one-hour fire resistance for a floor-ceiling assembly

Having done residential construction almost exclusively, the IBC is a relatively weak area of my code expertise. I’m in the process of submitting drawings for a simple tri-plex–22 x 30, three stories, one unit per story–and am trying to choose a floor-ceiling assembly with a one-hour fire rating. There is no shortage of options, almost all of them including multiple layers of sheetrock and sound channel. I just can’t shake the notion that it would be cheaper and more effective against both fire and sound to have–moving upward from the top of the walls on one of the lower two stories–ceiling joists, then a layer of continuous mineral wool insulation, then the floor joists for the floor above. However, I haven’t found anything like that mentioned anywhere. Two questions:
1) Is that approach not allowed for some reason? I guess that if an assembly is rated for resistance from below and the assembly I described is considered to start at the bottom of the floor joist rather than at the ceiling joist, that would be explain it being prohibited, which would be frustrating, but hardly my most frustrating experience with code compliance.
2) What accepted assemblies have readers found to be relatively economical and easy to do correctly, not necessarily on paper but on a real job site with real workers?
GBA Detail Library
A collection of one thousand construction details organized by climate and house part
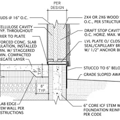
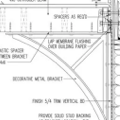
Replies
As you have alluded to, you need ratings for both fire and sound.
A good, constructable assembly is (top to bottom)
- 1.5" concrete topping
-3/4" plywood
-Lumber or Ijoists spaced 24" O/C
-Rockwool insulation
-Resilient channel spaced 16" O/C
1 later 5/8 type X gypsum board
This assembly gives a 1hr fire rating and a high sound resistance. The concrete topping will add deadload that the floor system will need to be designed for.
A similar assembly, without the concrete topping, will require 2 layers of 5/8" type X gypsum board., but may or may not get you your sound rating, depending on your code.
You will want to find the U/L listing for this type of assembly and follow the directions, they are very specific.
I work in residential multi-family and we almost always have to use Type C board, but that might be related to the size of the buildings. In reality, Type X would provide a sufficient fire barrier.
The typical rules for RC-1 in multifamily would be 24" O.C. if there is no insulation in the truss space. 16" O.C. if the insulation is pinned to the decking above or 12" O.C. if the insulation is laying on the drywall/channel.
You can find specific UL assemblies on the manufacturer's website. There are a few ones that allow you to use pretty much any brand of drywall and some that are manufacturer specific. I would go with the generic ones if you can or one for National or Georgia-Pacific, just in case the inspector is a stickler for brands.
There are a lot of assemblies out there, I would pick on that can be built with simplest materials and without specialized knowhow:
https://www.certainteed.ca/resources/cdn-gypsum-systems-manual-e-ca-2202ctg.pdf
The one plumb_bob suggests is a good one. My one suggestions is that adding an more layers of drywall is much cheaper than the 1.5" of concrete topping plus you can use regular nail down flooring.
Most STC rated assemblies will preform reasonably well provided flanking paths are taken care of. This is the hardest part in any sound separation and the one that requires a lot of up front design effort to get right.
Seems like this is a business venture and paying for an expert’s opinion would be money well spent.
Like with most things the first few times you do something you are unlikely to be perfect and the mistakes are likely to be expensive and the real experts are unlikely to work for free.
Walta
Agree with Walter - this is what the professionals are for! There are UL assemblies I think for what you are describing, but how these interface with other assemblies and penetrations is where it can get trickier.
I think what you are describing matches up to the UL design BXUV.L539 (need free account to view https://iq.ulprospector.com/en/profile?e=14293)
https://database.ul.com/graphics/lisu/ulu751.jpg (image only)
Have you looked into Magnesium Oxide (MgO) at all? We use it to make our non-combustible structural insulated sheathing panels. Adding it into an assembly gives the assembly as a whole a 1-2 hour fire rating.
We did a burn test if you're interesting in seeing the performance for yourself: https://youtu.be/n094d7wG_Do
Peter
Compelling--thank you. I'll confess to not being as interested in the performance as in the rating--do you know where I can find literature legitimate enough for a punctilious plan reviewer? And would you be so kind as to tell me who you have for a supplier?
Shoot me an email at [email protected], I can send you our testing details for the board we use. Our supplier, like all other MgO suppliers, is in China. We've done a great deal of due diligence to get high-quality, tested, and consistent quality board.
We'd be happy to sell you just MgO Board.
Peter,
Unfortunately, adding individual fire-resistant materials to floor or ceiling assemblies doesn't make them rated assemblies as required by building codes. They need to be tested as a whole and certified.
To add to what Malcolm said, code says the assemblies must be "listed for the purpose", so you need a listed *assembly* that was tested for the application. I have ocassionally seen some confusion because with a typical commerical wall, each additional layer of 5/8" drywall gains you an hour of fire resistance (one layer of 5/8" type X drywall on both sides is a 1 hour wall, two layers of 5/8" type X drywall is a 2 hour wall, 3 layers on both sides is a 3 hour wall). The reason these all meet code isn't because a sheet of 5/8" drywall "counts" as 30 minutes of fire resistance, so when used on both sides gets an hour, the reason the assemblies all meet code is because ALL OF THEM have been tested and are listed as to the fire ratings they have. As far as I know, for example, you can't put 4 layers of drywall on both sides and call that a 4 hour wall -- a testing lab would need to test the assembly and "list" it before it could be used, per code.
Note that I have nothing against MgO board, and am actually rather curious to try it sometime, but it would have to meet fire codes the same as any other wall assembly, as a listed assembly, and not just "added" to an existing assembly.
Bill
Bill,
You can understand the reasoning behind that when looking at ceiling/floor assemblies, which as sisubuilder said are rated from bottom to top. Adding something like MgO board in the wrong part of the assembly would be ineffective.