Old Barn Wall Assembly

I’m working on a 2 story 2,400 sq ft barn with traditional framing on 24” centers that was built in approximately the 40’s. Someone slapped a bunch of OSB on the exterior and it’s badly warped and rotted. I considered boxing in the interior side of the walls with plywood, removing the exterior OSB, then spraying the exterior side with closed cell foam. The plan would be to hang corrugated metal on the exterior after the spray.
The assembly seems sound to me, but it’s definitely non-traditional for these parts, so I’m looking for a sanity check. Am I crazy?
GBA Detail Library
A collection of one thousand construction details organized by climate and house part
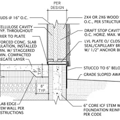
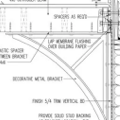
Replies
1869farmhouse,
What the goal? Is this just renovating it as a barn, to are you converting it to a dwelling?
The goal is to make it a usable workshop and storage area that is reasonably water tight. As far as conditioning, 99% would just be the take the structure from 10 degrees to 55 degrees in the winter
If the plan is to make it livable space. I have to ask what part is in good shape that you get to reuse without reworking?
My guess is the foundation is a few large rocks. The frame has some rot and most of the posts happen to be in inconvenient location. The siding was so rotten it had to get covered up. Of course, the roof leaks.
My guess is for 50% less money you could knock it down build something that is the same size and shape that is code compliant and uses half the energy.
Before you do anything make a list of your goals for the place and a budget for the full list.
There is something about the blank canvas that is an old barn that call most of us. Let the math do the thinking and not your heart.
Walta
Great points. The goal is that it will be a mostly watertight workshop and storage. The framing itself is actually it pretty decent shape, it’s just the exterior OSB that is old and rotten. As someone that works solo, I admit that my first thought was that it would be much easier to carry sheets and apply them to the structure from the inside vs the outside - especially the second story. Also, metal siding is the cheapest, and it’s much lighter, so will be far easier to apply to exterior.
But possibly most importantly, the structure exists in a city where such a barn is no longer allowed. City code designated that it can be repaired, but not replaced.
I think I would replace the osb since it is rotten anyway.
Is the building is square?
IF it is still square, perhaps sheet foam then plywood and siding, properly flashed and sealed.
Attention to detail now will pay off if plans change in the future, IE it wants to be a dwelling
1940 isn't old!
Let me reframe your question. Imagine you have a frame building, 2x4 24 on center. It has a roof but the walls are just studs. How would you finish it?
I don't think spray foam would make my short list.
I like the idea of plywood on the interior walls, it makes it very easy to hang things. It also solves the problem of supporting the walls when you take the exterior OSB off. I would hang it with drywall screws so you can take pieces off to get into the walls.
Steel siding is a fine choice. Usually it wants to be on either a sheathing or horizontal supports, which means at a minimum 1x3s on 24" centers. You really don't want mice living in the wall, which means detailing the siding edges to keep them out. But at the same time you want moisture in the wall to be able to dry to the exterior. Check with your siding manufacturer as to what trims they have. If you go with sheathing instead of strapping you can probably get away with just insect screening.
For the use you've described I think batt insulation would be adequate.
Curious why spray foam wouldn’t be in your short list? I’m a fan of the product typically. You get a solid air seal and a moisture barrier all in one with your insulation. My other “go-to” is rock wool, but cutting a million batts to fit irregularly spaced stud bays is exhausting!
It's expensive and bad for the environment.
Because it sets so hard it's hard to work with. You can't fill between studs very full because any excess is hard to cut away so in practice you don't get very high r values.
If you want to run electric or plumbings in the walls after spraying it's a pain to cut it out.
It's easy to damage wires because the foam hides them and anything that will cut the foam will cut the insulation.
I like the metal siding exterior and the plywood interior.
The way I see it the spray foam marketing had bought their way onto all the DIY TV shows and wrongfully convinced the world that spray foam is a superior product. It does have two advantages one is that you can pack the highest R value in the smallest space and two that it is also an affective air barrier. The down side are one it is 100% the most expensive way possible to buy each and every R of insulation so much so that most people refuse to spend enough money to get the code minimum R value. Simply put spray foam costs so much that it will never save enough energy to recover it costs at the code required values. Two the amounts of energy required to make the nasty chemicals to make the foam insulation is huge making a very ungreen product when compared with cellulose insulation that is almost a 100% post-consumer recycled product. Three spray foam is the riskiest insulation still on the market in that it is a complex chemical reaction mixed in the field in uncontrolled conditions by people with little to no knowledge of the chemistry or how the different variables will affect the results. When thing do go wrong there is no simple fix removing bad product is almost impossible.
If this will be a hobby shop consider not conditioning most of the space when you have big projects you work in them only when the outdoor temps are mild and you have a smaller all weather space.
All my large machines live on custom pallet that move easily with a pallet jack in a matter of seconds. Maybe a move them into a compact conditioned storage area.
Walta