R-50 wall construction: Double 2×4 stud vs. single 2×6 with exterior XPS
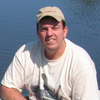
Are there any good reports using actual construction experience comparisons for the cost to build double stud 2×4 (or 2×6) walls compared to single 2×6 with exterior insulation?
Also, most of the articles I’ve read regarding double 2×4 walls use 24″ OC. I would think for the minimal cost difference to stay 16″ OC you get better drywall finish, and shear wall capacity for 2 storey construction.
Wondering if there is a recent (within the last 2-3 years) comprehensive report that has evaluated material costs, construction labor, advantages/disadvantages, etc. of all of these factors.
GBA Detail Library
A collection of one thousand construction details organized by climate and house part
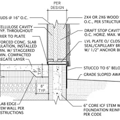
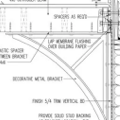
Replies
To hit R50 whole-wall (or even center-cavity) with 2x6 + exterior foam takes a LOT of foam- about 6", which is awkward to do for a wall (if still within reason on a roof.) A double studwall is far more practical, since the distance between walls is flexible- two feet thick isn't substantially more difficult than a foot. You have to pay attention to the thermal bridging of the subfloors & band joists, etc, and dense packing celluose gets harder, making fiberglass (which unlike cellulose won't sag or settle if you don't quite hit the target density) perhaps a better option.
For comparative ease of construction & moisture aspects of different high-R walls, see this document (even though it's not in the past 2-3 years it's really quite good):
https://buildingscience.com/sites/default/files/migrate/pdf/BA-0903_High-R_Value_Walls_Case_Study_rev_2014.pdf
Thanks.
That brings to mind another question. Are there any "super high" R-value insulation materials that are being worked on for construction purposes? For example, materials that are R-10 or R-20 per inch. Maybe Silica Aerogels?
Aerogel is ridiculously expensive, and would be totally wasted as cavity fill, but there are commercial products designed for framing edge strips, the primary market being commercial construction with steel-stud curtain walls. eg: http://www.thermablok.com/
The other somewhat viable use for aerogel is for skylights & daylighting clerestories, etc. Wasco offers aerogel insulated daylighting products for both commercial & residential applications, and there are a few others. One nice feature about aerogel daylighing is that it softens shadows and scatters the light considerably, but it's still possible to view (in soft focus) at least some of what is on the other side.
It comes down to builder preference. The ones who prefer double stud walls and don't like working with foam say that double stud walls are the best value, and that installing exterior foam is difficult. The ones who like using foam say that double stud walls are twice the labor and twice the material, and that installing exterior foam is not a big deal. I've had this conversation with many different builders and most of them fall into one camp or the other.
In my experience, if you only want somewhat high performance, say in the R-30 range, exterior foam of some sort is going to be the best value. If you want R-40 or higher, use a double stud wall, where the cost difference between an 8" thick wall and an 18" thick wall is mostly just the cost of the extra insulation. But there are many variables in the equation so the answer will depend on your specific situation.
There are super high-R materials but they are expensive and construction is extremely cost-sensitive as it is.
I agree that 16" o.c. stud walls don't use a significant amount of material more than 24" o.c. walls, in most cases, but they do use more material, and the extra studs don't contribute greatly to the building's ability to withstand design loads, so again it comes down to builder preference, at least for one- and two-story buildings. (When you get to 3 stories, the IRC requires 16" o.c. studs.)
I have a feeling substantial price differences between the different insulation types has a big influence.
I just ran some numbers on the cost of insulation material only, and without getting into any volume discounts, to get theoretical R-50 in each of these insulation types currently costs:
1.) Rockwool (12" thick) = $2.05 /sq.ft.wall area (US$)
2.) EPS (13" thick) = $3.59 /sq.ft.wall area (US$)
3.) XPS 25 psi (10" thick) = $5.47 /sq.ft.wall area (US$)
XPS is 2-1/2 times the cost of Rockwool. Wow.
I think Rockwool is almost 2.5x the price of cellulose (say $.88).
Can I ask the big question? Why R50?
Given the current prices of fuel, materials and labor in most places an R50 wall is unlikely justify its cost in terms of dollars and cents.
If you have some other goal like Passive house X number BTU per square foot regardless of cost then R50 may make sense. Perhaps you live someplace fuel is much more expensive than is normal.
If you are interested in balancing cost and performance spend some time with a no cost computer program BEopt. It models your home with your local weather, different insulation levels and their costs and fuel options adjusted for inflation over the life of the building. Expect to invest more than 20 hours.
https://beopt.nrel.gov/
Walta
R-50 walls, R-100 ceiling, etc. will save about $500/yr. in HVAC utility costs. But I will also save $20,000 CD$ in HVAC mechanical systems. So if we look at it simply (no interest, etc.) over 15 years I should save at least $25,000.
Additional costs to super-insulate and seal a 2,200 sq.ft. house will be approx. $35,000 CD$. I can live with the extra cost for better comfort, quieter house, and being green (never thought I'd hear myself say that, lol).
I'd like to see further details on upgraded insulation saving $20K in HVAC. And quantification of comfort improvements going from well-built current code to super-insulated.
As a general statement, I'd say the opposite. More HVAC capacity makes little difference in price and once you have a well sealed/insulated building, going to "super" makes imperceptible differences in comfort.
I would like to see those details too.
Where is this house going to be located?
At R30+ whole-wall R the cost difference between R30 vs. R50 whole-walls or an R50 vs. R100 in the attic is often better spent on upgrading/fine-tuning the window options. Walter's recommendation for maintaining a BeOpt simulation as you adjust the design features is a good one. In most climates the heating & cooling loads can be cut to the level where point source heating/cooling can work without taking it to R50 whole-wall/R100 attic.
Take a look at Table 2 in this document:
https://buildingscience.com/sites/default/files/migrate/pdf/BA-1005_High%20R-Value_Walls_Case_Study.pdf
While those "whole assembly R" values were estimates of the limits of financial rationality, in a reasonably optimized house design those are sufficient for Net Zero Energy with a PV array that still fits on the house, and could be heated with a few mini-splits (or maybe just one.) The only US climate zone that calls for an R50 whole-wall R and R100 attic is zone 8- the interior of Alaska. There are existence proofs of PassiveHouse designs in climate zones 6 & 7 that still make it, even at lower wall & roof R that R50/R100. But with the wrong windows (or too much window) it could still miss the mark by quite a bit even in zone 5 at those values.
If the plan is to save HVAC cost by going to single source heating/cooling, expect a noticeable decrease in comfort.
The floor plan hasn't been finalized, but I've run rough numbers with simulated buildings to get a feel for the effects. I believe in iterative design, whether it's software, or well designed houses. Once the floor plan is finalized I will certainly run all of the necessary calculations and play with variations of window quality, etc. - which may in fact lead to some changes. But to me it's a circular process, and there's no harm setting some targets and working towards them - even if once in a while you have to back track.
My design criteria in this location: Zone 7A, HDD(F65) = 10,000, Design Temp. Jan.= -20F, July= 82F Dry, 72F Wet. Snow load is 75 psf. There are no utilities available other than electricity. No gas, no water, no sewers, and it gets damn cold for 6 months solid. Propane can be delivered but it's costly, and why rough in another set of lines when I can see electricity really is the future.
I've narrowed it down to essentially a 2 storey house, 2200-2300 sq.ft. if you count the bottom level, 1/2 of bottom level will be walkout basement, on the shores of a windy lake. To minimize construction costs ideally I would stick to a cube with a gable roof. I'm all about simplicity these days, but I would also like it to be aesthetically pleasing as well as functional, so the design and roof lines haven't been finalized yet either.
I wasn't clear, but I'm comparing R-50 "super-insulated, super tight" against the standard that most decent homes would be built to in this area today which is about R-24 walls, ACH50= 3.0, etc. This happens to be about the quality my current home was built to 20 years ago, so I use electrical and utility useage from that house to make some of my comparisons. Will it end up being R-35 or R40 instead of R-50 - maybe, but it will certainly be far more insulated than R24.
I've concluded I will do a separate air source heat pump for each floor of the building and eliminate all of the traditional HVAC ducting. This building will be a relatively simple shape so I probably won't need multiple heads per unit. Backup heat will be electric resistance heaters of some sort, or possibly a fireplace for nostalgic reasons. I've also concluded I will put in the best air circulation (HRV/ERV) system possible with as much control possible room by room. Windows will be very good tilt and turn, and possibly extremely good. They will be fiberglass or vinyl, definitely not wood. Triple pane or quad pane European R10+ I'm not sure yet, because I don't have a good handle on cost comparisons yet. And I need to take another close look at the report from the engineer in Manitoba about not getting much benefit from extreme high quality windows. Floor joists will be truss joists so we can route HRV ducting and plumbing more easily. Definitely 9' ceilings on both floors for comfort and natural light. I lean toward 2x6 walls with Rockwool, plus 4" of XPS on the outside, but as per this thread I'm open to the idea of double 2x4 walls.
Why not PolyIso? The dramatically reduced R-values at colder temperatures, and from what I recall I think there are a lot more environmental concerns with PolyIso. Cellulose is cheap yes, but I'm not thrilled with it's fire properties or the fact that it will probably settle in walls.
going to the higher insulation is more a matter of selling comfort to the end buyer. If you are trying to sell energy .. you are playing Don Quixote
T. Barker,
1. You wrote, "R-50 walls, R-100 ceiling, etc. will save about $500/yr. in HVAC utility costs. But I will also save $20,000 CD$ in HVAC mechanical systems." Compared to what? Clearly, not compared to an R-40 wall. So what are you comparing the R-50 wall to? It's hard to justify the cost of an R-50 wall compared to an R-35 or R-40 wall.
2. No one has mentioned it yet, so I will: If you end up with 2x6 walls, why are you choosing XPS for exterior rigid foam? Most green builders prefer EPS or polyiso. For more information on these issues, see these two articles:
"Choosing Rigid Foam"
"How to Design a Wall"
Even new polyiso & EPS has an environmental footprint. Go with used stuff if you can- its out there. Large industrial & commercial flat roofs are usually insulated with polyiso or EPS, which is often swapped out & upgraded during re-roofing. The used foam is "gold" for materials reclaimers- they make a good margin even when reselling it at less than 1/3 the price of virgin-stock foam.
A 2x6/R20 wall with 3" of reclaimed roofing polyiso comes in north of R30 whole-wall. With U0.20 windows tuned for SHGC by cardinal orientation shading factors, with a bit of care that's good enough for point-source heating in US zone 5. On a deep energy retrofit on an antique 2x4 framed house I worked on in zone 5 they went with 3" of used foam + 1" of foil faced, and VERY comfortably heat/cool the 3 story house with 1 mini-split per floor. The project savings on the foam-over by predominantly usting reclaimed foam was well north of $10K. The only XPS in that house went under the basement slab (but it could have been EPS.)
The set of assumes that could justify an R50 wall in terms of dollars and cents would sound very strange to most of us today. With that said most prediction are worth less than the paper that are written on.
For me R26 wall is what made sense.
You may want to read Martins articles about “The Pretty Good House” with the understanding fuel prices were on a very different curve 6 years ago.
https://www.greenbuildingadvisor.com/article/the-pretty-good-house
Walta
Am thinking you are the lowest cost builder on the block.. Nothing wrong with that.. This is the market you aim for and likely the largest one on the block. Adding insulation as you know is a different animal. This is the creature comfort market. R 26 is just get a roof over head and call it good. Insulation lets you down size to mini split heat pumps which can shave Thousands compared to ducted systems. Like anything it becomes a balancing act. Getting to near net zero or net zero ready can be done for just around the same cost as many houses on the market. Sad to say most consumers are not very savey and they just buy what they have always bought. Know your market segment allows one to keep building
Just to focus the discussion a bit, T. Barker is planning to build in Northern Ontario on the North Shore of Lake Superior.
"Why not PolyIso? The dramatically reduced R-values at colder temperatures, and from what I recall I think there are a lot more environmental concerns with PolyIso. Cellulose is cheap yes, but I'm not thrilled with it's fire properties or the fact that it will probably settle in walls."
The reduction in R-values of polyiso at low temperatures probably isn't nearly what you think it is, and with Dow Thermax polyiso there is no derating at all. At a mean temp through the foam layer of -20C even the worst 2lb roofing polyiso is still delivering more than R4/inch. That's mean temp, not the outdoor temp. When the "warm" side is +20C it has to be -60C for the mean temp to be that low. When the warm side of the layer is 0C it has to be -20C.
If that isn't sufficient performace for you, go with EPS. The ~15% performance boost XPS has over EPS is temporary. Over the lifecycle of a house XPS will evenetually hit the same performance as EPS.
For fat double stud walls & Larson trusses cellulose can have settling issues if not installed by a true expert. If local expertise for dense packing cellulose in thick walls is lacking, dense packed fiberglass will never settle even if the density doesn't quite hit the intended target density. While it's air-retardency isn't quite as good as cellulose until it hits 1.5lbs per cubic foot, it's R value will be higher. A standard dense packing density is 1.8lbs, 2.2 lbs is also pretty standard. In a fat wall if you target 2.2lbs there may be spots that don't quite get there, but it'll all be over 1.5lbs density. Even targeting 1.8lbs with a few spots that come in shy of 1.5lbs is good enough.
In zone 7A air source heat pumps may not be your best option. What is your 99% outside design temperature? Thunder Bay's is -28C/-18F which is only SLIGHTLY cooler than the lowest temperature with a specified capacity for Fujitsu's cold climate mini-splits, but within the extended temperature capacity charts for some Gree units. Mitsubishi's cold climate mini-splits can go into an automatic shutdown at temps that warm, according to the fine-print on the submittal sheets, but they automatically re-start when it warms up to -25C. If your 99% design temp is cooler than -35C it's worth considering some electric resistance heat for backup, and for keeping rooms doored-off from the mini-split from getting too cold.