Reinsulating basement walls

We recently moved into a new home. Tracking down a modest amount of mildew, we ended up stripping the wallboard from 2×3 studs on basement and removing all fiberglass batts. Now that the mildew has been remediated we are ready to re-do the wall surface.
Your articles on basement wall insulation have been very helpful, causing us to be disinclined to re-insulate with fiberglass. It is not clear to us how to most effectively work with the 2×3 stud system, which stands off the concrete block wall by 1 to 2 inches. Since we are not concerned with getting high R value, would it suffice to simply slide (and glue) 1 inch foamboard behind the existing studs?
GBA Detail Library
A collection of one thousand construction details organized by climate and house part
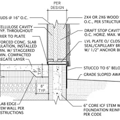
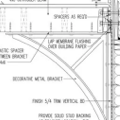
Replies
If you don’t have any existing moisture problems with those walls, then it’s probably safe to slide in some 1” foam board behind those studs. Be sure to tape all the seams. I’d use polyiso too, that way you get the maximum R value in the space you have available (1” is about R6 for polyiso). The framing looks to be in really good shape so I’m guessing that wall has been dry.
Bill
Seems like a good application for closed cell spray foam. What climate zone are you in? You should at least insulate to the code minimum for a basement wall. There may be enough space behind the studs to meet the continuous insulation provision which would reduce the total R value needed . Also, the void between the top plate and the foundation wall should be fire blocked. See attached detail.
I'm having a hard time visualizing this fireblocking- wouldn't that space be filled up with hard closed cell foam if they were hitting the walls and air sealing the rim joist area as well?
I believe you put the fireblocking in before you spray the foam. The foam itself doesn't count as fireblocking.
Closed cell foam is not a code approved fire block material, at least in my area its not. Additionally, most spray foam and rigid foam products are combustible, further stressing the need to properly fire block this location. Another method is to fill the void with mineral wool and then spray the closed cell above and below.
I'm planning on sprayfoaming my basement first, finishing it off later. I'm picturing CC foam going up and over the foundation and completely covering the sillplate and joist area. Seems like I would have to use the wool to seal off the cavity after the walls have gone up.
kjmass1,
In your application you can still put a code approved fire block in place before you spray foam. The best solution would be to use strips of 1/2" drywall and install them as shown in the fire block detail above. You can let them extend out further than where your wall top plate will be and cut them flush after framing is done. You would want to put in proper blocking where your floor joists run parallel with your walls to support the fire block and your future top plate before you foam.
Any air leaks that allow interior air to get behind rigid foam will increase heat loss and deposit moisture (a problem if it runs out on the floor or grows mold). Spray foam is far more likely to be airtight.
See Fig 7 below for how basement wall moisture varies with added moisture (90% is much worse than 50% when it comes to mold).
https://aceee.org/files/proceedings/2006/data/papers/SS06_Panel1_Paper27.pdf
Air leaks that deposit moisture on the cold concrete are not a moisture problem. The CMU block is going to be at whatever ground moisture level there is on the soil side of the foundation once the foam is in place. Tape the seams, can-foam the top & bottom to prevent convection and call it a day. If you're in climate zone 3 or lower that's enough to meet code min on it's own.
With uneven spacing between the stud edges and concrete it's true that closed cell spray foam will be easier than rigid foam and would provide a more consistent depth for installing void-free fiber insulation going into the 2x3s. Compressing 3" sound-abatement rock wool batts into the 2.5" nominal depth of a 2x3 cavity would yield about R10 performance, and with at least 1" /R6 of closed cell foam between the batt and concrete at the above grade section there would be no moisture or frost accumulation in US DOE climate zones 6 or lower, but might on the cold half of zone 7. Where there's 2" of closed cell there is zero moisture risk in any US climate zone.
If going with 1" rigid polyiso and blown fiberglass insulation to fill the voids behind the studs there is a small potential for moisture accumulation above grade in zone 6 in parts of the wall where the foundation to stud edge gap is 2" , but it's fine up through zone 5. If using EPS rather than polyiso drop one climate zone. (At 1" EPS would not meet code min even in zone 3.)
If using polyiso, keep the cut bottom edge off the slab, since it could wick any foundation moisture or leakage up from the slab. That's not an issue for EPS or XPS, and if there has been a flooding history it's better to use EPS up to the high tide mark and a bit beyond.
Don't use XPS (unless it's reclaimed/reused goods), which is the least-green insulation in common used in North America, primarily due to the HFC blowing agents used, but also the polymer type & weight per R. As the HFC blowing agents dissipate over decades the performance drops to that of EPS of similar density. The performance warranty on XPS is only for "90% of labeled R value", so an inch of XPS is only warranteed at R4.5, not the labeled R5, and even that is probably too optimistic after 50 years.
If going with spray foam, most closed cell polyurethane is blown with similarly bad HFC blowing agents (usually HFC245fa) but there are a number of closed cell foam products blown with HFO1234ze, and they tend to run R7 @ 1" , compared to R6- R6.5 for the HFC blown goods. Price wise it's about 25-35% more expensive per board-foot, but only a 10-15% premium per-R, due to the higher R/inch.
“If using polyiso, keep the cut bottom edge off the slab, since it could wick any foundation moisture or leakage up from the slab. That's not an issue for EPS or XPS,...”
Why? Is EPS or XPS better in high moisture situations than polyiso?
Polyiso is mildly hygroscopic- it will wick and retain liquid water and take forever to dry.
EPS and XPS are non-hygroscopic- they don't wick water. When submerged in liquid water they can take on water, but it will eventually leave, drying at a rate much faster than polyiso after the tide goes out.
Great to know. Thanks.