Pretty Good Price for Pretty Good House

I have a construction project in the dream stage right now–looking to calibrate my expectations in terms of cost. For instance:
– Pretty Good House envelope/mechanicals
– 2 stories
– roughly 2000 sq ft
– modest to mid-level finishes
– relatively low cost area (ruralish Shenandoah Valley)
– assume no DIY
– ignore costs for land, driveway, and getting utilities to house
Is $150/sq ft a reasonable target? Is it a pipe dream with current materials costs? I imagine breaking ground in 2 years or so.
GBA Detail Library
A collection of one thousand construction details organized by climate and house part
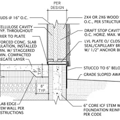
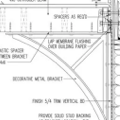
Replies
I am working on a design myself here in Minnesota. Using $200 per sq ft with me doing plumbing, electrical, HVAC, air sealing, sheet rocking, painting, and some finish work in the basement.
Thanks for the data point. I'm hoping it will be cheaper than that around here, but this is the sort of thing I need to know.
Paul,
Unfortunately you would do much better to Ask around locally. The differences between regions, and even between what several builders in your area will charge make any estimate you could get here useless.
Malcolm, indeed--I'm just thinking that people here will know what Pretty Good House means and might be more willing to give out a ballpark number to someone who is not a potential client (because I won't later fuss at them for not holding to that number). And if my hopes are way off then at least I am spared be laughed-at to my face...
Paul,
As Armando said, material prices have gone mad here too, but they still don't account for the increase in building cost we are seeing. It isn't rational and that's what's got a lot of us spooked. Right now what a particular house will cost seems to be whatever a builder ends up quoting you. I wish I could be of more help. Although price per sq ft is a poor metric, for a couple of decades I could predict it within a small margin, knowing the types of components and finishes houses I designed typically contained. That's out the wind0w now, and it makes it very difficult to tell clients how big a house they can afford on a given budget.
Good luck figuring all this out. If it's any consolation, many of us are in the same boat.
+1 what Malcom said. Cost of building houses have gone up by 20%+ just last year. Who know what's going to be in two more. Scary times.
You know, 20% is better than what ill-formed imagining I had in my head. I guess I was seeing lumber prices and imagining the full cost scaled up by the same amount (which is, of course, wrong). My gut tells me prices are up temporarily, but I'm not going to bet on it.
Dollars per square foot isn't really the right metric, because that's not really what drives cost. Think instead that your budget is $300K, the question is what can you get for that? What's a really good exercise is to start a budget: list all of the things that go into the house, put in a number for each and see what it adds up to. Even if you put in a placeholder number it's still helpful. It has never been easier to price stuff online than it is now. Talk to lots of people, and ask them what things cost in your area. As you learn more, refine the numbers.
What really drives cost is choices for interior finishes and features. You can spend $0.99/square foot per tile, or you can spend $30/square foot. I live in a high-cost area, and I've heard stories of people spending $50K just for tile, and $300K will get you a nicely appointed kitchen. That's not going to fit in your budget.
I would look at the houses that other people are building in your area and see what you can get in your budget. Believe it or not, home building is not a high-margin business, so the cost of new construction is going to be in the same ballpark as what it's going to cost you. You can also get an idea of what tradeoffs they're making. Their choices may not be your choices but it helps you think about what you want.
For your budget, here is the list of categories I use. Where things are grouped it's because the same contractor takes care of them.
Land Acquisition
Pre-construction (permits, architectural and expert fees)
Site Work
Foundation and Concrete
Structural and Framing
Roofing, Siding, Gutters, Downspouts, Exterior trim
Windows and Exterior Doors
Stairs and Rails
Plumbing
Electrical
HVAC
Audio, Network and Alarm
Insulation
Drywall
Flooring
Cabinets, built-ins
Interior trim, interior doors
Countertops
Interior finishes
Appliances
Decks, hardscapes and driveway
Landscaping
Final cleaning/punchout
Project costs (costs not included elsewhere like dumpsters and porta-potties)
Also add a line item for contingencies.
Let me add that for a PGH, which of those line items are going to change? Not many. Probably the biggest change is windows and doors, and then insulation. Framing may change a little.
You'll probably end up spending a little more in pre-construction on the plans.
That's for the excellent list! This is helpful.
The list is also pretty much in the order that things happen. So fill it out and you have your construction schedule too. Then the house practically builds itself (kidding).
You forgot beer after working all day on the project.😊
That's priced into the individual trades. For drywall, beer before and during the workday is included as well.
This list assumes you have water and sewer hookup. If not, add cost of well and septic.
Just wanted to say thanks for listing this out. This is a really fantastic overview of the components to budget for.
If you look at that list you'll see why dollars per square foot isn't really a helpful measure. Most of the things on the list aren't sold by the square foot. Some don't correlate at all -- what you spend on countertops has no relation to the size of the house. Some are loosely correlated -- other things being equal, you'll spend more on plumbing, HVAC and electrical in a bigger house than a smaller one -- but it's a loose fit. Others are sold by the square foot -- drywall, insulation, roofing, siding -- but it's not the square footage of the house, it's the installed square footage, which only loosely correlates to the area of the house.
The only one that is priced by the square footage of the house is flooring. And that is instructive too. You can spend fifty cents a square foot on flooring or fifty dollars. If you have a budget and the flooring you want doesn't fit, you have two choices: pick something cheaper, or do less of it. Which is pretty much the choices you have everywhere in the house.
Let's look at it this way--how does one go about choosing a budget? I could define a pretty hard upper limit based on how much we have now (minus what we want leftover) + how much we expect to net from sale of the current house + the largest loan we could get. But I don't want to spend that just because we can. So where to set it from there is pretty arbitrary. My first cut at this was to replace "largest loan we could get" with "15 yr loan with payments equal to our current payments". It's a pretty conservative budget for our current situation, but I wanted to see if what we want out of a house is remotely possible with that budget. It sounds like it is not... Anyway, the idea is to explore the trade space to arrive at a the target house and budget at the same time rather than letting one drive the other. Of course this only works when the house you want fits comfortably below the upper limit.
In any case, I like to think the parameters I set in the original question should allow for somewhat reasonable estimate. For instance, $50/sf flooring would violate the condition of "modest t0 mid-level" finishes. I'd say we'll stay below $10/sf for flooring, maybe closer to $5/sf for materials. I'm interested in healthy materials (however one might define that...), not luxury.
Now just to go off on a mental exploration, I wonder if we could, say, use the bathroom faucets as a good index to predict final cost/sf. That is, whatever level of bathroom faucet someone chooses probably reflects the overall level of finishes that someone will choose. Kitchen faucets, on the other hand, may be more prone to splurges. Or maybe you could use the kitchen faucet to predict the whole kitchen, the master bath faucet to predict the master bath and bedroom, and a common bath faucet for everything else. Or maybe flooring would be a better index. Maybe there's a research paper out there on this...
I think you've hit on exactly why cost per square foot can be useful -- it's a shorthand.
Guys who build houses for a living are generally pretty in tune to what sells a house, so they try to put as much of that into each house as they can. This means that at a given price point all of the components that make up the house are likely to be at a certain level.
I'd turn your example around and say that cost per square foot is a good predictor of what kind of bathroom faucets you're going to see. And floor coverings and electrical fittings and doorknobs and HVAC and dozens of other things.
The caveat is that this sort of comparison is highly regional. Not only do costs vary by region, but so do tastes. I will make a blanket statement however and say that energy efficiency does not sell homes, most builders will build to code minimum (if that). Which brings up another point, which is that you're building your house for your tastes, which may not be what everyone else wants. Everyone involved in the process will push you to do things the way they're normally done. "Think resale value!" will be the common exhortation. And there is a certain practicality to that, even if you plan to live in this house forever. If you are financing the house, it will be easier to finance -- and you'll get better terms -- if it's an easy-to-sell house. The energy improvements you make probably won't move the appraised value at all.
But I recommend them. Not only will they pay for themselves in energy savings, a tight house is just a more pleasant house to live in.
Here in the homeland of PGH, Maine, good-quality custom construction, PGH or otherwise, is starting around $250-350/sf. Upgrading to PGH details might cost 5-10% more than non-PGH but reduces expenses so you don't pay more each month. You can cut back fixtures, finishes and equipment to recover most of that 5-10% but not more in most cases, I find. If you're looking at $50/sf tile, you're not likely looking at a $300/sf starting price.
I tell clients that pricing homes by the square foot is like pricing cars by the pound (I stole that from someone, not sure who) and is really only useful to establish a basic ballpark budget starting out. After that, it's as DCContrarian says--you have to price out the parts, because every custom home is different.
Thanks. Unless I misremember, a house featured on a recent BS and Beer came to ~$300/sf? That house struck me as pretty high-end. And I'm not sure I can imagine what the properties of a tile would have to be to make me willing to spend $50/sf...
Yeah, I hated to ask in terms of $/sf, but I'm only looking for a number which matches the level of precision in the description I gave of the house.
Paul, yes I think Greg Fischer mentioned $300/sf for his bark-sided house, which seemed low to me, but I believe he clarified that he wasn't counting his own labor and he did a lot of the work himself. I'm designing several homes now that are very simple, PGH boxes, Passive House style, nothing over the top, and they are running around $300/sf.
Regarding square foot pricing, unfortunately it's the only tool we have before starting design on a custom home. I've just learned to mention repeatedly that it's a blunt object, not a surgical tool.
I suppose an unfinished basement doesn't count in the total square footage?
One of many problems with square foot pricing is that it is not consistent--everyone has their own way of doing it.
I use modified square foot ranges for spaces other than finished, conditioned space. Basements are not free--I include slab foundations as my baseline and add for basements.
Other elements I don't include in the base square foot price:
Land acquisition
Site clearing
Well, septic, sewer/water hook-ups
Electrical service from the street
Photovoltaic system
Standby generator
Decks and patios
Covered porches, screened porches, 3-season rooms
Garages
Site restoration or landscaping
Driveway
Design fee
Permitting fees
Another problem with square foot pricing--where do you measure to? Most measure to the exterior sheathing, but I usually have 12" walls, which can add 10% to the size of the same house with 6" walls.
Alex,
Under modern building codes the cost difference between an unfinished basement and a finished one is getting pretty marginal.
Why not just split the bid into two parts. Completed shell (forgive the terminology) fully wired, drywall, hvac (this can vary a lot i know but we can put something that will work) and then a second bid to finish it with basis of minimal finishes.
Seems like you have to get the bones right first. Finishes can be crazy expensive, but we can estimate with builder or Bog Box grade. I have been in million dollar homes that have had home depot kitchens.
1/5 acre or less here is $200-300K for land. The floor as they say is $150sf. Hard to study PGH is a place that has such expensive land!!!
Michael Maines, DC Contrarian, Paul Pfeiffer and anyone else.
Cant there be an agreement on what the components of the basic build would be for comparability.
Slab vs basement
Insulated slab (conditioned crawlspace)vs non insulated slab
Traditional vs double stud walls.
Understanding the variations even between those elements.
We should probably be able to get to a code min house as a basis and then guesstimate what each PGH feature gets you.
Seems this is doable certainly at a regional level.
I’ll add one thing there is an FHB article from the 90s I think issue 87 that talks about a house for $48sf.
I wrote to the podcast and they challenged, correctly I think, how realistic even back then, that number was.
Built on a slab, with 10 mil poly underneath, 12 inch Larsen trusses filled with insulation, r-60 attic and mid grade windows with splayed openings designed to be sat on.
There was an architect and he wrote the article. This was zone 6 in Maine. Cute house about 2000sf ($96k) had a blower door <1.
The article was written by the architect, Jim Young, and I don’t recall any sophisticated German/Swiss tapes wraps or anything like that. The author makes no mention of DIY.
The price quoted may be crap but i am dying to know how this house has done over the years as o think under scrutiny this might be a pretty good house.
I believe it’s in Dummerston Maine but try as I may I have not been able to figure out where exactly it is.
Oh and I would not use the build show as a reference
Thanks load this is a great discussion
Deleted
Paul,
Great input here. As a non-builder who has completed two custom homes and is planning a third, I advise you to set a not-to-exceed budget and then adjust the home to fit into it. Make the home as small as possible while still meeting your overall objectives. Find a builder/designer who demonstrates a talent for visualizing the type of structure you want to call home. If you have to stretch financially to accommodate a feature or finish, find another solution.
Avoid wishful thinking. Once you are into the build, it is very difficult to find any meaningful cost savings.
I'm going through this exercise now with a $550K maximum budget for a 1,800 (maximum) square foot home (not including land). Our market isn't particularly expensive, but I'm finding it more challenging to balance all of our wants and needs than I expected.
Good luck with your project.
On the matter of price-per-square-foot, I agree with Steve that it's far more critical to set a do-not-exceed all-inclusive cost to build, and then work backwards to see what you can and cannot afford--including, most importantly, square footage. There's an entire 20-season British TV show called Grand Designs that watches a hapless builder blow out their budget every episode. It's great cathartic TV to see others make worse decisions than me.
Do you tell the architect/designer/builder your not-to-exceed price and let them deal with setting a lower "target" price that leaves them some margin, or do you tell them you have a budget of X when your not-to-exceed price is something like 1.15X? It seems like providing your not-to-exceed price would lend itself to a fixed-price job where you are going to end up with a contract for that price (minus a budget for change-orders).
Somewhere I have a spreadsheet where I think I concluded 1600 sf would be sufficient. Then my wife upped it to 2000. If the responses I'm getting here truly represent the cost for the level of build we're seeking, then perhaps she'll come around. I am a little surprised, though, that we're converging toward a number roughly 2x what I find cited multiple places with a generic internet search. I expected higher...but not that much higher. I guess this is why Malcolm and Armando gave the advice they did.
If you don't mind saying, would you call your project "high end" or something more mid-level? Well, that's kind of a pointless question without a reference point. Mainly what I want is a durable, high performance enclosure with a thoughtful layout. The interior can be pretty modest.
Hi Paul,
I've done fixed and cost-plus and think either approach can go off the rails if your builder is (1) incompetent and/or (2) unscrupulous. So find a good builder is the first step.
On pricing, I did a quick search here and saw new production builds at around $150 a square foot. I imagine these homes did not include a bunch of nice finishes or "green-oriented" bells and whistles. I also checked some new builds in a community where I used to live that tends to have homes with fairly nice finishes and good energy efficiency. Those homes were listing between $350 and $500 a square foot (including land, which is way overpriced in my opinion). Backing out the land cost probably puts them in the range of $250 to $350 a square foot. But keep in mind that smaller homes tend to have a higher per foot cost. I've seen listing for nice 1,000 square foot homes priced at $500,000.
One other thought... Buying an existing home might get you more of what you want for less upfront cost. A lot of people take this approach and then make strategic investments over time to improve efficiency and comfort.
Upon reflection, I think the question is how much does going PGH add to the cost of a house? We can't tell you what it costs to build the house you want in the place you want. You can get an idea of that from looking at similar houses being built nearby. But we can give an idea of what additional costs would be involved in taking it to PGH standards.
Yes, that is a large part of the question. Michael has already chimed in with 5-10%. Whatever the cost is otherwise, that small premium seems obviously worth it to me.
One of the things you need to know in order to answer is what the non-PGH house includes. What's the starting point?
I’ve been working with DOE teaching the Zero Energy Ready Home Program for several years, and designing high-performing houses for over 20 years. Now, I can tell you with certainty, there is plenty of information on this website (GBA) and elsewhere demonstrating that the cost of building a Zero Energy Ready house is not that much more than a code house.
The Rocky Mountain institute came up with a study at the end of 2018, showing the costs of building a ZER home is around 1%-3% more, on the top 50 markets of the US. Anyone telling you it costs more than that, is usually someone NOT EXPERIENCED in the design and construction of these houses. The DOE’s ZERH programs also has plenty of homes in their Tour of Zero listing. Here are some links you should look into…
https://www.energy.gov/eere/buildings/zero-energy-ready-homes
https://www.energy.gov/eere/buildings/doe-tour-zero
https://www.greenbuildingadvisor.com/article/zero-energy-homes-ready-mainstream
https://www.greenbuildingadvisor.com/article/new-zero-energy-homes-almost-cost-parity
https://www.greenbuildingadvisor.com/green-homes/large-connecticut-home-is-zero-energy-ready
https://www.greenbuildingadvisor.com/article/zero-energy-ready-homes-gain-ground
I believe this out-of-hand for otherwise higher-end homes, but does it hold for more modest homes? I constantly get the impression that these homes are substantially more expensive. Some of that is probably due to a sampling error, that is:
(1a) Homes featured on the web or elsewhere are naturally biased toward higher end.
(1b) This includes things like PHI or LBC homes which are inherently high-price.
(2) Custom home clients bias toward wanting high end.
I also wonder if an economic force is also at play:
- Builders who require little extra to go ZER/PGH are better builders who already command higher premiums.
- These builders are also in high demand from high-end jobs making it difficult for more modest projects to hire them.
- Other builders actually do require a lot extra to go ZER/PGH because of their inexperience.
That second bullet is total speculation on my part as I haven't even talked to builders yet. Well, actually all of them are speculation. But in any case, my hypothesis is that if you otherwise want a modest home that going ZER/PGH is more expensive (than it theoretically should be) because you're either working with an builder inexperienced in those things or you are upping your project to be high-end enough to secure the better builders. I would love to hear that that is 100% incorrect.
How much of this strikes you as true? Anyway, as I go on I am talking myself into the paying the premium for better builders. Your links actually led me to one pretty near me, although I can't find evidence that they've built more recently than 2014 so I'll have to check on that.
@Paul - I just gave you plenty of info on the costs of ZER homes, plus the ZERH Tour of Zero. If you take the time to look at all the houses, or at least several of them, you'll see there, the majority are not large custom homes. In fact there are many affordable housing projects, Habitat homes, etc. I've also worked on several affordable housing projects, with the same lower costs. The main difference is we are not using granite tops, but Formica, or lower price flooring, roofing, etc.
The scale of economics are the same, you just need to learn how to get there, or hire the right people in your neck of the woods.
Yes, thanks for the great info. I did look at a sampling of those in mixed-humid. But mostly I focused on the builder of the only home in the tour that was (almost) in my area. Perhaps the newness of everything in the photos fools me into thinking things are higher-end than they are.
This is one of the best threads on the subject I’ve seen on GBA or anywhere else. Thank you to Mike Maines, DCContrarian, Armando, Steve, and everyone else. It’s made me feel much better about my project’s cost.
I agree. The only way it could be better if someone here could speak to Rockingham County, Virginia specifically. Well, that and if reality were different and my $150/sf was not a pipe dream.
You may wish to specify what you mean by "Pretty Good House" in some detail. I doubt most builders would understand that term from GBA. For example, tell the builder you want R-60 ceilings, R-30-ish walls (2x6@24" o.c. studs, R-19 fiberglass batts, plus 2" exterior polyiso or EPS foam, 1x4 rainscreen battens; or double stud walls 12" thick with rainscreen); or upgrades they are comfortable doing); Casement/awning/fixed double pane windows with argon fill and low-E coatings; air-tightness specs, etc. Try to have habitable rooms and larger windows facing south (for more wintertime solar gain if you have decent solar access, and less summertime heat gain). Avoid lots of west-facing windows to avoid summertime heat gain in the hot afternoons. There's lots of useful details that you will have to know to add to contract specifications.
Otherwise, they may tell you the houses they build are better than "pretty good", they are excellent, and you likely get code minimum everything. ("Incredible insulation" quoted one builder I know, then spec'd code minimums.) Ask about their experience making homes airtight, highly insulated, and window upgrades. See if they are open to at least having a conversation about energy efficiency upgrades or they claim it will cost tens of thousands when you know the approximate price of simple window or other upgrades. If they don't want to make adjustments, or haven't done it before, it likely will cost you much more than necessary.
You might try to let builders make a proposal then ask for upgrades for some of the items. That way you get a cost anchor point before telling them you want greater energy efficiency modifications at a reasonable price. You might note the flexibility or customer-service orientation of the builder at that point.
You might also specify some things that would keep costs lower, such as rectangular Colonial style home (minimize bump-outs and details that add labor costs and reduce energy efficiency, simple shed or gable roof). Keeping your plumbing centralized (bathrooms stacked above/below, kitchen sink nearby). Try to align windows and doors on existing framing members (to reduce labor and heat losses). Maybe the builder has some examples of homes or efficiency upgrades they have built that appeal to you.
Hopefully builders in your area are not so busy that they won't work with you except on their terms only. Some upgrades you can do later like adding ceiling insulation, but most cannot.
Best of luck!
Good advice from Robert. If you can, find a builder with "green" experience. If that's not possible, try to find someone who really wants to do the homework. If you end up with a traditional builder and still want lots of efficiency details, expect to act as the on-site expert (the shadow builder). This last option invites that's of stress (for you) and conflict (with the builder and the subs).
Thanks, while I like to believe I have gained the knowledge to be the on-site expert, it's a job I'd like to avoid for the reasons you cite. I think I need at least one pro with relevant experience to check/improve my ideas and to deal with subs. Presumably they would know who already does a good job. Or at least I imagine a sub would take direction better from a builder than a know-it-all non-builder. Also having worked on a renovation myself upstairs I have a respect for how hard this stuff actually is and how many details I am bound to be ill-equipped to deal with in a timely manner.
[I deleted my comment since it won’t help the OP with his issue.]
The problem is the high end is the thin tail of the distribution, there's only so many high end houses out there and a lot of guys who would like to compete there. It's telling to me that production builders target the fat middle.
Ah, I like the Build Show. It probably contributes to my perception of the expense of high performance building, though. I think he once referred to $400/sf as if it were surprisingly affordable. If $400/sf were the low end of the spectrum I either wouldn't build or DIY as much as possible.
So thinking about the turns this discussion has taken, I think I can offer an answer to Paul's original question.
Building a house to PGH standards will cost more. How much? Let's say 5%. While it will be a nicer house, it won't be reflected in the valuation. So if your budget is to spend $150/sf, you should be looking at houses that are currently being built in your region that are selling for $140 to $145/SF. Because that's what your house is going to look like.
Well put, thanks. I'm probably going to have to consider upping the budget and possibly reducing size, but clearly I need to talk to some local builders. Incidentally, if our current house can really sell for what Zillow estimates, then that will help a bit.
Paul -
I'm going through getting bids on an almost PGH level house in upstate NY. Pricing is coming in at $275 - $325 / sq.ft. Based on my experience, I think the premium for a PGH is likely 10% to 20% over a code minimum home. It shouldn't be this high based on the actual difference. But builders like to do things the way they always do things. Certain details that they aren't used to will be met with a fairly significant premium so they can cover themselves. The energy efficient builders will be more comfortable, but around me they tend to do luxury projects with premium level finishes, and in many cases passivhaus type stuff, so engaging them on a budget is questionable.
We are building an almost PGH house in Long Island, NY, and it’s coming in at around $450+/sq.ft. The minute you tell the contractors you need all these “extra” PGH details, whether it’s sealing, insulation or using certain products, their quotes always go up. Nothing fancy here either (doing Formica countertops in the kitchen, etc).
You know the price is the price. People who do good conscientious work should get paid appropriately, and the same for the makers of quality materials.
What blows my mind is the gap between what it costs to build a decent home built by decent people. A 2000sf house is $900K at the price. We need to close that gap. A PGH or Passiv house or dry basement and better home performance shouldn't be the exclusive province of rich people. How did we get to this point!
Here is a thought that was not intuitively obvious to me until I spoke with some builders.
When you say 150 $/sqft, make sure you are taking into account your garage, your screened back porch, covered front porch. I had somehow mentally assumed unconditioned square footage was free.
Also, if the green home industry as a whole cannot do better than 300 $/sqft, they really need to rethink the feasibility of it being adopted by the masses.
A simple 2000 square foot home would be 600k. Really out of reach for most people except the upper middle class.
Thanks, I was aware of that but had not included such spaces in my mental budget yet, so that's a good point. Yeah, the consensus above seems to be that green building does not cost much more than code, but at the same time the only cost numbers I actually see are pretty high. I'm not sure how prices compare between homes for sale and custom building, but I'm not finding much in my area for > $20o/sf, and that price includes the land it's on. So that gives me some hope. I'll have to let everyone know what estimates I get when I talk to builders around here.
In the last few months when looking at building a nice (luxury but not crazy) 2k SF home in NY, I got quotes of around $350/SF for a stick-built certified passive house and closer to $270 for code-minimum insulation construction using SIPs. Similar designs (each with a vaulted living room), and neither including architect fees (a considerable expense here at least, so keep this in mind) or site work. I ended up not going with either because I couldn’t justify the PH price and didn’t feel right pursuing the SIPs option, FWIW.
Jkonst,
Just curious. What was bothering you about SIPs?
Basically the whole house would be insulated with EPS, and the R values this company quoted were essentially code-minimum. Felt a little off going from planning a certified passive house insulated with cellulose to that! The fact that they didn’t offer an ERV/HRV also made me worry what other corners they might have been cutting.
I’ll note that I spent a lot of time (and a decent amount of money) with the PH firm going through design, and just did a very quick review of this other option as a reference point.
Also, a few other notes for the OP in terms of cost (not really PGH-specific but potentially helpful - things I wish I’d thought more about):
- If you want a garage or carport, make sure to budget for that upfront ($40k-$100k around here)
- Architect / design fees can be 5-10% of your project cost, if you are going the custom route
- $ / SF measures from the exterior walls, generally - might seem like a minor point, but with thick exterior walls your interior square footage can be 15-20% smaller than exterior
- Finishes are a critical element, as mentioned above. Think about what floors you want, cabinets (IKEA + custom fronts is reasonably affordable and attractive, but still a meaningful expense), plumbing fixtures, etc. My design/build team gave me allowances for each finish, which I realized I could very easily exceed
I just built a 1430sqft PGH and it came in at about $140 square/foot. But that was me providing half the labor and ordering all materials myself and managing subs. That price does not include any of my time.
By contrast, contractors in my area are throwing out numbers like $600-700 square/foot for a new build.
If your area is booming with building right now like so many are, contractors are getting used to getting paid pretty much whatever they ask for.
So, if you had to value your time at a skilled tradesman, add benefits, overhead, management fees and profit, what would you estimate your sf costs? $250?
Yikes, the builders are pretty busy around here too. I can't imagine any of them asking for $600-700/sf, though. A couple years ago I got bids to finish out the attic upstairs and the numbers I got pretty much said to me "we don't need this work". So I decided to do a lot of the work and hiring out of subs. That experience is partly why I just want the pros to do the new house. But if it comes down to it, got any tips for finding good subs?
I've spoken to one local builder who I think only does renovations but is familiar with the market here. The story is that a basic home pre-COVID was $125/sf, which would potentially have put PGH < $150. So it is nice to know I has some basis for my thinking. However right now that same home is $300/sf. Here's hoping prices come mostly back to pre-COVID levels in the next year or two.
The State of VA currently adheres to 2015 IEEC. IMO the only significant upcharge you should see is with regards to exterior insulation. Current code for walls are R13 + R1 (yes R1) or R15. This is a basic 2x4 wall. Using ZIP-R would go a long way to keeping the process as close to "normal" as possible.
Air sealing is 5 ACH50 and additional guidelines regarding HVAC sizing so there's some familiarity.
Basically what I'm saying is that you're not asking the trades to reinvent the wheel.
It’s hard finding contractor in zone 4 who can do exterior insulation. Most I’ve met in my market respond with “we don’t do that. Our climate is too moderate, we don’t need it.”
It’s really hard right now, when the market is so hot, the GC decides you are too much trouble and they can slap together a house cheaper and faster and with a bigger profit margin with a homeowner not so focused on quality and energy details
That's a constant challenge. Most building performance contractors and trainers recommend not selling on the energy savings but on increased comfort and building durability. But I have found repeatedly that clients don't think they need or want additional comfort if is costs more, and they don't understand the building durability argument. When shown energy model outputs that confirm that adding a little insulation is a good investment, though, they are reassured and usually go forward. That approach rarely, if ever, convinces a skeptic. But if a client want to do better, showing a reasonable return on investment has been effective for me. And if it's a terrible investment, it's hard to argue why it should be done.
Fighting against GCs who want to stick with what they know is another challenge. I try to stay out of that situation and work with builders who have similar values and priorities to mine. They can be hard to find but they are out there. One reason for starting (or joining) a local BS + Beer group is to build a network of building professionals who want to do better work.
To Mike's point,
My wallet reminds me that most home buyers don't care about the issues GBA readers obsess over. To be fair, few people have lived in a well insulated and properly conditioned house. They have no frame of reference for valuing the things that GBA routinely recommends. It doesn't help that few people stay in a home for five or six years.
As much as people hate mandates, I think that's the best way to ensure that homes deliver something like a pretty good level of performance.
[It doesn't help that few people stay in a home for five or six years.]
- Yep. Seems that until it's a "forever home" it's all about minimum investment for maximum return.
John,
It would be interesting to see how long "forever" owners stay in their homes compared to average buyers. FWIW. I'm currently planning my third forever home. ;-)
Michael,
Thank you for fighting the good fight. This community is great. I always appreciate your thoughts
I will say I have met some builders who are starting to get it. For example, I recently met one who is very much on board with rain screen, importance of air sealing, blower door scores. He’s even using aero barrier to bring his blower door score down as low as possible.
But his roof detail was zip r3/r6 and 8 inches of open cell spray foam. Which comes out to r36. Aside from not meeting r49 code, he’s using open cell spray foam underneath the roof, risking sheathing moisture. He countered by saying they have a great ERV and whole house dehumidifier, which seriously mitigates the risk of moisture and wet sheathing. I sort of see his point but think, wouldn’t it just be easier to NOT use open cell? Don’t even get me started on his use of open cell on the wall cavities.
Eagleeyshawk, thanks and you're welcome. It is exciting to see good building science practices spreading.
It is unfortunate that even for a builder so close to doing everything right that they skimped on roof insulation, and used open cell at that. If they had just bumped up the exterior insulation to R-15 they would have a safe assembly, if not a low-carbon one. Even if they dehumidify the air to 30% at 70°F, which is pretty dry, it will condense on a 37° surface. Assuming R-6 exterior insulation, using a dewpoint calculation (more theoretical than accurate, but still useful) if it's 27° or less outside there would be condensation at the interior face of the Zip insulation.
He also offered that zip r is polyiso, essentially closed cell. But according to Martin if you are employing flash and batt in roof deck with closed cell in climate zone 4, you have to use Atleast r15 of polyiso. So still risky.
With using open cell in roof deck, I think there are two factors here.
First, it’s easier for the GC. Their familiarity with a product and being able to verify that it’s done is important. Most think this is good air sealing as well. Unfortunately he’s still below code.
Second is less generous. Spray costs more. From a cost plus 20% model, it pays to use spray foam instead of fiberglass, cellulose etc.
Zip-R insulation is indeed polyiso, which has a composition and properties similar to closed cell spray foam, just with a different blowing agent. At only an inch or two thick it will allow some water vapor to pass. The facing is glass fiber fabric which allows vapor to pass as well. The Zip coating is vapor-open, which leaves the OSB itself as the most vapor-closed part of the assembly unless it's saturated. The fact that it's closed cell doesn't help much--the dewpoint will occur within the open cell foam, not in the closed cell portion. And the fact that it's somewhat vapor-open doesn't help either, because it means that when it's colder outside than inside, vapor will keep pushing through the foam until it reaches the OSB and can't go any further because roofing is vapor-closed.
I don't believe the Zip-R sheathing system is approved to be nailed to the framing roof members; only for walls. For roof sheathing, they offer the 7/16" Sheathing, 4' × 8', 1/2" Sheathing, 4' × 8' and 5/8" Sheathing. 4' x 8'.
Interesting point Armando. I’ll have to take a deeper look into this off label use.
When factoring in costs keep in mind that in many cases that extra cost is being financed, which means it'll be compounded.
Big difference between paying for something that's $x vs something that's financed at $x. The later might also be more difficult to achieve due to funders' constraints.
I am shooting for a self-build at a given total cost that's based more or less on self-financing. In the long-run I figure I'll eclipse this amount as I stretch out some of the costs by deferring purchases (holding off finishing things like flooring): hoping that future money will be available; ensuring, however, that I have the basic needs met up-front will mean that should I fail at obtaining funds for such finishing I will still be OK. Sometimes placeholders are beneficial (as long as they don't compromise integrity of the building).
I'll be pricing out everything as detailed as I can in hopes of having a target that doesn't end up drifted far from shore.
At the current trend of rising lumber cost, maybe ICF walls will be lower cost.
For basic structure of the walls, perhaps, but then there's the associated sidings, general detailing of openings (windows, doors etc.), and there's the roof structure. I am working up some costs for a build, and while lumber for framing has a significant number to it I'm not seeing that it's enough to warrant trying to save costs here (and, perhaps, shift them to something else). Without identifying all other parts of the build it's kind of hard to say what the actual costs will be for any given part. Well, that's what my head is telling me, and It's been known to be wrong...
paul
I am late to this discussion, but I can add some actual numbers. I built a house in Lynchburg, VA, 2018-19. It was ZERH certified. I drafted a ppt on the project:
(https://drive.google.com/file/d/1HXfVqxz_x7tT6E72TcqnedwaLfDr11g4/view?usp=sharing).
If you look at slides 42 and 43 in the ppt, you can see a breakdown of the square footage and the cost. The cost worked out to $162 per square foot of conditioned and finished space - that's for for the structure alone. But the site, sitework, and landscaping added another $80 per square foot, so the total would be $242 per square foot of conditioned space. The photos will give you a feel for how much you get for the money.
I have another draft ppt on ZERH details (since I am an academic, I write up everything). If you are interested, let me know and I will post it.
Mark,
I've had "A Pattern Language" sitting on my desk for a few months and have barely made a dent in its 1,100-plus pages. So thanks for putting the key points into your PPT. I'd like to read the ZERH details as well if you can post the link.
I am very excited about this book. Turns out I can get through out interloan system. My "progressive, Prairie loving town doesn't have it, but the working class town next door does.
Not at all related to this but I saw somewhere that this book is loved by software developers, anyone have a clue why or to the history of that?
John
I am a huge fan of Christopher Alexander and Pattern Language! I have an old ppt, from my first house in 1998, that tells how I used it to design my New Hampshire house.
If you are interested to discuss PL, perhaps we should start another thread, on Pattern Language, rather than hijacking Paul's thread on costs. (I am not sure of the netiquette here.) Let me know . . .
Sure, Steve, here is a link to the "Energy Efficiency" ppt. The first 20 or so slides are an intro for a general audience, then I start talking about my own design experience. (I am a former petroleum engineer, but when it comes to residential construction I am basically an amateur designer.)
These ppts are both still very rough drafts. I plan to clean them up and then present to a general audience. If you have any ideas or suggestions, please do email me at [email protected].
https://drive.google.com/file/d/1GbzOr0ZpRcb63CZRoCf_XkiNBktWZsVq/view?usp=sharing
Unless someone takes a full set of drawings, with a full set of specifications, and distributes it in 50 different markets, its impossible to know cost from one place to another. Even with my set of plans and specs, we get price range differences of 5%. Without a full set of plans and specs, it can be as much as 25%.
In the past, we've had plans and specs cost estimated by professional estimating companies, and even them can agree on the same price. That's why they call them ESTIMATES!
Anyone trying to get cost estimates, really needs to do the homework, in their market. There is no shortcuts, or you'll be risking big surprises if not done right.
That's advised learned in 35+ years of doing custom design and build, over 500-600 jobs, in about 16 states.
Thanks I completely agree. I still think it is a worthy effort. I get that you don't want people to shop on price. Nothing is that simple and those are not the customers you want.
In my world we have tons 6/12 roofs. I've done three, and differences between them on cost can easy be explained by size height and complexity. On the one there was a question about decking and whether it was ply or board sheathing and that was bid separately.
On GBA I think the readers can understand those differences.
I I were to do any of these jobs again, much thanks to you all, I add to what I wanted my roofer to do. In that mix Zip over std OSB, Insulation with strapping, taped seems. If I add insulation updating the decorative details to account for the additional 4,5,6 inches that gets added.
So yes there is variance and there is variance by region, and in my land of historic houses some projects might become horribly complex, but all that said we should be able to do this.
If we really believe in climate change, and we really believe the time lines, we need to justify the added expense that all of these things call for. In other countries, mostly in Europe, this is widely recognized and structures are put in place to enable home owners to make good decisions that reflect the impact that the work will have.
I would highly recommend starting with checking what incentives your area provides. My state has fairly generous incentives for insulation/hvac/ventillation, to the tune of ~5k for PGH levels. The people involved in this program may have good leads on good contractors to work with in your area. I would add that you should be skeptical of any time or cost quotes until they are set into a contract, and even then don't have much hope of seeing any contingency back. This is especially true if costs continue to rise in the current crazy building climate. Like others mentioned, I often wonder about the %2-5 I keep seeing, as it is often mentioned in relation to very high end homes or some sort of energy program / habitat. Having a custom home builder alone will be a lot higher than a tract builder, and I would guess that starting with a builder versed in energy efficiency already starts at a premium. For walls alone for instance, adding exterior foam costs $1-2/sqft in labor and then ~$2/sqft for materials (of course depending on type and depth). For a smallish ~2000sqft house you're looking at around 2500sqft of wall surface, so that one detail is about 10k. Then an ERV adds about $7k (based on quotes in my area). Then roof and air sealing details... you can at least establish a rough baseline.
Thanks Carson B,
I will (re)check on Illinois. but most of the incentives are really for specific things, like replacing your AC with a heat pump. Nothing that looks comprehensively at energy reduction. We do have LIHEAP programs. I'd like to see incentives first at checking airtightness, when three things happen, roof replacement, and cladding replacement, those can be be readily predicted, especially that latter, and then exterior remediation of water infiltration in basements. I hesitate to call it sealing, as sealing doesn't really solve the problem and only looks at one aspect of the problem.
Thanks for the tip
Deleted
That sounds like a sweet deal you've got there for a pretty good house.
Deleted
Deleted
Your dream project sounds exciting! The cost per square foot can vary greatly depending on location, materials, and labor. While $150/sq ft can be reasonable in some areas, it's good to stay updated on current material costs, which can fluctuate. You could also use Grupo EcoQuintas services from https://grupoecoquintas.com/ for that. Good luck!