Flash-and-batt for new construction in Climate Zone 5

We are building a house in Ohio, zone 5. 2×4 construction. Builder is recommending flash and batt insulation with 1/2″ of closed cell spray foam, R-13 batt, and 6 mil poly between the fiberglass and sheetrock.
From what I have read on here that seems like a fairly risky way to insulate the house. While it does appear to meet Ohio code for insulation using the “Ohio Homebuilder Association Alternative”, I’m not sure that’s the best approach.
I’m considering requesting 1″ of closed cell and a “smart” membrane like Certainteed Membrain, rather than changing the entirety of the insulation plan like adding exterior foam.
My thought is that, even though the R-13 batt would be further compressed, I’d still maintain the overall R value of the cavity with the increase in foam while reducing my risk for moisture related issues by keeping the inside face of the foam above the dew point. I believe 1″ of foam is sufficient to keep the dew point high enough in Ohio, based on what I’ve read. Would this work as I’m expecting or would it cause additional issues I’m not thinking of?
I’m about a week and half from having to make a decision so any help would be greatly appreciated! First time we’ve built a house and we’re trying to get it right.
Thanks in advance.
GBA Detail Library
A collection of one thousand construction details organized by climate and house part
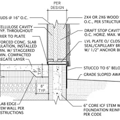
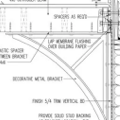
Replies
Zach, you're right that it's a risky assembly--not really due to the foam, which is thin enough that it will allow drying to the exterior in cold weather. Nobody can install a consistent 1/2", so you'll get either thin spots or thick spots. The problem is the poly sheeting--it gets hot and humid in Ohio, you probably use air conditioning, and when the A/C is running the poly is collecting condensation on the outer surface.
Using a variable permeance membrane is a better choice. Certainteed Membrain has good performance characteristics but is fragile to work with and in most places is a special order. If you're going to make a special order anyway, you could get a tougher product such as Siga Majrex (from sigatapes.com) or Pro Clima Intello (from foursevenfive.com).
R-13 fiberglass performs at R-10 when compressed to 2.5", so with an inch of foam (at R-5.5/in; don't believe the sales rep who tells you otherwise, unless it's HFO-blown foam at R-6.5/in) you'll have R-15.5 for the center-of-cavity. That's slightly better than the R-13 you would have without the foam, but it does not even meet IRC requirements for your zone, which are either R-20 in the cavity, or R-13 cavity plus R-5 continuous insulation. Maybe you aren't required to meet code, but it's a low bar so there's no reason to go lower. If you use continuous exterior insulation you don't have to use an interior membrane so you can save some money.
Thanks for the input. So another approach I was considering, depending on cost, would be the following:
2" of eps on exterior
Drainwrap
Osb
1/2" spray foam
R13 unfaced batt
I'm assuming they would flash the windows to the drainwrap.
Would this work better than the system they're proposing? My main concern is moisture management but I'd also like to get the best thermal performance I can within a reasonable budget.
The flash and batt I described originally is the system they include with all their houses so anything I change would be an out of pocket upgrade.
Zach, your approach would work, but it's often easier to use polyiso on the exterior, rather than trying to find high-density EPS. Both have about the same environmental impact, and polyiso has higher R-value per inch, though it decreases in cold weather, whereas EPS' insulating value increases. Easily available EPS is light-weight and crumbly. If you can find a source for used foam insulation, it would minimize cost and environmental impact.
I find it easier to tape the sheathing to create an airtight layer rather than using spray foam. You aren't getting significant R-value increase from 1/2" foam.
Drainwrap is not necessary between the sheathing and exterior foam, as long as the foam has enough R-value to eliminate condensation concerns in cold weather, which your assembly accomplishes, so you could just use Huber's ZIP system, or a basic WRB such as Tyvek, Typar or 15# felt. Drainwrap won't hurt anything, though. The usual place for flanged windows is against the sheathing, flashed to the WRB, though some prefer to push them out to the face of the exterior foam.
The batts can be unfaced or Kraft-faced. Sometimes Kraft-faced is less expensive, installed.
It sounds like this would be a new approach for your builder, so expect a significant upcharge. Maybe you can convince them that their standard approach is bad (they can't even reach code-minimum standards?) and that this is an opportunity to learn a new system that many builders find cost-effective once they've done it once or twice.
There are many, many articles here on GBA about the finer points of building with continuous exterior insulation, so you and the builder have a good resource at hand.
The drainwrap is absolutely necessary between the foam & OSB if the windows are mounted "innie" with the flashing directing water to the exterior of the OSB, not the exterior of the foam.
https://www.greenbuildingadvisor.com/article/where-does-the-housewrap-go
Ok great. Doing more research today and I'm not thrilled on the degradation in preformance of polyiso when it's cold. We recently had a cold snap where it was below zero for several days and in the low 20s for a period of time before and after that. I'm leaning towards 1.5" xps (R7.5)now based on Michael's comment regarding the fragility of eps. Also, Foamular seems to be readily availabile in my area.
Assuming the same setup I mentioned above but with xps, would this work and provide adequate drying potential in either direction should the OSB get wet?
I believe code requires at least a class 2 vapor retarder on the warm side of my walls, would one of the smart barriers be the best way to accomplish this with the above setup, if required?
Zach, the problem with Foamular is that the blowing agents are the most potent global warming agents of any building materials, 1400 times worse than carbon dioxide. You might not care, but it matters. As long as you understand that polyiso's performance drops with the temperature it's a fine product, relatively speaking, and the most common material to use for exterior insulation.
Also, to be clear, EPS can work great as outsulation, and an advantage is that it allows some outward drying. You just want to look for 15psi, aka Type 2, or denser material, which has working characteristics comparable to XPS. You just can't find it at your local big box store. (I get mine here: http://www.branchriver.com/pages/cfHome.cfm)
Dana has a good point about the Drainwrap location. When using exterior insulation, I either use flangeless windows flashed out over the insulation, or create an extension so the flanges can sit in plane with the outside face of the foam. But if you're installing windows conventionally, then adding foam, it would be wise to use Drainwrap (or another self-draining WRB).
The degradation of polyiso is less of an issue than it seems. It's the average temperature through the foam layer than matters, not so much the temperature on the cold side. Even the worst performing 2lb roofing polyiso is going to be no worse than R4/inch when it's 0F outside with 2" of foam on a 2x4/R15 wall. Take a look at figure 2 in this piece of marketing fluff:
http://msdssearch.dow.com/PublishedLiteratureDOWCOM/dh_09b4/0901b803809b49c0.pdf?filepath=styrofoam/pdfs/noreg/179-00263.pdf&fromPage=GetDoc
When it's 0F outside, 70F inside the average temp through the warm side of foam layer is going to be about +30F, and the average temp through the foam about +15F, so their straw-man product is still performing at about R4.2/inch.
When it's 20F outside the warm side of the foam will be about 40F with a mean temp through the foam of about 30F, where it performs at R4.5/inch.
At your average heating season temperature it will be even higher performance. And that example is crummy roofing foam labeled R5.2/inch. Almost all foil faced lower density sheathing foam is going to beat that by quite a bit. Dow Thermax polyiso sheathing has beaten the polyiso derating game with a proprietary process, and continues to rise in performance with falling temperature in much the same way other insulation products do.
But foil faced polyiso is an excellent price/performance product, easier to air seal than XPS, and a lot greener too.
XPS is only warranteed at R4.5/inch (90% of labeled value), and even that may be optimistic. The HFC blowing agents that give it a performance boost over EPS are extremely powerful greenhouse gases (more than 1000x CO2 @ 100 years), and is it dissipates performance falls to that of EPS.
EPS and polyiso are both blown with low-impact hydrocarbons.