Plastic under slab and insulation

I’m in the process of building a net zero house, and my builder is about to pour the slab. The house will have 4 inches of Dow XPS insulation under the slab. My builder indicated that he thinks the insulation alone should provide a sufficient moisture barrier, and a plastic barrier under the insulation should not be needed. Is this true?
Thank you
GBA Detail Library
A collection of one thousand construction details organized by climate and house part
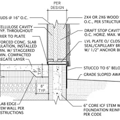
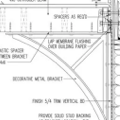
Replies
You might find this discussion useful.
https://www.greenbuildingadvisor.com/question/poly-vapor-barrier-under-xps-foam-board-in-slab-radiant-pour
Do you have radon concerns? Do you have a free draining material bed (i.e. crush stone)?
A radon systems was installed, and crushed stone has also been installed. I will not have radiant heat though. I will be heating and cooling with Mitsubishi mini splits.
GPF,
I really can't speak as to whether your builder's notion is correct or whether it is common practice to omit the poly.
The link I provided was to show that, from a numbers perspective, even 4" of XPS won't get you as low a permeance as 6 mil poly. I don't think you'll quite reach the value of a true vapor BARRIER of 0.1 perms.
Someone with a lot of experience specific to your conditions (evidence of success/failure) or with a thorough moisture analysis (scientific proof) may be-able to say for sure. Consider that many older buildings used neither poly nor foam, and not all had problems. There are many factors to consider (local and imported soils, surrounding grade relative to slab, water table, finish floor material, tightness of overall house design).
I'd be curious if your builder does this often and has a good track record? To me, poly seems like relatively cheap insurance. Unless the foam is taped, poly may also keep the foam from 'floating' and the concrete from seeping into cracks. Perhaps a non-issue.
Two other notes:
1)If you're concerned about global warming potential, EPS is superior to XPS (blowing agents) and if you spec the correct type is totally sufficient. That will change the perm numbers.
2) If you use poly, many argue it should go above the foam (against the underside of concrete) so as to not trap moisture between the foam and poly.
The poly is so cheap and easy to install it’s not worth the builder arguing. It’s better for the reasons mentioned.
We did this retrofit with plastic above the foam, I asked here about it at the time. The real moisture issue was from the concrete during the pour. Which was why we went above. Your XPS foam won’t work very well when it’s super wet, and your concrete will cure better if the water stays with it.