Missed Thermal Bridging in the Slab

We missed putting the thermal bridge in the doorway and just poured a 4″ slab through it. Is there any reasonable solution? Climate zone 5, Salt Lake City. See attached picture.
Thanks!
Matt
GBA Detail Library
A collection of one thousand construction details organized by climate and house part
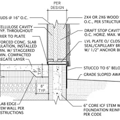
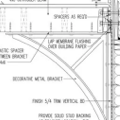
Replies
No great solutions, but it's not going to really cause much trouble either way. You can minimize the heat loss by installing an inch or two of edge insulation between the floor slab and whatever your stoop treatment will be. Depending on your floor coverings, even a half inch of rigid foam on top will warm up the slab at the threshold. Of course more would be better, but eventually you get a big enough step that people trip over it. It wouldn't be all that hard to cut the concrete out of the door opening and replace it with a 2" concrete (or stone) slab with 2" of XPS foam on top. That would be plenty stable for installing a threshold over it.
The biggest issues with it as-is, are: 1) some heat loss. If you are going to super high performance, you will notice the difference. For a PGH, probably not. 2) There is some potential for warm, humid interior air to condense on top of the slab, under the threshold in winter. But in Utah, the air is pretty darn dry and in winter, the interiors are even drier. So unless you have some reason that the interior air will be particularly damp in winter, this is probably not an issue for you.
Condensation is not a problem in winter. My current home is slab on grade with no insulation for the concrete and it has no issues.
Would that 8” concrete lip break off of we did a 2” saw cut and used a can of spray foam in the 2” gap we cut?
Matt,
Is this a garage?
No, it is a walkout basement. I just added a photo that shows what it was like before we added the slab. I want to fix it but maybe it is more headache than it is worth. My contractor has not got back to me with his perspective yet. I suspect he will recommend letting it go.
Matt,
I was just confused because it is rare to see a slab extending out between the stem-walls. If you decide to fix it, it's probably easier to remove that chunk of slab (saw cut or just jack hammer), continue the insulation, then re-pour the sill with several anchor bolts to keep it in place. It may well be more of a headache than it is worth to do.
Thanks for the reply. There is about 200 linear ft of basement wall and this 4ft represents 2% of my wall missing insulation. I will have to see if the contractor has any ideas.
Malcolm,
I'm sure this is obvious, but not being very familiar with slab on grade foundations , how would this usually be done for houses with SOG with stem walls? Slab poured even to the top of the stem wall?
And why is it done differently for garages? Just to keep the garage slab close to grade for vehicle entry? (I ask partly because I wonder if building a gravel/paved ramp up into the garage wouldn't oftentimes be better than having a low slab in relation to grade. To better protect against water intrusion and flooding.)
maine-tyler,
There area few variations, mainly different ways to deal with the joint between the stem-walls and slab, but yes, they are almost invariably the same height.
https://www.greenbuildingadvisor.com/article/insulating-raised-slab
I agree: the way slabs on garages are dealt with at the doors is ripe for a re-think. They are very difficult to insulate, and the transition between the usual 6" to 8" space between the top of the stem walls to grade, and the flush entry slab, is pretty awkward. I hope someone re-imagines it.
Malcolm, do you have any pics you can share? This article is locked.
lance p,
Malcolm, do you have any pics to share?
Tyler, garage slabs extend to the exterior so there is not a vertical joint in the floor which would trap water and debris, and direct water under the slab. It's also hard to get the top of a concrete wall nearly as smooth or uniform as when troweling a monolithic floor slab. It takes extra effort to form the opening for a slab that extends to the exterior; it's faster and cheaper to pour the slab more or less flush with the top of wall. Since it's extra work anyway, I like to make the slab edge thick at the door; 8-12" vs. 4-5" for the rest of the slab. It's stronger and you can connect the slab to the wall with rebar so frost doesn't separate them.
I agree with Malcolm that this is an area that needs improvement. I have thought about it a lot, with no great solutions other than to not heat garages, which seems to be a losing battle. Any solution would have to include re-thinking the overhead door system as well.