New video
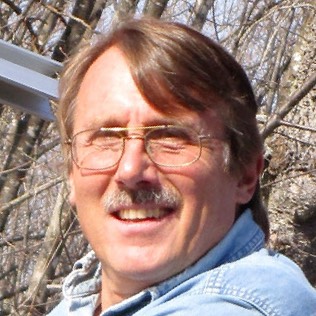
We’ve posted a new video — an interview with Al Rossetto — here:
https://www.greenbuildingadvisor.com/blogs/dept/green-building-news/do-it-yourself-home-building-enabler
In the video, Al discusses walls without thermal bridging, dry foundations, ERV ventilation systems, and radon.
GBA Detail Library
A collection of one thousand construction details organized by climate and house part
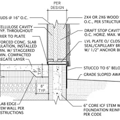
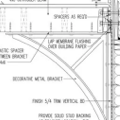
Replies
This is the comment I just added to the Al Rossetto video page:
Nobel? I don't think so.
There's no doubt that Al knows how to build a tight and efficient house, but he no more deserves a Nobel for environmental health than Obama deserved one for peace while waging five wars.
For instance, by connecting the inner and outer footing drains with the overly-expensive and unnecessary Form-a-Drain and daylighting the drains, he's effectively short-circuited the radon vent. The function of the passive radon stack (as he correctly points out) is to create negative pressure under the slab. But with the interior drain (radon vent) connected to the daylighted exterior drain, the radon stack will only draw outside air from the outlet pipe and not protect the occupants from carcinogenic soil gas.
I'm familiar with Al's Waitsfield VT Energy Star home, the one featured in Fine Homebuilding in the Feb/Mar 2004 issue. I wrote the following letter to FHB in response:
Fine Homebuilding
June 29, 2006
To the Editor,
At the conclusion of a week-long Sun-Tempered Super-Insulated Home class I taught at Yestermorrow Design/Build School in Warren, Vermont, I took my students on a tour of the Mad River Valley, including visits to two super-insulated homes in the area.
One of them was featured in FHB March 2004 in an article by the builder, Al Rossetto, who moved out of Vermont because – as he told me on the phone – there is no market for his homes here. This is in spite of his having received the highest Energy Star rating at the time.
I am writing to Efficiency Vermont to propose that they downgrade this home and be careful in the future to consider a wider array of design elements in their ratings. This is why:
While a variety of clever efficiency features were utilized in its construction, including shallow frost-protected footings, ICF foundation (insulated concrete forms), SIP walls and roof (structural insulated panels), solar-assisted radiant floor heating, and heat-recovery ventilation – some of the most basic design elements were overlooked.
These include sufficient fenestration and natural ventilation, proper solar orientation, and summer shading for south-facing windows. The result of this, according to the current owner, is an uncomfortable house in the summer and the possibility of having to install air-conditioning. In north-central Vermont, air-conditioning is rarely needed and should never be required in a super-insulated home.
There is another reason why this home is problematic in spite of the highly efficient construction system – or rather, because of it. As Rossetto points out, the house is built like a picnic cooler with windows. It is basically a tightly-sealed foam plastic box with some holes punched in it and an electrically-powered system to supply fresh air and to rid the house of excess humidity (without it, it would be a rain forest, Rossetto wrote).
This is what I call the Hermetic Home – a box that is hermetically sealed so that it cannot breath without artificial respiration. And it is because of this that his house tested at the incredibly low air-exchange rate of 0.04 air changes per hour (ach) and received its 5+ rating. And, of course, artificial respiration works only when the power is not disrupted, which happens with some regularity in rural Vermont.
However, this also means that the house cannot breathe on its own. For a house to breath means not only that it exchanges sufficient air for healthy human habitation (typically 0.25 ach), but that it can cyclically absorb and release excess humidity to prevent the “rain forest” environment which will produce mold in the house and make it uncomfortable in the summer.
Because negligible infiltration and optimum insulation were the design principles for this house, there is a minimum of natural lighting and passive ventilation and insufficient overhangs to adequately shade windows in the summer. Since Rossetto’s house incorporated “high-efficiency” R-5 windows, most of the potential solar heat gain would be reflected. Never-the-less, the house is uncomfortably warm (and likely too humid) in the summer.
Additionally, though the builder believes he was being environmentally responsible by creating a house with very low heating requirements and consequently a low contribution to greenhouse gas production, he failed to consider the considerable embodied energy in the petrochemical materials that he used. The manufacturing process, transportation requirements, and ultimate disposal of the large mass of plastic foam that constitutes both the structure and insulation of the house has already contributed considerably to environmental degradation and global warming, leaving the as-built house with an ecological liability that will have to be “paid back” by years of reduced fuel consumption.
This is the ecological pay-back period that most builders and homeowners fail to consider. This more important pay-back must also consider the associated air and water quality degradation and other deleterious impacts on the Earth’s biosphere which have been traditionally considered externalities – the price that someone (or something) else is required to pay for our economic security and comfort.
There are better ways to build. Two of my homes, for instance, were built with native rough-sawn lumber, a modified Larsen Truss envelope system filled with 12” of dry-blown cellulose insulation (recycled newspaper with borate for fire, insect, and rodent resistance). One also had a shallow frost-protected foundation with radiant floor; the other used a rubble-trench foundation with flagstone thermal mass floor. Both incorporated passive solar design, which supplies approximately 50% of their very low heat requirement. To supplement the solar gain, each house consumes 4/5 of a cord of wood per year and remains comfortably cool all summer. A healthy indoor environment is maintained by kitchen and bathroom exhaust fans, the negative pressure created by the woodstove, and passive make-up air vents in bedrooms and living spaces.
One of these homes won a Citation for Excellence in a national energy & resource efficiency design competition; the other was a Massachusetts Energy-Crafted Home and incorporated the first state-approved site-built indoor composting toilet. They were both constructed for less than the cost of a conventional house, in part due to the use of the homeowners as crew members. These homes are not only more energy efficient than the SIP home described above, but also more comfortable year round and with a healthy indoor environment whether or not the electricity is on, in addition to having very small ecological footprints.
Response to Robert
I've had the great fortune to spend time in traditional buildings in Korea -- clay walls, wood fired hypocaust systems that heat stone floors covered with mud and oiled rice paper – really wonderful places. As a professional designer I aspire to perpetuate the beauty I experienced there which poses minimal stress on plant and animal life. Robert, I identify with most of your suggestions and arguments, however in a very cold climate (Minnesota, Vermont) wouldn’t you agree that an airtight house (~.6 ACH) with an ERV/HRV balanced ventilation system is preferred because it will reduce the total energy consumption by optimizing the amount and tempering the outside air coming into the building and, consequently, offsetting a greater amount of energy used for “artificial” heating? One of your main criticisms (hygroscopic and material issues aside) seems to be directed at a system because it uses energy (i.e. “the artificial respiration system”). But if this individual energy system can be used to reduce the total energy consuming by the overall building system by offsetting consumption of another energy system (i.e. the heating system) isn’t that a good thing?
Growing up in turn-of-the-century houses in Minneapolis I resisted the arguments (and codes) that say mechanical ventilation is required for new residential construction. It seemed ridiculous to add another energy consuming system. But all my research supports it is most responsible to create very tight houses with sophisticated ventilation systems (like the German ones) to try to radically reduce the energy we use to heat (even more than keeping the thermostat way down). Do you think mechanical ventilation systems preclude the proper hygroscopic dynamics of the interior environment for persons’ health and well being?
J,
No, I don't think that "mechanical ventilation systems preclude the proper hygroscopic dynamics of the interior environment". But the movement towards increased air-tightness, in practice, almost always involves a movement towards non-hygroscopic materials and the hermetically-sealed box.
I use mechanical ventilation in all my homes. High-quality, quiet bath fans and kitchen hoods to eliminate source pollution and some means of depressurizing the conditioned space (which could be as simple as a woodstove) to provide a baseline flow of fresh air through strategically-placed make-up air inlets. The passive inlets, in addition to some minimal natural leakage (my houses are very tight but not hermetically sealed à la PH) allows for some air exchange when the power is interrupted by the inevitable outages.
I have no argument against capturing a percentage of the exhaust heat with another piece of equipment, even though that requires additional maintenance which may or may not be done by the occupants. But my argument is precisely with equating energy efficiency with green or healthy. Energy efficiency should be only one part of the equation, not the primary concern. Otherwise, it leads to absurdly extremist approaches such as PassivHaus.
As I've said elsewhere, a small log cabin with a woodstove is far more green and healthy - for both its occupants and for the environment - than a plastic McMansion with all the latest mechanical marvels, even if the latter uses fewer BTUs.
Robert,
Thanks for you reply. I appreciate very much your presence on these forums and that you continue to make the materials we build with an important consideration. I wish BuildingGreenAdvisor hired a blogger to cover ‘appropriate technologies and materials’, who was as good as Martin Holladay is covering energies issues. I think the material culture of contemporary building practices is the most underestimated issue of all the issues related to green building. The prevalence of engineered materials saddens me because of all the capital that is funneled into industrial manufacturing and the economic and social structures tied to big business.
I think we tend to focus on energy efficiency too much because of our familiarity and comfort with solving engineering problems rather than being faced with changing our culture.
That said I don’t think the most productive green building discussion is “Plastic [energy efficient] McMansion vs. Log Cabin”. Instead I think the issue worth debating is “Modeled Calculations vs. Shooting from the Hip” (and I’m not necessarily convinced that computer modeling always leads to better results). I think your characterization of PassivHaus as “extreme” is based on specific buildings that have formed your perception of what PH offers. I think the energy saving principles PassivHaus proposes and the software tool it makes available can lead to results that you would applaud.
PassivHaus standards do not inform designers on material selection. While it may seem that PassivHaus projects are primarily foam enclosures, my understanding is that this is not the case in Europe. A common PH wall assembly in Europe seems to be masonry with mineral fiber insulation on the outside. These assemblies are purported to perform well hygroscopically as vapor open construction.
I am currently working at an architecture firm in Minnesota that is designing houses to meet the PassivHaus standards for a very cold climate. I am observing that to meet the requirements in a very cold climate there is a tendency to employ polystyerene foam products as insulation to keep the wall thickness from getting out of hand. So far I have only worked on single family houses. Multi-units with more square footage may not require such thick envelopes and be less problematic.
I don’t know yet whether the energy limits set by the PassivHaus Institute in Europe are appropriate for our very cold climate but I do believe that the energy modeling software and the building products that have developed around meeting PassivHaus standards (the window frames, the sealed doors, the glazing with high SHGC and low U-values, the ventilation systems, the recognition of the effects of thermal bypasses and uncontrolled air infiltration) are a means of raising the bar. I would tend to argue that with PH we can build a better “log cabin” then before.
I am working towards designs that meet PH standards by employing less industrial engineered materials. I have looked closely at your discussions on the Larsen Truss and Modified Larsen Truss and see promise in that approach.
The “Hermetic Home” criticism I’ve come to believe is a red herring (although I started with the same opinion). The ACH numbers that we reference are the blower door results, when all the windows are closed and ventilation system is sealed off. We only rely on the absolute airtightness and ventilation system during extreme weather, the same weather when people with no mindset for conservation turn their heaters and air conditioners on full blast. The rest of the time the operable windows suffice and the newer more sophisticated ventilations systems can be dormant.