where the sheathing won't be in any danger. It's going to be a simple home. less than 1200 sq ft, 2 bdrm, 1 bath, single story on a raised slab.
Greg,
Sounds like everything is on the right track. You should end up with a great house. Merry Christmas!
Greg,
Looking over all of the responses to your post it was really response #13 from Akos that caught my attention.
"Your are in pretty mild and dry climate." - 4B, high elevation I presume
"If you are looking for budget high R value wall without foam, your best bet is 2x8 walls 24OC. With R30 batts that gets you an R24 assembly..."
I am also planning a small home build in 4B, although on the New Mexico side of the White Mountains. Very similar climate to Prescott, AZ. I wonder if going from 2x6 to 2x8 is even worth the added cost. Personally, I like the idea of a single stud wall 24 o.c. with mineral wool batts (whatever thickness you can afford), and a rigid air barrier on the exterior (taped sheathing), with the windows being the building component to really focus on.
I would be interested to hear Akos further describe the suggestion for adding thermal mass to this type of assembly. What might that include?
Aaron
If that is all I would need I'm on board with that. Are you saying that you don't think thermal bridging is an issue in our climate?
I am NOT saying that thermal bridging is a non-issue. I am suggesting that minimizing the thermal bridging with a 24 o.c. stud spacing is the low hanging fruit. To move beyond that to double walls seems hard to justify for our region.
After finding and following GBA for 2+ years I have been tempered by the many tales of folks having a hard time with contractors just doing a good job with standard construction. Maybe in the NE dense pack contractors are easy to enlist and builders are more experienced with high performance assemblies. In the SW you'd probably have an easier time finding a well respected builder to put up an R30 straw bale wall than to find a dense pack contractor.\
Keep the wall details simple, focus on the air barrier, and save your budget for nice windows.
I hope my wife doesn't see your straw bale comment. She loves straw bale houses.
What counts is your $/assembly R value. 2x8 with batts is a simple upgrade over "standard" construction, even though R30 batts are expensive, you are still way ahead of any comparable double wall or 2x4+rigid construction in terms of overall cost.
It definitely has a lot of thermal bridging but it is more insulation than a 2x6 wall and about the same labor cost.
Depending on your energy costs, in that area, it is probably hard time justifying more than a well detailed 2x6 construction. There might be an argument for going for higher R value if you can downsize your HVAC equipment a bit.
Thermal mass is a not an easy thing to get right without some simulation. For it to work, you need a fair bit of temperature variation between day and night (~15F), usually the most effective location is a concrete slab on the main floor. An interior masonry wall (brick/CMU/concrete) could also work but adds a lot of extra cost.
I'm not in an area where thermal mass works well, so my knowledge on that topic is limited, but there is a lot of information out there specifically from the folks down under.
Lot of good ideas here. Following is my assembly from exterior
1. hardie siding
2. rain screen
3. WRB
4. 2x6 exterior load bearing . 16 inches on center with rockwool between studs
5. Vapor retarder (Smart vapor retarder from 475)
6. 1 inches gap
7. 2x4 interior studs . 24 inches on center with rockwool between studs
Insulation R value would be around 38 and effective would be around 25-28.
Question: do I really have to fill the gap between the studs. Would it have any moisture problems in the future. Trying to avoid dense pack cellulose if I can .
Thanks for your inputs. Appreciate it