Necessary to fully insulate deep overhangs?

I’m in southern Idaho, zone 5, “cold” region. The house I’m building has 3.5′ overhangs on the south side. It will have an exposed plank and beam roof with a 2:12 pitch, 10″ of rigid foam on top (R50), sheathing on that, and a standing seam roof.
In watching Lstiburek’s videos, he said to prevent ice dams, the overhangs on the south side of these type of roofs “have to be” ventilated AND well insulated…..WHEN the ground snow load is 50# or higher. Our ground snow load is 15#. In this day and age, we rarely get more than 4″-6″ of snow that sticks around long.
I can save myself ~$2000 by not insulating these overhangs. My question is: Might I run in to problems if I do not insulate even though I’m in such an area that does not typically get much snow?
GBA Detail Library
A collection of one thousand construction details organized by climate and house part
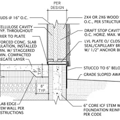
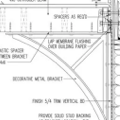
Replies
Generally when insulating roofs with expensive insulation, there is no ROI for going above code min. In case of a roof with exterior rigid, you want to look at U factor based compliance as there is no thermal bridging. Check your code but this could be either an R30 or R38 assembly. Your T&G deck also adds to this, in case of 2x6 deck, this adds about an R2.
I would also look at using fiber faced roofing polyiso (carried by any commercial roofing supply) for the roof. This is slightly higher R value per inch and tends to be significantly cheaper than box store rigid.
As for the overhangs, they don't need to be insulated but it is hard to work on without it. Continuing the insulation out is probably simpler than framing it in.
The challenge with any T&G deck is it needs to be sealed. You want a peel and stick over the whole thing, make sure the membrane is not modified SBS but butyl or acrylic adhesive. SBS can react with sap and ooze and since it is essentially tar, it can smell. If your T&G extends from over the wall plates, you need to figure out how to air seal the gap between boards. These will increase over time and even a small say 3/32" gap times many dozens of boards is a huge air leak. The best is to stop the T&G half way across the outside wall plate, carry the roof peel and stick down to the sheathing for air barrier continuity and continue with the soffit T&G from there.
A lower cost insulation option is to simply set rafters over the T&G deck, essentially build a standard vented roof over the post and beam structure. This can now be insulated with batts or loose fill. The rafter tails can be trimmed at the overhangs past the walls so your facia can look more normal sized. The bottom of this can be trimmed with T&G and fake log tails for the look. The air sealing of the ceiling T&G still needs to be the same as above.
Thanks for your post. I should have mentioned that the roof is already framed. 4x8s at 24" o/c with 1x8 t&g over that with Sharkskin Ultra SA peel and stick membrane on top of that for the air barrier. I'm prepping to finish the roof soon.
I will be using EPS, primarily due to a locally owned manufacturing plant being less than 4 miles from me. They will make any thickness I want, and it's significantly less money than polyiso. I've worked with this company before and they have been excellent.
As far as ROI, I have debated just how much to install over and over in my head. It has been a while since I designed the house so don't remember why exactly I chose to go with R50. I know that code is lower and this will be better than standard insulating methods by virtue of being continuous with no thermal bridging. Perhaps it was my belief that code means "bare minimum" and that surpassing it by a decent margin would be money well spent. Reasoning could also have been "go the extra mile, spend the extra buck" since the house will have no conventional HVAC system. Passive solar, straw bale construction, double and staggered stud walls where there are stud walls.
At any rate, this has veered quite off from my original question. Yes, running the foam out would be easier than framing. However, I will still need to accommodate for the fascia which will require something of framing anyway. So, it won't be that much more work to hold the foam back and not insulate the overhangs. And, as I mentioned before, it will save me money...and I have the time. I'm just wondering if ice damming could be a concern.
We have about 4" of snow here now, and in looking at my current house, there is only a tiny ice dam on the south side, and only in an area that is partially shaded by trees. The roof is at a 10:12 pitch with R20 insulation. The new home will only be 2:12, but there will be no shading on its south side. It will receive 6 hours of full sun in the winter.
deanbowman,
I am CZ6B at 8,000 ft similar snow reality.
As practical experience has shown me, a un-vented and top only insulated roof overhang works just fine. My snow load design is 58# ground snow 45# (inexplicably) and my R-38 top foamed roof over my east porch does not ice dam. My west porch was framed to save the thick nail base so it is only the 4" panels so roughly R-20 total with sheathing and what not counted. My completely un-insulated shed roof over the front door does produce some amazing snow curls but those are driven by sun warming the wall intersect enough to get a bit of metal exposure that speeds up the melting.
My low 1:12 roofs are membrane not metal because no one would guarantee the low pitch. 2:12 is down to the point that how you detail can be important. My metal roofs are 3.25:12 and have posed no problems. The snow stays longer on the membrane, but will, if very sunny, still have melt water that runs under the snow and off. I do not have gutters or snow brakes having been advised against both. They just give sticking points for ice. The snow does slowly slide down the metal once a film of water develops under the snow from house warmth. This occurs when outside temps hit closer to 30F not below. I have R58 above living areas and I do not regret the relatively small additional expense incurred.
I would be a bit more concerned about the T&G boards if they extend past interior walls, which it sounds like they do. The first skin of Ultra SA sounds like a gummy kind that will help to seal the long screws holding the second sheathing layer. Do be sure to use a high temp rated. If you could possibly schedule a 1" polyiso over your base EPS, I would recommend it. EPS will soften around 165-170F. A temperature that metal roofs in full summer sun can reach. The reflections of of certain windows in my situation seem to have caused a sagging of the EPS under the 7/16 OSB skin on the nail base. Hard to determine now as the membrane is down for keeps. Maybe the density used is partly at fault.
The better than code is money well spent in my opinion and a roof/attic is the least interrupted surface in most homes. The extra R added is pretty much conserved as opposed to walls with windows. Plus it will keep you cooler in the ever increasing summer sun heat loads.
Thanks, Onslow. Appreciate that!
Akos believes that I don't need to insulate my overhangs but, if I'm interpreting your post correctly, it sounds like you might be leaning towards insulating them in my case. Is that correct?
As far as my T&G, yes, they extend past the wall, all the way to the rafter ends. And yes, the Sharkskin I have on top of the T&G is the peel and stick membrane which is supposedly self-sealing. Was it the sealing of the long screws that you were concerned with...the screws that will be going through my 1/2" plywood and 10" of foam and into my rafters? Or is there something else I have missed?
Also, I will use the same Sharkskin on top of my 1/2" plywood (between that & the metal roof). It is high temp rated for this very application.
Your comment about the sagging EPS has me a little concerned. I was hopeful the 1/2" plywood on top of my EPS would insulate it enough to prevent problems. Perhaps it won't be an issue for me as you mentioned the reflection of windows playing a role in this. Could you elaborate? And what density is your EPS? I was planning to use 2# density in my living areas (for the extra r value) and the less expensive 1# or 1.25# above my shop.
All are welcome/encouraged to chime in with ideas, questions, or concerns. Hoping to get this as right as possible. I plan to finish out this life in this house at which point I hope my daughter will take it over and call her own.
deanbowman,
No need to insulate overhangs. There may be reasons to end up with insulation over a porch or overhang, but those reasons will be driven by making the roofing framing easier to complete. In my case, the east porch got thick nailbase because making the eaves match drove the layup. The west porch presented a way to lift the roof framing higher with thin insulation to give a bit more head room without creating a mis-match on the eave line. There were likely no savings, as the panels for that area had already been ordered. The porch feels a bit less cave like now, so win anyway.
The T&G issue is one that gets mentioned here and there on GBA. The gaps between the deck boards form an air path from outside to inside once the groove extends past wall framing and siding. While the Sharkskin will seal major areas of the gap path from room ceiling to outside, the smaller path from extending past the wall/siding line remains. It is a bit late to apply sealant between each board at the wall location, so the only path I see now would be to seal the eave face of the boards with something like Sharkskin. I would wrap the material up onto the ends of the boards to cap the path there. It may seem like over-kill, but imagine sucking air into the house via a couple of hundred straws (the T&G gaps). It wouldn't be much, but it would invite moisture issues to develop as cold air meets warm moist interior. Wood will cycle dimensionally over time in a way that could increase gap sizes.
The EPS I have for nail base is likely 1.25 or 1.5 lb density. The panels are quite light for being 4'x8'x 8.5". The sagging issue was first noted outside of an east facing window. I have since felt similar spots up on the main roof area and it might be overly aggressive setting of the long screws that cause the dips there. I do know the metal roof material gets crazy hot at our altitude and with no sleepers under the panel anchors, the heat is readily conducted downward. If you want peace of mind maybe test a sample of the foam by placing the plywood firmly in contact and heating it with a high wattage brooder bulb. Though the R-value of plywood is minimal directly hitting the foam with a heat lamp is probably unfair.
The local code requires high temp ice and water shield under metal roofing, so I went with high temp Grace product over my second layer of sheathing. The primary layer of sheathing under the foam got a synthetic roofing paper that was not self adhering. The long screws holding the nail base were of course put down before the high temp I&W so the heads were encapsulated along with OSB. The screws holding on the clips for the standing seam are sealed by the gooey adhesive. The grip in 7/16th OSB is tenuous enough without adding in slow rot from water intrusion around the screw body.
None of my ceiling area under the primary sheathing is exposed to view. Your T&G boards are meant to be the ceiling finish, so it will be a good idea to think about fairly precise setting of the long screws. The crew was quite good at hitting 1 1/2" framing edges and I only noted 3-4 places where the screw tips came out the sides of a joist or truss. A little foam on the metal to keep it from making frost and all was good. Butting panels over a 4" edge may seem easy-peasy, but a failure will be quite visible in your case.
Speaking of overhangs and insulation...
I have two sheds which are very similar. One is un-insulated which we use for storage, the other is my wife's she-shed, which is heated and insulated with 2" of foam on all six sides.
So the tool shed overhang has metal roofing directly on top of the exterior plywood roof sheathing, while the she-shed has a layer of plywood as the soffit, a 2" air gap, and the same plywood roof sheathing.
This being Coastal BC, both occasionally get bit of black discoloration, but the she-shed gets a coating of quite thick white mold on the soffits I have to remove each year. Something about that 2" air space must cause it.
Thank you for sharing that experience, Malcolm! Interested stuff.
deanbowman,
I haven't been able to draw anything definite from the differences, so I'd be reluctant to say insulation would solve the problem.
Thanks, Onslow!
Try as I might, I can't wrap my brain around the T&G issue. Perhaps we're thinking of different assemblies? Attached is a quick sketch (didn't quite fit in my scanner). For clarity, I omitted the 10" EPS, fascia, sheathing, & metal roof.
(not that it matters much but the exterior side blocking above the double wall is actually flush with the plywood sheathing....not as I have drawn)
If you, and others, have time...take a peek and let me know.
The rafters and all the T&G, is exposed from underneath....inside and outside under the overhangs.
As far as my long screws hitting the rafters...the 4x8s give me a pretty big target to hit. My plan is to get everything temporarily tacked down then snap a chalk line down the center of each 4x8...then drive the long screws in. Hoping I don't get off too many times!
I think posters are referring to the t&g in your case on the gable ends, as in my house. Here every 5 1/2 inches there is a small gap which is an air path. On my house some 13 years ago 2ith 2 1/4 thick t&g I drilled a 1/4 inch hole at every joint at the center of the wall and squirted spray foam in the hole. The plan was that it would fill the entire gap rather than just the bottom or the top.
Awww....thanks, Gusfhb! I was so focused on the rafter tail side of things that I completely missed the obvious gable end dilemma.
The gable end T&G, plus rafters, will all be exposed as well (see attached pic which is a covered porch area).
At this point....I wouldn't know what to do other than apply silicone at each joint...trying to squeeze it as far into each groove as possible. It wouldn't take me long....though I don't know how effective it would be with the continuous movement of the wood which would likely break the joint. Still better than doing nothing...
Perhaps I missed something else though....something in Onslow's post. ?
Deleted
deanbowman,
gusfhb did pretty much what I would suggest if you still had access to the boards without violating the Sharkskin. I would have used a sealant over foam, but the idea is to interrupt the path from inside to outside. Alternatively, putting a squirt of sealant in the groove of each board where it crosses the wall line when first planking up the roof would have worked too. Not sure which would be more tedious.
The photo you posted puzzles me. It reads as if there is a hatch opening into an attic space. Can you clarify what is going on.
Thanks, Onslow. My T&G is only 3/4" thick... so the risk of violating the Sharkskin would be high. That's why I was thinking to fill up the groove with silicone as much as possible from underneath, against the gable wall. For redundancy, I could do the same on the inside of the same wall. It wouldn't work as well as your idea and Gusfhbs....but, at this point, I'm not sure how to handle it. I'm open to ideas.
That opening is actually an open clerestory in the porch and above where my summer outdoor shower will go. Its purpose is threefold: Let a little more light in; a vent; and esthetics. It's mostly the latter though, to add another line to the roof. I don't have a great pic of it from the side....so here's a pic of the model (clerestory on the right), and one from an angle.
What if you hit each seam diagonally from outside and below. The reason for the 1/4 is the spray foam straw will fit. Spray foam will expand and fill the gaps. Will it last forever? Dunno.
deanbowman,
gusfhb is ahead of me again. You could make a guide block to limit drilling depth and put the holes in diagonally like he says. Stuff the plastic tube in a give a little squirt and back out the tube. The foam will expand outward. I have poked at foam I put around windows years earlier and aside from being a bit crunchy, it does seem much the same as first applied.
I would recommend low expansion or you will end up with to large bubbles in the foam. The regular kind does not develop a consistent bubble size. The expansion will still be enough to seal. The little mushrooms that will grow at each hole should be dry before you attempt to knock them off. Unless of course you love sticky messes.
To make a guide that prevents holing thru the Sharkskin, a 45 degree rip off a 2x block scrap will leave you with an easy guide that will lay into the roof to wall corner. Buy a brad point wood drill and use it in place a standard twist drill. The brad point drills cleaner and clears the hole better. Put the guide hole through the wide face until it exits on the 90 degree corner. To limit the drill depth to what is desired, you can either chuck the bit deeper or add plywood scraps to the wide face until you get the drilling depth needed. Put a fender washer over the drill bit so you can use the jaw face as a stop. Without the washer you will chew into the wood and get deeper holes which might poke out through the Sharkskin.
I have attempted a diagram to show what I mean.
Even if you do ding the Sharkskin now and then, put a patch on it and remember in most cases you will be covering it with foam. There shouldn't be any water getting that far down anyway.
Excellent. Thank you for taking the time to do that, Onslow. Thanks also to Gusfhb, Malcolm, and Akos. Appreciate you all and this forum.
I just got around to filling the t&g gaps. Luckily, I didn't have to drill any holes. Being that my t&g was the "nickle gap" style, the gap was wide enough for the foam spray tube nozzle to fit. I sprayed the foam in from the exterior....and sprayed liberally....enough so that it came out on the interior.