Unvented Roof Construction & Ventilation in Tiny House

Hello!
I have a few questions as I’m in the midst of redoing my tiny house roof (for the 2nd time) due to mold. I’m in western WI – Climate Zone 6A.
History of Build:
Original Roof Construction:
We were given faulty advice from green building materials consultant to put a non permeable Vapor barrier on the exterior of our sheathing roof and walls and with no interior vapor. I am an inexperienced builder and didnt understand a lot of this in the beginning. So roof and walls were covered in non-permeable vapor barrier. Roof pitch 1.5/12 (also didnt understand implications of this). Interior to outside: Pine tongue and groove, 2×6 rafters filled with r-19 wool insulation, exterior grade plywood, denny foil vapor barrier, metal barn siding for roof. Roof was unvented (unintentionally). We heat with wood. No attic. Some mold happened on interior side of roof sheathing.
2nd Roof Construction:
We were given advice that we needed to vent our roof and take the vapor barrier off of the outside of the house, especially without having one on the inside. Roof from interior to exterior: pine tongue and groove (no mold or moisture damage to original), 2×6 rafters with wool batting, cardboard baffling to give a 1-2 inch air space on top of insulation, new exterior grade sheathing, metal barn siding roof. I drilled 2 inch holes on lower side of rafters of which there is a 1.5 ft overhang. I vented the high side. Significantly more mold happened than the first time and was most heavy around the wood stove area.
3rd and current roof construction:
I have now learned through reading some building science type articles that with no attic and such a low pitch single slope we want an unvented warm roof to prevent condensation from happening in rafter space. I have also learned the metal roof material (the barn siding, not the seamless kind) is not good for our pitch. So here is our current plan:
Current build plan: from inside to outside: pine t&g, some kind of vapor barrier/retarder, 2×6 rafters with wool batt insulation r-19, OSB, 7″ of polyiso = R20-24 (3″x4x8s aluminum backing, 4″x4x4s paper backing), 1/2″ fiberboard, 45 ml epdm rubber.
Additionally I’ve purchased a through wall erv (TwinFresh Expert” from US-Vents) to help circulate and control air.
**Our hope was to have a draftier house to allow for good air flow as opposed to building it air tight. We are learning that may not have been the route to go but are now trying to creatively deal with it on a budget. Biggest concern is mold and moisture not heating our space. Despite the drafts from windows and door our house is warm (sometimes hot) in the winter as long as we keep the wood stove going when sun isnt shining and our lower sleeping space is cool which we like.
Questions I have are:
1) what vapor barrier/retarder would be recommended to put on the rafter side of the pine tongue and groove?
b) will I be okay installing this barrier in the ceiling only, for this winter or do I need to make sure I get in the wall as well? We mostly have had very little mold in the walls at this point but I am concerned with a vapor barrier in the ceiling that this will push moisture out into walls. I am hoping ERV system can help alleviate this. I’m balking at putting vapor barrier in walls as it means tearing down the shelves, t&g there, stairs, counters, etc -while trying to live in it and colder weather coming and with a 4 year old.
2) I’m installing the polyiso on roof right now. I’ve been layering it all up, putting a bit of liquid nails to hold the different layers (CDX ,aluminum faced foam, paper faced foam, fiberboard) in place, Good Stuff foam in the cracks, and planning on using a 9-10 inch screw with a plate on top through the layers of foam and fiber down into sheathing/rafters to really hold it all in place before sticking the rubber down. Am I going to create a bunch of little metal thermal tranfers with the screws running from just under the epdm down through my foam and into sheathing (they will stick out of sheathing into interior of space if I miss the stud). Is this a problem; is there a smarter way to do it?
3) any best practices for where to install the through the wall ERV? When we called US-Vents and described our place (8.5×24 ft trailer, 11 ft tall tiny house, shed style roof with 1.5/12 pitch, and lofts at both ends, 1 higher and 1 lower) they answered really quickly that anywhere would be fine and didn’t educate us in any way beyond that. Left us feeling uncertain, but the item still seems like best one for our situation and budget. We have no bathroom in the tiny house, so no shower vapor. The natural airflow goes from the kitchen side, which is close to the wood stove where we also cook from time to time, to the opposite side where we did have significant mold in the corner of the wall sheathing. We currently have a low force fan installed into the wall on that corner.
Thanks!
Alex
GBA Detail Library
A collection of one thousand construction details organized by climate and house part
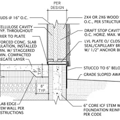
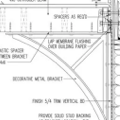
Replies
The air barrier of your wall needs to connect to the air barrier of the roof. The ideal location for your air barrier and vapor control would have been directly on top of the CDX beneath the polyiso. Peel and stick is a common choice being that it self-seals at screws run through the foam.
Had this been the approach, you wouldn't need any additional membrane vapor control at the interior aside from latex painted drywall (class 3 vapor retarder). I wouldn't trust canned foam at polyiso joints to act as a primary air barrier. Foil tape on foil facing would be better, but it still needs to connect to the wall --that's the weak point for air leakage.
Alex, you aren't thinking enough about air sealing. What is your plan for testing air tightness?
The problem with both of your earlier attempts has been the lack of warm side air barrier. T&G is not it, a well detailed vapor barrier could work if you are careful. A sheet good of some type is better, taped osb or cdx, drywall or foil faced rigid insulation work much better. Since you are moving the insulation above the deck, sealing the deck is the simplest.
Slope rating on metal roofing is interesting topic, the reason you see a cutoff at 3 in 12 for most roof profiles is not that they won't work but the test they use to evaluate them changes.
For low slope roof, the metal panel needs to keep 6" of water out. This is reasonable for large commercial roofs, but never happens on a small building. So even though the roof is not rated for low slope, it generally will work. The nice part about metal roof is that you can install it on 1x4 strapping saving an extra layer of plywood on top. You still need an underlayment over the foam.
Your proposed roof does work, just as Jason said, you need to air seal the roof deck. The simplest is taping the seams of the roof deck with a quality sheathing tape. Normally you need a class III vapor retarder (craft faced batts or smart vapor retarder) on the warm side of that assembly but you are installing much more than the required 50% exterior rigid, so you can get away with not including one.
The new roof won't "push" any moisture into your walls.
A house that is less air leaks, which will be the case with a well detailed roof, will have higher interior RH. This could cause issues with your walls. Make sure to stay on top it, any ventilation (ERV included) does reduce your interior RH but it still won't be as low as it was with a leaky house.
Generally if your walls are plywood and a siding that allows for airflow (vinyl or siding over rain screen) are pretty robust and you might be able to get away without doing anything extra.
If it does become a problem, the simplest would be to add 2" or so of rigid insulation on the outside. This does mean pulling off the siding, so it would be last resort.
P.S. 7" of polyiso is closer to R35 even with cold temperature derating taken into account.
Thanks for sharing your approaches!
It sounds like if I tape the sheathing seams on the roof deck, install the polyiso layers like I've said (staggered seams), I won't need a vapor retarder on the interior.
I do not have a particularly robust wall (t&g, wool batting, T111 siding) - its leaky at the seams but we thought that'd help us mitigate interior RH, along with the ERV.
I've already been thinking a little of going for rigid foam on the outside, but won't be doing that this fall unless its clear its imperative. We're planning on installing this new roof, the erv, and checking to see what the upper areas of the walls look like next spring.
Anyone have any concerns about those long screws going through all the layering?
The only issue with long screws is that it is hard to get them in straight and hit the rafters. Make sure to mark out your rafter locations before the rigid goes on and make a small jig by cutting a slot the width of the screw shank into a 2x6 and use that to keep the screw straight while starting.
Also taping the seams of the foil faced polyiso with a budget sheathing tape is a good idea as a backup.
Akos,
These aren't accurate enough for fine woodworking, but are great for sinking screws though thick foam: https://www.leevalley.com/en-ca/shop/tools/jigs-guides-and-fixtures/73237-drill-guide?item=46J8370&utm_source=free_google_shopping&utm_medium=organic&utm_campaign=shopping_feed&gclid=EAIaIQobChMIosrEzd6b7AIVt_3jBx06-QhBEAQYAiABEgJm9vD_BwE
I'll tape the sheathing & the metal faced polyiso layers.
another idea regarding the screw situation:
What if I put the screws down through the polyiso, installed the fiberboard on top of that with liquid nails, then adhered the epdm to the fiberboard. Epdm would also be attached all around edges with metal trim.
This way seems less secure in that the screws and plates aren't mechanically fastening the fiberboard, and therefor the epdm. The epdm seems a bit less secure.
On the positive side, this would insulate the screws with 1/2" of fiberboard & they'd be a smidge easier to aim at the rafters. I can also imagine the epdm being secure enough with all the edging metal holding it in place down by the fascia, and it'd be easier to replace when that time comes in 10+ years.
thoughts?