New Mountain House cannot get warm

Kind of a long question so bare with me. Have a customer that just built a mountain house which she cannot keep above 50 degrees. Sounds like he has fiberglass insulation, bark siding on the exterior and wood t&g on the interior. (We did not build it, he is asking us to figure out what is wrong and have not seen it yet). Sounds like wind is just blowing through the house with the wood siding and wood trim on the interior – no shteerock. They had a company come out and run a blower door and said the number was through tthe roof – I think 10-12 air changes per hour. Here are my questions:
Is an air barrier needed on both sides of the wall insulation for it to work properly. I know from energy star and backing up knee walls the answer is yes. But we do floors and ceilings all the time without air barriers on both sides (e.g. crawl space and attic). I would think that mountain houses are built all the time without the “new building science” air barriers – why would this house behave so differently? I would assume there is plywood/osb behind the bark siding – should be a decent air barrier even if the seams are not caulked.
Is there any way a T&G wood trim on the interior can qualify as an air barrier?
If there is already insulation in the wall – are there any options to blow in additional insulation or foam to create an air barrier?
I will obviously check out the duct system, etc. but she has had several people go look at this already and have not been able to solve the problem so I am assuming they have checked out the basics. I feel like I am going to have to tell her to remove the interior siding and install an air barrier on the walls and then reinstall the T&G – very expensive. For the ceiling – which is also T&G in some places – we can at least pull back the fiberglass and spray a flash coat of foam or something on the attic side to air seal which should not be too costly.
Any thoughts or ideas?
Thanks for your help.
GBA Detail Library
A collection of one thousand construction details organized by climate and house part
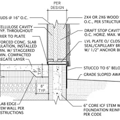
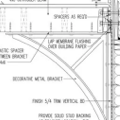
Replies
Danny,
"Is there any way a T&G wood trim on the interior can qualify as an air barrier? " No.
Obviously, the first step is to visit the house and do a little investigation. Drill some holes or pull off some trim boards and get a look at the actual wall construction details.
To do it right, it sounds like either all of the siding has to come off, or all of the interior T&G boards on the walls.
What kind of foundation? What is the heating system and output?
Seal all mechanical penetrations, seal around sill and bandjoists. Seal the ceiling thoroughly. Make sure there is a WRB on the exterior under the siding. Check insulation on all six sides of the envelope. Add more where feasible.
Did he/she build the house themselves or have it built? If the latter, there should be some guarantee of servicability.
Thanks guys - they said they had the "best builder in the mountains" or best reputation anyway build the home so I do think it was a qualified contractor although maybe not up on all the latest and greatest of building science. It is on a closed (sealed) crawl space, propane heat. They have had energy audits, HVAC companies, Blower doors, etc run and nobody can seem to figure out the problem. I think all the obvious things have been done and investigated - seems like everyone is missing something pretty obvious for the house to perform this poorly. Even without great air sealing it does not seem like it would be this bad - this seems to be the "standard wall detail" on all homes up that way. Will let you know if I learn anything new if I make it up that way - not really in our nexk of the woods. Thanks for the thoughts.
Danny,
Although your most recent post implies that the house has "standard wall details," that assumption is contradicted by your original question that stated, "They had a company come out and run a blower door and said the number was through the roof."
You really need more information, including:
1. An examination of the wall construction details.
2. An accurate report of the blower door results.
3. An assessment by a blower-door-equipped building performance contractor who is able to identify the main air leakage paths.
Martin - yeah looks like i left part of a sentence out - what I was trying to say was, they used a typical wall detail for their area which most of the builders/architects use in the mountains - so the point I was trying to make was - if they have built 100 homes this way, although not the best detail to use, it shouldn't be underperforming the way that is it. I'll know more when I get by to look - was just wondering if anyone had run into something similar before and if there is something special I should be looking at beside the obvious/typical - HVAC system, tight ducts, air sealing, insulation levels, thermal bypasses, etc.
Wall detail from plans - bark siding/plywood/osb/2x6 stud/R-19 fiberglass batts/wood paneling.
Energy audit reports comfirms R-19 crawl and a R38 Attic. They say they have a closed crawl which typically has the walls insulation in lieu of the floor but I guess there are several ways to do it.
The original blower door was 9155 CFM50 - 12.2 ACH. The builder performed some air sealing measures, etc. New results were 7550 CFM50 with 10 ACH. So the air sealing did help a little but those numbers still seem unusually high for new construction. Which is why I was thinking wood paneling needs to come of - air barrier installed and then paneling re-installed. Nobody is going to like my solution so want to be sure I am on track. Only I thing I can think of is the HVAC is way undersized.
My plan is to inspect with a thermal camera both before and during a blower door - that should answer a lot of the questions - as of now, just kind of guessing. Thanks for the thoughts.
Danny,
About 8 or 10 years ago, a study showed that the average new home in Minnesota had an air leakage rate of 2.5 AC/H @ 50 Pascals. So the house you are describing is 4 or 5 times leakier.
Needless to say, those Minnesota houses are still a far cry from the Passivhaus standard of 0.6 ach50.
That actually sounds pretty good for a house built that long ago - isn't energy star about 3 AC/H?
Yes - this house has a serious problem.
At 7550 cfm for 10 ACH, that would be a floor area of 5662 SF (with 8' ceilings) . Is the house that big? You say mountain house. Where is this and what is the HDD?
2x6 R-19 construction is woefully inadequate by today's standards in a mountain climate. And, if there is really no air barrier, that builder should be tarred and feathered.
I don't know how it's possible to build such a leaky house. If it's really as big as my calculations indicate and as leaky as that, I'm not sure you could buy a residential heating plant big enough for its load.
That is kind of what I was thinking - that is the leakest house I have ever seen, especially for new construction. The builder and architect and not going to be very big fans of mine when I give them my opinion (and cost) to repair this. That is why I was asking so many questions - to be sure I am not overlooking something. When I tell them it is a design problem and the wall was not designed properly - I'm sure I'll hear how they have been doin it that way for 30 years story and I don't know what Im talking about.
I have not had a chance to see the house or plans yet - i would guess it is between 4000 and 5000 SF though - probably a lot of vaulted ceilings - typical rustic mountain home. I am thinking it is a two story in the center with single story wings on it. I do not know the exact location - NC/Tenn mountains - sounds like it at the top of one of them - very cold, lots of snow and very windy according to the client - I think most of those mountain areas are 4500-5000 HDD but this may be off the chart considering how high up it is.
Thanks for everyone's feedback and help - will be back in touch for sure when I gather more information.
Hi Danny,
You wrote...``When I tell them it is a design problem and the wall was not designed properly``
It`s not a design problem... it`s a design failure. This really shouldn`t be considered acceptable.
Good luck,
Andrew
Finally got a little more information - Looks like they used Optima insulation (R-23 in a 5.5" cavity) by Certainteed
http://www.certainteed.com/products/insulation/fiber-glass-insulation/blowing-insulation/317369
Density is only 1.8 lbs/cubic foot - so I guess it is not an air barrier. although better than batts - does not seem to be doing the job.
Anything's better than fiberglass batts, but BIBS is most definately not an air barrier and it doesn't deal with themal bridging at the typical 25% of the wall that is framing.
I'd be very surprised if fiberglass of any kind could achieve an R-4.2/inch, but even at that rate the whole wall R-value would be no more than R-18. If air is moving through the insulation, then it will be significantly less.
Danny,
"So I guess it is not an air barrier" — you got that right.
If the builder was depending on blown-in-place fiberglass to be a component of the home's air barrier, then the builder needs to attend some educational courses.
The IECC requires, in section 402.2.1, that "the building thermal envelope shall be durably sealed to limit infiltration." Many building codes include similar language.
Needless to say, it would be better if the code were more specific. It would also be a nice idea if code officials started enforcing existing building codes requiring air sealing measures.
Danny did you go and test the house? If your conclusions are right and the significant problem are the walls you could get a competent cellulose contractor to vacuum out the walls. They maybe able to do this by removing a few courses of boards from the exterior. Then the walls could be dense packed with cellulose significantly reducing infiltration.
Everybody's talking about the wall detail, but what's the roof detail? I'm guessing it's something like 2x10's with propa-vents and poorly installed batts. Maybe with kraft facing, maybe not. With the wind howling on a mountaintop and a leaky rim joist, the air could be gushing in from below and right on out the roof.
Still have not made it up there. Good point Rich - I guess that's the upside to the Optima insulation.
Michael - I pretty much assumed the attic was a given for air sealing but since it did have Sheetrock installed it at least had a air barrier and did not think that could have been the only cause of the severe underperformance of the house - but yes will check it out for sure.
Thanks.