Insulated Nailbase for Basement Subfloor Labor Reduction

Preface: Climate Zone 5A, 1999 home unfinished block wall basement with (suspected) no insulation or vapor barrier under the concrete.
After much reading, I was planning on a floating assembly of concrete -> vapor barrier -> 2″ EPS -> 3/4″ OSB -> 3/4″ OSB
This should handle rising water vapor, potato chipping, and provide a very rigid floating surface.
Someone mentioned SIPs (these have OSB on top and bottom) and then I found Nailbase Insulation like
https://www.insulfoam.com/insullam-nailbase-insulation/
https://www.lunaassoc.com/wp-content/uploads/2015/03/606943_CCW-3750_CCW_R2_Base_Tech_Data_Sheet_4-8-13_V2.pdf
These seem commonly used for walls/roofing, but not mentioned for floor applications. These are not structural panels so that manes sense.
This could cut out a layer of labor (DiY) so concrete -> vapor barrier -> Nailbase (EPS+OSB) -> 3/4″ OSB (screwed to top of nailbase).
Based on reading other’s experience, I was avoiding other click together options (like DriCore subfloor panels) for various reasons. Other foam options (like DriCore InsulArmor) would still need 2x layers of OSB on top. The seam sealing would be a bit different (caulk vs tape most likely).
Has anyone done this and can offer their experience or thoughts?
In theory this all seems fine, but I am very new to all of this.
GBA Detail Library
A collection of one thousand construction details organized by climate and house part
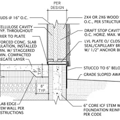
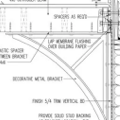
Replies
Bumping.
Additional context. For OSB I was planning on using Advantech.
I did come across this thread: https://www.greenbuildingtalk.com/Forums/tabid/53/aff/5/aft/77622/afv/topic/Default.aspx which mentioned water leaks with no way to dry. But I think that is a common risk amongst all basement insulated flooring retrofits. (Unless I am misunderstanding that thread).
I would be concerned slightly about the nail base OSB not being as moisture resistant as Advantech OSB. Two layers would be better than one, but maybe a single layer on top is still good enough to protect the nail base OSB if used.
Since your question does not seem to be getting any attention.
I do not think it makes sense to retrofit insulation in a basement floor.
The costs are to high and the saving is low.
Personally, I don’t like the idea if adding insulation over the slab because of the way it will reduce head room and the change will make the stair case no longer code compliant.
Walta
Agreed, the costs are high and the savings is low (or non existent). Some warmer climates would even lose free cooling in the summer. Also agreed that the headroom reduction and any staircase modifications are not ideal.
I am pursuing this primarily to increase underfoot comfort, provide condensation risk reduction, and retain flooring options.
The stair issue is significant. The proposed assembly would raise the floor by 3-1/2". You would have to rebuild the entire staircase to make it code-complian. I guess you could put a 36x36 landing even with the bottom step and then have a 3 or 4" step off of that, but it would be awkward.
I had given it some thought. I found this during a search for a solution:
https://diy.stackexchange.com/questions/224126/basement-subfloor-at-bottom-stair-landing
This lines up with your suggestion to have a new landing even with the bottom step. I would definitely trial it out before making it the final solution.
Another possibility would be to leave the area in front of the staircase alone. The bottom of the staircase is the foundation wall (in front) and an open layout basement area (to the left), which is where a step up cold be. Still a bit awkward though.
A little insulation is nice on a basement floor. I put 3/4" of [low GWP] XPS (because that's all that's actually reasonable available) on my slab with two layers of 1/2" plywood on top of it. LVP is the finished floor. The floor is incredibly comfortable and easily holds room temperature even below design temp for the area.
Note: I was also replacing the stairs in their entirety, so they were set up to accommodate this. That being said, if you are raising the floor, you can likely feather out the additional height over 10-12 risers without rebuilding the stairs--as long as the increased height is modest. (In this case, 3 1/2" of additional height is not 'modest'.)
Awesome, I love having options, thank you. I'll look into feathering. I've got 14 steps to work with.
2" EPS was chosen for R-10, but maybe with the plywood/OSB and floor covering less insulation can be used for a thinner assembly. I think many discussions said that even 1" EPS would easily solve condensation concerns (e.g. carpet/pad).
In terms of modest, what are possible acceptable ranges? Under 1.5"?
Hi Curious,
I'm planning on something similar in a shop/garage space behind my house. Similar setup (currently no sub-slab insulation, no poly beneath slab) and similar reasons (comfort). I posted about it a while back, and a few people weighed in:
https://www.greenbuildingadvisor.com/question/slab-w-o-vapor-barrier-renovating-garage-into-living-space
Kohta mentioned that, much like a wall in heating-dominated climates, he'd locate the vapor barrier above the insulation, not below.
It seems like the nail base would work okay (but let me qualify, I'm the furthest thing from an expert on this). I'm curious, is there a significant cost delta between (insulation + 2 layers of Advantech) vs (nailbase w/ integral insulation + 1 layer of Advantech)?
(And if anyone was wondering, no - I have not done this in my shop yet. It's going to be a bit of a pain, so naturally I started other projects and left this one partially finished)
Thanks for your thread Paul.
Interesting. I had gathered a bunch of comments regarding placing the poly between the slab and rigid.
https://www.greenbuildingadvisor.com/article/whats-the-best-basement-flooring-system
#18: poly -> rigid -> subfloor
#34: Fine to install poly on top of the concrete
#42: poly between slab and foam
https://www.greenbuildingadvisor.com/article/installing-rigid-foam-concrete-slab#comment-168352
#41: poly above the slab
It seems (I think for basements) that Martin advocates for it in contact with the concrete. I wonder if the science is different for garages, which are typically more unconditioned (temperature delta) than conditioned basements. I could see that being the case especially since it seems so difficult to decouple an attached garage from the space around it (e.g. the concrete floor of the garage extends under the garage door and to the outside).
I can still see it going both ways, however. Drainage mats and dimple mats are seem to be between the concrete and foam (makes sense for drainage to work). Some sources say a dimple mat and poly are interchangeable. For basement retrofits, I have more reference sources for the poly in contact with the concrete than I do for above the foam (like it would be under the slab).
Regarding the cost delta ... for my sqft and a google search (I haven't called around attempting to source it), the nailbase would be a few hundred cheaper (not much in the grand scheme of things). For DiY purposes, this could also save lugging another 20 sheets Advantech into my basement.
A couple of things:
You could source recycled rigid foam and save a bundle.
The floor might end up squeaking if the slab isn't even. I ended up putting some concrete anchors in strategic locations to prevent any gaps from opening and closing with someone walking. Make doubly sure the floor is tight wherever cabinets or toilet is going to go.
One thought: those sheets of 3/4" Advantech are a bear to work with, they're like 80 pounds each. Zip-R only uses 7/16" OSB, two layers of 7/16 should be plenty stiff.
I would put a few tapcons into the lower level, flooring has a tendency to slide around on you when you're working. It's frustrating to make a careful cut and then go to fit it and find the floor has moved 1/8" since you measured. Once you get a few pieces down, and a second layer to hold them together, they'll stop moving.
I have always been a little nervous about using OSB anywhere near a basement floor. What are the thoughts of the experts here on instead using two layers of 3/8 inch cement backer board (Hardie Board or Wonder Board) as the base? Or perhaps two layers of 1/2 inch exterior plywood? The backer board is only 3x5, making them easier to handle but a lot more seam length. It is also fragile on its corners, so I do not know if it would hold up over foam...The 1/2 ply is easier to handle than 3/4 OSB and would reduce the height increase by a 1/2 inch around the stairs. I think it would be enough if the seams are properly staggered.....What do you think?
Nick,
When used on floors backer-board is typically bedded in mortar on a solid structural substrate. I don't think it would hold up just screwed together over foam.
I think 1/2" plywood is definitely preferable to OSB, but would preclude the OP's intent to use nail-base as the first layer of the assembly.
The bigger question is whether the difference between OSB, AdvanTech and plywood is large enough to rescue an assembly that gets wet enough to damage any of them? I'm not sure the choice is that important.
A lot of considerations. I don't have first hand experience with any of these materials, really (not a handy guy), so most of based off of research/marketing.
I believe Kohta used cement board on top of his foam and his goal was ultimately for storage. I think one of the building science basement PDFs also mentions cement board or similar coverings that can be used keeping in mind the use for the space.
Supposedly AdvanTech is more stable and moisture resistant than regular OSB or plywood, which is why I was drawn to it.
For nail base, I would be concerned about the protection of the non AdvanTech layer under. Due to expansion gaps, I would assume water that got under a finished floor would go between the expansion gaps and get anything under it wet. Delamination from the nail base would be an issue that would not be a risk in a foam + floating OSB assembly.
Would two layers of moisture resistant plywood (or even regular plywood) survive a similar water event better than two layers of AdvanTech? I certainly don't know the answer.
I believe, also, that discussions for this type of foam/osb subfloor assembly caution against bulk wetting as the entire floor assembly would need to be removed (e.g. if the foam gets wet it stays wet).
The water events (on top of the floor) would also need to be large enough to go through any finished floor, any underlayment, and the first layer of OSB. With drain pans under everything and good grade around the house I think the main concern becomes broken/leaky pipes and floods? I think the investment balances the cost of the assembly vs the risks that would destroy it and their likelihood.
I've also considered a wedi/kerdiboard tile floor, but that is even more expensive, though surely the most water and flood resistant.
Cement board doesn't hold screws or nails well. The idea behind the two layers of subfloor is they can be overlapped and attached to each other to make a single rigid floating piece. I don't see how you could do that with cement board.
Will you have the 80 inches of head room over your landing code requires with the landing on above the insulation. If the ceiling is dropped was shimmed into level you could lose some more headroom. In 1999 most basements were 8-foot pours.
Has this basement ever flooded?
Any current moisture issues?
If you had a pipe burst is your new floor survivable?
Walta
Appreciate the extra insight, Walta.
On top of my bottom step (assuming the top of the step becomes a new landing) I've got 90". I've got about 85" under the I-Beams in the space and a few more inches under the joists.
I think this means I should be ok on headroom.
The basement has not flooded to my knowledge (4 years).
I am not aware of any current moisture issues besides what I believe to have been condensation under some plastic storage bins. The RH in the basement is under 60% during the summer. There is evidence of efflorescence in a few areas, and I am continuing to improve the grade and drainage features outside. The walls are painted white, but unknown whether it is a retarder/sealer type of paint or not.
I'm not confident on which floors survive a burst pipe. I suppose it's primarily based upon time (amount of water). I think the only solutions to intense flooding are inorganic (tile, rubber, vinyl) and removable to ensure drying (floating assemblies).
My proposed would not survive be due to using wood (ply/osb) as it fails for being organic. Many flooring types are not recommended to be installed directly on foam, so an insulated system would require wood. (Edit: also fire code requires the foam to be covered with an approved barrier, which some flooring is not).
I would not think drywall, wood trim, wood doors, wood studs, or wood blocking in metal studs survive a burst pipe either. These are 'cheap' compared to a floor investment; however, which I think is your point. I do think most homeowners insurance 'covers' burst pipes where they do not cover natural flooding/leaks.
I suppose the compromise is a plastic thermal break with a dimple mat + flooring, which would survive at the cost of comfort. Ultimately the discussion here: https://www.greenbuildingadvisor.com/article/whats-the-best-basement-flooring-system