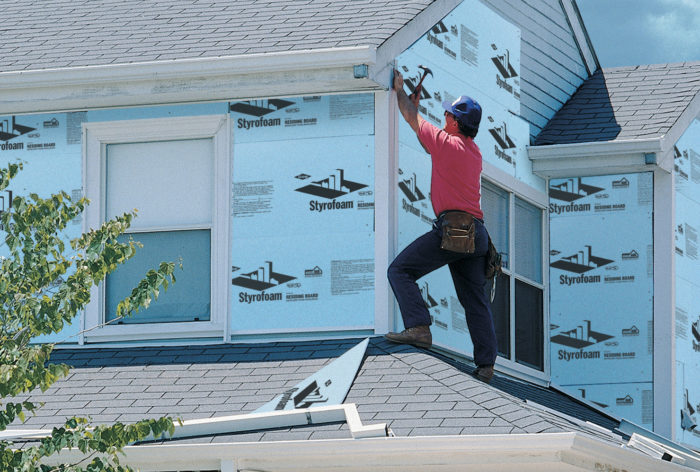
Six months before its scheduled phase-out, a chemical used to manufacture extruded polystyrene (XPS) insulation is getting the green light for continued use from the U.S. Environmental Protection Agency (EPA).
The EPA has proposed a new rule that would allow the insulation industry to continue using a hydrofluorocarbon blowing agent called HFC-134a in combination with other compounds to make XPS. That practice was to have ended on January 1, 2021 under terms of an EPA rule dating to 2015 as the government looked for ways to reduce the global warming potental (GWP) of the insulation. HFC-134a has a GWP of 1,430 (compared to the GWP of carbon dioxide, which is 1).
In a proposed rule posted by the EPA on June 12, manufacturers would be allowed to continue using the chemical for making insulation, but only as part of specific blends with other compounds. The blends were suggested by DuPont, one of three U.S. manufacturers of XPS.
The proposed blends would cut the global warming potential substantially, but still leave it hundreds of times higher than a complete conversion to a hydrofluoroolefin (HFO) blowing agent or C02. Manufacturers say a total switch to an HFO, with GWPs in the 1-to-6 range, isn’t practical.
Some green builders avoid XPS because of the high GWP of the blowing agent, the compound that creates tiny air or gas bubbles that slow the transfer of heat through the foam. Instead, they prefer expanded polystyrene (EPS) because its blowing agent, pentane, has a GWP of 7. XPS, however, has a higher R-value than EPS, R-5 per inch vs. R-3.6 to R-4.2 per inch (depending on its density, with some graphite-infused versions going to 4.7).
DuPont markets XPS under the Styrofoam trade name. Other manufacturers include Kingspan, a multinational based in Ireland, and Owens-Corning.
The proposed rule (Proposed Rule 23) was made under a program called Significant New Alternatives Policy, or SNAP, part of the Clean Air Act that gives the EPA authority to review substitutes for existing products and compare their relative risks. HFC-134a and HFC blends became widely used in XPS after 2010, according to the EPA’s docket. But in 2015, the EPA changed the status of certain HFCs used in XPS, including HFC 134a, from “acceptable” to “unacceptable.” That change was scheduled to take effect on January 1, 2021.
Now, EPA plans to list as “acceptable” three blends that contain 134a, thereby accepting DuPont’s claim that over a period of five years and hundreds of trials it had not been able to hit R-value targets with alternatives that included HFO-1234ze, HFC-152a, and C02.”Further,” the EPA wrote, “the submitter indicated that if in some cases it could meet R-value requirements with those neat blowing agents, these alternatives were not able to meet other requirements such as compressive strength, density and thickness, or fire test results.”
The XPS blends, containing up to 52% of HFC-134a, would have GWPs of 580 to 750.
Comments on the new rule will be taken until July 27.
Technical hurdles remain
One industry insider complained privately that European producers of XPS have been able to switch from HFC-134a to something else while producers in the U.S. say it can’t be done. (European versions are blown with C02 but have an R-value of about 4 per inch). And even though the blends cut the global warming potential by as much as 59% when compared to 134a alone, the person said, new blends do not eliminate it.
“They’re watering the whisky down, but there’s still whisky in the water,” they said.
DuPont said through a spokeswoman that it has been unable to find a “technically viable, cost-effective alternative” despite seven years of R&D.
“The blend alternatives that we proposed, and that were ultimately published in the Proposed Rule 23, offer the whole XPS market the opportunity to continue our HFC Phase-Down program, which is more aggressive than the Kigali Amendment Schedule and supports DuPont’s commitment to the Paris Agreement,” the company’s statement reads.
DuPont says there is still no drop-in HFO replacement for 134a that would work for its entire product line. The company pointed to an EPA statement in which the agency said that only one of the substitutes it was counting on would in fact be available by 2021, and that it could be used for only part of the XPS foam market.
“As acknowledged by the EPA, it is not the intent of SNAP regulations to limit the market by picking winners and losers,” DuPont’s statement said. “DuPont has innovated and found success with a portion of the XPS category using a novel HFC-134a replacement and is working to implement those conversions as quickly as possible.”
The company said one technical issue was that HFO-1234ze, a possible replacement for 134a, can be flammable under conditions typical for extruding XPS, especially at higher humidity. In addition, the company had trouble meeting “density and physical property code requirements” for some end uses. “Additionally,” DuPont said, “under infrequent circumstances, there remains an increased risk of toxicity concerns with replacement technologies that must be addressed.”
Owens-Corning says it can meet deadline
While DuPont apparently couldn’t hit the January deadline to rid XPS of 134a, Owens-Corning says it could.
Frank O’Brien-Bernini, vice president and chief sustainability officer, said in a telephone call that Owens-Corning has been working on the problem on the assumption that the order would be imposed on its original timeline. “We are well prepared to respond,” he said.
Owens-Corning’s Foamular XPS has a GWP of roughly 750 now, but the company is prepared to get that number down to 150 or so, the practical effect of removing 134a from the mix and using another HFC blend.
O’Brien-Bernini said he was not prepared to discuss the specifics of any rollout schedule for new blowing agents. “We don’t disclose compositions and all that,” he said. “We do use HFCs. It’s well known in the industry that there is 134a, there is 152, there are different blends and everybody’s got their cocktails. We don’t specifically disclose what we use.”
However, he said, consumers can check the Environmental Product Declarations of a product to check the GWP of a product.
Although it’s possible to use C02 as a blowing agent, as is the case in Europe, it must be combined with another component—pentane or butane, for example—and that raises concerns over volatile organic compounds. But the lower R-value, which O’Brien-Bernini said is about 4.2 per inch in those forms of XPS, is a more critical factor, and Owens-Corning isn’t convinced that consumers would be willing to give up a higher R-value just to get the GWP down.
“We have not been interested, we do not believe the market is interested, in reducing the R-value of the product in order to use C02,” he said. “We have been working ever since the Montreal Protocol in 2010 but most especially the last five years or so to match the current performance expectations of XPS in the North American market while reducing the GWP, so doing both.”
He said the company didn’t object to the original SNAP rule and viewed the changes more in the context of its own sustainability goals than it did as an added regulatory burden. The company, he said, is committed to reducing greenhouse gases by 50% by 2030 from its 2018 baseline, and a “material part” of that strategy involves using foam blowing agents with a low GWP.
Kingspan had no immediate comments on the EPA rule.
Scott Gibson is a contributing writer at Green Building Advisor and Fine Homebuilding magazine.
Weekly Newsletter
Get building science and energy efficiency advice, plus special offers, in your inbox.
24 Comments
EPA: "You have seven years to change your formula in a meaningful way to help our planet.
Europe: "No Problem! We've eliminated 134a altogether. Problem solved. "
Owen's Corning: "We've successfully reduced the global warming potential to just 150 from over 1,000."
DuPont: "No Way, this is impossible!
EPA: "Oh no problem DuPont, sorry to inconvenience you... Can you please write the law to regulate yourself?" Sorry again!"
The EPA should consider changing its name.
Keep mind that although Europe "solved" the problem their solutions included a reduction in R-value.
Also Dupont didn't say that they don't have a solution, but that they don't have a cost effective solution.
BTW..what you're complaining about is called regulatory capture. Regulations include stakeholder inputs. This arrangement can lead to some severe distortions of the market because it can make it cost prohibitive for competitors to enter the marketplace.
John
I am familiar with the lower R value of XPS in Europe. American XPS becomes R4 at some point anyway, so this is a non-issue.
The original regulation was fair. The GWP of XPS is staggering and should be banned altogether. We can't rely on the market alone here as people have no idea that XPS is so damaging. Also, there are suitable alternatives out there such as EPS, so its not like this stuff is critical to society.
If DuPont doesn't have a cost effective solution then they shouldn't be allowed to sell the product. If a car company suddenly started offering cars achieving only 7 miles to the gallon then they wouldn't be allowed to enter the market.
Owen's Corning was able to arrive a formula with a lower GWP so they should reap the rewards. I'm sure DuPont is capable of coming up with something if they want to participate in the market. I'm all for companies making money. The more the better. What I'm "complaining about" is that the EPA is unwilling to inconvenience DuPont in order to meaningfully reduce the extreme GWP of XPS.
John,
" Dupont didn't say that they don't have a solution, but that they don't have a cost effective solution."
I'm confused. Are you saying that the EPA should subsidize Dupont by overruling the greater public good of eliminating the high AGW potential of Dupont's formulation of XPS because they can't compete against other manufacturers' low AGW formulation of XPS? That seems to be what you are saying.
I'm NOT saying the EPA should subsidize DuPont. I was just pointing out why.
There's a frustration with regulatory bodies and people with competing interests pine about how everything would be fine if only "the right people" were running the place.
Is is a never ending cycle of disappointment.
en.m.wikipedia.org/wiki/Regulatory_capture
>"Some green builders avoid XPS because of the high GWP of the blowing agent, the compound that creates tiny air or gas bubbles that slow the transfer of heat through the foam. Instead, they prefer expanded polystyrene (EPS) because its blowing agent, pentane, has a GWP of 7."
Not mentioned here, but most of that low GWP isopentane blowing agent leaves the foam whille still at the factory where it is recaptured, and NOT vented into the atmosphere.
Also not mentioned is that over a few decades as the R134a migrates out of the XPS, the performance drops toward that of EPS of the same density. Most vendors only warranty the performance to 90% of the labeled value (R4.5/inch) at 20 years. In 50 years it's more likely to be performing lower than that- roughly the same R4.2 /inch as EPS.
>"Keep mind that although Europe "solved" the problem their solutions included a reduction in R-value."
In the US the being able to label it at a higher R/inch is primarily marketing thing to somewhat rationalize the higher cost of XPS vs. EPS. It's both cheaper and greener to use CO2 or isopentane for blowing polystyrene than using an HFC or HFO soup for the marketing benefit.
Most XPS in Europe is blown with CO2 (strangely enough, with a CO2e footprint of 1.00 x CO2 :-) ). Unlike the HFC or HFO blown XPS, the labeled performance is stable over the decades, since the blowing agent doesn't give it a short term performance boost.
In my estimation the European solution truly solved the real problem, (no quotes needed.) It didn't solve the MARKETING problem, yet they still manage to sell XPS in Europe, presumably marketing it on it's other characteristics (lower vapor permeance, better dimensional stability, higher pressure ratings / less creepage than EPS at the same density, etc). That "...reduction in R-value...." is only relative to the labeled R, not the full lifecycle performance (unless the lifecycle is anticipated to be < 20 years).
Dana, I really appreciate your informed reply here. No mention here that the change we are observing in the EPA's decisions are a core change from its original reason for being, i.e. preserving the environment. The wacky philosophy of libertarianism espoused by Mr. Clark is that individual freedom is all that matters. It doesn't seem to matter that exercising of certain freedoms can affect a vast number of people in a negative way. That includes my ability to live comfortably in world free of pollution and global warming.
Your reply did a lot to lower my blood pressure. Thanks!
Eric,
The EPA's job is to determine the maximum level of poison which businesses and industry can hoist upon the people.
Never forget that.
Of course individual freedom , property rights and tort reform matter. Think of it like this. Would you mind if the EPA said it was okay for me to dump sewage on your yard because it was by their measure "just a little" ? Of course not, but there would be nothing you could do about it.
Well of course it's a marketing thing. I suspect the initial higher R-value is probably what makes it profitable to produce.
Owens-Corning said they've made it work but we know absolutely nothing about the performance of the product.
Maybe a few of need to start writing some product reviews for XPS foam and EPS foam at the major box stores?
I wonder if that might be an avenue to get some attention to this. It is at least a place that general consumers have a chance to see.
XPS is actually a nice product and worth a small premium in some applications, except for the global warming issue...
Here is one way to think about XPS:
You can add 2" of EPS to your 1600 square foot home (walls and slab) and then burn 3,900 gallons of gasoline in your yard just for the hell of it.
Or, you can use 2" of XPS instead.
The environmental impact is the exact same. Yea, XPS is that bad.
Source: https://www.buildinggreen.com/blog/global-warming-potential-insulation-materials-new-calculator
(deleted)
Can anyone tell me why XPS seem to be the top choice for builder? Except for the initial higher R-Value I don't see why?
- It's most expensive than EPS.
- Its production is far worst for the environment.
- The compression rate seems to be the same.
- Doesn't dry out very well compared to EPS.
- It loses almost half its R-Value when very wet.
Thanks,
Arnold
>"'Can anyone tell me why XPS seem to be the top choice for builder?"
It's mainly about marketing and ignorance. XPS is a bit more rugged in handling. There is a not well supported but widespread belief that it's a vastly superior product for ground contact applications than EPS, mostly driven by marketing, not data.
Contractors / architects / designers can also multiply inches x R5 in their heads easier than inches x R4.2. Code compliance is only about labeled-R, not the true lifecycle performance or warranteed performance (either of which is less spectacular than the labeled R.)
You know what, I didn't actually realize EPS was so much better wet until just now. XPS advertising uses short term water exposure testing, in which XPS appears superior. In long term testing EPS appears superior.
The only other difference seems to be that EPS is most commonly available in a lower compression strength version than commonly available XPS. This give the impression of a better product I guess, even though it is not needed in most applications. Otherwise all the differences are based on deceptive XPS marketing.
Interestingly, Home Depot doesn't even offer standard sheet EPS on their website at this point.
>"Interestingly, Home Depot doesn't even offer standard sheet EPS on their website at this point."
Box stores have generally only carried Type-I (1lbs nominal density EPS) with facers. But sheet EPS is widely available in 1.25lbs (Type VIII) density, commonly used in commercial roofing applications, and 1.5 lbs (the same density as most box store XPS) Type-II, which has a range of common uses.
Really sad to see this. I wrote that calculator - 10 years ago - over this very issue. If we still have a government in two months, maybe we'll see action on this. Obviously preservation of R per inch is not an argument that should hold any sway with the EPA.
This article is due for an update: Owens Corning has announced that they their new low-GWP XPS will be available throughout the US and Canada starting Jan 1.
Their current offering "Foamular" uses a mix of HFC blowing agents with a 100 year GWP "of less than 750." The new stuff is called "Foamular NGX", and is a mix of HFO and HFC blowing agents that has a 100 year GWP "of less than 80." That's 5.6% of the GWP of the traditionally used HFC blowing agent (1430). I'm not completely clear on whether that means that it will completely replace the old offerings or just start to be an option.
Meanwhile, DuPont has a new grey XPS that they stay will start to be phased in in regulated areas, Canada and states like CA and VT, Jan 1, 2021. It's kind of like Neopor, with carbon black making the cell walls opaque to radiation and increasing R-value to make up for the loss in R-value from the change in blowing agent. And it seems that they have a hydrocarbon blowing agent, based on detailed guidance on their web site about making sure that materials are stored and transported with sufficient ventilation to avoid flammable gas build-up. Probably more of a concern than with EPS because the lower permeability means it takes longer to dissipate.
https://www.energy-manager.ca/owens-corning-foamular-ngx-insulation/
https://www.owenscorning.com/en-us/insulation/products/foamular-250
https://beyondblue.dupont.com/
Annoyingly, I can't find anything about the new Dupont products on their regular website--only at the new "beyondblue" web site. I suspect they want to keep selling their stock of polluting blueboard without admitting that there's a problem with it. Whereas Owens Corning has it listed right up front on their regular web site.
Charlie, this is great to hear! Thanks for sharing. The more I learn about these two companies, the more admire Owens Corning. Dupont/Dow not so much...
Charlie,
Thanks for the update on Owens Corning and DuPont. We are working on an update that will be posted as a separate article.
Terrific, looking forward to it!
Anyone know how these GWP figures are calculated? Since climate scientists keep changing their estimates of ECS for CO2, wouldn't the GWP of other gases be dynamic? It would seem like we'd need calculators hooked into a feed that updated the estimates based on ongoing research. I doubt we'll have settled estimates before 2040 or so, assuming that estimates of the effects of single gases/variables in complex systems was even a valid possibility to begin with.
One issue with XPS is that its R-value isn't that much higher than EPS, though it might be a bigger difference than people realize. On GBA people often overstate the R-value of EPS as 4.2 or 4.0. Only higher-end, denser EPS versions deliver those levels. The standard cheap Type II EPS that most people use is around 3.8, maybe less.
For me the biggest value of XPS is its much greater compressive strength. Even at similar densities, it's much stronger than EPS. You can get it at 60 and 100 psi grades. But R-5 isn't impressive in a universe where polyiso, polyurethane, and phenolic Kooltherm exist (though if anyone has successfully bought a Kingspan product, or been able to even communicate with Kingspan, I've not heard about it).
BlueSolar, different densities and brands of EPS have different tested R-values. Different densities also have different compressive strengths. Type 2 EPS is rated for the same load as the blue or pink XPS most builders use, and the type I typically spec, Foam Control, is tested to perform at R-4.2 per inch, the same as aged XPS. The R-value of EPS does not change over time.
I don't know what you mean by "higher end," but the type 2 EPS I spec costs about the same, delivered, as XPS picked up locally. You can get both EPS and XPS in higher densities, with higher compressive loads. I've spec'd EPS with a 40 psi load rating, it wasn't hard to get, and I can't imagine needing foam with a higher compressive rating for regular use. I'll attach the spec sheet.
I have samples of Kooltherm's phenolic foam. I don't know why it hasn't made it to market yet, but it exists. In cold climates, aged a few years, polyiso is worth about R-5 to R-5.5. Closed cell foam is about the same.
I can't answer your question about how GWP values are calculated, but I trust that very smart, dedicated scientists put a lot of effort into it. I can appreciate that it's not an exact science, and that exact values are not important. It is abundantly clear that we need to do everything we can, as soon as possible. Suggesting that we should use climate-damaging products when perfectly equivalent products are available with greatly reduced impact because you don't know their precise impact on our climate does not seem very logical.
The GWP figures for other gases are calculated by looking at the absorption and emission spectra for solar and thermal radiation. From that, you can calculate the impact on the climate forcing coming from them and compare to the same for CO2. That doesn't involve climate modeling--only radiation heat transfer. If our estimate of the effect if CO2 is revised because of a more detailed climate model, all the rest of the impacts get revised right along with it.
The other factor, however, is how long-lived the different gases are in the atmosphere; with that factored in, the GWP for different time horizons is different. Looking at the 10 year or 25 year effect vs. the 100 year effect will change the numbers, but not enough to change the conclusion that current standard XPS is vastly worse than EPS.
Log in or create an account to post a comment.
Sign up Log in