Planned exterior rigid insulation meets unexpected poly sheets

Hi all. I’m starting an addition/renovation on my 1920’s home in Ohio (Climate Zone 5). First bump – unexpected poly abutting the drywall in some of the walls. I’d previously encountered cellulose when coring the walls to install bathroom vents. Operating under the assumption that the insulation would be consistent (the house was renovated in the 90’s and again, in part, in the 00’s), I planned on removing the exterior siding, air sealing and installing a 1.5″ layer of polyiso board on the exterior of the house, including the new framing (2×4 walls; FWIW the wall assembly is attached). I removed the trim on the windows this past weekend and discovered that a large portion of the house appears to be batt insulation with poly sheeting abutting the drywall. I’ll pause to acknowledge what happens when you assume and what happens to best laid plans (Dana had even led me to sourcing reclaimed polyiso nearby). So…now what. Moving forward with the polyiso board would result in large sections of the walls having no pathway for drying, which feels like a pretty terrible idea. It seems like one option is to shift to 1.25″ or 2″ of Rockwool Comfortboard since that would allow drying to the exterior. Unfortunately, the Comfortboard is much higher cost than reclaimed polyiso. Another alternative would be to let sleeping dogs lie, not mess with exterior insulation and flip to 2×6 walls on the addition with either cellulose or open cell spray foam. I’d then turn my energy to air sealing as best I could on the addition and existing house. Any other ideas or glaringly obvious things I’m missing? Thanks.
GBA Detail Library
A collection of one thousand construction details organized by climate and house part
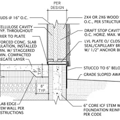
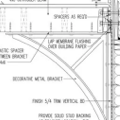
Replies
If you have the walls open anyway, you could easily remove the poly. All you need to do is run a knife down the edge of the 2x4 to cut out the poly. It’s ok I have a little bit of poly on top of the studs and other small areas you can’t access — as long as you remove the bulk of the material you’re wall will be fine.
If you end up replacing the batts, I’d consider replacing them with mineral wool. I’ve been doing that with my own house. The advantages are a little more R per inch, and typically also a better installation since rockwool is easier the cut and fit tightly into place compared to fiberglass.
Bill
Thanks for the response Bill. I actually wasn't intending to open the interior walls - I discovered the poly in pulling off the window trim. The vast majority of the existing wall interiors won't need to be demo'd, so that poly would stay. Although it seems like you can get the poly and vapor closed rigid foam to play nice together in some climates (caught this by Martin: https://www.greenbuildingadvisor.com/article/rethinking-the-rules-on-minimum-foam-thickness), as the climate gets more humid, that seems to get riskier. Columbus, OH is in a "cold" county, but (sadly) I'm guessing in the coming years it's going to trend more mixed-humid (we had heavy AC days this summer). Seems like the safe route is to use something vapor open, which led to the Rockwool. I'm curious if others have had experience with exterior insulation and poly in a mixed-humid climate. Would unfaced EPS allow for enough exterior drying potential?