Minisplits – overcharged vs undercharged – there is a way to tell easily

So we all know the mantra – “if in doubt pull out the charge and weight it and then put it back in”. Never try to judge by subcool/superheat or target pressures as it is not accurate, blah blah blah. We who do this for living know the drill, right?
Well , in my line of work sometimes it is not practical or possible to know how much refrigerant needs to be in let alone take it out. I do large commercial installations so often even the lineset length is not known. Go figure.
So a couple weeks back I had to refill an installation where nobody knew how much gas was supposed to be in it. So I call the manufacturer (one of the big Japanese brands) and after lengthy discussions because of the importance of the account I get to talk to some smart folks in engineering.
I told them that when too many unknowns I would crank up the heat in heating mode and shoot for 400-425 psi on the high side and look to confirm 1-3f degrees superheat. They tell me this is close enough, but there is a better way to precisely know if I am under or overcharged. Do I have energy monitoring on the circuits? I do…. turn on heating and after 15-30 minutes of operation observe compressor draw in Amps or Watts… The strategy is that for every value of resulting compressor draw from a combination of rpms and load the high pressure should be fairly constant over time. So if you are looking at energy monitor you should see the compressor stepping up / down and the high side (draw) moving up/ down and staying there as a constant as long as compressor is on the same step. If at any compressor rpm the high pressure is steady for a bit and then starts climbing forcing the compressor to step down- the system is overcharged. If pressure is steady and then starts progressively dropping forcing the compressor to step up- the system is undercharged. Steady compressor rpm should equal steady draw (pressure). The system should be in a steady state (hence the 15-30 minute delay) so the pattern should be repetitive- only then it can be used as a charge indicator.
Best working strategy is to slightly overfill system (put what is on condenser label plus some more as you deem appropriate according to lineset lenght + some more) and as it runs at constant rpm the pressure goes up (best observed by increasing amps/ watts on compressor) start taking gas out until the climb stops. Wait for next cycle and if it does it again- take gas out again until for every compressor rpm setting the draw reading (pressure) stays the same until rpms change. I was advised to not do the opposite- undercharge and then introduce gas as the pressure dips at steady rpms until it becomes constant as I can end up with an undercharged condition where the pressure is constant (good) but due to the compressor working extra hard… so you always want to take away until flat vs introduce until flat.
I followed their advise and the system was spot on as superheat, pressures and delta t.
I hope this helps the curious handy homeowner and also can confirm/ deny suspected charge issue for a tech in a pinch.
Now, this is not an advice, but more of another tool in the toolbox. Use at your own risk 🙂
GBA Detail Library
A collection of one thousand construction details organized by climate and house part
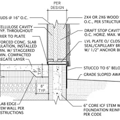
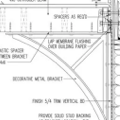
Replies
With a variable speed compressor, how do you get constant speed? Run it at 100%
I can go into checkout mode and force a constant 'demand', is this constant RPM?
The way they all work is generally upon start compressor ramps up in the first 10 minutes or so to max or close to max rpms, then drops rpms steeply to what it thinks will produce around 400 psi high side (based mostly on current outdoor temp I believe) and then it steps up and down over time in small steps. Eventually after 30 minutes or so it will settle to certain speed that will maintain said pressure... or at least will move up and down in small steps every 1-5 minutes depending on brand. That is where your observation takes place... When the compressor is at constant rpm for 2-5 minutes or so the high pressure should stay constant too. If at constant rpms the high pressure is constant all is good... if however the high side is constant for a minute or two and then curves up (you can tell by the draw on the compressor increasing) the system is overcharged... if it curves down (compressor draw drops)- it is undercharged. So ideally at any compressor rpm when system has settled high pressure should be also constant and not increase or go down.
The thinking as it was explained to me is that the system has tables with compressor rpms vs pressure vs outdoor temp. So for any scenario when system has settled the firmware selects rpms that it thinks should produce the correct target pressure and subcool/superheat If the gas amount is just right, the system will arrive at that state fairly quickly and stay there without much manipulation of compressor rpms and ev pulses. So if the system has settled at particular rpms but pressure goes up - there is too much gas for that particular installation. The goal is to match the gas amount to the firmware expectations so it does minimal amount of compressor rpm adjustments.
And yes- often in the commercial world the tag on the outdoor is gone, destroyed, faded and you dont know how much was in there after all leaked out... and you cant calculate it because you see one lineset going into the wall, but in there there is a manifold and 5 different diameter pipes throughout the branches and you dont know how long any of them are...
And yes- this is not a gas-n-go procedure. It took me 1 hour to observe and reclaim in small steps gas from the system. I did the same on Friday on a different system with same great success. So in my mind this works. Confirm ofcourse with service tool pressures are where you need them to be, subcool/superheat and compressor exhaust temps are within limits.
Great story. As unfortunate as the reality is, I must agree. Thank you for sharing.
The only issue with this method is how one manufacturer's software responds to conditions another will respond differently. The secret sauce to each VRF OEM is the software.
No matter the OEM, a technical may need one or two days to balance the charge and leave the service tool connected for data logging over night.
Sadly, there are a lot of “HVAC techs” the do almost nothing but play the gas and go game. The add gas and go to the next call all day long. When the customer gets tired of paying, they quote a new system. Turns out to be a profitable business model unless they call someone else and they actually fix the leak and make you look like a fool.
The way I see it if the unit was install properly, it had the correct charge at that time. The system can’t make refrigerant so over charged is impossible and if the system is every under charged there must be a leak to be found and repaired. Repairing the leak will require evacuating the system and you will weigh in the correct charge at that time. In short the charge should not need to be adjusted every time a tech is on site.
I seriously doubt the manufactures repressive actually put his job at risk and recommended your charging method. My guess is he listened and said that it might get you close but they are not rewriting the manuals.
No way the gas and go guys are sitting around for 15-30 for the system to stabilize and my guess is you could recover the charge and weigh it back in in less time and neither are you or you would follow the procedure and be done in less time.
Walta
Greenright,
This is great info, thanks for sharing it.