Referral for Manual J & Radiant System Design – Thoughts on Arctic Heat Pumps
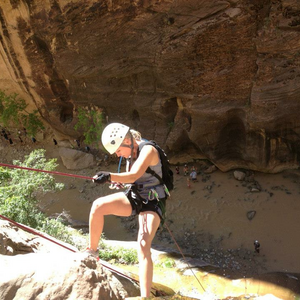
UPDATE: For future readers, Borst Engineering has agreed to run new manual J numbers and design our radiant system. Now to address my concrete slab concerns. It seems the magnesium concrete renaissance hasn’t hit Arizona yet.
Hey all,
Our J-calcs are way off (10 tons in 3400 s.f. living space) and we need someone who can do them accurately, but quickly. There are a few online services, but I don’t know who’s good and who to avoid.
Also, we’ve decided to run radiant heat in the slab and our prior designer, Rob Brown, isn’t doing system design anymore – neither is Morgan Audetat, who he recommended. I don’t think John Siegenthaler is still designing, either. We’ve ready to pull the trigger on an Arctic heat pump, who does their own design, but I’m wary of using the person selling the system to do the design.
Thoughts?
GBA Detail Library
A collection of one thousand construction details organized by climate and house part
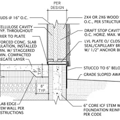
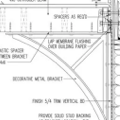
Replies
You could ask Corbett Lunsford, or one of his HVAC experts, Alex Meaney.
Manual J Deep Dive - Part 1
https://www.youtube.com/watch?v=LEKEMI05dJE
Manual S Deep Dive - Part 2
https://www.youtube.com/watch?v=LGhE4XwbDDE
Will check them out, thank you.
A couple of questions which may help others answer yours:
1. Is this an existing house you’re retrofitting or a new build? If the former, you can use methods such as https://www.greenbuildingadvisor.com/article/replacing-a-furnace-or-boiler
Basically, use the existing heating bill to determine heat load. I will caution that if you do this, programmed setbacks in temperature can make the heat load seem lower than what you’d get with a Manual J.
2. Do you have blower door test results? You’ll need this in any case to get an accurate heat load calculation otherwise you’ll be guessing a lot. Fortunately air infiltration has a limited effect on total heat load, but ymmv depending on age of your house.
Sorry, this is a new build so no prior numbers to reference and no blower door test yet (not yet framed). :)
http://www.energyvanguard.com
I have reached out to them but am trying to get it done quicker than they have time on their schedule.
I think you should give the smart people here a chance to talk you out of radiant in the slab.
A summary of the arguments:
* In a house built to modern standards the heating loads are so low that floor temperatures are so low they're barely noticeable.
* Even if you decide to go with heated floors, a concrete slab is a terrible way to do it.
We've installed radiant heat in three of the homes we've built or done full remodels on and lived in radiant heated homes ourselves for almost 20 years now. I understand the arguments against it - including the shoulder season responsiveness issues with in-slab piping - but I just really like radiant. I don't like the feel of hot air blowing around, I love the feeling of warm floors, and most importantly, we can do it ourselves. Working from professionally designed plans makes it pretty easy.
The home is in Arizona in zone 4B where it does snow a couple times a year - it's supposed to get down to 32 tonight. We're renting a place while we build, which has a conventional furnace. I keep getting a bloody nose and feel like I can't put on enough lotion. We've gotten bids of $40k and $53k for traditional HVAC. We can install a high quality low-temp heat pump heating and cooling system for about half that.
The winter dryness is caused by air leakage, not by the heating system.
I understand the appeal of floor heat, but I'd still like you to reconsider a concrete slab. If for no other reason than that concrete is the most environmentally destructive building material you can choose.
A low heat capacity floor will give better responsiveness. It's still something you can DIY.
And a slab is just a lousy surface for a house.
I tried to find a more environmentally friendly cement plant - offering magnesium cements for example - but they don't exist here. If I had this to do over again I would not have done a raised slab. It was one of those "this is how we do things here" moments from the designer and other builders I spoke with and we went along. Here in AZ they build with CMU stem walls filled inside with compacted AB - 800 tons later (not counting the exterior backfill), and it definitely would have been cheaper to just use BCI joists. Can't exactly go back now, though.
I did get a bid for warmboard - $9k+ just for the 1200 sf upstairs of our place. That alone would blow the budget without even considering using it over the slab. It may not be ideal, but under-slab it is. The crete heat foam we'll be mounting the pex to is paid for and will be delivered next week, so we're kinda committed. (Yes it was a splurge, but our backs aren't as inclined to endless wire tying like they were 13 years ago.) We plan to use in-slab sensors and will try to detail the system to control as many of the negatives of the slab as we can, but it is what it is at this point.
As an aside, I'm getting all kinds of weird outrage for things like the exterior insulation you see in this pic. They about lose their minds when I tell them we're doing 2" - 3" of exterior EPS on the whole house including the roof. The inspector thought I was nuts for installing a hard piped, perforated, french drain burrito instead of the corrugated black pipe with a sock. My guys told him not to start an argument about it unless he had a few hours to spare, lol. At least he passed us.
So you've already poured the slab and now you want to design the system? That's kind of backwards.
This is a last-minute change. We had been facing a deadline we're no longer facing so we've taken a pause to rethink a few things. We haven't poured the slab yet. We need the radiant system designed before we know the spacing and pex runs to put in it. We'll be ready to place the pex and pour the slab in a week or so after underground sub rough and interior footings are installed. My crew isn't thrilled about it, but we won't pour the slab until we have the design. We have 10 mil poly to prevent the fill from getting wet if it rains while we wait. I used to be more of a curmudgeon myself. It's a depressing path.
Delaying until you have a design is the right call.
I know there's a huge amount of pressure during construction to stay on the schedule. But there are details that you want to get right.
"Sin in haste, repent at leisure."
"Sin in haste, repent at leisure."
Couldn't agree more.
An air to water heat pump will always be more complicated than air to air, and that’s if you’re just using ductwork. Why would it be cheaper to use air to water with a radiant surface? I’m not opposed, just trying to understand.
Air to water you can DIY.
I'm not sure I can help here. I'm just basing this on the bids we've received for radiant vs. ducted HVAC. I don't trust the radiant designs provided by the usual DIY sites which is why I'm looking for a more experienced designer. All the systems we've installed before have used gas-fired, suitcase style boilers. The whole idea of a heat pump is new to us, but we're trying to get away from fossil fuels and our house is in sunny Arizona.
On one of the projects, the BOM cost of two ducted units, all ducts including custom plenum adapters was $4700. For anything radiant, that probably doesn't cover the cost of manifolds, thermostats, valves and fittings. Duct install is pretty easy as long as it is part of the original design process and proper chases are layed out.
A modulating heat pump is nothing like the furnaces of old, in a low load structure you barely notice that unit is even on. Until you experience it, it is hard to believe how comfortable and even the temperature is in a place like that.
You can still use resistance mat floor heat for things like entrance mudroom, kitchen and bathrooms. As long as the air source heat pumps is doing the bulk of the space heat, the operating cost of this is so small that anything hydronic the ROI is pretty much never.
One more thing, tight home needs mechanical ventilation. The minimum vent duct for a bedroom is 3", but you most likely want 4" to keep velocity and sound low. The heating duct (which can also be used to deliver fresh air) for a bedroom would be 5" so you are not saving any cost or ductwork.
If you can post the detailed Man J, we can take a look at where the issue is. 10 tons is silly.
I don't believe 10 tons is correct, which is why I'm looking for someone to do those calcs correctly and design an accurate system. There are plenty of forum posts where professionals comment about correcting systems designed by some of the big DIY sites. That said, they may not be way, way off since the view side back of the house (facing north/slightly east) is mostly big glass doors. Add to that a great room with 15' ceilings and radiant heat from the floor, instead of above, makes more sense.
Regarding your $4700 system, cost is highly dependent on where your job is. I've never paid more than about $15k for a whole house system in northern Utah, but the lowest quote here is over $40k. Everything costs more here (near Sedona, AZ). I've brought some materials from Utah and gone to Phoenix for others.
The roof trusses and mid-floor BCIs are designed/CNC'd for HVAC runs. We were thinking of switching to minisplits with ceiling cassettes, but therein lies the problem -- we need someone to think cohesively about the whole house, including ventilation as you note, rather than a jumble of single components.
Please post the FULL manual J, in a higher resolution, so we can read it (can't read any of the text as posted). We agree 10 tons is probably incorrect, but we are going to try to help you ID exactly why it is incorrect - ie which inputs are incorrect resulting in the wrong output.
Based on your plans, one thing that jumps out to me is the multi panel sliding glass doors. These are typically VERY leaky. Can you please also post both the spec for the airtightness of the doors and window, and the spec for the type of glass you are using.
Also, it is very hard to read due to low resolution, but those window sill details don't look correct. Read up about the red line test for air tightness.
I'm not sure how to make the resolution higher, but here's the pages of the manual J (I can only load 5 at a time so the rest are on another post). Hopefully you can read these.
The doors are Quaker Quartz CityLine Multislide doors with the energy max option. Quaker is a commercial door company who moved into residential. These have cardinal glass and a 1" thermal break. Details:
Zone 4B
Main floor = finished concrete floors
Upper floor = engineered white oak flooring
R10 under slab -- 2" crete heat with 10 mil vapor barrier, slab edge insulated
R10 foundation insulation -- 2" EPS continuous exterior to footing
R26 wall insulation (3" EPS continuous exterior + open-cell interior foam)
R50 roof insulation (3" EPS continuous exterior + open-cell interior foam)
R15 on structural frames of sliding glass doors
U .34 on Doors
U .27 on Sierra Pacific Windows - we've changed the front awning windows to fixed
- Garage will be radiant heat and insulated as part of the house but likely not part of main cooling system (isolated mini split at hobby area).
-Slab edge will be insulated at garage door opening using Energy Edge or similar detail.
- No ceiling cans, no skylights, minimal building envelope perforations
- Will be as airtight as we can make it
Many of the details in our plans are not the way we're actually building - we were rushing to get the permit and the designer scoffed at nearly everything we wanted to do differently - capillary breaks, under-slab insulation, full exterior insulation, flashing and window details, minimal perforations of the building thermal envelope, etc - so I just left his as drawn. He did think the Maine deck brackets I showed him were cool. This was a 1031 exchange with a 180-day valuation deadline of whatever was built by that date - we made it to footings. Now the rush is off. The inspector has been pretty good about approving as-builts when I've provided docs to support what we're doing. It's better than code anyway. We were the first to get Salt Lake City to accept Schluter rather than rubber pans so I'm used to raised eyebrows. There are a few builders here who do things better but not enough for the inspectors to be real familiar.
Here are the rest of the Manual J pages...
I’m not really seeing a compelling reason not to just run ductwork for this house, like almost all homes in America use. Ductless heads will be too inefficient, and you’ll need cooling with radiant either way.
@ Paul - you're not wrong. I don't know how the local contractors got to the $40k - $53k range for our system. I'm also trying to understand if and how a 60k btu-rated cold-weather heat pump could do everything including the radiant cooled floor, which has been suggested. It would still have additional air cooling, as I understand it, and I'm not sure what that entails. Would it need the full-sized supply & return ducts anyway? I'm just not sure.
Based on the Manual J you posted below (the thread has reached it's maximum reply level so replying here...) the Manual J was calculated based on simplified infiltration method with average construction quality.
First thing is to get that corrected...
Your square footage to cubic footage indicates the entire house is 10' ceilings.
There is nothing on what you posted that indicated the slab, wall and ceiling/roof construction type and insulation, and the fenestration, etc. Those are all inputs to a Manual J...
As other have said, need the detailed Man J to figure out if correct.
You have a pretty detailed HVAC design there already, it is mostly a question if the sizing and equipment is correct.
There are some seriously high CFM numbers on lot of the registers, which indicate some pretty high loads but hard to see if correct without the details.
One thing that jumps out to me is the spray foam. With exterior rigid, that open cell in the walls buys you nothing. I would swap that out for batt insulation, you'll end up with similar R value assemblies but much greener option without any of the potential (low but does happen) complications of a spray foam install gone bad. Batts will also cost significantly less money.
The one issue you'll have is any major changes now mean new drawings and permit updates. Sometimes this is not worth the cost and project delay, so I would focus on getting the right equipment in there instead of a major redesign.
@ Akos - It will definitely be a delay, but the county prioritizes supplementals and tries to get them back quickly. I just need to get the design with corrected Manual J in their hands. Still trying to find that person.
"* In a house built to modern standards the heating loads are so low that floor temperatures are so low they're barely noticeable."
That is not my experience. It's not "leaky Colorado mountain condo with radiant floors" noticeable, but it is certainly "pleasantly warm" noticeable. The effect is much greater for the slate floor areas, but still very much there in the areas with 3/4" oak. Water temps for our system max out at 100F and are typically 85-90F. All flooring is installed on top of Warm Board. I don't have any experience with in-slab or other high mass, low-temp radiant.
It's a peeve of my when people equate mass with heat capacity. I'm pretty sure you mean high heat capacity, not high mass.
I guess I should have used the more specific term "thermal mass" rather than assume the "thermal" part was implied by the context. My understanding is that this is the right term to describe the significant difference in heat-change inertia between slab based radiant and "low thermal mass" options such as radiator panels and Warm Board. https://en.wikipedia.org/wiki/Thermal_mass
"Thermal mass" is not a term used in physics or engineering, it's a term made up by architects. The property of matter you're talking about is properly called "heat capacity." There is no such thing as "heat-change inertia", that's more pseudoscience.
The reason I get pedantic about this is that words matter. People read about "thermal mass" and come away with the impression that it's important to make a house as heavy as possible and they load it up with concrete. Which does nothing for efficiency or comfort. And concrete is pretty much the most environmentally destructive material you can use.
You've done the right thing so I don't want to pick on you too much. Low heat capacity emitters give the most responsiveness.
That is the worst Wikipedia article I've ever read. It basically parrots all of the pseudoscience about "thermal mass."
"Flywheel effect"? Give me a break.
'"Thermal mass" is not a term used in physics or engineering, it's a term made up by architects.'
Seems to have caught on at engineering schools like MIT:
https://ocw.mit.edu/courses/4-401-environmental-technologies-in-buildings-fall-2018/c03cdb9ea591216d81a3f2febd616a3c_MIT4_401F18_lec12.pdf
https://cshub.mit.edu/sites/default/files/documents/ThermalMassBenefit_v10_13_0920.pdf
You can find references to it in many building science articles too (e.g. from BSC).
"Popular understanding" of the term can also be completely wrong and that misunderstanding used to derive really poor choices in how folks construct buildings. Both can be true.
I don't think the chance of misinterpretation is so fundamentally worse in this case, relative to all the other things we discuss here, that we should single out and ban this term.
Well those two articles are pretty embarrassing for MIT.
One of the issues I have with "thermal mass" is that nobody seems to know exactly what property of matter they're talking about. One of my favorite questions when someone says a building has "high thermal mass" is to ask how many units of thermal mass it has. What are the units, and how are they measured? Usually that gets a blank stare.
Reinhart, in the first link, goes with the most common definition, that it's just a synonym for heat capacity. He goes all the way around the barn to get there, but he gets there. He defines (on page 8) thermal mass as volume times volumetric heat capacity, where volumetric heat capacity is heat capacity per unit of volume. In other words, thermal mass is heat capacity. Fair enough.
The paper by Ghattas, Ulm and Ledwith uses a completely different definition: (page 5)
"Thermal mass is the ability of a material to store energy at one point in time and release this energy at another. It is dependent on the relationship between the specific heat capacity, density, thickness and conductivity of a material." So that is a completely different definition. It brings in conductivity, which is not a factor in heat capacity.
But it's worse than that. Ghattas, Ulm and Ledwith can't even use the term consistently on the same page of the same paper. On page six they write, "Solid wood has low diffusivity because it has very low conductivity, despite its thermal mass." One sentence later they have a chart of "Thermal Properties of Building Materials," where under "Thermal Mass" timber is listed as "low." So despite its thermal mass, it has low thermal mass? Really?
Note that in the chart while the other properties of materials are listed with two significant digits of precision, "thermal mass" is merely listed as either "high" or "low."
So what are the units again?
Again, this is all about getting people to stop putting unnecessary concrete into their homes. The Reinhart article is actually pretty good because he shows the limits of adding heat capacity to a building. On page 56 he really gets to the heart of the issue: "Thermal mass has really no effect if the direction of heat flow through the building envelope stays constant for extended periods of time." Bingo. He might also add that typical construction doesn't lack for heat capacity, between the drywall and the framing there's plenty to buffer daily temperature swings.
Although he loses me on the next page when he starts talking about "Solarium with thermal mass." That's a road to hell.
Borst engineering has great calculators and they also do radiant design. I have not personally hired them for anything.
Thank you, I'll reach out to them.
Harvey Ramer, who was recommended by John Siegenthaler, did the design for our house.
https://www.linkedin.com/in/harvey-ramer-591a3315/
I've spoken with Harvey. Seems like a really nice guy. He said he's not doing design right now, but I'm trying to talk him into it. Wish me luck!
If I had to guess, ten tons sounds to me like they wanted to put a minisplit head in every room, and the manufacturer they chose doesn't make a had smaller than 3/4 or one ton.
Could be. I only understand enough to be dangerous, which is why we're not going forward until someone who does know the intricacies of all this, designs it.
It sounds like you're one of those ... do you also design radiant systems (even though including in-slab would be under protest)? If so, are you interested?
I'm not licensed. I am more than happy to consult though.
I'll need to resubmit a new Manual J along with the radiant & cooling system designs. An Arctic Heat Pump engineer told me we can use the same heat pump for heating and cooling, but their full system designers are 4 weeks out. I'd still feel better using someone independent.
On the one hand, if we could at least get the pex in the slab, it wouldn't be a big deal to wait for full design since the slab needs time to cure anyway. The problem is the county will want the entire system design, and the new J calcs it's based on, before approving it. They are pretty flexible around here, though. I could see the inspector okaying the slab pour if we document what's there to get it capped before the weather turns - but it would be a big risk if the county had an issue with something.
Aaaand we're back to just needing a really good designer who also happens to have all the time in the world right now. If none of those recommended are available, maybe you'd be down to review a 2nd tier design?
I'm seeing slightly over two tons heating and cooling -- 26,000 BTU/hr -- over 1350 square feet. That sounds really good. Am I missing something?
OK, figured it out. It's in 3 parts, of 28K, 19K and 26K. So 73K total. The parts are 1349, 649 and 1247 square feet for a total of 3285. Overall 22 BTU/sf.
Yes, it's currently 3 parts. A vented cooling system would likely remain at least 2 parts - the upper and main floors could be combined, but the great room (with its 15' ceilings and no truss connections to the rest of the house) would probably stay separate.
(Replying to Paul, #37)
Yeah, my advice is to run ductwork for what you need for cooling and then use floor heat to the extent your heating load exceeds your cooling load. In the winter use a two-stage thermostat so that the floor heat comes on first and the duct heat only comes on when the floor heat isn't enough. Place the floor heat strategically in the places where you're most likely to appreciate it.
If it's 26K BTU over 1350 square feet, that's 20 BTU/SF. Heat transfer is 2BTU per square foot per degree of temperature difference. So that's a 10F difference on average. You're not going to be able to get 100% of the floor area heated. I would do as much as you can at 15F, that's a floor temperature of 85F which probably means a water temperature around 105F. Then make up the rest with the air handlers you're going to need for cooling anyway.
For the radiant, I think an air-to-water heat pump would be a good match, the load is in the sweet spot and the design temperature of 26F means you're in the sweet spot.
Just to give an idea, Chiltrix makes a 2 ton and a 3.5 ton unit. Their spec sheets are at https://www.chiltrix.com/CX34-air-to-water-heat-pump/ for the 2 ton and https://www.chiltrix.com/CX50-air-to-water-heat-pump/ for the 3.5 ton.
The thing you have to look out for is cold weather performance. The 2-ton would be a little undersized, at 23F the 2 ton produces 22.6K BTU/hr at 104F water temperature with a COP of 2.5. That's about 4,000 BTU/hr under your heating load at that temperature. They have an inline resistance electric heater that can be used to supplement the output at cold temperatures.
At 23F outdoor temperature, the 3.5 ton unit produces 35.3K BTU/hr at 104F with a COP of 3.0. So it has plenty of capacity and a higher COP. It's also $3100 more.
Thank you! I'll check out those links as I try to understand this better.
I've been looking at an Arctic heat pump: https://www.arcticheatpumps.com/application.html
https://www.arcticheatpumps.com/specifications.html
This is an email one of their reps sent me regarding our project. He isn't one of the designers, unfortunately:
"Your house has a LOT of square footage of glass, and when I changed my calculations to reflect a glass R-value of 2.9, I got a number much closer to that of the Manual J calculation that you sent to me. They got 73,883 BTUH for heating and I got 66,962 BTUH. They got 65,341 BTUH for cooling, and I got 46,181 BTUH. I think part of that is I specified that your roof was white membrane, and part of it was I said the garage temperature was 50 degrees in winter and 80 degrees in summer.
I will continue to refine my calculations, as I find better numbers to use. But if the most recent numbers are correct… one 060ZA/BE produces 49,047 BTUH., which is 73% of the required heat load. Two 050ZA/BE heat pumps, however, produce 84,502 BTUH at Sedona winter design temperature, which is 126% of the required heat load.
Current industry wisdom says not to oversize or undersize a heat pump by more than 25%, so the 060ZA/BE is just a tad too small, and two 050ZA/BE’s is just a percentage point too large. Industry wisdom, however, also says it is better to be too small than too large, so the recommendation is still one 060ZA/BE.
If you install the 060ZA/BE knowing that it is a tiny bit small, what does that mean? With a little algebraic manipulation you can calculate that what that means is that when the outdoor temperature is lower than 36 degrees, you will need to have a fire in the fireplace, or the heat pump will need to rely on the electric backup boiler for help.
The heat pump will continue to run, even when it calls on the backup boiler to help, in order to minimize the additional electricity that the backup boiler needs to operate. Whenever the heat pump activates the backup boiler, it will deactivate it when the buffer tank temperature reaches its setpoint. The bottom line is that if the heat pump is undersized a little bit, the additional annual expense due to the backup boiler use will be on the order of a couple of hundred dollars. It’s just not worth spending an additional $6000 in order to save two hundred dollars per year. That’s why it is better to undersize than to oversize.
By the way, I calculated that the heat pump would only begin to need occasional assistance from the backup boiler when the outdoor temperature drops below 36 degrees."
Makes sense - backup electric resistance heat is cheap to install and expensive to operate, the reverse of an air to water heat pump.
Is it accurate that you have R2.9 glass? This is a U-value of 0.34. Given the efforts you are doing to insulate, I was surprised by that.
@ Tim O. Yes, that's my bad. I thought they were a lot better than they are. Long ugly story, but we're stuck with them now.
Deleted
It might even make sense to look at small battery "back-up system" to the electric resistance/backup boiler - where you purchase off peak electricity rates to run during use of supplemental heat & maybe even use during summer peak too w/cooling ...
Not exactly sure of the economics of that - just a thought ...