Nailbase roof retrofit

I’m a roofer in Western Pa. I am looking at a project with a cathedral ceiling throughout. It was built in the 70s and had little to no insulation in the roof/ceiling. A local SIP manufacturer will make me 5 1/2” nailbase panels to insulate the entire roof. I have a layering question. I need to weather in the roof as we strip it. 1/2 the roof( 20 sq) is wood shakes on a 20 pitch, so it will be slow going. As best as I can tell, the roof deck is 1 1/2” t&g timber decking. I would like to: put down a layer of Titanium paper to weather in, then the nailbase, then more titanium and ice and water, then aluminum standing seam. Any obvious issues with layering in this order?
Thanks in advance for any advice.
GBA Detail Library
A collection of one thousand construction details organized by climate and house part
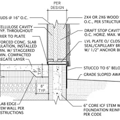
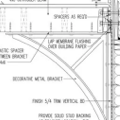
Replies
With any over roof you need to make sure you have a decent warm side air barrier otherwise you can end up with SIP rot.
If there is just t&g for the ceiling, your best bet is to cover the whole thing with a peel and stick (ie blue skin vp100) to seal it up.
Roofing underlayment could be detailed to be an air barrier, but it is hard to get right.
The rest of your stack up is fine.
A 20-pitch? Wow. So basically a sloped wall ;-)
As far as I can tell, your proposed approach should work fine. My only advice would be that because nailbase panels shrink a bit over time, there will eventually be gaps between panels. Best practice is to install at least two layers, with seams staggered and offset. Otherwise you could get moisture accumulation at the sheathing, and pay a bit more for energy. The moisture accumulation is the bigger risk.
Moisture accumulation in a SIP roof is well documented. For that roof I would select a variable permeability air barrier to install on the T&G layer. Make sure to tape seams and penetrations VERY well. With that much pitch you don't want or need ice & water on the top layer - there is a risk of moisture and condensation on the bottom side.
What is the foam core made of? If it is EPS, it will have a relatively high vapor permeability, and the quality of the air and vapor seal at the T&G becomes more important. XPS is not very green, but has lower permeability. Polyiso has even lower permeability, none if it is foil faced.
When I did my 12/12 R60 roof 10 years ago, we had similar issues with taking some time to get the topside foam installed. We opted for ice&water on the roof deck, then the foam insulation, then OSB sheathing, with the top layer of OSB being sacrificial should water get into the assembly. This turned out to be a good solution, as we lost parts of roof and flashings in both Sandy and Irene. We had zero water inside the house, as it all ran out the eaves over the ice & water layer. In fact, after Sandy I was so busy on other people's houses that I didn't even know we had damage for two weeks and a couple more storms when I saw it from the ground. Some simple topside repairs and we were back in business.
And another note: 5-1/2" of EPS only gets you to R22. Your local code probably requires R-49.