Plastic at bottom of exterior walls cavities: a partial vapor barrier?

Hi folks,
Longtime lurker but and first-time poster here. I have a 1960s brick ranch on a crawlspace in the midst of a partial remodel. Some details about the construction:
Foundation: CMU, crawlspace
Sheathing: Celotex fiberboard, no housewrap
Insulation: Originally dense-pack cellulose installed through sheathing, installing Roxul
Framing: 2×4
Siding: Brick, 1″ gap to sheathing, no brick ledge, no weep holes
The dense-pack holes were all patched with stapled-on cardboard when the house was built, and I have caulked the patches to reduce air leakage. My goal is to make the home as airtight as possible with a reasonable DIY effort. I am partway through insulating with Roxul and had, after agonizing over the issue and combing through this site at length, intended to omit an interior-side vapor retarder due to the vapor-open nature of the assembly. The home is located in southwest Ohio in Zone 5 but only about 50 miles north of the Zone 4 border. We run the A/C six months out of the year.
Black poly sheet is present in the stud cavities along the bottom 4-8″, depending on the wall, on the inside face of the sheathing. This poly extends down to the sill in the crawlspace but is hidden between the band joist and the brick. (I encountered it while working on the framing in the crawlspace.) The gap between the brick and sheathing breathes near the crawlspace vents. (Don’t get me started on the crawlspace–that’s a work in progress!)
I would guess the purpose of this plastic is to shield the wall cavity from wind-driven moisture or splashback, but it’s odd to find it inside the wall rather than as flashing on the outside. The home has 24″ overhangs, so rain hitting the brick is rare. Ground splashback was happening when I bought the home but has since been addressed with new gutters.
When a wall has plastic as shown in the pictures, does it create a localized vapor barrier that will collect condensation cause moisture concentration on nearby framing? In particular, I have a wall junction that contains horizontal blocking that partitions the vertical extent into four sections, one of which is almost entirely lined by poly on the sheathing.
The framing is in mint condition except in spots where there have been bulk water leaks, but the original insulation was cellulose, which adsorbs moisture, and not rockwool which resists moisture. I have never seen walls detailed like this and am concerned that installing rockwool instead of cellulose with this plastic present may create a localized problem at the bottom of the walls that will rot nearby lumber. Am I overthinking this, or should I be concerned?
W.
GBA Detail Library
A collection of one thousand construction details organized by climate and house part
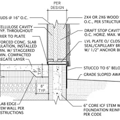
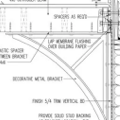
Replies
Hi Whiseve -
Always hard to address all the connectedness around a simple question...
In short: that black poly sure looks like a mason's flashing. In otherwords, a bottom-of-the-wall flashing installed by the mason, and because of sequencing, quite often reverse-lapped with other components of the exterior wall (like the WRB, which your assembly lacks, a big concern frankly). Good for the builder to weatherlap the flashing with the wall sheathing; shame on the builder for leaving out the WRB.
What impact does this 8-inch flashing have on the vapor profile of the wall assembly? Zero. Vapor pressure is a field effect so localized vapor permeance of that little flashing is noise.
On the other hand, without an WRB, water that gets to the backside of the wall sheathing will be COLLECTED rather than shed by this flashing.
On the other hand, proof is in the pudding: if you only have localized bulk water leaks you have already addressed, excellent and thank the builder or the architect for those hefty eave overhangs. Might be a different story on gable walls...I would carefully check them for bulk water leakage as well.
Peter
Agreed with Peter... whatever localized dampness/humidity that might occur behind that flashing will have an easy time evaporating/migrating in some other direction. It only needs to travel a few inches to find a way out of the wall.
Thanks guys. I won't worry about it then. The sheathing definitely runs below floor level to the sill plate, so the explanation that it was installed out-of-sequence makes sense and fits with other aspects of the construction.
There is that one section, at the junction where an interior wall tees into the exterior, where horizontal blocking is located just 1" above the top of the plastic sheet. The cavity, once insulated, would have only a 1"x6" strip of exposed sheathing and would otherwise be surrounded by 2x4's and would be open to the cavity of the interior wall. Is it still true that there would still be ample ability of moisture to escape this confined area? Originally, the cavity had two layers of crummy foil-faced fiberglass insulation jammed in there haphazardly and was a definite cold spot on the IR cam.
I have been installing the insulation rather slowly and discovered the hard way that you can't take your time in the middle of winter. The sight of damp sheathing led me to consider the flashing as another potential problem area. My intention is to get the insulation up and follow quickly with drywall.
With this type of assembly, would MemBrain or comparable product be a good idea? I'm trying to air seal as much as possible and had planned to gasket the drywall. We're in Zone 5, just north of Zone 4, where a class III retarder is acceptable with vented cladding. My brick doesn't appear to have a well thought-out ventilation system, but there is an air gap open to the crawlspace on each wall. Not sure how air exits the system other than through slight gaps in the soffit.
My electrical system is all metal, but I've used fire putty on all the boxes to reduce leakage as much as possible. A small amount of air will likely leak through the MC cable. I had hoped to be able to just drywall and paint. The original construction had no vapor retarder, nor mold, but was dense-packed with cellulose. I would have gone with cellulose again (why mess with what works) except doubt I'd be able to schedule a contractor in the middle of winter given the other challenges of this project. A simple DIY installation is very appealing.
I have confirmed, while patching damaged isolated damaged areas of the sheathing (mechanical damage) that there is no house wrap at all. Nor is there a brick ledge or weep holes. I almost never see wet brick, though. Peter, your point about the gable is noted. The roof is a hip design with a perpendicular gable facing the street with significantly shorter overhang. There is no brick above the front window, only vinyl siding. That's one of the walls I have not opened, but I have not encountered any evidence of damage yet.
Thanks for your input. This web site has been a tremendous resource and I really appreciate your help. The local area lacks contractors with attention to detail or knowledge of building science, so I'm on my own here!
W.