Peel-and-stick similar to drainable housewrap

I’m in the process of designing and thinking through a house in zone 4A, about an hour north of Nashville TN. I’m planning on installing recycled exterior rigid foam insulation with innie windows. I like the idea of having a drainable house wrap installed between the sheathing and the rigid foam, but I don’t like the idea of thousands of holes from staples.
I have been looking for a peel and stick membrane that would be textured or rippled like the drainable house wraps that are available, but no success so far. I like that this removes all the staples, works as an air barrier, and can be properly shingled going up the side of the house.
I was going to go with Zip sheathing behind the foam, but when I read on here about the drainable house wrap it made me question the idea of having the foam pressed up against the WRB.
Does anyone know of a product that might do what I’m looking for? Or is Zip behind the foam going to allow the water to drain like I hope?
GBA Detail Library
A collection of one thousand construction details organized by climate and house part
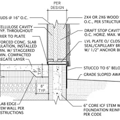
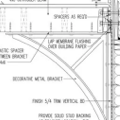
Replies
Justin,
All the house-wraps I know of require them to be install with cap-nails not staples, so you don't need to worry about lots of holes. I'm not trying to disuade you from using a peel & stick WRB, just giving you more choices.
Check which type of reclaimed foam you can get. Lot of the stuff is fiber faced, which means you need to put your WRB over the foam.
When it comes to sheet WRB, you can skip a lot of the staple holes if you install the foam shortly after. You can staple around the edges and than tape over them. Once it is sandwiched by the rain screen strapping, it won't be going anywhere.
Small holes through the WRB do little to effect is efficiency. There should not be enough water ever moving over it for small holes like that to matter.
Cap-nails and just going around the edges makes a lot of sense. I also hadn't thought about only being able to get fiber faced foam. I will have to call a few of the places and see what the inventory looks like. Thanks for a heads up on that.
Hey Justin.
There will be some fully-adhered drainable housewraps hitting the market soon, maybe this year, but I am not aware of any that are available yet. I do think they are a good idea to use behind exterior rigid foam, though many builders use ZIP or other WRBs as they feel the rigid foam will do most of the work of keeping water out.
It's a judgement call.
One other thing to consider is your air barrier. In this assembly (mechanically fastened housewrap and exterior rigid foam, it's probably best to detail the sheathing with sealants and tape as the primary air barrier.
Brian,
I will keep on the look out for the new fully-adhered drainable house wraps. They sound like exactly what I want. I plan on sealing and taping the sheathing as my air barrier for any scenario I choose. Thanks for the info.
If you are taping the sheathing, then a fully adhered house wrap doesn't buy you much. I've only ever done fully adhered membrane on walls when going over old lumber or T&G sheathing. There you need it to air seal.
About the only spot I could see you would want that is if you are doing something silly like a house without over hangs and gutters where the house wrap is used to channel rain water down to the ground. In that case the WRB should be above the foam anyways and the textured surface is not needed.
I just realized that my first comment here is confusing. While I think fully-adhered WRBs are a good option for many reasons, when I said, "I do think they are a good idea ... behind exterior rigid foam," I was referring to drainable WRBs, not necessarily fully-adhered WRBSs. And I agree with Akos, one or the other, taped sheathing and mechanically fastened WRB or fully-adhered WRB, but not both.
Akos, I agree I'm not planning on taping the sheathing if I use a fully-adhered WRB somewhere in the assembly. And Brian I only feel comfortable with the WRB between the rigid foam and sheathing if it is drainable. Sorry if my thoughts didn't come across in words.
My plans are very open at this point I'm just trying to think through all my options. I plan on doing the WRB, air sealing, and insulation myself so I can save some money on labor and use the best practice available. I know I want some form of exterior insulation, but my first priorities are making it water and air tight.
That being said I have a few more questions. With R23 in the walls is R5 exterior insulation safe in my zone 4? The article that I read said in zone 4 anything goes on the exterior insulation R value. Also can I attach a fully adhered WRB to the outside of the rigid foam? And to throw in a curve ball in does roxul comfortboard require a drainable WRB between it and the sheathing? The installation manual from roxul just states that it needs to be vapor permeable.
Thanks again for all of your help and advice. It is great that there are so many products and options available, but this also makes it difficult to narrow in on exactly what I want. It is even better that there are websites like this where I can get advice from people that have done this before.
Sorry I'm late to the convo.. so I have been contemplating the same dilema and came up with a solution that I would be curious to see if anyone else has some feedback on.
For the WRB I'm planning to go with a fluid applied membrane such as prosoco cat5. On top of this membrane and between the membrane and the foam I would then apply a 1/8" drainage mesh to facilitate water drainage. There is a product called Dryvit Drainage Matt that does this. https://www.dryvit.com/products/primerssealersaccessories/drainage-mat/
The cat5 is elastomeric and should cut down on air leakage from any siding or strapping holes. I read somewhere that a 1/8 mesh should only reduce thermal performance by a couple percent, but I haven't confirmed that yet. I would love to find a 1/16 mesh but haven't seen anything of that size on the market.
The house I am building is going to be passivhaus certified, so I'm a little nervous if any issues will arise from the foam not being in direct contact with sheathing and how it relates to thermal performance.
Thanks!
This drinage mat between foam and WRB feels like a solution in search of a problem.
I think the simplest solution if you must have drainage is to use one of the grooved foam products. These are typically intended for EIFS and foundation insulation. Even our local box store carries this but cheaper from commercial sources.
Hello from Chattanooga. If you're going with Comfortboard, it has a textured side that would allow drainage if installed against the Zip, removing the need for a dedicated drainable WRB. If going with foam, you still might not really need a drainable WRB. I was told that the surface of the Zip is sufficiently textured to allow for drainage, which I did not believe until I did a mockup and tested it myself. Risinger recently published a YouTube video showing this as well. I don't think this falls under any sort of liability-proof warranty type claim, but in the real world, it seems to work. YMMV.
On the topic of exterior to cavity insulation ratio, GBA did a good article on this a few years back that you should be able to find pretty readily with the search. The IRC says minimum R3.75 exterior insulation over a 2x6 wall for CZ4A. But BSC would say that there's an optimum minimum ratio. However, I want to say the data they base that on was gathered through cold climate sheathing risk study. I don't think it gets quite cold enough in our climate to get risky if you go off-ratio, and those who study climate would contend that things will only get warmer as time goes on.
Good luck with the project and thanks for bringing more high performance building to TN.
Chris and Justin,
Everyone else has made most of the important observations so far, but I will add that the biggest issue you (Justin) face will be the innie windows and flashing them out to the siding plane. While you should have detailing that does not allow bulk water to get anywhere near your sheathing plane, (no zero overhangs as Akos notes) you still need to plan for driving rains. Top, sides and sill trim around the windows will need to be detailed carefully and with an eye for sloped top and sill elements. If it helps, think of water intrusion like a chocolate fountain and watch for pooling spots.
Assuming some form of furring over the foam to create a rain screen, it is important to keep an eye on the top elements over windows and doors. It is very easy for a dead level setting to get distorted into a backward slant that will cause water to pool toward the sheathing. All caulk is best considered a temporary not permanent solution. Your cladding selections will drive the detailing choices around windows and doors. Looking at synthetic materials to minimize future maintenance is worth considering.
Justin, your CZ in Nashville makes me wonder if analyzing your interior temperature and humidity control is more important than the exterior. Once you have foam on the outside, your moisture control of materials will largely be relevant to the siding. Comfort Board may be moisture open, but in Nashville humidity moisture open could work against you. Even with R23 between studs your whole wall behavior might manage to get the sheathing plane closer to dewpoint than you think. I have not had to deal with humidity on any of my new work, so I will let better minds advise you on the risks. It may be that the Intello type materials will be important for your wall design and climate situation.
Chris, you didn't mention your CZ, but I am guessing heating dominant if going for PHIUS. I personally think the 1/8 air gap should have no discernible effect. Even if the gap is air open on two sides of the wall plane, air transport through such a small gap is going to be difficult at best. If most GBA experts agree that 1" of under roof air channel will not ventilate adequately, then I suspect an 1/8" would be effectively zero in your situation. Remember, most wall insulation modeling allows for the air film at the exterior surface to add R value. An 1/8" gap that is not subject to wind wash should behave as a static air gap much like double pane windows. You should also be designing with the intent that bulk water never finds your gap.
As for what to gap with, Benjamin Obdyke has many choices you might consider. I went with Henry Blueskin VP100 under my 6" foam outsulation. It is gummy enough to seal fasteners. I used it for air tightness rather than vapor open properties. My lay up is for vapor open to interior, which works well in the arid area I live in. My air gap is 3/16" due to the foam fastening method. I do not have free air exchange except at the bottom perfed J channel. It is static air. Application is not that big a deal if you have ever done wallpaper or graphic arts films.
I skipped all the taping and goop choices. The cost for Proseco were just too high for me, plus I don't believe I could have gotten anyone to put it on in my area. The window box-outs might have been a bit easier to seal with liquid seals, but the Henry tapes proved amenable and stuck well. By the way, using a lot of long steel screws to hold the foam will affect the thermal properties far more than your air gap.
Thanks for all of the great replies and information. I have settled in on a wall that I feel comfortable with. Hopefully I'm not making any great errors with vapor open and permeability . It's definitely not the cheapest solution, but I get to make up for the higher cost in materials with my own labor to install them.
It will be Hardie siding, 1x4 rain screen, R6 Comfortboard, Grace Env-s WRB, 7/16 OSB, 2x6 framing with R23 Rockwool. 1/2 Drywall.
I really like have the ability to shingle the WRB all the way up the wall with the fully adhered membrane. I also like that it will seal subsequent nail/screw holes to keep the air barrier tight. I also like that it eliminates the possibility that my OSB itself won't be air tight. Since it seems from reading, that air tightness is the most important factor for efficiency.
I feel that using the comfortboard eliminates any worry about trapped moister between the insulation and the WRB. Nathan I did watch that video that Risinger posted a few days ago. It was pretty amazing how quickly that water moved through, so I think that worry was quickly washed away. I'm still not a fan of the horizontal laps on the zip system. I like being able to shingle lap everything dealing with water.
Roger, this guide from BSC has some good details for working with exterior mineral board insulation.
https://www.buildingscience.com/file/5764
I'm using it as a reference for detailing my innie windows. I'm still trying to decide which trim material I would like to use.
Are there some worries for my climate with this system being vapor open and indoor humidity levels? Roger mentioned this and now of course I'm worried, its what I do. LOL
Justin and Roger, Nashville just doesn't get anywhere near the kind of prolonged severe cold that leads to risky sheathing moisture in winter. Even if it did, Ben Bogie is doing a lot of vapor open construction in Maine and showing through embedded moisture sensors that, at least the way he builds, things are fine.
Most of the humidity in Nashville is on the exterior in spring, summer, and fall. I know how good your air barriers are from Instagram - that will keep most of the humidity out of the wall. Vapor drive by diffusion won't amount to a hill of beans and indoor summertime humidity will be easily handled by your mechanical system, assuming it is properly designed. I agree that bulk water is where your focus needs to be, as this presents the most opportunity for failure.
Nathan,
I agree. According to table 8 in the giant BSC tome that Justin directed me to, his wall should be fine.
I was mostly concerned about the potential for air conditioning of the interior cooling things down far enough to meet a dew point somewhere in the wall. I was reacting to other's posts about moisture issues they discovered when remodeling in similar locations. The explanations offered by others indicated that water vapor passing into the wall found its dewpoint. A/C chilling the walls was the culprit.
Most likely the homes in question had poor air and vapor control. One situation was bad enough that the back side of the drywall was quite moldy. Maybe that person liked to cool things excessively. I realize interior humidity shouldn't be the source, I was referring to the possibility that high summer humidity outside the house might condense behind the exterior insulation. Even in Illinois, patio furniture will frequently have very heavy dew on them from relatively small shifts of temperature.
Not cladding the house in fake stone or brick will certainly help reduce the vapor drive. Meantime, back to the BSC tome, I need to work on my next build's window details as well. Sorry to make you worry, Justin. I spend most of my time worrying about the details, too.