Air Barrier/Vapor Retarder and Canadian Building Codes

This comes up quite frequently and I thought it might be useful to lay out what is actually required by the code. My description relies on the BC Building Code, but I am fairly confident it applies to all provinces that have based their codes on the NBC.
The code requires all building assemblies to include an air barrier and a vapour barrier.
The air barrier can consist of a variety of sheet or panel materials. It can be located anywhere in the assembly. That is the inner, intermediate or outside surfaces of the assembly (9.25.5.1).
The vapour barrier can be any material less than 1 perm. It has to be located “sufficiently close to the warm side of the assembly to prevent condensation at design conditions (9.25.5.2). The requirements further explain it must be “at a location where the ratio between the total thermal resistance of all materials outboard of its innermost impermeable surface and the total thermal resistance of all materials inboard of that surface is not less than that required by table 9.25.5.2.” This table has columns for degree days, minimum RSI ratio, minimum outboard thermal resistance, and sheathing thermal resistance.
The code anticipates the use of exterior foam as a vapour barrier and requires that the inner-surface of the foam meet the requirements of maintaining a condensation free temperature or the assembly is required to include another vapour barrier closer to the interior. ((9.25.5.1 Appendix A (thermal Insulation).
So in summary: Poly is only one of a variety of materials described in the code accepted as both air and vapour barriers. Other sheet goods, panel materials such as plywood and OSB, paints and coating, and foam are all explicitly mentioned. Exterior foam may be used without an interior vapour barrier as long as it is thick enough.
GBA Detail Library
A collection of one thousand construction details organized by climate and house part
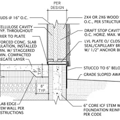
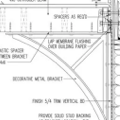
Replies
Malcolm,
Thanks for posting this information clearly and completely. In the future, I will refer Canadian readers who are confused by the code to your useful summary here.
Using exterior foam as a vapour barrier serves no useful function in most Canadian locations & wall stack ups, but rather only impedes moisture from leaving the susceptible sheathing material toward the exterior. The interior temperatures and the sheathing temperatures rarely dwell below the outdoor air's dew point long enough to matter, which is why in most wall stack ups it's safe to install interior polyethylene. (The exception is in some masonry or stucco stack ups, where sun driven moisture coming out of the cladding brings the dew point of the entrained air inside the wall cavity above the temperature of the interior, causing liquid moisture to condense on the polyethylene.)
When dry both half inch CDX and OSB both perform as vapour barriers at the Canadian code definition thereof, but become more vapour open than the definition when wet- they are "smart" vapour retarders. If the code really intended for there to be a vapour barrier on the exterior, it wouldn't matter what the vapor retardency of the exterior insulation was, only the RSI value.
Table 9.25.5.2 in the NBC is not the equivalent to the IRC's TABLE R702.7.1, since it presumes a Class-II or tighter vapour retarder, whereas the TABLE R702.7.1 presumes Class-III vapour retardency. Under the NBC the outboard insulation material is ALLOWED to be low permeance, as long as it meets the minimum ratio in the table, but it is not REQUIRED to be a vapour barrier, and in fact the assembly will be more moisture resilient if the outboard insulation is high permeance (such as rigid rock wool) allowing moisture to easily leave the sheathing toward the exterior.
A quick internet search comes up with that table, found on page 39 (PDF pagination) here:
http://www.nrc-cnrc.gc.ca/obj/doc/solutions-solutions/advisory-consultatifs/codes_centre-centre_codes/revisions_errata-revisions_errata/2010_nbc_revisions_errata_november2013_2nd_printing.pdf
Dana,
Thanks for the useful commentary. Whether or the code requirements make sense from a building science point of view is much better left to you.
Two points that need clarifying:
- The table you have linked to from my post (9.25.5.2) was not the one I should have cited. It is found in 9.25.5.2 Appendix A, Sorry I can't find it online.
- Here is what the code says in relation to foam (9.25.5.1 Appendix A):
" Thermal Insulation
Where low-permeance foamed plastic is the sole thermal insulation in the assembly, the temperature of the inner surface of this element will be close to the interior temperature. If the foamed plastic insulation has a permeance below (1 perm)... it can fulfill the function of a vapour barrier to control condensation within the assembly. However, where low permeance is installed on the outside of an insulated frame wall, the temperature of the inner surface of the insulating sheathing may fall below the dew point. in this case the function of vapour barrier has to be provided by a separate building element installed on the warm side of the assembly."
Malcolm,
OK, I'm a little confused now.
How would the statement " rigid foam can only be used without an additional vapour barrier "where it is the sole thermal insulation in a building assembly" apply to a wall with interior batt insulation and exterior foam (where the sheathing is the air barrier and the wall is designed so that the sheathing temperature remains above the dew point)? Does this wall assembly then technically not meet code?
Dana, good point that with insulation outboard of the sheathing, from a building science point of view, it is OK for it to be a vapor barrier, but it is not necessary for it to be one, assuming the R-value ratio is adequate. In a typical design with mineral wool exterior insulation, requiring the vapor barrier is silly. I can think of one scenario in which the lack of that vapor barrier might cause a problem, but it's a pretty unlikely scenario: If you used exterior mineral wool board, and then used T1-11 siding over that, with no rainscreen gap and with the top, bottom and seams well sealed. Maybe the code is designed to avoid that problem? More likely they just didn't think it through as carefully as you did.
Rob,
Apologies, the confusion was all mine. I stumbled downstairs in the middle of the night for a snack, looked at the code appendix, thought I had mis-read the intent of the section and posted that caveat. Once I fully awoke i edited my post.
Charlie and Dana,
It does seem like the situation is only halfway towards reconciling the old, expected interior poly vapour barrier to a solution that that deals with impermeable exterior insulation. Coincidentally, I just received a package of six hundred pages of recent code revisions. I'll wade through them in the next couple of days and see if they have addressed the problem further.
Very opportune comment. Until today, I had never seen table 9.25.5.2. (and I've only read the Ontario code a hundred times!) I am currently being taken to task by my building officials, because I am against putting a second vapour barrier in the wall. My configuration is 8" brick, 1" air gap, 3" polyiso (foil and sealed to the interior), 2x4 stud wall with batt insulation and 1/2 drywall with primer and latex paint (no poly). It seems that the official policy in my town is "when in doubt, put poly in", and well, they are always in doubt it seems. Aside from table 9.25.5.2, we did a lot of dewpoint simulations, and found our assembly to be fine. We presented this to the staff, and received our permit. Now that we are executing the plan, they have doubts. But the table seems clear. If I read (and interpret) it correctly, they are discussing the ratio of insulation outboard (to the exterior) of the vapour barrier (impermeable surface) to inside. If this interpretation is correct, and as an example, a wall with R-6 to the outside and R-19 to the inside would still pass muster (according to the code). So R-20 outside and R-20 inside would also pass (= 0.5). As I have R-19.5 outside (3 inches polyiso), it appears that a truly absurd amount of interior insulation (up to R-64) would still pass. Am I missing something? And I guess, why are they busting my chops??
From my understanding as long as your latex paint is an approved vapour barrier from the manufacturer and meets the relevant can/csa standard for testing and you said to have R-19.5 of polyiso you exceeded the minimum code. Not sure why the building officials are giving you a hard time.
I heard of some designers who won't spec polyiso or XPS on their exterior walls even though it meets/exceeds the minimum code. Some designers just don't feel comfortable with it based off their experiences.
Alec, I am having the same discussion with a code official here. He insists on the 2/3 exterior to 1/3 interior. I referenced that same table, and haven't gotten a comment back. I have followed up.
My preferred stack up includes the following, from outstide-in
Cladding (stone skirt, fiber cement)
1/2" rainscreen
1/2" exterior gypsum (26perms)
2x6 stud wall with Roxul R22
1/2" plywood (vapour control layer, 1 perm)
3.5" dense pack cellulose R12
2x4 interior stud wall with dense pack cellulose R12
1/2" interior gypsum (26perms)
Primer + paint
Exterior ratio is 0.47, which exceeds the 0.20 required by table 9.25.5.2. I feel like this is a very robust, resilient, and easy to build wall, but can't seem to get anywhere with it.
Reply to Alec and Ryan,
I'd urge you to read the appendix A-9.25.5.2, especially the table A 9.25.5.2 which spells out in much greater detail how to calculate minimum thicknesses of low-permeance materials and also gives examples with ratios. It really clears things up.
The 1/3rd -2/3rd ratio seems to be folk wisdom and certainly isn't in the code.
Thanks for all the responses. At the end of the day, the city accepted the proposed profile we developed with the engineer. We are good to go.
Now all I have to convince them of, is to let me use Comfotube (semi-rigid ventilation duct). Sigh!
I know it's an old thread, but did you end up getting approval for use of Comfotube?
Since this is a reference thread:
> "air barrier ... can be located anywhere in the assembly"
But not without restrictions. In Ontario code I see:
9.25.3.1: "...include an air barrier system that will provide a continuous barrier to air leakage,
(a) from the interior of the building into wall, floor, attic or roof spaces sufficient to prevent excessive moisture condensation in such spaces during the heating season..."
For example, take a Zip sheathed wall with no exterior insulation. It's tempting to use the Zip as the sole air barrier. But IMO, it's quite possible that this won't "prevent excessive moisture condensation" - air can flow from the interior, deposit moisture on the cold Zip and then return to the interior. So in this case, an interior side air barrier may be required.
See various Lstiburek documents and here and 4.2.3 here for support for "exterior only air barriers can allow excessive cold climate condensation".
Hi all, I didn't read the entire the thread but from my understanding is that:
1) A vapour barrier must be installed.
2) The vapour barrier must installed on the warm side of the wall assembly.
3) An air barrier must be installed on the interior of the wall(a caulk/tapped poly will accomplish this) AND a air barrier must be installed on the exterior wall (Tyvek or foam board depending on if the manufacturer allows it and using your installation instructions).
4)If you install foam board on the exterior of your house which acts as a vapour barrier(you must check your manufacturers specifications to confirm this). It must be:
a) Installed on strapping for an air space for potential drying OR
b) Installed with a sufficiently high R-value using 9.25.5.2.
5) If you need to use Table 9.25.5.2. you need to find the r-values of every material in your assembly and calculate the in-board and out-board ratio. The appendix in the building code shows an example which can be followed. Your in-board r-value is the sum of the r-values of all building components from your dry-wall up until you reach your foam(do not include your foam). The out-board is the sum of the r-values of all your building components from the foam to your cladding(include your foam).
Without knowing your assembly and where you are located, it's hard to say for sure what will be the minimum code compliant option in your case. I did a practice calculation for a cold northern ontario climate and it turned out R-10 would be needed, however in other parts of the code r-7.5 also was "code compliant", which shows the need to do an in-board out-board calculation. Not many people are aware of this from my experience.
Moose_head27,
There are some differences in the code wording from province to province, but in general:
1. You need vapour-barrier.
2. The vapour-barrier does not have to be installed on the warm side of the assembly, just close enough to the interior that it don't cause condensation. The ratio is taken from table 9.25.5.2.
3. There is no explicit requirement for the air-barrier to be located the interior face of the wall, as long as the assembly will not experience condensation if located elsewhere (that's the point Jon made above). I don't see a requirement for a second air-barrier on the exterior, just a WRB.
4. a) Is there a code requirement for an air-space to help dry the foam?
5. The ratio in table 9.25.5.2 applies whether there is exterior foam or not. It is the ratio of insulation inboard or outboard of the vapour-barrier.
Malcolm I took this from the Ontario Building Code along with my comments. From what I'm told the National Building Code of Canada is very similar.
2. There's no mention of having your "Primary" vapour barrier located using 9.25.5.2. The code states it must be on the warm side indicated below.
9.25.4.3. Installation of Vapour Barriers
(1) Products installed to function as the vapour barrier
shall protect the warm side of wall, ceiling and floor
assemblies
3. The code below mentioned a interior and exterior air barrier. From what I know this means you need two air barriers for your wall assembly. From what I've seen the WRB is installed and acts as exterior air barrier.
9.25.3. Air Barrier Systems
9.25.3.1. Required Barrier to Air Leakage
(1) Wall, ceiling and floor assemblies that separate
conditioned spaces from unconditioned spaces or from the
ground shall be constructed so as to include an air barrier
system that will provide a continuous barrier to air leakage,
(a) from the interior of the building into wall, floor,
attic or roof spaces sufficient to prevent excessive moisture
condensation in such spaces during the heating season, and
(b) from the exterior inward sufficient to prevent
moisture condensation on the room side during the heating
season.
4. That drying air-space is only an option if you are installing foam board on the exterior which has the properties of a vapour barrier. For example, lets say you want to install R-7.5 XPS insulation, which has the properties of a vapour barrier but when you complete the in-board/ out-board calculation your assembly doesn't meet the minimum ratio. In this case you can install the R-7.5 XPS but you need to install it on strapping to create the air-space.
If you are against installing the airspace, you then need to increase your exterior foam to a R-10 XPS and do you calculation again to see if you meet the minimum ratio. Generally speaking you would only alter your insulating materials to meet the minimum ratio. If you are using a batt insulation you could look at lowering the R-value of the batt which would increase the ratio. All substitutions like your sheathing or gypsum will have a small effect when you calculate this ratio as well.
9.25.5.2. Position of Low Permeance
Materials
(1) Sheet and panel-type materials described in Article
9.25.5.1. shall be installed,
(a) on the warm face of the assembly,
(b) at a location where the ratio between the total
thermal resistance of all materials outboard of its innermost
impermeable surface and the total thermal resistance of
all materials inboard of that surface is not less than that
required by Table 9.25.5.2., or
(c) outboard of an air space that is vented to the
outdoors
5. The table 9.25.5.2. only applies if your exterior foam acts as a vapour barrier. The publishers of the code recognize that exterior foam used in todays construction have properties that can act as a vapour barrier. Since we have a vapour barrier on the warm side we need to have a solution if we create a second vapour barrior on the exterior by builders using foam products.
You can have foam that doesn't act as an vapour barrier and not installed on an airspace and not using the table. The code above states you need a vapour barrier on the warm side so if your exterior foam has the properties of a vapour barrier then you either install in with an air space or use the table and do you calculation to ensure your assembly meets the minimum ratio.
Overall this is only my interpretation of the Ontario Building Code and what I've been taught. Other codes may be different but if I'm wrong in any way please let me know!! Forgive me for any grammar mistakes!
9.25.3.1 (b) seems like a typo. Perhaps it means "cooling season", when exterior moisture is high and interior side condensation is possible.
All the code references were a copy/paste from a PDF Ontario Building Code I have.
moose_head27,
This is confusing stuff - especially when there are differences in how Provinces have worded the same sections - and it says something about how poorly the codes are worded that we are having this discussion. Here is my take:
2) If you continue reading 9.25.4.3, clause two goes on to say that the vapour-barrier only has to be "installed sufficiently close to the warm side to prevent condensation at design conditions ". That means the primary vapour-barrier can be exterior foam as long as it meets that criteria. If you go that route you have to use table 9.25.5.2.
3) I don't think the code is asking for two air barriers. it is just defining how the air-barrier must work, and what it must protect. Houses can still be built with board sheathing and building paper, which would not qualify as a second exterior air-barrier.
4) The option to use an air-space vented to the outside, rather than meet the ratios of table 9.25.5.2, is for other impermeable sheet goods, not foam. It would make no sense to have a vented air-space with foam outboard. It's basically saying if your exterior sheet goods do not allow drying you need to put them on a rain-screen.
5) I agree. Table 9.25.5.2 only applies to low-perm exterior insulation. But that (usually foam) can act as your primary vapour-barrier. There is no requirement for the second one "on the warm side". The table is there to ensure it is on the warm side.
So my takeaways are:
- You only need one air-barrier. It can be located anywhere in the assembly as long as it doesn't cause condensation problems in the wall.
- You only need one vapour-barrier. It can be located anywhere in the wall where it will not cause condensation problems. Exterior foam can act as the vapour-barrier by using table 9.25.5.2.