Minisplit in tandem with a conventional heat pump?

A friend is getting ready to build a 2800 sq-ft retirement home in the hot and humid south, (Houston). His HVAC contractor is recommending a 5 ton, two stage heat pump. This is ~ the traditional 1 ton / 500 ft2 formula that prevails in this area with the added benefit of the two stage compressor. But 5 tons seems like a lot for a tight house and 2.5 tons is hardly the optimal dehumidifier in the light HVAC seasons. The house will be insulated with closed cell foam in the walls and under the roof deck. It is not what you would call an open floor plan.
Our question is would the house be more comfortable with a 3 ton single stage unit for the main house and a 1 or 1.5 ton Mini-split in the Master suit? It seems to us that this could accomplish both dehumidification and partial zoning without unnecessary complexity? Air changes will probably be handled with an ERV.
GBA Detail Library
A collection of one thousand construction details organized by climate and house part
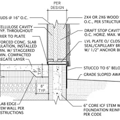
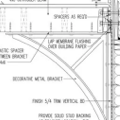
Replies
Dean,
Does anyone ever perform heating and cooling load calculations anymore? These calculations are required by most building codes.
Once the calculations are performed, you can start thinking about designing your cooling system. For more information, see Saving Energy With Manual J and Manual D .
So my friend did the Manual J three times and the answer comes up 4 tons. As always the contractor had a reserve built in. But the real question is still, does anyone have Southern experience using a mini split, in parallel with a conventional single speed heat pump to get dehumidification without an expensive dehumidifier or a full variable speed unit? This is can not be a $200/ft2 house and money will first go to sealing and insulation. 4 tons will be a great mid summer cooler but even a 4 ton, two speed unit will be over sized for dehumidification on the clammy spring/fall nights. We understand the relationship between Humidity and Comfort, we are just trying to get there on the common man's budget, both initial and operating.
So is anyone out there using this approach and is it working well for you?
If the common man has a budget, maybe he could consider building something smaller than a 2,800 square foot house. :) With an efficient floor plan, smaller size can be barely noticeable.
How do you end up with 4 tons of cooling for a 2800' house? Is there a lot of west facing window area or something? Are they including load for ducts & air handler being above the insulation that shouldn't be there, if it's being insulated at the roof deck?
Seems high. I could believe 2.5-3 tons though.
In a very tight house a room dehumidifier located in a room with lots of air transfer volumes to the HVAC is enough to cut the latent loads, even in Houston.
Even if the master bedroom suite has floor to ceiling sunset-view windows it's unlikely you'd need anywhere near 1.5 tons of cooling in there. There might be a case for a 3/4 ton mini-split though.
Closed cell foam in framed walls and under the roof deck isn't really a great value, and it's quite expensive to get to IRC 2012 code-min R38 for US climate zone 2 in the roof. ( http://publicecodes.cyberregs.com/icod/irc/2012/icod_irc_2012_11_sec002.htm ) That makes me think part of the high load number is that they're not taking it to code min there. That would take 6" +, at about a $6 per square foot of roof area. It would also have to be applied in three 2" lifts with a cooling off period between lifts to avoid shrinkage or fire-hazard issues.
http://publicecodes.cyberregs.com/icod/irc/2012/icod_irc_2012_11_sec002.htm
Doing R38 with 9-10" of open cell foam would have less thermal bridging (due to the longer paths through the structural timbers), and delivers slightly higher air-tightness, and could be done in two 5" lifts without creating problems. And, it would be half the total polymer, and WAY less global warming potential.
The only reason to go with closed cell foam under a roof deck Houston would be the enhanced resilience under hurricane winds, due to it's structural strength and adhesive properties.
Dana,
Thank you for excellent feedback and comments. Our logic was that the over sized Mini Split, in the master suite, could run at very low speed to provide energy efficient dehumidification during the day,. During the night, comfortable, dry sheets while maybe cooling the rest of the house buy itself with the bedroom doors open? The Mini Split provides the variable speed and high efficiency at a good price point where upgrading the whole house unit gets expensive quickly. The design temp for Houston is about 95 F but we do see week long excursions over 100 F. If the target is 75 F, this is at least a 25% overload. Schedule 10-20 birthday guests over on that hot day and it gets very sticky fast. Hence we are trying to keep a little in reserve without being wasteful the rest of the time.
Understand that neither of us had heard of GBA, Building Science, Mini Splits, Rainscreens just 9 months ago, So much to learn, we are on a very steep learning curve but you would be surprised how many links and concepts we have shared with others.
Your foam comments are especially appreciated, obviously we need to dig deeper there. Thank you for your patience.
Nate,
Bad choice of words on my part.