Refinishing / Insulating a 40 year old “finished” basement without insulation or vapor barrier

Hello,
Hoping for some help in the most logical way to refinish / rehab a full basement that does not appear to have been built with a vapor barrier, and very minimal insulation.
The house is a monolithic (concrete) dome, and as such, the basement is round. It was built in 1982 and located in Evergreen, CO at 7700 feet above sea level and low relative humidity. Climate Zone 5. The basement is 45′ diameter, 1600 square feet, and the poured concrete walls that are 9″ thick. The original plans indicate 2″ foam board on the outside of the poured concrete walls. The basement is below grade most of the way but about 1/4 of it is above grade with a walk out door. House is at the top of a hill and there are no signs of water or moisture issues that I can tell. Original construction photos show no indication of any vapor barrier or insulation under the slab. (There was a hydronic radiant heating system poured into the slab that I do not plan to reuse due to age and apparent issues with it).
The basement was originally finished with a wet bar, full bathroom, and had a pool table, etc. in it. I am refinishing it into a separate apartment/living space and have removed the drop ceiling and the linoleum flooring so I am back to floor joists above, the concrete slab below, and the bare poured concrete walls around the exterior.
So… any suggestions on if/how I should approach vapor barrier and insulation for both floor and walls?
For the floor, my initial thought was minimal insulation due to budget and also the 90″ ceiling height I am working with. Or just do the majority of the basement in carpet and do a minimal amount of LVP or tile on top of the concrete slab in high traffic areas.
For the walls, I am planning to frame them out in 2x4s (with curved top and bottom plates) to be able to add R15 insulation and finish the walls with drywall. Current design leaves a 1″ airspace between the concrete wall and the framing to allow for any slight variances in roundness and also to keep the insulation and wood off of the concrete. I have read differing opinions on this though so I wanted to check here to make sure I’m getting it right.
For the basement ceiling I would like to try and do a bit of sound isolation and was thinking either doing some fiberglass insulation or doubling up the drywall, or both. I don’t want to go crazy with it, just help manage sound a bit.
Being in CO, I don’t have major worries about humidity or moisture, but are there any steps to take before I put all of this back together?
Photos attached of original construction from 1982 that the original owners family sent me which provide some clues as to construction.
Look forward to your input, thanks!
GBA Detail Library
A collection of one thousand construction details organized by climate and house part
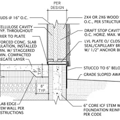
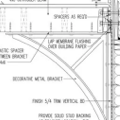
Replies
Anyone have some thoughts they could share on this one, or any resources I can reference to make sure I do this correctly? Thank you!
To address the acoustic issue between the first and second floor, I would be most concerned about footfall noise, as other than conversation, that is the most objectionable. To address this you need to decouple the framing above from the gyp ceiling.
I'd look into hanging the ceiling gyp on acoustical resilient channels. HOWEVER, these must be installed 100% accurately in order to work. Unless you are doing the work yourself or are going to supervise the RC install and the subsequent install of every single board of ceiling gyp, you may wish to spring for the more expensive isolation system that is less prone to field error.
Before hanging the gyp at the basement, I'd use a combined fire and acoustical sealant material on EVERY SINGLE penetration. You will be shocked at how much this can address noise transmission of conversations, etc. Do not forget to put putty pads around the electrical j-boxes in the ceiling of basement to reduce noise transmission into the joist bay. Insulate any ducts you have in the joists bays not just to prevent condensation but to prevent noise transmission. It is my understanding neoprene helps with this but do your research.
Insulation between the joists cannot hurt, but air sealing to prevent sound transmission should be the priority, and with the basement as a separate apartment, you will also need fire sealing, so these can be combined with the correct products. Second priority is footfall noise with a resilient clip system. Consider also a gyp product with acoustic properties. The cost differential is minimal - a bit higher material cost, and perhaps a premium to hang the heavier board, but tape & finish are the same. If you are going to insulate the joist cavities, consider doing so with rockwool.
Concurrently attempt to isolate footfall noise from above, with an underlayment under the finish floor of the main level above. This has varying degrees of success - the cheap products don't do much, but some of the products are useful. Avoid hard tile floors on the main level - resilient flooring such as rubber, or even a step down to LVT with an excellent backer is much quieter than porcelain tile. Carpet and pad are the quietest.
Thank you for your input here.
Unfortunately for sound transmission, there will be tile throughout the common area and kitchen on the main floor.
I don’t know if it changes anything, but the main floor has 1.5” of concrete poured on top of the plywood subfloor (covering a radiant hydronic heating system). This obviously increases mass but I don’t know that it would help with footfall noise?
Pictures that you posted on an earlier thread showed a spiral staircase connecting the first floor and basement. Sound travels more readily through air than through any construction material, if you have an open-air passageway it really doesn't matter how much soundproofing you put in the floors. It's like having a boat where only half of the bottom is waterproof.
Good catch, I will actually be enclosing the spiral staircase at the basement level, with a solid core door that can act as a lock off. Not a perfect solution, but a solution nonetheless.
"you may wish to spring for the more expensive isolation system that is less prone to field error. "
Can you share an example of a more user-friendly, but expensive system? Some terms to research would be interesting.
What I would want to know is whether the foam board that the plans show on the outside of the basement was really done. It's incredibly common in residential construction for things not to be build according to the plans, it's especially common in exotic designs where the enthusiasm starts wearing thin as the reality of construction sets in. I think it would be difficult to fasten foam board to the exterior of a dome.
You want to have a vapor barrier on the floor and walls, concrete wicks moisture and it will draw moisture out of the soil and into your insulation and the interior of the house forever if you let it, it's not like you're going to be able to dry out the earth under your house. It's OK to have it on the inner surface of the concrete. Plastic sheeting is usually the cheapest way.
We argue here about whether batt insulation is ever appropriate underground. I say it isn't, but my experience is limited to the east coast. Here in DC we had a day last week when the dewpoint was 77F. The problem with batt insulation -- or any permeable insulation -- is that there is no drying action in a basement wall. Moisture tends to flow from warm to cold, and in a basement the interior is warmer than the concrete surface every day of the year so the vapor drive is from inside to outside -- but there's nowhere for the vapor to go on the outside. If it ever happens that your interior air has a dewpoint higher than the concrete surface temperature you run the risk of condensation happening in the insulation, and no way for it to escape. I'd image where you are the soil temperature is around 50F, a dewpoint of 50F equates to indoor conditions of 72F and 45% RH, which is very normal indoor conditions.
Studding out a circular wall seems like an enormous amount of work, I'm trying to imagine ways to make it easier. One thought is to make the bottom plates and top plates out of two layers of 3/4" plywood, cut in an arc. Overlap the joints. You could even attach the bottom half of the bottom plate, then assemble the studs and one top and one bottom plate into an assembly on the floor and tip it up into position, then slide the second top plate in to snug it all up. I think you could make a jig to cut the arcs relatively quickly. You'd need 17 pieces for each layer so about 70 pieces total. If my math is right you could get ten arcs out of a sheet of plywood.
You are very on point with your observations, thank you.
I do see signs of foam board sticking out of the dirt in some places around the house now and I also saw it in one of the original construction photos. I'm not sure if it goes all the way down to the slab, or they just went down 4' with it though. See the 4th photo attached above with the man standing next to the building -- looks like silver faced foam board and hopefully the black next to it is a waterproofing coating on the concrete? I don't know though... I have no info other than that if any moisture/vapor barrier was put in place.
With regards to the plastic vapor (moisture?) barrier -- this is really what I am trying to nail down and unsure of. My current plan was to allow a 1" airspace between concrete wall and wood framed well to account for any inaccuracies in original construction or my construction, and also to keep the wood and insulation off of the concrete wall. I have seen this done with plastic sheeting hung in between the concrete and the wood framing which also helps keep the insulation from touching the concrete. Do you think this air gap will help me or hurt me? I could do this with R13/R15 insulation which would maintain the gap, or I could use R19 which would fill in the air gap. I hear what you're saying about batt insulation and moisture/mold but I am hoping that the plastic sheeting (6 mil?) will keep any moisture from outside from getting to the insulation.
I guess my only concern and unknown is if hanging plastic sheeting over the wall has any adverse/negative affects with trapping moisture up against the concrete, or anything else I'm not considering.
As for the floor, same type of 6 mil plastic sheeting under whatever subfloor I choose? I need to choose either tile or vinyl plank flooring for a smaller part of the basement, and will likely carpet the majority of it. Do you see any benefit in trying to add a small amount of insulation under the floor?
Also, you were spot on with the curved wall framing -- I am in the process of cutting templated arcs in 3/4" sheets of plywood just as you have described. They are 3.5" wide and I am getting about 12 per sheet of plywood and they're roughly 8' long each which makes for 96' per board. Pressure treated for the bottom and normal up top. I've got about 135' of linear wall length, which means 3 sheets of pressure treated and 3 sheets of normal plywood to have enough for two courses top and bottom.
I figured I would trace out 4.5" from the concrete wall to mark out a circle where I would align the front edge of the bottom plate, and use a laser level plumb point to transfer that point vertically to the ceiling. I figured building the wall on the ground may be tough but I'm sure its possible -- my thought was to just install top and bottom joists and then place the studs between them. I haven't been able to find any contractors who actually follow up about anything, so looking like I'll be doing this myself, hopefully with a helper. It'll take time but it'll save money.
Also, FWIW, I have been logging temp and humidity in the basement, main floor, and loft. With the windows and doors shut and no inside conditioning here are the temps:
Outside Low Avg. 60F
Outside High Avg. 90F
Basement Temp: 63F - 64F
Basement Humidity: 62%-63%
Main Floor Temp 68F - 72F
Main Floor Humidity: 45% - 48%
Loft Temp: 70F - 76F
Loft Humidity: 42% - 47%
This was with the ceiling fan off, I am also curious to see if having the ceiling fan on a low/medium speed will bring the loft and main floor temps a bit closer together.
"I hear what you're saying about batt insulation and moisture/mold but I am hoping that the plastic sheeting (6 mil?) will keep any moisture from outside from getting to the insulation."
The concern is that moisture in the indoor air will condense in the insulation and have no mechanism for drying out.
Wouldn't faced insulation create the vapor barrier to prevent that?
Do you have a recommendation on what these wall assemblies should look like? What is the ideal, and what is the budget minded and also satisfactory solution?
I am admittedly starting from scratch and learning as I go, but I am still unclear on where there should be moisture management in a basement wall, and where it should breathe.
Even with that poly vapor barrier against the wall, you can still have moisture migration from the living space through the batt that will then condense against the interior facing side of the poly. You need an impermeable insulating material here that is an air barrier and vapor barrier/retarder to make sure moisture can’t migrate through. That pretty much means rigid foam or spray foam. Batts are not air barriers, so moisture can move right through them along with the moving air.
Bill
Revisiting this with a new question that I'd love some feedback on:
I had originally planned to frame a standard 2x4 wall freestanding and inset 1" inside of the poured concrete foundation wall. Now I have seen another method where rigid foam board is adhered directly to the concrete foundation wall and 1x3 (or up to 2x4) furring strips are fastened directly on top of that and secured through the foam into the concrete. Then drywall is laid directly on top of this.
Main motivation is that it is roughly 135' of curved wall and I feel it would be faster and easier furring out from the existing curved concrete wall than to build a freestanding curved wall, it would also utilize thicker continuous foam board insulation and be an overall thinner wall construction which leaves a little more square footage in smaller rooms especially.
Best I can tell, either method could work, I'm just trying to finalize a method so I can get started on things soon.
The furring strip approach would be about R-10 and wiring would have to run into the foam behind the furring strips but thats ok. I would have to shim the furring strips as needed to keep the wall plumb but would probably install a good bit quicker and easier than a freestanding wall and would also allow for continuous insulation with no breaks.
One question I run into -- can I use shallow depth electrical boxes if I don't have enough depth otherwise? The furring strip method would likely be 2" foam board insulation plus 3/4" furring strip plus 1/2" drywall = 3.25" total depth from concrete wall. Is it acceptable to use a 4"x4" shallow box for one or two outlets? Or is there a better solution?
Next question would be how much and what kind of flooring vapor battier / insulation to use for the subfloor, but that also depends a bit on flooring I will be going with. Liking the idea of a combo of LVP and carpet, I think. Existing headroom from concrete slab to floor joists above is 92" so I'm trying to mind my head space through this process.
I was thinking about your house after your last post. A straight 8' wall against a 45' diameter curved wall would be about 4" inside the wall at the midpoint. It seems it would simplify things a lot to just put up 18 or so 8' sections made from 2x4. Where they join the drywall would make a 20 degree joint or so. So basically your basement becomes a polygon instead of a circle.
To your questions:
The problem with the shallow boxes is that normally wiring is run from box to box, the shallow boxes are too small to allow a junction within so they have to be at the end of a run. It's not impossible but it complicates things. There is also a style that is shallow and wide like this: https://www.homedepot.com/p/Carlon-1-Gang-17-cu-in-PVC-Shallow-Old-Work-Electrical-Switch-and-Outlet-Box-B117RSWR/202077341. They're normally used on old work.
In terms of insulating the floor usually messing up the stair step spacing is as big a deal or bigger than losing headroom. All riser heights have to be within 1/8" so if you raise the floor you have to redo all of the steps. So normally the advice is don't mess with the floor height.
Thanks for the further input — I really wanted to aim for a constant curve on the basement and we are quite far along with it now.
We tested a variety of options and found this to be the best in this situation:
2’ wide sections of 1” xps insulation (r-5) glued to concrete basement walls, then curved 2x4 wall installed inside of that which can take r-13 insulation.
I also went with 1” xps on the floor with 3/4” osb over top of it screwed down with two cons.
I also took care to seal up and insulate the rim joist area all around with a combo of 2” xps and canned spray foam as well which took some work with the way the blocking was installed.
I was trying to attach some photos from my phone but it doesn’t seem to like my iPhone images unfortunately.