Raised Platform Passive House Detail

Wanted to get some feedback on a detail for a passive house in CO raised up on piers and timber support beams. Attached is the detail showing the proposed solution of wrapping the entire box in rigid and a vapor control layer and pouring an interior slab with radiant heat to heat the home. Any red flags you see with this detail?
Feedback is greatly appreciated!
GBA Detail Library
A collection of one thousand construction details organized by climate and house part
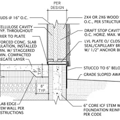
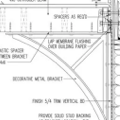
Replies
Kyle,
I anticipate that some will question the need for in-floor heat if you are building to the passive house standard.
What is the climate zone for your build?
Climate zone 6B on the edge of 7. I talked to a structural engineer and he mentioned the possibility of the wall crushing the rigid insul. Attached is a modified detail, moving the control layer under the floor structure
Kyle,
The second detail is a lot better. It also allows the wall sheathing to tie into the floor system for shear.
If the control layer is outside the 2"x6" wall, and there is that much exterior insulation, are you sure the service cavity serves any real purpose? They are usually used to limit the openings in air-barriers, and at 1 1/2" not much will fit in there. Interior strapping also complicates framing the intersections of interior and exterior walls and inside corners. My own feeling is service cavities should be targeted to address specific areas where running services is difficult. Used on all exterior walls, they rarely make sense.
I don't think the spray foam over the beam is doing much for you. As others have mentioned, a radiant heated concrete floor has no place in a Passive House. I agree with your structural engineer that your first detail puts too much load on the foam, but the revised detail should work.
The radiant floor heating is more of a backup and request by the homeowner.
Kyle,
Is the homeowner using a stove as the primary source of heat? If so a minisplit or PTAC is likely to be a much more affordable backup (and provide AC).
A concrete slab is unnecessary, will make the house less comfortable, and is environmentally insensitive.
When radiant floor heat first came along 30 years ago, early proponents believed that "thermal mass" made it work better. They talked about floors where it took days for the temperature to stabilize like it was a good thing. It turns out that what you want in your floor is high thermal conductivity, so that the surface is at an even temperature. And concrete has high conductivity. But you actually want the floor to respond quickly to inputs of heat so that the heating system can respond quickly when weather conditions change. A slab that takes two days to get to temperature is going to be producing what was needed two days ago. If you look at modern systems like WarmBoard, they promote fast response as a selling point. You're much better off using WarmBoard or putting together a floor using aluminum plates and plywood.
Concrete is also uncomfortable as a floor, it's hard on feet, knees and backs. Even a tile floor over a wood floor has a little more give to it.
Producing concrete releases large quantities of greenhouse gases into the environment. While it has a place, using it where it is not necessary is irresponsible.
Agreed--I think the concrete floor is a bigger mistake than the radiant floor, which does not harm other than being an unnecessary cost, and it actually a good way to utilize the output of an air-to water heat pump. In addition to the drawbacks of concrete that you mentioned, it adds significant extra weight that you need to support in the structure underneath.
I'm curious about construction sequencing. The second detail definitely helps things but I still think a lot of work has to take place from underneath the floor after the roof is on and the structure is dried in, including batts, sheathing, airsealing tape and/or membrane, then foam and rodent protection. Make sure to leave enough space for this work to occur or compromises will be made on site.. The spray foam appears to be needed before the subfloor is installed, so that will delay framing of exterior walls...and I'm not sure it can be installed in an airtight fashion as configured. I would skip the spray foam and opt instead for a roll of membrane laid over that timber that could later be taped to the bottom sheathing.
Consider polyisocyanurate in lieu of XPS for similar cost, performance and much lower environmental impact. Also if the client insists on in-floor radiant you could use 1 1/2" gypsum self-leveling underlayment to encase the pex tubing instead of a thicker heavier concrete slab, unless that's the preferred floor finish.
Jason,
My experience has been that any structures larger than say 200 sf. built on piers, are enormously more labour intensive and difficult than they would have been placed on a full foundation or slab.
Seems like it! whew.
And all to pour a slab anyway... Doesn't seem worth it unless the site dictates this approach.
Yes, the whole reason I find piers interesting is the potential to avoid concrete and perhaps also foam.
Jason, there's some good news about XPS. As of Jan. 1, Owens Corning will be selling XPS that has GWP down to 5% of standard XPS, available throughout North America, and Dupont will start having limited availability of foam that's about that good or better. More details in comment #18 on this page: https://www.greenbuildingadvisor.com/article/insulation-makers-win-epa-reprieve. Still not clear why you'd choose XPS when EPS is cheaper per R-value, and polyiso has higher R-per-inch if that's your goal, but at least there's a reasonable XPS option about to be available for those who are willing to make sure they buy the right stuff.
Reclaimed foam is likely to be the cheapest and most environmentally positive option.
Charlie, don't get too excited about the new XPS--it's still orders of magnitude worse than EPS or polyiso on an R-value basis.
How is your structural engineer dealing with the piers and lateral wind loads? Or earthquake lateral loads? do you have a xx ft stem wall on each wall line? then piers for the rest.
Also seems like your under floor foam needs a critter shield - and a fire restive layer - the foam would be good kindling fire starter to get the house ablaze. Perhaps Mineral Wool is the right material for under the joists.