Need Zone 2A wall help

Hello,
I need advice on the best wall assembly for air, moisture control and insulation for my house.
The location is Austin, TX which is climate zone 2A hot humid. My house is about 60 years old, concrete slab, 2×4 wood studs and brick exterior. I’m not sure exactly what is between the bricks and the studs but there is a black colored perhaps particle board visible from the inside.
I want to insulate my wall from the inside but what is best way? Closed cell spray foam, open cell spray foam, tyvek air barrier next to the particle board with rock wool batt next to the interior drywall or rigid styrofoam or ?
Thank you for your help. Your advice years ago when I needed a new roof worked out great. I now have an energy star metal roof, radiant barrier, R18 insulation above the roof deck and R30 below.
Tom
GBA Detail Library
A collection of one thousand construction details organized by climate and house part
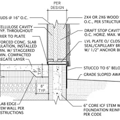
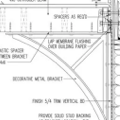
Replies
You need to figure out what is exactly behind your brick.
Generally, if you have a proper gap without excessive mortar droppings and a WRB, than the wall can be safely insulated by any of the above ways. If any of these missing, your best bet is to inclue a small air gap behind the sheathing or at least install a crinkly WRB on the inside.
You are in warm enough climate that the R value of the finished wall does not matter much, as long as you get some insulation in there it will be good enough.
Air sealing does matter though, so if you can install an air tight drywall, you can go with standard batts in the walls.
If you some of the uglies like balloon framing that is open to the basement/crawlspace and roof, than dense packing or spray foam is a better idea.
No matter what, you need to make sure your window flashing details are good, any leaks there will result in moldy insulation/walls. With lot of older houses, flashing details are non-existent and need to be added in.
Tom,
Just to echo Akos' point: old buildings did a great job of avoiding damage from water leaks and air/vapor infiltration. So much warm air is allowed through these assemblies that they are able to dry before real problems occur such as mold, rot, insect damage. When you suddenly insulate these cavities, less energy is now entering the assembly and any existing (and previously benign) leaks may now cause damage as the wetting exceeds the limited drying. This is certainly true in colder climates but can apply in warm climates as well, especially when you have a reservoir cladding (brick/grout) and if you use AC.
I suspect the black material you described is some kind of fiber-board? If you chip a piece off, does it smell like a petroleum product? This stuff is very vapor open. Not good in a warm climate with a reservoir cladding. As I think about it more, I agree with Akos about how to address the insulation / air gap behind the brick.
Once you've insulated the cavities, you should really pay attention to bulk water. Like Akos said, check your window flashings. Also, avoid interior poly, vinyl wallpaper, outdoor sprinklers near the walls. Hopefully you have adequate overhangs and functioning gutters. Insulation is great but only if you consider it as part of a broader, well executed system.
Good Luck!!
>" I’m not sure exactly what is between the bricks and the studs but there is a black colored perhaps particle board visible from the inside. "
Asphalted fiberboard sheathing (Celotex was one popular vendor) behind brick veneers is/was very common in the Gulf Coast states 50-60 years ago or more, largely because it's very moisture-tolerant. But it's also very vapor-open, which sometimes leads to moldy wallpaper (or worse) in air conditioned buildings, especially vinyl or foil wallpapers.
For air tightness it's likely that a full cavity fill open cell spray foam (R13-ish) will be the best bang/buck. To use fiber insulation requires other air sealing at the sheathing layer, and it's difficult (impossible?) to reliably air seal asphalted fiberboard with goop (maybe with asphalt roofing repair caulk it would work, but would introduce an indoor air quality problem until it outgassed, which would take years.) Closed cell foam would be too vapor-tight, potentially putting the stud edges closest to the brick veneer at risk, and is generally a waste of money when installed between framing:
https://www.finehomebuilding.com/2017/07/10/closed-cell-foam-studs-waste
Fiberboard sheathing adds about R1 "whole-wall" to the assembly as compared to a plywood sheathed wall, and it would still meet/beat IRC 2018 code minimums with R13 open cell foam in the cavities. If you want to go better than code, building out the framing depth with "Bonfiglioli strips" would work, albeit a bit labor intensive:
https://www.finehomebuilding.com/membership/pdf/9750/021250059.pdf
With 1" foam board, and 1x furring the cavity depth would be 5.25", which would run about R19.5 if filled with half-pound open cell foam, but the improvement of the R4-R6 thermal break over the framing provides a bigger performance boost than the marginally higher center-cavity R.