Pressure pan readings on can lights and exhaust fans

I was testing a house yesterday and took pressure pan readings at some of the can lights and bath fans, while the blower door was running with the house at -50. One story house, flat ceilings, vented attic. The can lights are older style, had a good deal of air coming in through them, and tested at about 45 pa wrt indoors. The bath fans are newer Panasonic models vented to a gable wall with well-installed flex, and tested at about 10 pa. They didn’t have much air coming in, according to my trusty biometric airflow sensor.
Questions: any of you blower door geeks check stuff like this, and if so, what do you normally find? If a fan is +10, is that a fairly low level of leakage, or is there room for significant improvement, perhaps by installing a better wall cap or maybe an inline damper? No doubt a can light at +45 is a major hole to the outdoors, so if I change it for an IC/AT version with an “air tight” trim, what kind of numbers would I be getting? Any other comments?
GBA Detail Library
A collection of one thousand construction details organized by climate and house part
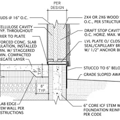
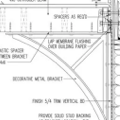
Replies
We've not been testing cans or fans during the blower door test but have been confirming exhaust rates for a while and the bath fans, even with 6" hard steel duct and exterior damper hoods are often quite under-performing. Strangely, the ones that we use to exhaust air from the crawls through a 4" galv by 20-30' vertical stack up the chimney do surprisingly well. go figure.
Michael, I usually test all the fans and only a few perform near the rated CFM. Those are the ones that are not more than a few feet of straight duct from the wall cap. Anything with more than that is likely to be 75% or less of the rating. Curious to know why you are venting crawl spaces with fans...?
I believe 45pa translates to 90% connected to the outside. 10pa = 20%. Can lights are notorious. You are supposed to box them from uptop. IC rated of course.
We routinely replace light housings with ICAT housings. Contrary to popular belief, the manufacturers allow you to put pretty much anything in direct contact with them, so there's not much reason for them not to be excellent in terms of air-tightness. We hit the wiring penetration and housing/drywall gap with can foam as we're sealing the attic.
10Pa is on the fan is not horrible. The catch with fans is that they leak through the duct and through the housing/drywall connection. Again as part of air sealing we'll seal the housing and ductwork. I like Broan's roof caps, but the backdraft dampers are a bit mediocre. I've used the cloth back-draft dampers sold by EFI with good results @50Pa. However, my gut instinct is that the cloth dampers may be effective at high pressures but not the low pressures typically seen in most houses. E.g. get one of the cloth dampers and blow on it.
We are completing an ICF home and recently ran tests with the blower door just before blowing in the attic insulation. We set the blower door to -50 Pa and used a pressure pan to document readings for all ceiling boxes and the four IC rated can lights that were in the kitchen. The boxes had wire penetrations sealed before sheet rock but none had been caulked to the sheet rock. The initial readings were in the -18-25 Pa range with the house at -50 Pa. As we used the pressure pan, we also noted the relationship in decreased air leakage by noting the change in CFM @ 50 on the manometer as each box or can was covered up. We noted that depending on which location was covered up, the CFM reading changed relatively in line with the Pa change at the pressure pan, somewhere around 18-25 CFM @ 50 per location. We were performing this experiment to have another useful tool to QA air sealing without going into the attic and what the significance would be of a certain pressure pan reading.
Additional information you will want to be aware of is that this 3780 sq ft home was only leaking 850 CFM when we started, which is pretty tight by normal standards. The other thing that was going on was that our insulator was in the attic with Knauf Eco Seal. After the initial readings we turned him loose to seal along both sides of each of the interior walls to the sheet rock and also to fan spray over all of the electrical boxes in the attic. The final result was a 3800 sq ft home that leaked just a little over 500 CFM @ 50 Pa. All in All it was a pretty informative day. By the way, the Eco Seal application would have been around $650 to $800 for the insulator to make a reasonable profit. The product is in the neighborhood of $225 per five gallons and they got well into a second bucket before they were done.