Two Insulation Types in One Wall System

PGH double stud densepack+fiberglass (service chase) wall???
Has anyone proposed this idea before? I find nothing when I search. picture is worth a thousand words so see attached.
I really like the idea of a service chase that is easier to get into than densepack cellulose filled wall. If you have ever had the joy of opening up a customers wall filled with cellulose (dense or loose I have done both) then you will understand my concerns. Things and needs happen walls get opened for wiring/plumbing changes.
Project is in lower section of CZ6 NH. My concern with this approach is the hydro holding ability of cellulose to hold and release in this situation being reduced to a point that it would cause too much condensation on the interior of CDX plywood.
I am unclear if the Building Science co. “perfect wall” with CDX in place of Intello Plus would make a difference or not.
Links to any past discussion on this is much appreciated.
GBA Detail Library
A collection of one thousand construction details organized by climate and house part
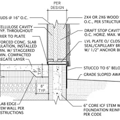
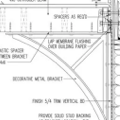
Replies
dirkgently,
That's a logical and well performing wall. You still have enough cellulose to moisture buffer, the wall can dry both ways, and the vapour-retarder is in the right place.
I like the idea, cellulose is a pain to work with. The question I would have would be about constructability. Presumably you'd blow the cellulose before putting up the fiberglass and drywall? I'm trying to think how you'd get the Intello onto the back of the 2x4 wall. Put it on with the wall flat on the floor and then stand up the wall?
Perhaps use the intello as the insulation netting? Cut the fill holes in it to dense pack the cellulose, then tape them up and proceed with fiberglass batt installation. 7.5” is a lot to dense pack through those access holes though.
Yes, Intello is rated for blown insulation support. The question is how to get it into the middle of a double wall.
My thinking is a 7.5" space dense packed may be easier to accomplish than a 11" space. I have densepacked 2x4 and 2x6 cavitys before from 1 hole in center of wall. I had good results. despite my past success, I would prefer to sub this one out.
DC,
Stephen Sheehy did a similar setup on his build in Maine. As I recall they attached the membrane to the inner-wall sections before standing them, and then sealed where they came together. https://www.greenbuildingadvisor.com/article/framed-walls-and-air-barrier-membranes-for-a-pretty-good-house
exactly, install intello on backside of 2x4 interior wall while laying on the floor. stand it up after putting a bead of caulk on floor. secure it to the plywood top plate (see PGH double stud wall detail for this clarification). seal it to that top plate with caulk.
Thank you for the link to past article. I am not clear if his primary air barrier is the Intello on the back of 2x4 wall.
I intend my sheathing to be my primary air barrier.
I would try my best to detail the Intello to be an air barrier as well. The weakest link to that seems to be managing to tape the intello to the floor after the wall is stood up. In the article above he did that by leaving sheathing off on outside (which I would not want to do for a variety of reasons).
From a building science point of view, it's a good assembly. Whenever I get the urge to reinvent the wall wheel, I end up with something similar, and similar ideas have been proposed here at GBA many times. The problem is installation.
I have discussed this type of detail with various insulators and industry experts, and all agree that it's difficult-to-impossible to get proper density behind an impermeable membrane, because the air needs to evacuate the space. There are dual-wall hose extensions that help but nobody seems to like using them. You can insulate behind the membrane with batts, or you can take a chance and hope that they get a dense-pack density correct, but I wouldn't risk it.
Michael, in all of the videos I found about Intello (including those from 475), it is inevitably used to retain the dense pack cellulose. It appears that the problem you and others have noted has been downplayed. Do you know if this is being done regularly? Clearly, the safer approach is to use the air permeable netting for the cellulose install and add the Intello after.
That's exactly my PGH wall, built in 2015. We used a Siga membrane attached to the outside of the inner wall. The membrane was stapled to the studs while on the floor, with a flap on the sides, top and bottom. We taped over the staples.
We cut holes in the membrane to allow for dense packing the cellulose. After wiring and plumbing, the inner wall was filled with fiberglass batts.
As far as I can tell, it works fine.
Edit: I just noticed Malcolm's comment above.
Stephen,
Your build is one of my touchstones for it's combination of simplicity and performance.
Thanks, Malcolm. We've been very pleased with the performance of the house. We're in the middle of several days of un-June-like weather. High temperatures around 50°F, overcast, not a bit of sun, heavy rain and lots of wind. Interior temperature has stayed right at 70°.
I also built that exact wall, but with mineral wool in place of fiberglass.
Like Stephen, I attached the intello with the wall on the floor (made sure it was square), and left flaps of intello on all four sides to tie in from the front afterwards. Other than a bit of origami in the corners, I didn't find this process that difficult.
I did, however, have some issue with the result of the dense packing. I've brought this up in other posts here before, but essentially what happened is my intello was installed before insulating for way too long (like an entire season... long story) and I beleive it become a bit stretchy. (It was drum tight at install but moved with temp fluctuations). Perhaps it is always a bit stretchier than insulweb. Either way, I ended up with bulging in the middle of the 24" bays that forced me to do some slicing of the mineral wool to keep the drywallers happy. That process was NOT fun or efficient.
For what it's worth, the installers didn't seem to struggle to get the density. They cut small slits in the corners of the bays for exit airflow which encourages the cellulose into the corners. The inside of the walls were also open to the attic (but netted off with landscape fabric as a stand in for insulweb) which also helped with exit airflow. This detail was partly due to the retrofit nature of the project.
The dense packers did say the intello was not as stiff as insulweb, but whether that is inherent to Intello or due to the temperature cycling I mentioned above, I don't know. I suspect a bit of both. They did say though that it was not common to blow behind intello like I had set up, but rather people usually placed the intello after.
It's totally possible I just goofed up with how long I had the intello up, so I don't know if anyone sould use my story as evidence of anything. I personally won't risk that set up again though unless I hear other success stories.
Deleted
Thanks so much for replies. Sounds like 2 of you did this in Northern new england....this project is in Campton, NH.
What was your Primary air barrier? I plan on using exterior sheathing for air barrier.
So if my primary air barrier is at the sheathing out side......Can insulweb were used in place of the intello in my picture to make it easier to dense pack?
My ORIGINAL plan was densepack the entire 11" cavity with cellulose....then install smart vapor barrier. Pretty much the same idea as above is it not? The only difference is that there is some fiberglass or roxul insulting the inside 2x4 wall....and cellulose in the rest.
Hope that make sense.
As a side note: I was all in on dense pack whole wall....then I got a call to consult on WRB leak on a double stud wall with spray foam (not my work work). I will not go into details on that failure here here but it got me thinking a LOT about the serviceability of 11" of dense pack. sometimes leaks happen. and cellulose is a mess inside.
Our primary air barrier is the membrane attached to the outer surface of the interior stud wall. It was easy to make it continuous with the ceiling (same membrane) and the other walls. But we taped the sheathing joints too. And used a rubber gasket between the foundation and the mud sill. Air sealing is so cheap and so important that I didn't consider obsessing about it to be a bad idea.
Insulweb should be ok.
In my non-professional opinion, we got a significant benefit from using the interior stud space as a chase for wires and plumbing. Dense packing it would have required a return trip by the cellulose installer, whereas using batts was done by the builder.
Stephen, did you use 24 inch centers?
Yes, 24" . We used 5/8" drywall.
Stephen, did you manage to magically get some gusset plates tying the 2 walls together? Other than the window gussets?
All my details sound very similar to Stephens:
--Intello was primary air barrier
--I used Solotex Mento as a wrb and taped that with tescon vana as a secondary (this was partial retrofit so taping the sheathing didn't make sense).
-- I also used epdm gaskets beneath the sill plate, but also taped the Intello to the floor (actually to a slab vapor barrier in my case)
--the wall Intello tied seamlessly in with ceiling intello. Ceiling got strapped with 2x2s providing enough space for slim led canlesss overheads.
This setup appealed to me because the primary air barrier was protected and provided a service cavity that could be filled with batts.
Insulweb could certainly be used in place of intello on the outside of the inner wall. Then you could still put intello or similar on the very inside beneath the drywall. In some ways it feels less worth it (extra work for the sole benefit of being able to use batts), but it could perhaps help with sequencing or getting a better dense pack (maybe talk to installers and see what they would prefer). I also get what you're saying about retrofit work on cellulose filled walls.
The disadvantage to intello or even insulweb on the outside face of the inside wall is that it's difficult to partition the bays or add gussets if desired. I had enough windows that I didn't feel gussets were necessary. And it's possible the cellulpse installers would have preferred partitioned bays, but they didn't really flinch at blowing into the open wall. They said it would "fetch up" and it appears it did just fine.
Hoping that mainetyler can comment on this. I did a mock up of my current idea. It was made out of scraps so not exact materials I intend to use. here is how it goes.
2x6 wall as primary air barrier and taped seams
2" Polyiso cut to width of 1.5" and nailed/glued? to 2x6 wall
2x4 wall with insul-web, membrain or intello stapled to the outside as MT did above.
Dense pack the 7.5" space with cellulouse....each bay is now seperated with the polyiso strips.....this is to make it easier for the installers.
run all wires and plumbing in 2x4 wall....eventually insulate with fiberglass or roxul
install sheetrock
Attached is a few pics of my mock up. They are Worth a thousand words and based on kolbert/bogie video with plywood/zip/osb strip connecting 2 walls at top, and my ceiling zip air barrier.
note lag bolt to connect 2x6 wall and 2x4 wall together.
I think this may be extremely easy for insulators. keep the 2x4 wall accessible for plumbing/wiring changes, and not break the piggy bank wide open on budget.
please comment
dirkgently,
This is more of a general question brought on my y0ur assembly I'd be interested on hearing some discussion around:
We routinely use 2"x4" and 2"x6" walls and expect them to bear loads and stay when we place them. Why when we build double wall do people often tie them together with gussets or hardware?
Great point. Excellent feedback for me. I have been wondering the same thing.
Especially, Since I am using a 2x6 exterior wall (architect and engineers specs)
dirkgently,
I am not necessarily qualified to comment on what wall iteration is best. My experience with dense pack installers and double stud walls has been limited to just that one build and one cellulose installer, whereas others here have worked with numerous installers. Ultimately what matters most though is what you have determined from your local installers. If they all want partitions, then I think your proposed assembly with the foam probably works. You would want to make sure the foam is well secured, as dense packing creates a good bit of pressure. Run it by the installers to get their thoughts.
In the larger scheme of wall assemblies, I'm not sure its the most efficient option from a buildability standpoint.
I don't believe you can dense pack behind membrain, btw, you need a reinforced product.
If I did build the wall I built again, I would probably just use fiberglass on the inside instead of mineral wool for cost savings and it can be compressed against the bellying a bit better.
Another option: If you're going to have the foam strips either way, you could dense pack the 2x6 wall with insulweb, then tack the foam strips to the face of the 2x6's, then stand a 2x4 wall against this and finish off with 5.5" batts, your membrane of choice, and drywall. The possible benefit to this is that the dense pack operation is as simple as it gets, if you are worried about that. It's still a lot of labor with the foam strips and whatnot.
But if you are set on a wall similar to this, and are set on using batts on the inner wall and needing bay divisions in the outer wall, I can't think of a better way to divide the bays then what you've proposed.
If you're not 100% set on that wall assembly, here are a few you could consider:
FYI I've used #8 with different materials
1. 2x4 w/ Cardboard sheathing and batt fiberglass R-13 insulation
Price Per SqFt: $1.62
Effective R-value of opaque assembly = 10.526
Pros: Inexpensive
Cons: Hard to install correctly because it is not very durable. Easy for other trades to damage. Thermal breaks because insulation isn’t continuous. Fiberglass batts are hard to install effectively.
2. 2x4 w/ osb, standard house wrap, and batt fiberglass R-13 insulation
Price Per SqFt: $2.18 (+35% from last assembly)
Effective R-value of opaque assembly = 11.11
Pros: Inexpensive. Most builders are experienced with this technique. Can tape the seams for improved air sealing.
Cons: Air barrier and WRB are seperate. Thermal breaks because insulation isn’t continuous. Easier to damage than WRB that is already bonded to the sheathing. Fiberglass batts are hard to install effectively.
3. 2x4 w/ zip and batt Rockwool R-15 insulation
Price Per SqFt: $2.63 (+21% from last assembly)
Effective R-value of opaque assembly = 11.905
Pros: WRB and air barrier is one unit and easy to install. Most builders should have no problem as it is the same as OSB/Plywood sheathing. Rockwool is fire resistant, hydrophobic, and easier to install effectively.
Cons: More expensive than OSB and house wrap.
4. 2x4 w/ zip R-3 and batt Rockwool R-15 insulation
Price Per SqFt: $2.95 (+12% from last assembly)
Effective R-value of opaque assembly = 14.7
Pros: Continuous exterior insulation = less chance of condensation on back side of sheathing. Standard 2x4 construction all builders are familiar with.
Cons: More expensive than standard OSB and house wrap. Nailing sheathing with insulation is new to some builders.
5. 2x6 w/ plywood, Aluma Flash peel-and-stick, and batt rockwool R-23 insulation
Price Per SqFt: $4.17 (+41% from last assembly)
Effective R-value of opaque assembly = 16.949
Pros: 2x6 should be easy for all builders to work with. Increased cavity depth = more insulation. Peel-and-stick WRB are easy to install, fairly durable, and not reliant on mechanical fasteners.
Cons: More expensive. No continuous exterior insulation = Thermal breaks in assembly.
6. 2x6 w/ zip R-3 (or R-6, R-9, R-12) and batt Rockwool R-23 insulation
* Effective R-value of opaque assembly = 22
* $3.62 per sqft
7. 2x6 w/ plywood, Delta Vent SA, Rockwool Exterior comfortboard 80 (1.5”), and batt Rockwool R-23 insulation
* Effective R-value of opaque assembly = 25
* $5.82 per sqft - (60% more than previous assembly)
8. 2x4 w/zip sheathing, Atlas energy guard 2” polyiso (R-13), and batt rockwool R-15
* Effective R-value of opaque assembly = 27
* $ 4.05 per sqft - (30% less than previous assembly)
9. 2x8 w/ zip R-6 (or R-6, R-9, R-12) and batt Rockwool R-30 insulation
* Effective R-value of opaque assembly = 30
* $4.82 per sqft - (19% more than previous assembly)
10. 2x8 w/ plywood, Prosoco R-guard, 3” of Polyiso (2 @ 1.5”, offset seams), and batt Rockwool R-30 Insulation
* Effective R-value of opaque assembly = 45
* $7.13 per sqft - (48% more than previous assembly)
First five assemblies:
https://www.youtube.com/watch?v=VYqINjqKafY
Second five assemblies:
https://www.youtube.com/watch?v=Gvd4NRHvmO8
See comment above last one for my proposed solution for isolating stud bays for dense packing. each installer I have spoken with wants bays sectioned off into smaller spaces to dense pack. Only one so far seems to have done a deep wall more than a few times so it is a potential problem. my theory is.....make it easy for them....you will get a better price and job.